由于美国将从2021和2024年起将颁布温室效应气体排放法规并建议实施欧Ⅶ废气排放标准,加重了商用车柴油机制造商降低CO2排放的压力,为此必须提高发动机效率,同时降低机械系统摩擦。而用于发动机低速化的新的变速器设计又使任务变得更加繁杂,而由活塞、活塞环和气缸套组成的活塞系统对于提升耐磨性和降低摩擦起着重要的作用。
1 初始状况
为实现降低摩擦的目标,通常会以活塞系统(PCS)为研究对象,其产生了源于基础发动机的大部分机械损失,即使该系统的摩擦损失已相对较低,但是仍能进一步优化摩擦。采用类金刚石碳涂层(DLC)活塞环与光滑气缸工作表面相匹配能降低活塞环-气缸副的摩擦,而具有最佳裙部接触和低摩擦裙部涂层的紧凑型活塞则可减小活塞的摩擦,此类活塞系统具有最多将摩擦降低达37%的潜力。除了数字优化方式之外,有一种创新方法是按照浮动缸套原理测量单缸柴油机的摩擦力,测试机型以30 kW/L升功率的13 L发动机为基础,并在整机上进行曲轴箱窜气量和机油耗的测量。
2 活塞设计
鉴于降低商用车发动机的摩擦功率,KS Kolbenschmidt公司提供了定制活塞的结构,以满足不同用户的需求。在现有情况下使用通过压缩高度以降低摩擦的Weldteks式活塞设计,通过较小的高度以减轻活塞质量,对侧压力产生较为有利的影响,并与加长型连杆相互配合以降低发动机摩擦功率,而通过摩擦功率优化的较小活塞环组就能将活塞环区设计得较为紧凑(表1)。
表1 用于2021车型年度LF PCS的活塞设计
采用数字模拟优化活塞设计就能使活塞在发动机运行中实现协调变形,与传统设计相比还能降低摩擦,而且通过数字模拟可将活塞裙部廓线导致的接触压力和摩擦优化到最低程度。现代数字模拟优化工具能确保活塞设计所必需的疲劳强度而无需多次重复优化设计。
与量产活塞相比,Weldteks活塞能使压缩高度缩短17 mm,从而使质量减轻达23%,而且还因发动机气缸体高度也可相应降低17 mm从而进一步扩大了减轻质量的效果。
3 活塞摩擦模拟
现代商用车发动机实现低速化的趋势相应提高了采用有限元(FE)模拟设计低摩擦活塞的要求。为了即使在低转速时也能确保活塞裙部完全建立起流体动力学压力,在活塞设计上需仔细地调整活塞的细节轮廓,并结合机械负荷和热负荷所引起的变形,加工的轮廓就决定了活塞与气缸之间接触区域的机油油膜分布。与多体系统算法相结合,弹性流体力学接触模型考虑了活塞在气缸中的运动以及随曲轴转角变化的由气体压力和惯性力所产生的负荷。作为对上述效果的补充,摩擦损失计算包括了转换到混合摩擦状态时表面粗糙度的影响。
1 025 r/min的转速和100 kW的功率对于道路行驶工况下燃油耗的降低具有重要意义,采用图1中所示的低摩擦(LF)活塞显示出了明显的优势。良好的流体动力学压力的建立导致在360°CA和540°CA之间工作行程中的机油油膜厚度得以增加。在裙部表面被机油润湿的同时,LF活塞的累积平均摩擦压力从量产活塞的3.1 kPa降至2.0 kPa,即降低了35%。
在额定功率时采用LF活塞方案的总体优势是其具有相同的数量级,但是在侧压力较高的工作行程中其主要是由混合摩擦损失减少引起的。不同运行条件下的模拟节油效果通常在0.11%~0.20%范围内,对此与OEM制造商在商用车行驶循环中的测量值0.15%具有良好的一致性。
图1 道路行驶时量产和LF活塞的机油膜分布和平均摩擦压力
4 活塞环设计
针对降低工作表面摩擦的目标,利用降低活塞环高度、减小切向力和应用DLC涂层等方法,而设计出了具有较低摩擦的LF活塞环组(表2)。与量产活塞环相比,LF活塞环组的第一和第二道活塞环具有较小的环高,分别为2.5mm和 2.0 mm,以此相应减小了活塞环内径上的气体压力和对气缸的接触表面。刮油环的高度并未得以改变,当然其圆锥形环岸明显减小了有效接触表面,因此对机油进行剪切的有效表面将变得较小,并且降低了流体动力学摩擦力。
表2 活塞环设计
总摩擦较小的活塞环组使切向力降低了33%,从而降低了摩擦。正如在活塞系统试验结果一节中所言,在整机上成功地防止了因活塞环张力过小而使机油耗增加的风险。总体而言,横截面较小的活塞环对其形状贴合能力产生了较为有利的影响。
第一道活塞环和刮油环的工作表面均涂有DLC涂层。由于DLC涂层的摩擦系数较低,降低了混合摩擦而产生的摩擦力,同时因DLC涂层具有较高的耐磨性,使活塞环能比量产的铬基方案更长地保持最初的工作表面廓线,这类轮廓运行时间更为持久,即使经过长时间的运行仍能保持低摩擦的优越性。因此,LF活塞环组满足了现代商用车柴油机对可靠性和耐磨性的要求。
5 气缸工作表面设计
由活塞环形成的光滑摩擦副与有利于降低摩擦的涂层和用于活塞环-气缸套低摩擦的气缸工作表面相配对,目前已应用于汽油机,而对于其在商用车柴油机领域的应用而言,还必须具有较高的抗拉缸性能和耐磨性,而且耐腐蚀性也会带来相关优势。KSKolbenschmidt公司的铁基金属丝热喷镀能满足这些要求:最佳的均匀分布的气孔具有足够的含油容积并可减少磨损,而硬质组织和合金元素则可满足耐磨性和抗腐蚀性的要求。
气缸套镜面珩磨工作表面可减小摩擦系数,其优先选择的配对工作对象是DLC涂层活塞环,其不含合金成分,与气缸工作表面上的旋转喷涂单金属丝涂层(RSW)进行匹配工作。图2示出了RSW气缸套工作表面巴氏干涉仪的照片,这种涂层与表2中的LF活塞环组配对成功地经受了机油耗、疲劳强度和降低摩擦等方面的考验。
图2 气缸工作表面:RSW涂层和镜面珩磨
6 活塞环摩擦模拟
必须预先为DLC涂层活塞环和气缸镜面珩磨RSW涂层配对的新摩擦副拟定模拟边界条件。为测定摩擦系数在活塞环-气缸摩擦仪上测试Stribeck曲线并予以评估,由表面巴氏干涉仪分析模拟微观流体动力学摩擦系数,应用一种全新开发的Kori3D方法进行摩擦模拟。
图3示出了LF活塞环组降低摩擦的模拟结果与量产活塞环组的比较。在具有代表性的道路行驶工况点和当前变速器设计的情况下LF活塞环组摩擦可降低达21.8%,而在未来用于低速化的变速器速比情况下则可降低26.8%。
在额定功率情况下活塞环组摩擦可分别降低28.6%或37.6%。在所考察的运行条件下降低摩擦主要归因于LF活塞环组的混合摩擦较小,其影响因素是LF活塞环组的切向力较小以及DLC涂层与RSW涂层摩擦副的摩擦系数较小,而且RSW气缸工作表面较小的粗糙度明显减少了相对运动时的固体接触。
图3 额定功率和道路行驶时的活塞环摩擦
按照发展趋势,LF活塞环组与RSW气缸工作表面之间的流体动力学摩擦将会有所增加,因为气缸光滑的RSW工作表面较小的粗糙度使得活塞环与气缸之间润滑油膜较薄,当然LF活塞环组的润湿接触表面减小补偿了流体动力学摩擦方面的缺陷。
7 活塞系统的试验结果
在一台2015车型年度商用车柴油机上进行由Weldteks活塞、DLC涂层LF活塞环和RSW气缸套组成的活塞系统(LF PCS)的性能试验。为了补偿活塞压缩高度降低而使用了加长连杆。图4示出了LF PCS和量产型的机油耗和曲轴箱窜气量及其共同的限值线。两种活塞结构型式的机油耗都相对较好,而LF PCS的曲轴箱窜气量却比量产型的具有明显改善。
图4 LF PCS机油耗和曲轴箱窜气量在
量产条件下与量产方案的比较
KS Kolbenschmidt 公司采用一台按浮动气缸套原理工作的单缸柴油机来测量活塞系统的摩擦力。这种供测量用的发动机气缸由轴向方向上的4个力接收器支撑着,按照Furuhama方法(译注:以日本发明者名字命名的一种测量摩擦损失的方法)气缸压力的轴向分力在气缸上端由补偿牵引来平衡,而气缸工作表面通过改变使用的合金、涂层和表面轮廓而予以调整。
图5示出了在1 000 r/min和9 MPa气缸峰值压力时在浮动气缸套中测得的量产和LF PCS活塞系统在整个工作循环中的摩擦力曲线,从中可以清楚地看出LF PCS活塞系统在工作循环所有曲轴转角相位时的优势,特别表现在压缩和膨胀阶段,其中减小的接触表面与较低的摩擦系数相结合产生了较小的摩擦力,从而导致了较低的平均摩擦压力。
图5 在1 000 r/min和9 MPa气缸峰值压力时
在浮动气缸套中测量的摩擦力
8 活塞系统中的摩擦
图6以平均摩擦压力示出了在额定功率和道路行驶运行条件下的活塞系统摩擦,左侧两个柱状图标表示在当前变速器速比运行条件下的摩擦损失,而右侧两个柱状图标则分别表示为2021年美国温室气体法规设计的未来变速器速比下低速化机型的摩擦损失,蓝色代表活塞摩擦,红色代表活塞环-气缸副摩擦。因为量产型活塞已实现摩擦优化,为了实现进一步改善,特别是针对低速化作为可能行之有效的措施仅关注优化整个活塞系统。减小活塞裙部接触表面并与非常光滑的气缸工作表面相匹配,两对摩擦副的摩擦份额至少能降低22%。
与量产活塞相比,根据运行条件的不同LF PCS活塞系统明显降低了平均摩擦压力,在当前的变速器设计和道路行驶条件下可降低25%,而在未来的变速器设计和额定功率条件下则可降低36%。在道路行驶条件下摩擦至少降低25%。若在损失功率平衡中考虑到低速化特征的话,则在道路行驶中LF PCS活塞系统仅损失0.148 kW,而量产活塞系统在当前的变速器速比情况下却要损失0.234 kW,这相当于具有37%的优势,此时LF活塞仅呈现微不足道的混合摩擦损失。
图6 活塞系统的平均摩擦压力和
混合摩擦份额
为了在较低发动机转速下(在未来变速器速比下低速化)达到相同的输出功率,必须具有较高的气缸峰值压力,以此加大了混合摩擦份额,正如图6下方圆形蛋糕图例中所示的那样,LF PCS活塞系统有效补偿了量产活塞系统在低速化时混合摩擦的增加。
图7示出了预测的LF PCS活塞系统相对于量产活塞系统所降低的CO2排放:额定功率时为0.27%和0.40%,道路行驶时为0.33%和0.38%。
图7 LFPCS活塞系统降低的CO2排放
9 结论
通过改善活塞系统的摩擦状况以降低燃油耗是一种挑战,特别是在考虑未来发动机设计低速化的情况下,其成功的关键是活塞系统优化方法以及应用模拟方法以采取最有效的降低摩擦措施优化和组合系统。
德国KS Kolbenschmidt公司与日本Ricken公司采用摩擦优化的活塞和活塞环设计,并在活塞裙部、活塞环工作表面(RickenDLC)和气缸工作表面(镜面珩磨RSW)上应用最新的降低摩擦涂层,达到了使摩擦降低达37%的效果,通过用于商用车的单缸测试发动机证实了发动机运行时可充分降低摩擦的实际效果,整机试验也证实了其在机油耗和曲轴箱窜气量方面的良好效果。
-
柴油机
+关注
关注
1文章
171浏览量
26256 -
摩擦
+关注
关注
0文章
13浏览量
7655
发布评论请先 登录
相关推荐
农用柴油机原理使用及维护 pdf电子书
车用增压柴油机VNT和EGR系统匹配试验研究
柴油机电控燃油喷射系统开发与研究
6105柴油机连杆及连杆螺栓迁都分析
柴油机预混合燃烧机理的研究
[原创]2011中东商用车展/迪拜商用车展/商用车零配件展/商用车
[原创]2011中东商用车展/迪拜商用车展/商用车零配件展/商用车
柴油发电机组常见的错误操作(一)
柴油机使用中应注意的问题
闻香识女?听音辩故?10种听声音知道柴油机故障的方法
农用柴油机原理使用及维护
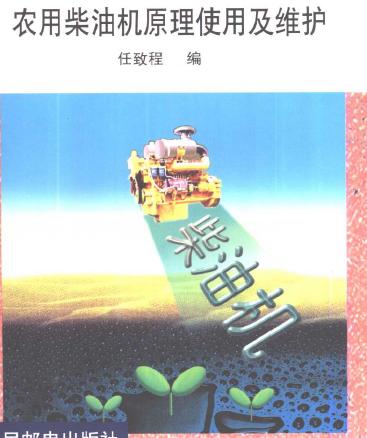
基于KPCA-SVM的柴油机状态识别方法
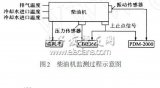
柴油机转速信号动态模拟电路分析与设计
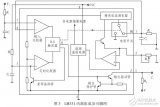
评论