降低排放和改善能耗是决定道路用和非道路用发动机未来发展方向的重要因素。通过采用天然气替代柴油以实现燃料灵活性。为了满足未来的需求,发动机将变得更加复杂。此外,基型机上将采用更先进的附属系统,用来进行回收废热、气态燃料供给、排气后处理及其控制。增加发动机的复杂性将会增大整个动力系统的尺寸、质量及成本。未来发动机发展的另一个关键因素是优化基型机,满足未来的排放法规(包括CO2)要求,通过优化基型机弥补附件增加带来的尺寸、质量和成本的增加。发动机缩缸强化、新材料、减小摩擦、先进增压和燃油喷射系统技术等方面已在轻型车辆领域显示出潜力并已处于具体实施阶段。介绍未来商用和工业用发动机基型机的改进方案及潜力,描述这些技术如何改善商用和工业用基型发动机,以满足未来排放法规及燃油效率要求。
0前言
近20年内,商用车辆柴油机污染物排放限值要求愈加严苛,这已成为发动机技术发展最根本的推动力。柴油机的主要排放物为氮氧化物(NOx)及颗粒物(PM),而这两者的控制是相互冲突的。目前商用车辆上重型柴油机排放标准要求降低发动机全工况范围(包括高负荷点)的NOx和PM排放。一种有效降低高负荷工况原始NOx排放的措施是在发动机上提高废气再循环(EGR)率,并保持空燃比恒定,可使PM排放处于限值以下。
此外,提高喷油压力也有助于降低PM排放。基型机不仅要满足未来排放法规要求,还保持甚至提高比扭矩及功率输出,这为设计带来了挑战。增加EGR率和增压压力导致缸内峰值压力提高到25MPa,增加了气缸盖、曲轴箱、曲柄连杆机构等部件的受力,需改进基型机设计和材料。较高的喷油压力要求燃油泵及其驱动机构能够承受较大的扭矩和压力。
未来,排放标准将更加关注于引起全球变暖的排放物,如CO2、N2O和CH4等。因CO2为石油类燃料燃烧的自然产物,研究关注点在于通过降低发动机部件摩擦及其他功率损失,改善内燃机燃油经济性。即使某些开发将由车辆技术负担,但内燃机仍需继续开发及优化,以实现性能、排放和燃油经济性之间的最佳平衡。
图1为过去几十年中道路用重型发动机技术及其未来发展趋势。从2014年到2017/2018年这一阶段,道路用载货车的CO2/燃油消耗率将降低20%,2020年或之后将进一步降低。为满足CO2排放限值,将在现有产品技术的基础上增加新的基型机技术。图1列出的某些或所有技术将与减小摩擦和增加热效率技术一起使用。本文介绍基型机的设计趋势,探讨基型机如何满足排放和燃油经济性限值。
1发动机缩缸强化
缩缸强化是提高发动机功率密度的技术发展趋势,要求在较低排量条件下产生相同功率。然而在不减少发动机气缸数,仅减小排量的情况下未必能够显著降低摩擦。表1对比1款中型载货车用发动机的2种设计变型。图2为缩缸强化对发动机摩擦的影响。
如按比例减小缸径和行程以保持行程/缸径比不变的缩缸强化方案,需要进行二级增压,这将导致缸内峰值压力增大约3MPa。缸径虽然变小,但气体力基本保持不变。因此,减少轴承直径不可能降低轴承摩擦及轴承润滑油流量。在相同的发动机转速下,只有缩小行程,降低活塞平均速度才能起到减摩作用。这个正面效果部分地被流过二级涡轮增压器的附加机油消耗掉,后者会导致较高的机油泵驱动功率。曲轴、气门机构、水泵和交流发电机产生的摩擦保持不变。摩擦评估表明,摩擦扭矩差异很小,仅在运行工况点转移可实现热力学上的燃油耗优势。
通过减少气缸数量实现发动机缩缸强化,能够显著降低发动机摩擦。采用二级增压和应对较高峰值压力及功率的措施必将显著提高发动机成本。减少气缸数量将缩减部件数量,平衡所增加的成本。图3示出了发动机成本的比较,表明如果通过减少气缸数量实现排量降低,缩缸强化在经济上具有相当的优势。
相对于6缸机而言,采用平衡轴以消除2阶自由惯性力优化4缸发动机噪声-振动-平顺性(NVH)性能的方案具有成本优势。考虑到摩擦和成本降低的潜力,采用大缸径4缸发动机代替常用6缸发动机将获得更大优势。大型发动机通常采用单缸排量为2L的4缸发动机,可实现300kW的功率性能级别,这一级别是40t级长途载货车用动力系统的主要级别,因而在减小生产成本方面具有相当大的潜力。4缸发动机大幅度缩小的长度将为发动机舱提供更大的自由空间,用于安装排气后处理和冷却系统。
此外,应用质量平衡轴,发动机质量估计可减轻150kg左右,可直接用于增加车辆有效负荷。为了满足用户对NVH方面的要求,发动机气缸数较少而引起较高的扭矩波动是发动机开发过程的关注点。但是,商用车市场用户相对比较保守,对此类发动机的接受程度有待验证。对于乘用车发动机而言,减少气缸数量已经成为主要发展趋势。对于小型乘用车而言,更是迫切需要以3缸发动机代替4缸发动机。
2气缸套和曲轴箱技术
气缸工作表面采用热喷涂技术也适用于批量生产,图4示出了涂层技术在减摩方面的潜力。在标定转速时等离子涂层缸套采用的平均摩擦有效压力(FMEP)相对基准铸铁缸套降低大约12%。在其他研究中有提到在标定负荷摩擦减小达到20%的情况。这一技术起源于乘用车发动机,之后在商用车辆和大缸径发动机上进行了试验。另外,不受缸套基体材料限制,可自由选择工作表面材料。
轻型/中型发动机常采用集成缸套的曲轴箱,被称为母体气缸。重型发动机采用母体气缸代替湿式缸套,可大幅降低曲轴箱生产成本及气缸间距(图5)。在发动机大修时,已磨损的气缸可以镗掉,喷涂1层新的涂层,不必更换各个气缸套。为此,不需要采用直径稍大的专用活塞。然而,进行这样的大修工作需要相应的生产设备。在具有良好制造基础设施的技术成熟市场可实现这一技术。
3曲轴和曲柄机构设计
曲轴主轴承和连杆大头轴承是发动机摩擦的重要来源。图2示出发动机不同部件的相对摩擦扭矩,曲轴摩擦占发动机总摩擦的14%。在标定转速和负荷时,此部分将增加到25%以上。通过减小主轴颈和连杆轴颈直径能够降低曲轴摩擦。图6示出了将柴油机主轴承与连杆轴承直径比和主轴承直径大小对比获得的统计数据。
主轴承直径减小能够降低流经轴承的机油量,减小对机油泵油量的需求,降低其驱动功率损失。因为减小主轴承直径与提升功率和缸内峰值压力相冲突,所以需要处理好连杆轴承的设计,使之不产生反作用。图7为FEV公司提出的独特设计,主轴承直径的减小是通过增加连杆轴承直径平衡,直到连杆轴承直径增加到与主轴颈直径相等为止。这种方法能够在保持曲轴刚度的同时降低整体机油消耗量,从而减小机油泵流量需求和驱动功率损失。
另一种减小曲柄机构摩擦的方法是在气缸轴线和曲轴轴线之间引入偏移量。采用运动仿真可预测总摩擦力和优化偏移量。图8示出有偏移量的曲轴与无偏移量的基线活塞侧向力随时间变化的仿真结果比较。曲轴偏移使燃烧产生的摩擦力峰值降低到50%左右。压缩行程摩擦力相应增加,然而摩擦力大小低于燃烧过程中的摩擦力,净作用使整体摩擦力及扭矩均降低。使活塞力最小的偏移量精确值需针对每一种发动机设计,根据仿真确定,并且因曲柄机构几何形状不同而略有变化。
4可变压缩比(VCR)
高增压和高比功率将产生较高的缸内峰值压力,在这种情况下需要加强发动机的整个机械结构。VCR技术通过降低高负荷压缩比,成为一种可选方案,从而使缸内峰值压力不会超过现有发动机结构的允许水平。VCR系统在商用发动机上的应用前景如下:(1) 升级现有发动机性能以提高比功率,将其应用于高级游艇动力和发动机缩缸强化;(2) 限制现有发动机缸内峰值压力,引入高EGR率并改善燃油消耗;(3) 提高多燃料运行时的压缩比,具体取决于使用燃料的点火性能及十六烷值。
实际运用中已有多种VCR系统,有些是压缩比连续可变,有些只是一级变化。连续可变机构应用于现有发动机上需进行重新设计。FEV公司开发了1款适用于乘用车用汽油机和大型柴油机的二级VCR系统。在这种二级VCR系统中,连杆长度的改变是通过连杆小头的偏心轴承旋转实现的,由气体力及惯性力叠加产生的偏心力矩来调节连杆长度。这是低成本VCR方案的关键特征,无需成本昂贵及耗能较大的执行机构,所有功能部件都集成于连杆这一组件上。这种VCR系统可集成到现有发动机设计上,设计变动很少。由图9可知,偏心力矩在整个燃烧循环中有正有负,使得在2个方向上均可调节。
图10示出在1款缸径为125mm的重型柴油机在不同转速,不同平均有效压力(BMEP)条件下试验获得的压缩比切换结果。最高燃烧压力为18MPa,压缩比在14和17之间切换。结果显示在整个测试过程中,压缩比切换一致性良好,未发现部件异常磨损或裂纹现象。
5气缸盖设计
高功率密度引起的缸内峰值压力不断增加为发动机设计带来了巨大挑战,尤其是在气缸盖设计方面。材料选择、设计原理和部件形状成为设计的关键问题。增加材料强度是改善高周疲劳(HCF)特性的适当措施。因此一些制造商使用的材料已经从传统灰铸铁向蠕墨铸铁转换。以GJV450材料为例,这种材料能够很好承受缸内燃烧压力产生的高频负荷,同时在不需要像灰铸铁(GJL250)那样详细优化高负荷区域的几何形状,允许缸内峰值压力超过20MPa。相比灰铸铁,蠕墨铸铁导热性明显降低,从而引起高热负荷区域热机疲劳(主要是低周疲劳(LCF))恶化,尤其在火力面鼻梁区。
只有通过增强冷却,保证大幅减小壁厚才能够避免气缸盖鼻梁区产生裂纹。在气缸盖前期设计中,为了满足冷却要求,在确定气门位置和大小时必须特别注意为鼻梁区留有足够宽度。为了实现相应发动机寿命的热负荷循环数,需要对气门直径与换气所需流通截面积进行平衡。气缸盖高度是气缸盖总刚度的1个重要边界条件,同时也反映了允许的缸内峰值压力。图11表示缸径在90~140mm间发动机气缸盖相对高度统计结果。相对高度值为气门弹簧支撑高度与缸径之比。图中示出了可长期接受的缸内峰值压力和气缸盖相对高度间的关系。在有利条件下,采用灰铸铁材料也可实现缸内峰值压力超过20MPa的情况。蠕墨铸铁证明用强度较高的材料解决问题要更容易。
对气缸盖刚度有积极作用的另一设计特征是铸造的喷油器顶板。独立的嵌入式喷油器套为喷油器周围高热负荷区域及气门间的冷却提供了较有利的条件。此外,因水套芯可通过中心喷嘴面与外界相连,这种结构有利于气缸盖的铸造。
利用中间顶将冷却液引入重要区域,引导冷却液到关键地区的中间隔板,可以很容易地在铸造结构中实现。然而,在气缸盖结构中喷油器套不能起到支撑作用,可采用强度更高的材料加以弥补。这些影响表明,对于中等功率密度,但要求缸内峰值压力较高、寿命较高的发动机,灰铸铁材料或强度比标准GJL250材料更高的灰铸铁品种与铸造喷油器顶板相配合将成为最有效方案。同时,采用这种材料具有很高的成本效益。对于功率密度更高的发动机,气缸盖需要承受更高的热负荷,为此构建最佳的冷却边界条件,这是使用喷油器套的重要原因。极高的峰值压力需要采用蠕墨铸铁材料达到HCF耐久性要求。与此同时,随着功率密度的升高,LCF问题增多(图12)。
6配气机构布置
近年来,商用车辆发动机大多采用带有顶置凸轮轴的整体式气缸盖来代替独立气缸盖。乘用车发动机采用典型的双顶置凸轮轴及凸轮从动件设计,这在大型的商用车辆发动机上并不常见。比较包括气门机构在内的整套气缸盖的生产成本时,用扭转式气门排列、滚轮摇臂和气门横梁的单顶置凸轮轴(SOHC)方案的成本约比用平行气门排列、单滚轮摇臂式凸轮从动件的双顶置凸轮轴(DOHC)气缸盖低20%左右(图13)。只用1根凸轮轴的设计需要气门扭转式排列。采用平行的气门排列时,对距凸轮轴较远的气门的杠杆比将非常不利。
研究人员进行了一项评估SOHC和DOHC布置成本及效益的研究,以帮助改善排气后处理系统的排气热管理。该研究试验了1台商用车辆中型发动机,研究了采用不同顶置凸轮轴结构时排气后处理系统的上游排气温度。通过以下策略提高排出气缸的废气温度: (1) 不使用可变排气凸轮相位(VECP)进行DOC加热——延迟喷油正时,辅助后喷以及不使用VECP的主动增压控制;(2) 加热催化剂并使用VECP;(3) 使用进气门节流阀(ITV)代替VECP加热废气,即采用ITV加热标定。
图14示出采用上述策略提高排出气缸的废气温度与基线标定发动机的对比。显然,在发动机全负荷范围内使用VECP策略将获得最高排气温度。然而,在平均有效压力大于1MPa时,使用ITV策略将获得最高排气温度,而在发动机较低负荷时,也最接近VECP策略最高排气温度。
ITV成本要计入发动机总成本。由图15可知,相比配置VECP的DOHC机构,配置ITV的SOHC机构的成本仍然为最有成本效益的配气机构理念。然而,可变气门正时(VVT)机构增加的成本及使用第2个顶置凸轮轴附加配气机构零部件的成本高于ITV的成本。
表2列出了SOHC和DOHC机构的配气和进、排气道组合的评估。考虑到影响气缸盖性能和耐久性的各种设计准则,主观地将气门排列进行分类。相比SOHC机构,DOHC机构气门排列能达到更高性能和耐久性准则。许多使用中的中型、重型发动机仍采用SOHC机构。每个主机厂的最终决定都是在气缸盖和发动机的性能和耐久性要求与系统成本间寻求最佳平衡。
7高压燃油喷射
多年来,商用车辆发动机的燃油喷射压力不断提高。提高喷油压力将缩短喷油持续期和喷嘴的喷孔。这样有利于喷射燃油雾化,加速燃烧。提高喷油压力通常能够减少燃油消耗和PM数量。然而为了降低NOx排放,需要延迟喷油时刻,这样会部分抵消燃油消耗和PM优势。喷油压力提高时,需考虑高压泵驱动功率的增加及喷油器可能出现的漏油现象对燃油消耗的影响。
当喷油压力提高到300MPa,除了改善排放外,还可以改善燃油消耗。在部分负荷和标定输出时,从传统喷油系统改为无漏油喷油系统能降低与排放无关的燃油消耗1%。喷油压力提高到300MPa,为进一步改善NOx-PM折中和较大发动机特性范围,尤其为全负荷工况下的燃油消耗量提供了潜在优势(图16)。如果改进发动机设计,以提高缸内峰值压力,可通过改变喷油策略改善排放,从而进一步大幅降低燃油消耗。
表2 不同性能要求下配气和进、排气道组合的评估
8结语
考虑到包括温室气体排放(GHG)在内的排放法规要求,需要进一步改善商用车辆发动机设计。在当前或更低NOx和PM排放下,较高热效率和较低寄生功率损失使得重型发动机的缸内峰值压力接近25MPa。要求发动机能承受更高的气体力,促进采用优质材料,例如气缸盖和气缸体采用蠕墨铸铁材料,以及优化所选材料的HCF和LCF耐久性的设计。
现有很多措施来降低摩擦和其他寄生功率损失,可联合用于1款发动机内或单独应用,低摩擦气缸套/活塞涂层和减少气缸数量的缩缸强化(从直列6缸到直列4缸)将提供很大优势。在传统6缸机市场,寻找能接受4缸机的最终用户很重要。不过在汽车市场上具有较高功率密度的缩缸强化发动机由于燃料经济性优势已被大型乘用车和轻型载货车广泛接受。
这个趋势预期将向商用发动机领域发展。减少气缸数量和采用改进耐久性的气缸表面涂层的母体气缸技术的发动机在尺寸和质量方面的优势,可补偿为满足排放法规限值而增加的后处理系统的空间和质量。这种发动机的再制造和大修需要更高水平的技术基础设施。采用的涂层能够延长大修期,有利于用户使用。
采用主轴颈和连杆轴颈直径相等的独特曲轴设计能在提供所需刚度的同时减小摩擦损失。结合缸孔偏移技术的应用,能够显著减小摩擦。
由于改变连杆的可变压缩比技术需要改变设计的程度较小,对现有发动机的实用性颇具有优势,在缸内峰值压力、EGR和NOx排放等限值下提供额外的灵活性。
SOHC气门机构的布置与DOHC相比,具有更好的成本效益,而DOHC系统在热管理及发动机冷起动后排气催化剂的起燃时间方面具有相当大的优势。
上述技术已在试验环境下或轻型发动机上得到了验证,可应用于商用发动机上,为满足将来的排放和燃油经济性提供了方案。
-
发动机
+关注
关注
33文章
2484浏览量
69452 -
高功率
+关注
关注
1文章
192浏览量
18425 -
喷油嘴
+关注
关注
0文章
11浏览量
9093
发布评论请先 登录
相关推荐
CA1261汽车发动机悬置系统隔振的研究
发动机参数采集与分析系统的matalb仿真
汽车发动机升级产品解决汽车发动机燃烧问题。
汽车发动机电子控制系统的发展现状如何?
发动机总成包含哪些部件_发动机总成包括什么_发动机总成图解
涡轮增压发动机的优缺点_涡轮增压发动机寿命是否长
汽车发动机构造是怎么样的?汽车发动机如何维修20个详细案例分析
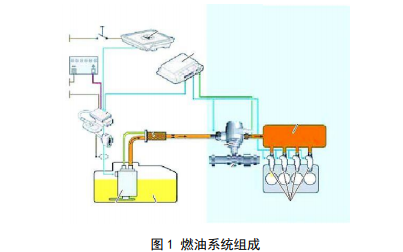
简述商用和工业用发动机未来的发展趋势
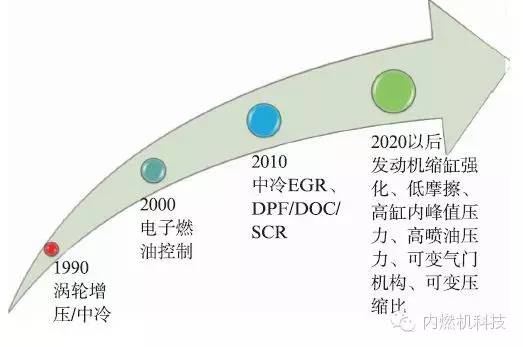
评论