只有适应各种燃油品质和不同的使用环境,柴油车才能在全球市场得到推广。因此,整个发动机管理系统应集成3项技术:(1)能适应各种燃油特性的喷油系统组件;(2)能优化燃烧过程的控制技术;(3)在各种行驶条件和使用环境下能提供高废气净化效率和高燃油效率的排气后处理系统。介绍能实现上述目标的新型柴油机管理系统。
0 前言
全球范围内针对汽车的排放法规日益收紧,从保护环境的角度出发,削减CO2排放的需求不断高涨,而汽车是CO2的主要排放源之一。因此,采取有效的排放措施以削减CO2排放量的需求已经变得极为迫切。
在提高燃油效率的技术中,除了以混合动力车为代表的利用电能作为辅助手段的汽油车外,对于热效率高、燃油经济性优异的柴油车而言,即使在至今未真正普及的日本等国,也以清洁型柴油机的全新形象掀起一股热潮。此外,在对物流行业及产业发展等不可或缺的大型商用车及农业机械领域,除柴油机外,尚未出现其他可替代的动力装置。因此,可以想象,以经济蓬勃发展的新兴国家为中心,柴油车的销售量将会不断增加。
柴油车销售区域不断扩大将对燃油系统产生诸多影响。在先进国家,为了适应以欧6为代表的强制性排放法规,喷油压力还将进一步提高。另外,2030年以后,预计化石燃料将会逐步减少,取而代之的或许是生物燃料和合成燃料,因此,在技术上也必须准备相应的对策。
另一方面,新兴国家亦会效仿先进国家,不断强化排放法规和燃油耗标准,可以想象,共轨喷油系统的应用将会不断普及和扩展,为此,必须解决因采用当地燃料而造成的燃烧波动及喷油系统零部件损坏等问题。
如上所述,作为先进国家和新兴国家未来的柴油车技术,“高压化”和“燃料多样化”等已成为重要的关键词。
1 开发理念
在这样的背景下,确定了本项研究的目标,即开发出不限地域和燃料种类的、能推进柴油车普及的发动机管理系统(EMS)。
为了开发出能在各地区对燃料具有很强适应性并具有优异性能的EMS系统,研究人员从喷油系统组件、系统控制技术及排气后处理系统应有的结构着手,进行了各种尝试。图1示出了各系统的开发理念和目标。
图1 EMS概念示意图
1.1 喷油系统组件
喷油系统的主要组件包括:(1)对于各种特性的燃料都具有高效率、低燃油耗优势,并且在安装方面也具有小型紧凑、坚固耐用特点的新型喷油器;(2)具有高效率、低燃油耗特性的高压供油泵。
1.2 喷油系统控制技术
控制单元的功能是,支持各组件发挥各自的特性,即检测燃油特性,然后据此修正喷油特性,以确保柴油机处于良好的燃烧状态,维持优异的燃油经济性。在提高排放性能的同时,确保车辆的加速性等驾驶性能。此外,一旦检测出可能对系统组件造成伤害的燃油特性,则立即发出更换燃油的警示,从而保证车辆的长时间行驶。
1.3 排气后处理系统
排气后处理系统的开发目标如下:在各种行驶条件及使用环境下,都能维持高净化效率,抑制燃油经济性的恶化,并且在不依赖基础设施的前提下发挥排气后处理功效。由此,开发出能适用于各种地域环境的高效率排气后处理系统。
综合上述3项技术的EMS系统将为普及清洁型柴油车作出贡献。下文将针对这三项EMS构成要素进行详细说明。
2 喷油系统组件
为了实现柴油车清洁、舒适的行驶,对于喷油系统组件,要求其具有高效率、高性能、高精度,以及对环境的适应性等各种性能。其中,为了适应世界各地的使用环境,不得不面对的是由不同燃料诱发的各种技术难题。因此,为了实现上述理念,关键在于如何适应燃料和使用环境方面的多样性。
2.1 喷油器
图2示出了传统喷油器的结构,由控制腔中的的压力和喷嘴腔中的压力控制喷油量。控制腔中的压力产生向下的作用力,并通过指令活塞传递给喷嘴针阀。
图2传统喷油器的结构
为了适应各地区不同的燃料特性,喷油系统组件必须具备良好的性能可靠性,从而可以燃用生物燃料、合成燃料等多种燃料,并且能在燃料品质管理不甚完备的新兴国家、甚至可能出现异物混入的特殊情况下使用。因此,为了在车辆整个使用寿命期内保证稳定工作,必须防止因沉淀物或杂质等嵌入系统滑动部位而引起的工作不良。一般认为,尽量减少滑动部位的微米级间隙是较为有效的措施。在传统的喷油器结构中,在指令活塞和喷嘴针阀处是有滑动部位的。
此外,随着高压化的进展,将燃油泄漏量降到极限是另一个重要策略。随着压力的升高,经由滑动部位或节流处的燃油从高压部位向低压部位的泄漏量将会急剧增加。高压燃油转为低压燃油时,其压力能转化成热能,所以,供油泵和喷油器的结构零部件将会因受热而达到高温。由于燃油温度的上升,燃油动黏度降低,这又将进一步促进泄漏量增加,从而形成恶性循环。
由此产生的结果是,滑动部位润滑不良,接口等树脂零件受热损坏,氧化稳定性较低的高浓度生物燃料等产生沉淀物,以及为了对多余浪费的燃料进行加压而使供油泵的做功量徒然增加,导致燃油经济性恶化。
为了解决上述课题,以适应各种燃料为目的,减少滑动部位数量,并且随着高压化的推进,尽量减少燃油泄漏量,最终开发出的全新喷油器(G4S)结构如图3所示。
图3 G4S喷油器的结构
将传统结构中设置在喷油器上部的电磁阀执行器布置在喷油器内部,在喷嘴正上方设置控制腔,从而可取消作为滑动部件之一的指令活塞。这样可以消除在滑动部位产生的静态燃油泄漏。
在传统结构中,喷嘴上部还设置有低压腔,所以在喷嘴针阀的滑动部位也会产生燃油泄漏。在新设计的结构中,喷嘴上方是高压腔,因此这一滑动部位不再会产生静态燃油泄漏。
由此,在新开发的G4S喷油器中,无论是在喷油状态下,还是非喷油状态下,静态燃油泄漏量都可能为零。
另外,喷油时控制阀动作过程中产生的动态燃油泄漏应尽可能少。为此,按全新概念设计的三通阀允许泄漏的燃油量只相当于针阀运动过程中挤压出去的容积(图4)。以下将对其作详细介绍。
图4新概念控制阀[4, 5]
传统喷油器中的控制阀是双通阀,只能开启或关闭与控制腔连通的低压油路。当开启控制阀喷射燃油时,高压燃油流入控制腔中,这部分燃油有可能会泄漏到低压油路中,产生动态燃油泄漏。
为了尽量减少动态燃油泄漏量,通过切换控制腔及与之连通的油路,在喷油过程中关闭高压油路,以防止高压燃油流入,为此必须采用三通阀。研究人员已在压电式喷油器中采用三通阀,这是因为只有压电元件的大驱动力才能实现这一结构,而电磁阀式喷油器则比较困难。
此次研发的重点是如何使电磁阀式喷油器成功应用三通阀的功能。为了实现这一目标,在控制腔中新增1块具有出油量孔的控制板。喷油时,控制板与图4中的上平面贴紧,控制腔中的燃油经由出油量孔排出,控制腔中的压力降低并开始喷油。此时,控制板将高压油路堵死,防止高压燃油流入。采用双通阀时喷油过程中产生的动态燃油泄漏量被限制在针阀上升所必需的容积范围内。喷油结束时,利用控制板上下的压差,使高压燃油从进油量孔充满控制腔,控制腔内变成高压,此时针阀下降并结束喷油。
图5是实际G4S喷油器的结构。由于取消了指令活塞,将电磁阀布置在喷油器内部,与传统喷油器相比,结构更加紧凑。并且由于取消了指令活塞,减少了滑动部件,从结构性能上来说,新喷油器在异物混入和沉淀物方面具有更高的可靠性。此外,由于在喷嘴正上方导入高压燃油,在高压燃油与低压燃油之间不存在滑动部位,所以,在结构上不会产生静态燃油泄漏。
图5 G4S喷油器的结构[4, 5]
图6是实际测量得到的燃油泄漏量。正如预期的那样,静态燃油泄漏量为零,动态燃油泄漏量可以控制在必要的最小量范围内。结果确认,新喷油器的燃油泄漏量可被降低至传统喷油器的1/6~1/8水平。
图6燃油泄漏量的比较[4, 5]
2.2 供油泵
这里介绍高压供油泵的开发过程。供油泵开发的重点是,对各地区的燃料都具有良好的适应性,防止因异物造成柱塞滑动故障,以及如何减少燃油泄漏量等。
由于进油油路的节流作用,在进油调量式供油泵中,只吸入必要的燃油量,并将其压送到共轨和喷油器中。当柱塞下行时,由于油路中节流的影响,柱塞腔中形成负压,产生穴蚀。在这样的状态下,柱塞上升,柱塞腔内的燃油被迅速压缩(快速压缩可减少热量逃逸),形成高温,这一高温促使燃料中的碳出现沉淀。
为此,本次研发中,研究人员采用预行程控制阀(PCV)结构,即全量吸入而只压送必要量的燃油,从原理上避免了沉淀物的产生(图7)。这样,在进油时没有节流作用,油路中不会产生负压,抑制了穴蚀的产生,从而可防止产生沉淀物。
图7新型高压供油泵[6]
其次,针对减少燃油泄漏的措施进行研究。随着柱塞上升,柱塞腔中的压力升高,从间隙仅数微米的滑动部位会产生高压燃油泄漏。如前所述,燃油压力越高,泄漏量就越大,并且由于压力能转化成热能,所以泄漏量越多,泵体温度就会越高。
为了达到抑制泵体温度的目的,将相对低温、低压的燃油压送到滑动部位附近的壳体中,采用了全新设计的冷却槽结构(图8(a))。由于壳体被冷却,使燃油温度降低,抑制了动黏度的降低,从而达到了减少滑动部位燃油泄漏的目的。
图8(b)示出了新结构的高压供油泵(HP7)性能与传统供油泵的比较。试验证明,在300 MPa的超高压条件下,由于设置了冷却槽,与之前相比,泄漏燃油的温度约降低70℃。这样,由于通过降低泄漏燃油的温度减少了泄漏量,使吸入并压缩的高压燃油可被有效地压送到共轨和喷油器中。与传统系统200 MPa的条件相比,HP7高压供油泵虽然采用300 MPa的高压,但却能获得同等甚至更高的容积效率(图8(b))。
图8新型供油泵及其性能比较[6]
3 喷油系统控制技术
为了最大限度发挥喷油系统组件的性能,下面将介绍支持这些组件功能的喷油系统控制技术。
3.1 智能喷油精度修正技术(i-ART)
到目前为止,研究人员已经成功开发出i-ART系统,即将压力传感器设置在喷油器内部,检测因喷油而产生的压力变动,从而推定喷油特性(图9)。将各种运行条件下的目标喷油特性作为标准模型值存储在发动机电控单元(ECU)内,通过反馈控制,使实际喷油特性与模型值保持一致,修正个体样本之间的喷油特性偏差,以及其生命周期内因工作时间延长而引起的各种波动。
图9 i-ART系统[7]
下面将介绍作为喷油系统控制技术的i-ART系统。燃油特性对燃烧特性和润滑特性都有很大的影响。所以,对于车辆性能和可靠性来说,燃油特性检测是非常重要的技术。换言之,为了确保输出功率、排放和驾驶性能,基于燃油特性实时反馈喷油定时等喷油特性参数,从而优化燃烧过程,这是最理想的方法。例如,低十六烷值(CN)的燃料着火性较差,难以实现氮氧化物(NOx)排放与CO2排放之间的平衡,如能利用i-ART系统检测燃料的十六烷值,就有可能使上述排放性能得到改善。
图10示出了利用i-ART系统检测十六烷值,并根据十六烷值反馈相应喷油定时的实例。试验条件是采用配装2.2 L发动机的车辆(车辆质量1.5 t),在新欧洲行驶循环(NEDC)下进行评价。采用CN=40的燃料时,即使喷油定时相同,由于着火时间延迟,会导致燃烧恶化。因此,与采用CN=57的燃料相比,其NOx-CO2的平衡关系会变差。因此,如能检测出燃料的十六烷值为40,则可以推定着火延迟时间,将喷油定时提前,以获得与CN=57的燃料相同的着火时间。由此,可以在燃用CN=40的燃料时,改善NOx-CO2之间的平衡关系,获得与CN=57的燃料相近的特性。
图10检测燃油特性的效果[3]
这里,介绍检测燃料十六烷值的方法。利用喷油量和扭矩随十六烷值(着火时间)的变化而变化的特性进行相关的研究。车辆在行驶过程中减速时是不喷油的,但此时如喷射微小的燃油量,则着火时间会随着十六烷值的不同而发生变化,与之相应的扭矩(发动机转速)也会随之产生变化。因此,通过检测发动机转速的变化,可以推断出燃料的十六烷值。
但是,在通常的喷油系统中,无法判断究竟喷射了多少燃油,所以,即使采用这种方法,也会因精度不高而无法付诸实用。
对此,如前文所述,i-ART系统由于可以推定喷油特性,从而可以准确地检测出喷油量。因此,可以从发动机转速的变化检测出与喷油量相应的扭矩波动,从而正确地推定燃料的十六烷值。
3.2 对于燃烧性能的考察
前文已介绍了对于各地区的各种燃料都有很强适应性的喷油系统组件及系统控制技术的开发情况。下面就对输出功率、排放及驾驶性能具有直接影响的燃烧性能,以及i-ART系统的功能定位进行说明。
前文所述对各种燃料具有极强适应性的喷油系统组件所构成的喷油系统在确保发动机可靠性方面已具备足够的性能,但在燃烧性能方面仍不是最为理想的。
此外,虽然利用缸内压力传感器等直接检测燃烧状态并反馈最佳值的方法是最为理想的[9, 10],但从成本和安装性来看,有些车辆未必能够安装此类传感器。
因此,将对燃料具有很强适应性的喷油系统组件与可以利用i-ART检测燃料特性的喷油系统控制技术结合起来,就可以构成适用于各国及各种燃料特性的最佳喷油控制系统。
另外,由于可以保证在整个使用寿命期内实现最佳的喷油, i-ART系统已成为确保燃烧稳定的一种有效辅助手段。
4 排气后处理系统
迄今,研究人员一直在致力于降低EMS的复杂程度和成本,并充分发挥柴油车的燃油经济性优势,旨在改善其市场地位,推动所谓“柴油机革命”的进展。
将“智能”(可实时反馈喷油特性的i-ART系统)与“动力”(最高喷油压力可达到250 MPa乃至300 MPa的超高压第4代共轨系统)融合在一起,最终目的是创造出迄今所没有的全新商品价值。
在这样的方针下,如前所述,研究人员将具有广泛适应性的喷油系统组件与i-ART系统的功能有效地结合起来,成功地开发出新一代的喷油系统控制技术。
然而,如果只对喷油系统进行改善,那么,即使对燃料特性的分散程度可以提出最佳解决方案,但对于减少排放和改善燃油经济性来说,其效果也是有限的。因此,要在超乎设想的燃料特性和环境条件下实现低排放性能,就必须开发出性能稳定、低成本、安装方便的排气后处理系统。
初步方案是进一步提高选择性催化还原(SCR)装置和稀氮氧化物捕集器(LNT)的性能,但最终是要实现不依赖于基础设施的排气后处理系统。
此次研究是对现有的SCR和LNT添加电气辅助手段所构成的系统可行性方案进行调查。随着法规限值的不断强化,燃油经济性改善技术的新进展,以及各种行驶循环的导入,NOx催化剂的低温净化性能变得越来越重要。为此,研究人员看准将来蓄电池电压升高及混合动力车的电动化趋势,研究有效利用电能并将等离子作为排气后处理辅助手段的潜在可行性。
图11示出了在NEDC工况,以及将来的全球统一轻型车测试循环(WLTC)工况下行驶时的催化剂进口温度。试验采用配装2.2 L发动机和自动变速器的车辆(车辆质量1.2 t)。在所有的行驶工况下,催化剂达到激活温度(200℃左右)的时间都在10 min以上,期间NOx未被净化而是直接排出。预测今后NOx法规还将进一步被强化,所以,为了降低这一过程中的NOx排放,必须采用某种升温手段。
图11各种工况下的催化剂温度
此次研究中,针对基于等离子的电气辅助手段降低NOx排放的效果进行预测评估。图12是这次试验的系统示意图。将模拟排气的气体导入等离子反应器,确认下游LNT催化剂的吸附功能。用电炉调整LNT的温度,研究各种条件下的温度特性。图13示出了试验结果。采用更细的电极,以及进一步提高电解强度的放电反应器,提高了能量效率,将低排气温度下氧化NO的燃油经济性恶化率控制在0.5%左右的极低值。图13(a)示出了与等离子供给能量相对应的NO→NO2转化效率,当施加能量达到某一程度,即使在常温下,也可以得到高转化效率。因此,可以期待催化剂具备充分的吸附量。图13(b)示出了等离子辅助LNT与尿素SCR装置的NO2净化率比较,由结果确认,即使与尿素SCR相比,等离子辅助LNT从常温开始就具备更高的净化效率。
图12试验系统示意图
图13 NOx净化性能的比较
5 结语
综上所述,为促进柴油车普及应用所制定的研发目标是成功开发不限地域、不限燃料品种的EMS。理想的EMS应由3项基本技术整合而成:(1)能适用于各种燃料的高效率、低燃油耗、小型紧凑且经久耐用的喷油系统组件;(2)为了支持喷油系统组件工作,必须具备可以检测出燃料特性、实现最佳燃烧的喷油系统控制技术;(3)能在各种行驶条件及工作环境下实现高净化效率和优异燃油经济性的排气后处理系统。以实现“柴油机革命”为目标,研究人员今后还将不断开发更新的技术。
-
喷油
+关注
关注
0文章
5浏览量
7227 -
柴油机
+关注
关注
1文章
171浏览量
26256 -
反应器
+关注
关注
2文章
97浏览量
11049
发布评论请先 登录
相关推荐
农用柴油机原理使用及维护 pdf电子书
车用增压柴油机VNT和EGR系统匹配试验研究
柴油机电控燃油喷射系统开发与研究
柴油机预混合燃烧机理的研究
轻型车柴油机燃烧过程的仿真研究
柴油机喷油泵维护“十要”
全面介绍嵌入式柴油机工作状态监测装置
农用柴油机原理使用及维护
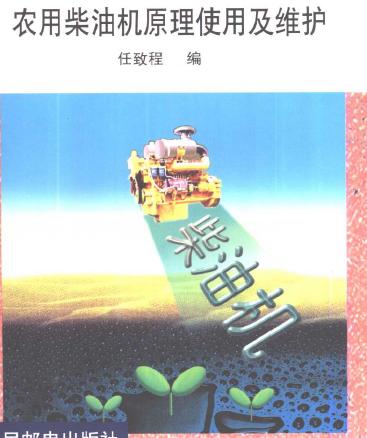
柴油机拆装实习指导书
柴油机电子控制的现状与进展
柴油机转速信号动态模拟电路分析与设计
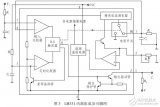
评论