前言
减少电子产品的组装尺寸、重量、避免连线错误,增加组装灵活性,提高可靠性,实现不同装配条件下的三维立体组装,是电子产品日益发展的必然需求,挠性电路作为一种具有薄、轻、可挠曲等可满足三维组装需求的特点的互连技术,在电子及通讯行业得到日趋广泛的应用和重视。
随着其应用领域的不断扩大,挠性线路板本身也在不断发展,如从单面挠性板到双面、多层乃至刚——挠性板等,细线宽/间距、表面安装等技术的应用以及挠性基材本身的材料特性等、对挠性板的制作提出了更严格的要求,如基材的处理,尺寸的稳定性的控制,去沾污,小孔金属化及电镀的可靠性及表面保护性涂覆等方面都应予以高度的重视,本文仅就在研究和生产过程中所选择的工艺以及应注意的问题进行总结和阐述。
2 多层挠性线路板
2.1 材料的选择
挠性印制线路板所选用的材料直接影响板子生产及其性能。
覆铜材料我们选用日本新日铁的无粘接剂聚酰亚胺(PI)挠性基材(SB18—25—18,SB18—50—18等),聚酰亚胺是一种很好的可挠性,优良的电气性能和耐热的材料,但它具有较大的吸湿性和不耐强碱性。之所以选择无粘接层的基材,是因为介电层与铜箔间的粘接剂多为丙烯酸、聚酯、改性环氧树脂等材料,其中改性环氧树脂粘接剂可挠性较差,聚酯类粘接剂虽可挠住好,但耐热性较差,而丙烯酸粘接剂虽然在耐热性、介电性能以及可挠性方面令人满意,但其玻璃转化温度(Tg)较低(40℃左右),以及极差的耐碱性给加工及焊接带来困难。
由于丙烯酸粘接片Tg较低,在钻孔过程中产生的大量沾污不易除去,影响金属化孔质量,以及其它粘接材料的各种不尽人意处,所以,多层挠性板的层间粘接层我们选用聚酰亚胺材料,如新日铁的SPB50A、SPB35A等,因为它与PI基材配合,其间的CTE(热膨胀系数)一致,克服了多层挠性线路中尺寸不稳定性的问题,且其它性能均能令人满意。
外层图形的保护材料,一般有两类可供选择,一类是干膜型(覆盖膜),一种是选用聚酰亚胺材料,无需粘接剂直接与蚀刻后需保护的线路板以层压方式压合,这种覆盖膜要求在压制前预成型,露出需焊接部分,故而不能满足较细密的组装要求,另一种是感光显影型覆盖干膜,以贴膜机贴压后,通过感光显影方式漏出焊接部分,解决了组装细密性的问题,还有一类是液态丝网印刷型覆盖材料,常用的有热固型聚酰亚胺材料,如新日铁SPI200以及感光显影型挠性线路板专用阻焊油墨,如高氏XV—601T等。这类材料能较好地满足细间距、高密度装配的挠性板的要求。
2.2 生产工艺的确定及非常规部分的控制
多层挠性板的研制是在双面挠性板及高密度多层刚性板的基础上进行的,在工艺制造方面与刚性板有很多相同的地方,但是,由于挠性材料及其应用的特殊性,决定了它从设计要求到制作工艺都有别于普通的刚性板,几乎对每一个生产环节都要进行试验、调整,最终优化整个工艺流程和参数。
2.2.1 工艺流程
基材下料→预烘→电解清洗底片准备→内层单片图形转移→酸性蚀刻→AOI检查→OPE冲制后定位孔→内层氧化→层压→钻孔→等离子体去沾污→金属化孔→外层图形→AOI检查→图形电镀→碱性蚀刻→退铅锡→通断测试→覆盖保护层→涂覆有机预助焊剂→外型加工
2.2.2 内层单片的图形转移
图形转移在高密度、细线条的印制板中占据非常重要的地位,对挠性线路而言,尤其如此。因为挠性单片既薄又软,给表面处理等操作带来很大困难,而铜箔表面的清洁状态及粗糙程度直接影响抗蚀干膜的贴附及细线条的制作。由于机械擦板对设备要求较高,且不适宜的压力可能造成基材变形、卷折、尺寸伸缩等,操作不易控制,故而我们选择使用电解清洗法。这种方法既可保证表面清洁度,微蚀步骤又可保证铜面的粗糙度,有利于0.1mm~0.15mm线宽/间距的图形制作。
酸性蚀刻除了注意控制蚀刻速率以保证设计要求的线宽、间距外,更要注意防止单片的卷曲、皱折,最好是加牵引板且关闭设备上的抽风系统。
2.2.3 挠性材料的多层定位
挠性基材的尺寸稳定性较差,这是因为聚酰亚胺材料有较强的吸潮性,经过湿处理或在不同的温、湿度环境中收缩变形严重,造成多层板的层压对位困难。为了克服这一困难,可采用以下措施:
(1)OPE冲制后定位孔,能消除湿法处理过程中材料伸缩变形带来的误差。
(2)层压后用X—ray对位钻孔,确定偏移量,使钻孔更为精确。
(3)针对聚酰亚胺的材料特性及环境特点,参考钻孔偏移量绘制外层底片,提高外层底片与钻孔板的重合度。
这样,我们就可以满足层间对位保证0.1mm~0.15mm环宽的要求,保证外层图形转移的精确度。
2.2.4 层压
即使是采用OPE冲制后定位孔,层压前的单片处理对层间对位也有着很大影响。首先,由于聚酰亚胺材料不耐碱,在强碱溶液中产生溶胀,所以在进行黑氧化处理的过程中,在强碱性工位如去油、黑氧化等适当地降低温度、减少时间。由于采用的是无粘接层基材,无须考虑粘接层在碱液中的变化,这种方法还是可行的。其次,氧化处理后的单片烘烤应避免垂直放置,应采取水平烘烤方式,可减少弯曲变形,尽量保持平整。烘烤后尽可能地缩短装模时间,防止单片再次吸潮。
由于挠性单片易变形,层压前平整度较差,加之所用粘接片的树脂流动度大大低于刚性板层压用的半固化片,所以,为使粘接片与单片结合良好并嵌入细密的线条间距中,我们选择使用覆形性较好的材料作为层压衬垫材料,如聚丙烯薄膜、纸、硅橡胶片等,可提高挠性板的层压质量。试验后认为理想的衬垫材料为硅橡胶材料,即可保证其覆形性又可相对减少被压件尺寸收缩变形。可采用以下叠板方式:
被压件较多时,可在一套模具中以不锈钢隔板按上述叠板顺利一次叠板2~3件。
压制参数可参考PI基材刚性板压制参数进行适当的优化。
2.2.5 钻孔
由于挠性基材没有加强纤维,既轻又薄,钻孔参数不适当可能造成介质层撕裂和大量粘污,所以根据不同的板厚、质材进行钻孔参数的优化,同时,盖板、垫板的选择也非常重要,因为挠性板柔软轻薄,盖、垫板不仅可以支撑板子,还起到散热作用,应当注意的是垫板最好用铝箔板或环氧胶木板,不要用纸质垫板,因为纸质垫板较软,容易产生较严重的钻孔毛刺,孔化前去毛刺时容易撕裂或擦坏孔口,给后工序工作带来麻烦,影响板子质量。
还有一点应该注意的是,虽然我们在湿法处理、冲制OPE孔,层压对位等方面做了大量的工作以保证层间对位精度,但是,由于聚酰亚胺材料本身受湿热影响较大,不可避免地会产生不确定的层间偏差及板间偏差。所以,钻孔前应以X—ray对位钻小孔,确定不同板子的不同的钻孔偏移量,参照该偏移量进行数据校正,确保钻孔精确有效。同时,该偏移量交至光绘工序,参考绘制外层底片,保证外层图形转移的对位精确。
2.2.6 去沾污及金属化孔
多层挠性板的孔内沾污以聚酰亚胺树脂为主。挠性聚酰亚胺树脂对浓硫酸溶液显惰性,而在强碱性的高锰酸钾溶液中又会产生溶胀,所以,常规的湿法去沾污很难奏效。我们也曾尝试过使用浓硫酸或碱性高锰酸钾溶液去沾污,改变浓度、温度、处理时间等参数,多次试验都没有收到令人满意的效果,于是,我们放弃了传统的湿法化学去沾污,改用等离子体法。
等离子体是指电离的气体,是原子在射频能量发生器的作用下完全或部分失去其电子层时的状态,由离子、电子、自由基、游离基团和紫外线辐射粒子等到组成,整体上显电中性,具有很高的化学活性。等离子体去沾污最大的优点是没有选择性,就是不分所处理板子的树脂类型,只要调整参数,均可进行处理。譬如,高活度的等离子流对环氧树脂、聚酰亚胺、丙烯酸、玻璃纤维等产生的沾污都能快速、均匀地把它们从孔壁上作用掉,并可以形成一定的凹蚀,有效地实现三维连接,提高金属化孔的可靠性。
等离子体去沾污一般分为三步:
(1)在设备腔体达到一定的真空度后向其中按比例注入高纯氮气和高纯氧气,主要作用是清洁孔壁,预热印制板,使高分子材料具有一定的活性,有利于后续处理。一般为80℃、15分钟。
(2)以CF4、O2和N2作为原始气体与树脂反应,达到去沾污、凹蚀的目的,一般为85℃、15分钟。
(3)以O2作为原始气体,去除前两步处理过程中形成的残留物或“灰尘”,洁净孔壁。
金相报告显示,等离子体去沾污后的金属化孔孔壁状态令人满意。
等离子体去沾污后板子的金属化孔前处理,亦不能按常规工艺进行,这是由于基材本身特性决定的。经去沾污处理后的板子,须用专用溶液对孔壁进行特殊处理。我们选用Neatraganth处理液(A十B)和HCF—45十H2SO4,清洗液对板子进行预处理(处理前应先擦板去毛刺),改善其表面状况,这样可以提高聚酰亚胺与化学铜结合的牢固性,预防孔化空洞。
2.2.7 外层图形转移
外层图形转移前的基板处理可采用擦板或电解清洗两种方式,这可视基板厚度及设备状况而定。若采用电解清洗方式,应注意控制微蚀速率,不能将孔中的化学铜蚀刻掉。而采用擦板则应注意卷板。
2.2.8 表面阻焊及可焊性保护层
由于挠性板在使用过程中有挠曲要求,普通的阻焊油墨易脆裂,无可挠性,不能满足要求;一般双面挠性板用的预成型的聚酰亚胺覆盖膜不能满足精细线路的要求,所以我们只有两种选择:一是贴显影型挠性覆盖干膜,一是丝网印刷挠性液态感光显影型阻焊油墨,两者都能起到阻焊、防潮、防污染、耐机械挠曲等作用。因后者覆形性较好,故我们更多地使用后者。
可焊性保护层使用有机防氧化保护膜,保证焊盘表面平整、可焊。
3 刚——挠性线路板
刚——挠结合印制板是指在一块印制板上包含有一个或多个刚性区和一个或多个挠性区的印制线路板。它可分为有增强层的挠性板及刚——挠结合多层板等不同类型。本文仅就无镀通孔有刚性增强层的多层挠性板进行阐述。
选择这样的结构是因为表面贴装技术应用于多层挠性板且焊脚越来越细密,这就要求挠性板焊接面在焊接过程中保持较高的平整度,而挠性板的轻、薄、软的特性又决定了它无法保证这样的平整度,故而要求在非焊接面的非挠曲部分增加刚性增强层,这样既可保证让焊接要求又不妨碍挠曲要求,且生产制作也较简单,可靠性高。
3.2 材料的选择
挠性材料前面已经讲过,勿需多言,而刚性增强板的选择也有一定的要求,我们最先选择成本较低的环氧胶木板,因表面太过光滑无法粘牢,后又选择使用FR—4.G200等有一定厚度的基材蚀刻掉铜,但终因FR—4.G200芯材与PI树脂体系不同,Tg、CTE皆不配合,受热冲击后刚——挠结合部分翘曲严重不能满足要求,所以最后选择PI树脂系列的刚性材料,可以用P95基材压合而成,也可以单纯用P95半固化片压合成,这样,相配合的树脂体系的刚——挠性板压合后,就可以避免受热冲击后的翘曲变形。
刚性板与挠性板之间的粘接层选择使用丙烯酸粘接片,因为这步过程仅是单纯的粘接加强作用,无须进行钻孔和镀通孔,无减少沾污的顾虑,而且丙烯酸粘接片的搞剥强度要优于聚酸亚胺粘接片,另一方面,丙烯酸成本较低,更经济一些。
3.3 刚性部分的工艺及控制
3.3.1 简要工艺流程
基材下料→层压前处理→压合→蚀刻外层铜→铣挠性区窗口→待与挠性板压合
半固化片准备
3.3.2 注意事项
加强板的压合主要应注意以下三方面的事项:一是不论是基材压合还是单纯的半固化片压合,都要注意玻璃布的经纬方向要一致,压合过程中注意消除热应力,减少翘曲。
二是加强板应有一定的厚度,因为挠性部分很薄且无玻璃布,受环境及热冲击的影响后,它的变化与刚性部分是有差别的,若刚性部分没有一定的厚度或硬度,这种差别就会表现得很明显,使用过程中就会产生较严惩的翘曲变形,影响焊接及使用,若刚性部分具有一定的厚度或硬度,这种差别就可能会显得微不足道,整体的平整度不会同挠性部分的变化而产生变化,可保证焊接及使用,若刚性部分太厚则显得厚重不经济,实验证明0.8~ 1.0mm厚度较为适宜。
三是挠性窗口应铣切精确,既不能小了影响焊接也不能大了影响挠曲,可由光绘直接出具铣切数据,也可出一张铣切图形作为编程基准。
3.4 刚——挠性部分的压合
刚、挠两部分的压合控制很简单,只要注意以下几个方面:
一是刚性加部分在压合前要用擦板机稍微粗化一下,提高粘接强度。
二是丙烯酸粘接片的裁剪应尺寸适宜。
三是挠性部分在压合前可只做些简单的清洁处理。
四是装模时应在挠性窗口部位加垫片,此垫片应厚度适中,大小合适,以防止刚挠结合部分压结质量及挠性部分皱折,可使用铣切窗口时的铣切多余部分,并用隔离膜包好,以防止脱模时粘接。
刚——挠板压合成铣切成型,作有机防氧化助焊处理后交付可使用。
4 小结
在多层挠性及刚——挠性板的研究制作方面,我们可能起步较晚,但经过近3年的实验、探索,立足现有设备,出适合于是我们自己的一套工艺、生产方案,虽然粗浅,但成功地解决了细线条的图形转移、尺寸控制、层间对位精确度、去沾污、刚挠结合等一系列的问题,较好地满足了用户的需求,还有很多问题如刚——挠结合镀通孔等问题还有待于进一步的研究探索。
- 多层挠性(5208)
相关推荐
多层PCB线路板结构解析
多层电路板怎么区分?
挠性印制线路板
挠性印制线路板
挠性印制线路板试验方法
挠性环氧覆铜板:技术决定竞争力
挠性电路的特性及优点
线路板加工核心设备辨析
线路板PCB加工的特殊制程
线路板、贴片
线路板基础教材
线路板基础知识
线路板基础知识解疑
线路板基础问题解答
线路板焊接基础知识
线路板焊接基础知识
线路板焊接方面的基本知识
线路板焊接方面的基本知识
线路板焊接的原理和条件
线路板焊接资料
FPC线路板设计需要注意问题
FPC全制程技术讲解
FPC柔性线路板叠层结构介绍
FPC软性电子线路板常用相关术语
FR-4单面电路板与精密PCB多层线路板区别
Molex铜制挠性产品生产效率提高
PCB多层线路板怎么区分?
PCB板制作工艺中的等离子体加工技术
PCB线路板为什么要做阻抗?
PCB线路板可靠性分析及失效分析
PCB线路板电镀加工孔化镀铜工艺技术介绍
PCB线路板的互连方式
PCB线路板的各层专业术语有哪些
PCB印刷线路板知识
PCB电路板和线路板的区别是什么?
PCB设计中专业英译术语之综合词汇
[原创]专业业生产单/双/多层 LED灯条板线路板
pcb线路板打样批量
pcb线路板的热可靠性概述
【PCB小知识 3 】PCB设计铜铂厚度、线宽和电流关系表
【转帖】柔性电路板种类及应用介绍
一般性柔性线路板的性能与参数
刚柔结合板和刚性板
单层PCB线路板
单面线路板与精密多层pcb线路板的区别
印制线路板尺寸设计的对成本的影晌
印制线路板的设计基础(上)
印制线路板的设计基础(下)
印制线路板设计经验点滴
印制电路板PCB分类及制作方法
印制电路板的分类
印制电路板设计的技术指导教程分享
印刷线路板及其加工
印刷线路板及其制作工序
如何提高PCB线路板的热可靠性
常用PCB专业用语的综合词汇
怎么提高pcb线路板的热可靠性
柔性线路板 柔性电路板FPC专业术语详解
柔性线路板三种主要功能叙述
柔性线路板三种主要功能叙述
柔性电路板种类及应用介绍
柔性电路板种类及应用介绍
激光加工技术在柔性线路板中的应用
电子线路板热可靠性分析与判断
电路板的分类与相关画法
盲孔与埋盲孔电路板之前的区别
离子迁移对印刷线路板绝缘性能的影响
详解PCB线路板多种不同工艺流程
钛金属和线路板制作的特点
简述高层线路板在生产中的主要加工难点

多层线路板构成

高层线路板的关键在哪一道工序

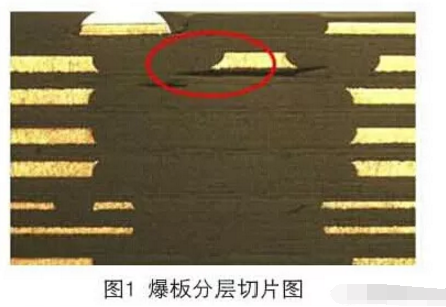
不放心?带你看看华秋8层以上PCB的工艺能力和服务案例

评论