双极步进电机广泛用于许多应用中,从打印机到工业设备中的移动XY工作台。通常情况下,电机驱动都采用较廉价的专用步进电机驱动芯片控制,简单的电流控制方法使电机的电流波形不理想、电机运行精度不高。
现在,通过在步进电机驱动IC内部集成双向电流采样,能有效提高电机运行控制精度,同时比传统解决方案降低了系统成本。
PWM控制和电流衰减模式
大多数的步进电机驱动IC,依靠步进电机绕组的电感特性实现PWM电流调节。通过每个绕组对应的功率MOSFET组成的H桥电路,随着PWM控制开始,电源电压被加到电机绕组上,从而产生驱动电流。一旦电流达到设定值,H桥就会切换控制状态,使得输出电流衰减。一定固定时间后,一个新的PWM周期又会开始,H桥再次产生线圈电流。
重复这一过程,使绕组电流上升和下降。通过电流采样和状态控制,可以调节控制每一段细分的峰值电流值。
在预期的峰值电流达到后,H桥驱动绕组的电流衰减控制方式有两种:
绕组短路(同时开通低侧或高侧的MOSFET),电流衰减慢。
H桥反向导通,或允许电流通过MOSFET的体二极管流通,电流衰减快。
这两种电流衰减方式称为慢衰减和快衰减(见图1)。
图1:H桥工作状态
传统峰值电流控制的问题
传统的步进电机峰值电流控制,通常只检测通过线圈的峰值电流。当预期的峰值电流达到后,H桥就会切换导通状态,使得输出电流衰减(快衰减,慢衰减,或两者的组合)。
选择慢衰减,可以得到更小的电流纹波,平均电流能更准确的跟踪峰值电流。然而,随着步率增大,慢衰减不能够及时降低绕组电流,无法保证精确的电流调节。
为了此情况,许多步进电机驱动芯片,在电流幅值增加的时候采用慢衰减模式,在电流幅值减小时使用快衰减或混合衰减(结合快衰减和慢衰减)模式。然而,因为快衰减模式时的电流纹波相对大很多,导致两种模式下的平均电流值相差很大,导致电机运行不平稳(见图2)。电流过零时,因为两种衰减模式的切换,也会有同样的问题。
图2:传统峰值电流控制下的波形
内部电流检测实现双向电流采样
传统的步进驱动,在每个H桥下管源极和地之间接外部检测电阻,只测量PWM导通时检测电阻上的正向电压。在慢衰减模式下,电流循环通过内部MOSFET,不通过检测电阻,因此无法测量电流。在快衰减模式下,通过电阻的电流翻转,产生的是负电压。对于目前的电源IC工艺,负电压很难被简单的采样处理。
内部电流检测允许在任何时候监测电流,如PWM导通时间,以及快衰减和慢衰减过程中。虽然它增加了驱动IC的复杂性,但内部电流检测大大降低了系统成本,因为外部的采样电阻不需要了,这些电阻非常大且昂贵,价格通常和驱动IC差不多!
MP6500/MP6600步进驱动IC自适应电流控制方案
MPS公司的MP6500系列双极步进电机驱动芯片,集成内部电流检测,很好的取代了传统廉价的峰值电流控制双极步进电机的驱动IC。不需要外部电流检测电阻,只需要一个接地的小型、低功耗电阻去设定绕组电流峰值。内部电流检测依赖于精准的功率管及相关电路的匹配设计,可以保证始终准确采样绕组电流,从而提高步进电机的运行质量。
通常情况下, MP6500工作在慢衰减模式下。然而,当一个固定关断时间结束,慢衰减结束后,如果当前绕组电流仍高于预期水平,快衰减模式会被开启以用来迅速减小驱动电流到所需值。这种混合控制模式,使得驱动电流快速下降到零,同时又保证平均电流尽量接近设定值。
当step跳变时,快衰减就被采用使得当前电流迅速被调整到零,如图3所示。如果电源电压高,电感值低,或所需的峰值电流幅值很低,电流很有可能高于设定值。由于blanking time,每个PWM周期都会有一个最小导通时间,此时许多传统的步进电机驱动器无法控制绕组电流。如果发生这种情况,MP6500会不断采用快衰退模式来保证绕组电流一直不超过设定值(见图4)。
图3:MP6500的自动衰减模式(step跳变时)
图4:MP6500的自动衰减模式(低电流情况下)
这种自适应衰减模式与只使用慢衰减模式相比,平均电流的变化比较小。由于快速衰减模式只用来控制驱动电流低于设定值,误差比在整个PWM关断时间采用快衰减模式要小的多。
这种控制方法的优点是,对于不同的电机和电源电压,用户不需要做任何系统调整,衰减模式是完全自动调整的。而传统的步进电机驱动,对于不同应用,必须调整衰减模式甚至PWM关断时间,以得到最好的运行质量。
使用了这种电流调节方法,MP6500可以确保整个周期的平均绕组电流都准确稳定(见图5),明显改善了电机的运行质量。
图5:MP6500输出电流波形
-
步进电机
+关注
关注
152文章
3131浏览量
148188 -
电流控制
+关注
关注
4文章
148浏览量
23239
发布评论请先 登录
相关推荐
安川伺服控制器MP系列优势特点及行业应用
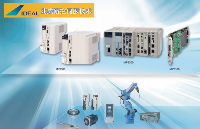
flash MP3语音IC芯片厂介绍儿童电子琴智能语音方案
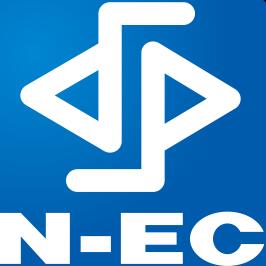
MP6500数据手册# 集成内部电流采样功能的 35V, 2.5A,步进电机驱动器
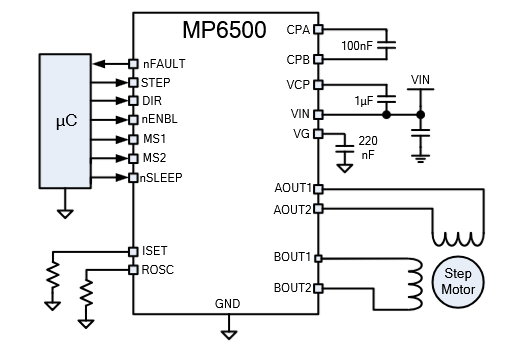
自适应电流焊接控制器:精准调控,高效焊接
国产PLC崛起:基于STM32MP257FAK3的工业控制方案
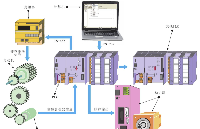
基于AR1335和i.MX8MP的视觉方案
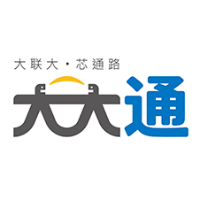
强大视觉方案:i.MX8MP与AR0144的完美结合
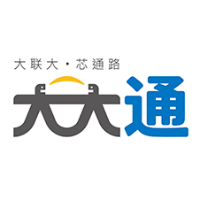
轩展科技 相比MP1010M-VC,腾龙MP3010M-EV有哪些优势?
步进电机如何自适应控制?步进电机如何细分驱动控制?
如何在自己的固件中增加wifi自适应性相关功能,以通过wifi自适应认证测试?
#参考设计#基于MP279x IC大电流 7 至 16 节串联电池管理系统解决方案
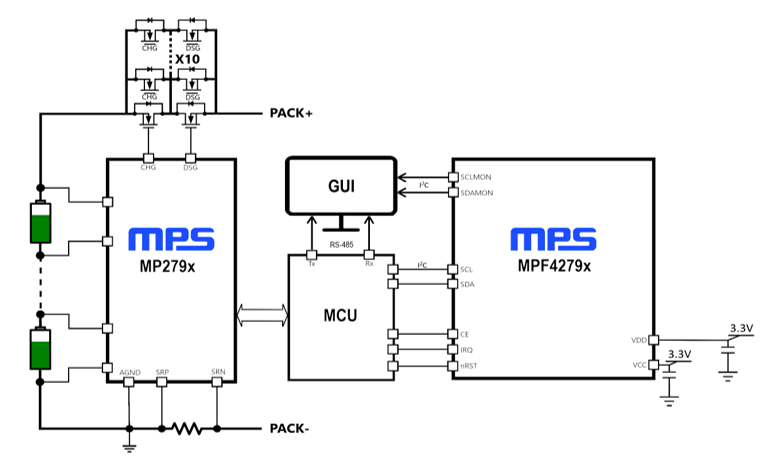
基于非线性自适应学习控制器的四轴飞行器避障方案
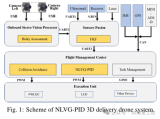
昂科烧录器支持MPS芯源半导体的多相控制器MP2891GQN
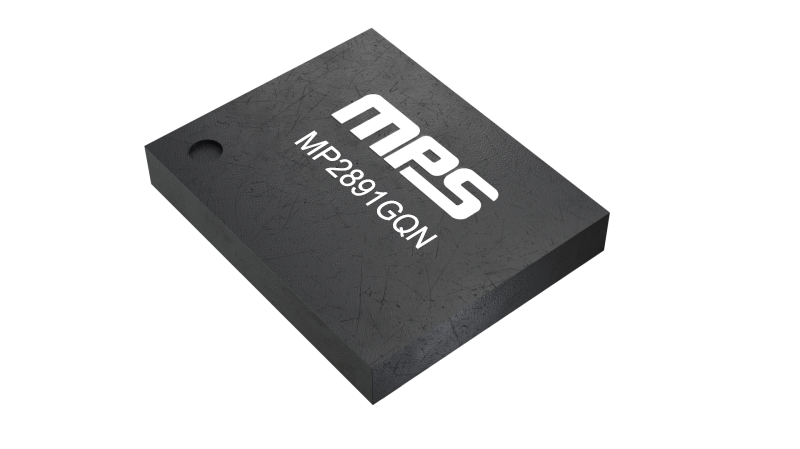
评论