柴油机的热效率通常可比汽油机高出30%,因此其在欧洲以及印度等地得以广泛应用。近年来,由于柴油机的噪音及振动现象有所改善,排放性能有所提升,因此,其在日本国内市场的保有量正逐渐增加。本文主要介绍乘用车用柴油机的相关技术特征。
柴油机向经压缩后的高温空气中喷射燃油,并通过压缩点火方式使其着火燃烧,目前以向气缸内直接喷射燃料的直喷式为主流技术。
与汽油机不同,燃烧状态下的柴油机燃烧室内只有空气。而当空气分布于燃烧火焰锋面与气缸壁之间时,其会吸收燃烧热量并进而膨胀,产生向下推动活塞的压力。同时,由于其抑制了气缸壁的热量释放,因此与汽油机相比,柴油机的热效率更高。由于具备上述基本特性,柴油机在商用车领域得以广泛应用。
早期有一类柴油机,其向在缸盖上设置的副燃烧室内喷射燃料,但是该类柴油机无论是压缩行程还是膨胀行程,泵气损失都较高。如要对燃料喷射量进行精细管理,就需要重点改善副燃烧室的技术劣势。因此,大型商用车从早期就开始采用向燃烧室内直接喷射燃料的方式,以此提升发动机的热效率。
乘用车用柴油机已在欧洲地区使用多年,并占有较高市场份额。但是,由于柴油机在噪声以及排放性等方面的性能仍有待改善,在日本国内市场除了四轮驱动(4WD)等重视车辆可靠性及通过性的车辆外,在过去较长的一段时期内,客户对柴油车可谓敬而远之。柴油车基本不会被优先选用,同时也几乎没有进口柴油车进入日本国内市场。
然而,随着排放法规对尾气排放清洁度要求的不断升级,日本国内市场转而开始重视柴油机的存在价值。在高响应性及高转速的技术要求前提下,需尽可能改善柴油机的排放性能、并进一步有效控制整机的振动问题。经相关改进后,日本国内的柴油机产品取得了显著的技术进步。因此,日本国内配装有柴油机的乘用车数量也在稳步增加(图1)。
图1 直喷柴油发动机系统图
近年来,柴油机不仅需满足严苛的排放法规,还应不断提升其燃烧效率,因此除了柴油机本体以外,还相应配置了涡轮增压器、EGR、SCR催化剂以及DPF等后处理系统。其中燃料喷射装置为柴油机的关键技术部件,近期则更多采用共轨式喷油装置。
最近上市的乘用车用柴油发动机主要分为三大类(表1)。
表1 乘用车用柴油发动机分类
日本国内应用于大型车辆及皮卡的柴油机,其排量为3.0L左右。主要配装于大型车辆或皮卡车、大型4WD车辆,该类柴油机不仅气缸数量较多,其喷射器、涡轮增压器、排气后处理系统均采用了最新技术(图2)。同时中高档及以上的车辆也会选用V型发动机。柴油机排气量较大,从而排放气体中的NOx会相应增多,因此普遍的应对措施是配装柴油颗粒捕捉器(DPF),同时加装尿素SCR系统。
图2 丰田汽车的柴油机“1GD-FTV”
(a)排量2.8L的直列4缸柴油机(b)活塞顶
日本国内应用于中型车及SUV的柴油机保有量近年来也在快速增长。在直列4缸以下、排量为2.0 L左右的柴油机上组装可变容量涡轮或二级涡轮,即可达到与大排量柴油机相当的扭矩。该机型在欧洲市场多用于C级和D级乘用车(图3)。排气后处理除采用SCR技术以外,还可用还原催化剂吸附NOx。
图3 瑞典VOLVO公司柴油机“D4”
该发动机排量为2.0 L,拥有与排量3.0 L的直列6缸涡轮增压汽油机同等的输出扭矩,可达到JC08法规要求的2倍以上。
应用于轻型车的柴油机,是基于排量小于1.5 L的柴油机的基础上使用压电式喷射器或NOx吸附还原催化剂,使整机成本有所降低,并可确保车辆具备强劲的动力性能以及出色的燃烧效率(图4,5)。
(a)发动机本体(b)活塞顶部设计
图5 五十铃在印度市场使用的
小型柴油发动机“E08A型”
该柴油机排量为0.8 L,配备有直列2缸涡轮增压器。配装于五十铃印度子公司Maruti Szuzuki公司生产的轻型乘用车“Celerio”。该款车型在印度本土的油耗为27.62 km/L。
尽管柴油机的热效率较高、二氧化碳排放低于汽油机,但是如要达到美国的“Tier2Bin5”、欧洲的“Euro5/6”,日本国内的“后新长期排放法规”所规定的较为严苛的排放要求,需进行精确的燃烧控制。而目前实现上述要求的核心技术则是喷射器的喷射控制技术。与汽油机不同,柴油机在燃烧时无需采用火花塞点火,因此主要通过燃料喷射时刻以及喷射量来控制柴油机机燃烧过程。
直喷式柴油机有5种燃料喷射方式(图6)。在进气行程中期到压缩行程初期进行预喷射,可以提升柴油机的点火性能。当进入速燃期之后,NOx的生成量有所增加,当达到一定的高温条件时,可通过喷射少量燃料的间隙喷射方式来加速燃烧过程。
图6 多段燃料喷射图示
在压缩行程内,为了提升点火性能,需进行预喷射,随后进行间隙喷射,再开始主喷射,并于缸内开始进行混合气的燃烧过程。后喷射是使主喷射后燃烧产生的PM进行再次燃烧。其喷射目的在于调整排气温度,提高催化剂温度。
随后,在压缩上止点附近才开始进行主喷射,使燃烧过程正式开始。此时如果再喷射大量燃料,会导致部分领域的燃料密度过高,使附近区域成为产生PM的重要源头,因此在气体膨胀行程中所附加的后喷射可有效稳定气体燃烧。
后喷射有着将主喷射产生的PM再次投入燃烧的作用。因此在膨胀行程结束时,为了进一步促进催化剂的排气净化性能,需要进行少量的后喷射。
通常而言,乘用车用柴油机,其转数上限为4 500 r/min,从进气行程到压缩、膨胀行程,需要在2/100秒内完成约5次的燃料喷射,并使每次燃料喷射时间控制在1/1 000秒内。
1关键是燃料喷射的高压和快速响应性
为了实现少量燃料在短时间内的正确喷射,就需进行燃料喷射控制。因此柴油机的燃料喷射压力在近10年内得到飞速增长。
部分大型商用车也采用喷射单元,而目前主流技术是使用可一次性供给燃料的共轨系统,并通过共轨将燃料输送至喷射器(图7)。
图7 共轨系统示意图
通过高压泵,将加压至180~240 MPa的燃料送至燃油轨,然后通过各个喷嘴实现燃料喷射供给。并且在燃料罐上设置有低压侧的燃料泵,可向高压侧的泵压送燃料。
为了将喷油器的喷射时长控制在1/1 000秒内,就需使得新喷射器比传统喷射器具备更好的响应性。压电式喷射器的特点是响应速度快,自2000年开始在日本国内投入使用以来,随着喷射压力提高,相应产品的性能亦在不断提升(图8)。目前喷油器已经进化到第四代产品,采用层叠的压电元件单元直接驱动针型阀的结构。
图8 压电式喷油器
利用压电元件实现喷嘴开闭运动。最新的压电式喷射器,通过压电元件的运动可直接驱动喷嘴开闭,因此其具备更高的响应性。
直喷汽油机的燃料喷射压力可达30 MPa,比传统的柴油机更高,但是直喷柴油机的喷射压力则明显更高,大型商用车用柴油机的实际喷射压力可达240 MPa。
拥有200 MPa燃料喷射压力的第四代压电式喷射柴油机,其在单次燃烧过程中最多可喷射9次,反应速度仅有0.1 ms,也就是说其喷射间隔时间可控制在万分之一秒内。
近年来,电磁式喷射器也在不断进行改良及优化,目前已经实现了高响应性的技术要求,并可以200 MPa的喷射压力进行工作,在每次燃烧过程中可进行5次燃料喷射,柴油机燃烧喷射压力增高是因为采用了多孔喷嘴,以此可使得燃料雾化效果更佳。
为了提高压缩比,传统的柴油发动机的活塞头顶部比较平坦。与此不同,当前的主流技术是充分利用活塞顶部的内侧空间。随着直喷技术的发展,活塞顶部的凹坑型燃烧室已经取代了传统的副燃烧室,并可在压缩上止点位置形成较小的燃烧室,同时可调整被燃料雾化颗粒的分布范围。
活塞材料一般选用轻量的铝合金,不过目前也开始使用具有高强韧度、高耐热性和厚度较薄的钢制活塞。
2必须采用涡轮与EGR的组合方式
最初,排气压力较高的柴油机通常会与涡轮增压器相匹配。但是为了降低NOx排放并减少泵气损失,对于当前追求低压缩比的柴油发动机而言,涡轮增压技术可谓必不可少。因此,日本国内近年来生产的柴油机都会配装有可变容量涡轮、可变喷嘴涡轮、二级增压等相关技术设备。
废气再循环(EGR)是柴油机提升排气性能和燃烧效率所不可或缺的机构设备。在EGR过程中,进入燃烧室的惰性气体越多,燃烧效率则越高;但是,如果燃烧室内排气浓度过高,也会产生PM,对喷射的燃料与氧气的结合造成负面影响。
高效率柴油机与轻量化及高转速关系密切。由于轻质燃油的着火点在250 ℃左右,即使不采用20以上的压缩比,轻油也可自行着火燃烧。但是,如果压缩比下降,则会对冷机状态下燃烧的稳定性造成影响,针对上述问题,普遍选择采用内部EGR或火花塞等辅助热源。
压缩比的机械性降低与活塞的行程减小有关,作为往复运动机构,该方式对降低摩擦损失具有一定的提升效果。目前也有该类技术诉求,即通过柴油机低压缩比化实现快速响应的加速需求。
对于乘用车用柴油机来而言,利用低压缩比和低振动化处理实现高转速的案例不在少数。为了解决振动问题,采用平衡轴以及可吸收振动的自适应液压式发动机支架,以此消除高转速区域的共振现象。
为了在低压缩比状态下进行高效燃烧,还有效利用了燃烧室内的空气流动。例如:在低转速时,提高空气流速,燃烧室内形成滚流及涡流等气流运动,为了加快燃烧速度,部分柴油机在进气口采用涡流阀或者单个阀门关闭的结构。
当前,乘用车用柴油机的压缩比通常设定为16左右,但是在高负荷工况下利用涡轮增压技术,可有效提升实际压缩比。此外,在高负荷时通过增压方式以增加空气量并增喷燃料,该措施会造成排气成分的暂时性增加,而NOx吸附催化剂和DPF能够吸收上述气体,以此可降低废气排放。
-
柴油机
+关注
关注
1文章
171浏览量
26265 -
涡轮增压器
+关注
关注
3文章
90浏览量
11683
发布评论请先 登录
相关推荐
柴油机电控燃油喷射系统开发与研究
发动机在线信号处理和工作过程控制
为生物质气体燃料发动机开发测量控制系统方案
基于CAN总线的汽车发动机智能电子控制器研究
与柴油机效率持平的汽油发动机
基于瞬时转速的发动机故障诊断研究
CAT C9型号发动机喷射技术分析
双燃料电控发动机性能研究
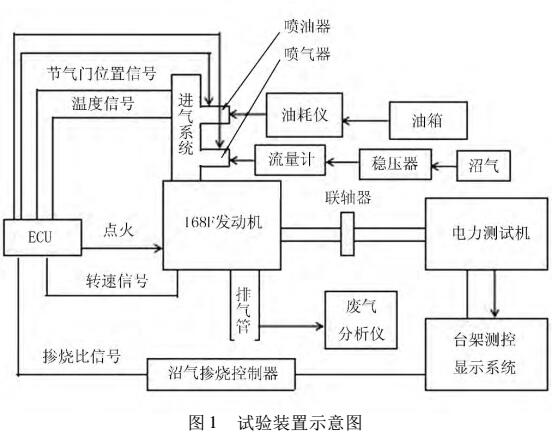
发电用沼气/汽油双燃料电控发动机性能研究
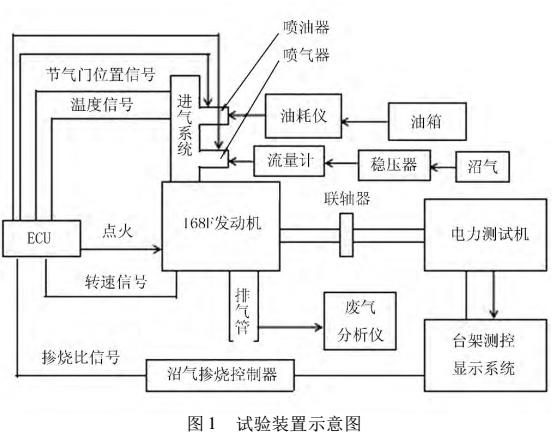
评论