A. Birckett N. Engineer P. Arlauskas M. Shirley P. Neuman
摘要:对1台具有进气门晚关米勒循环和高几何压缩比的机械增压2.4 L直列4缸直喷汽油机进行了仿真、设计及测试,并通过改动齿轮传动比降低发动机转速。选择1台3.3 L自然吸气V6发动机作为基准机型进行对标。该机械增压直喷汽油机目标用途是中型客车或中小型货车。采用计算机辅助工程软件GT-Power进行部件选取和进气道开发。相比于V6基准机型,利用动力总成仿真模型仿真可知直列4缸汽油机的燃油经济性及性能都得到了提高。机械增压器带电磁离合器、中冷器及进气歧管。通过改进内部电路将大量新软件集封于量产ECU中。容积效率采用发动机自动图谱技术和软件进行标定。数据处理方法把原始输出编辑为点-斜线格式。全因子试验设计为最有用的标定区产生模型。发动机测功机的试验结果表明在模拟的联邦试验规范行驶循环下有望大幅改善燃油经济性。现阶段正在开发增压器离合器控制和车载测试。
降低燃油消耗和排放,同时满足车辆用户对车辆性能和噪声-振动-平顺性(NVH)要求,是巨大的工程挑战。照目前的发展,车辆平均尺寸和质量都在不断增加,这为动力系统工程师带来了更多挑战。在短期内必须有先进的动力系统,以保持并吸引越来越多的汽车消费者群体。采用增压技术和米勒循环的发动机在改善燃油经济性、发动机响应效率和输出功率等方面已显示了很多优越性[1-3]。
本文所示的发动机设计及原型机建造由现代-起亚美国技术中心(HATCI)动力总成部发动机设计和试验团队完成。一系列已得到验证并且已可投入市场的技术已被用于新发动机中,与同类的涡轮增压发动机相比,该机型不仅有较低的燃油耗,而且有较好的发动机性能,特别是低转速区域具有大扭矩输出,并且有较快的瞬态响应。图1为本文研究的机械增压发动机。本文主要目的是描述机械增压直喷汽油机从概念设计到初始测功机试验,以及获得试验结果的工程过程。
1 仿真
采用Gamma技术公司的一维GT-Power及GT-Drive软件分别进行了发动机、车辆燃油经济性仿真[4]。以1台2.4 L自然吸气发动机为原型机。其主要特征包括壁面导向缸内直接喷射、持续双可变气门正时,以及快速起燃的紧耦合催化器。GT-Power发动机模型用试验室测量标定,包括可测量缸内压力的Kistler 6041B压力传感器、AVL 735S/753C燃油质量流量计、温度调节装置、Horiba MEXA-7500HEGR排放和空燃比分析仪,以及其他静压和热电偶测量设备。
以1台3.3 L V6发动机作为进行发动机性能和燃油经济性对比的对标机型。图2表示本机械增压发动机、原型机2.4 L直列4缸直接喷射发动机,以及3.3L V6发动机的扭矩水平。这台机械增压发动机的最初设计意图是在不牺牲车辆性能的前提下,与V6发动机相比,改善燃油经济性。其优势在于通过匹配变速器,而不是通过降低功率来降低发动机转速,达到良好的低速行驶性能和快速响应。对于柴油机而言,可通过机械增压和变速箱降低发动机转速,使燃油耗降低25%-50% [5]。
2 建模
首先,增加1台机械驱动“罗茨”式增压器,并修正发动机模型。选择1台传动比为3.63:1的Eaton TVSR900增压器。该增压器在发动机标定转速5 500 r/min时达到最高转速。进气歧管的设计包括一系列特殊的部件:机械增压器、增压器驱动离合器总成、集成式水冷中冷器、再循环旁通阀和节气门体法兰等都布置在1个紧凑的装置中(图3)。这使它可以安装在搭载2.4 L自然吸气基准发动机的现有车辆上。在发动机低转速时能使增压器的离合器分离,使发动机接近零损耗。图4为机械增发动机的GT-Power模型。
第二,仿真了一种新型进气凸轮轴。与2.4 L原型发动机相比,升程降低而持续期延长。将进气门延迟到压缩行程关闭,降低气缸内未燃混合气充量。这有利于在部分负荷工况下运行,因为进气可以不节流,但最大扭矩和功率降低。增加1台机械增压器能够提高发动机质量流率和输出功率,通常将其称为米勒循环。图5对比了新进气凸轮型线与原基准发动机型线,而排气凸轮型线未变。
第三,做了若干较高压缩比的方案,最后设计并试制了具有更高压缩比的活塞。建立了带准预测燃烧模型的GT-Power模型,并用1个爆燃控制器来设置Wiebe函数变量,基于转速1 500 r/min全负荷时的爆燃极限,最后选定了较高压缩比。因为压缩压力和温度较高,作为折衷,压缩比提高时,节气门全开的点火正时必须推迟。图6所示的数据表明,在压缩比从9:1变到12:1时最高燃烧压力(温度)变化不大,但压缩比为15:1时,在上止点的最高燃烧压力有大幅变化。上止点后50°CA的独特的第二压力峰是由于很晚的点火定时造成的,而后者为防止末端混合气的爆燃所必需。爆燃模型大致按1台运行中发动机的实际运行情况进行标定,并针对不同压缩比进行GT-Power仿真。
用主动爆燃控制器设置Wiebe燃烧相位重新试验了仿真模型,并设计了1个正交试验,在3种转速下,压缩比从9到15(点间隔为0.5)的试验。图7的数据表明节气门全开时,压缩比10.0~10.5左右时,比油耗最低。在发动机部分负荷运行工况下,通过测量在行驶循环下的燃油经济性发现,较高压缩比能有效降低燃油消耗。较高压缩比有利于降低燃油消耗,同时不会由于爆燃极限值而影响发动机在低转速时的节气门全开性能。最后,选择了压缩比12:1,因为这是在不大幅影响节气门全开性能情况下的最高可能压缩比值。在部分负荷运行工况下,压缩比高于12:1将提高发动机效率,但由于超过爆燃极限,这将限制节气门全开时输出扭矩的能力。
最后,发动机硬件的最后1项变化是增加1个低压冷却废气再循环(EGR)系统。多种研究证明了冷却EGR系统的好处,而它将与采用米勒循环的机械增压系统配合良好。因为正压梯度将驱动足够多的EGR流量从排气系统后的催化转化器供给增压器进气[6]。在GT-Power模型中,EGR对燃烧相位及燃烧持续期的影响是通过准预测燃烧模型参数来考虑的,而模型参数的设定是基于带外部冷却EGR的基准机型的试验。
3 模型分析以及燃油经济性预测
发动机模型的比油耗脉谱图作为GT-Drive车辆模型的输入。此外,为改善发动机低转速扭矩(比对2.4 L基准机型)及瞬时增压响应性,添加了1台降速变速器。采用了整车质量约为1 500 kg的中型乘用车。2013年下半年启动概念验证车辆建造计划,目前已完成6速手动变速车辆建模工作。表1对比了各种不同的传动比。
表1 基准发动机与降速增压发动机的变速器传动比
项目 | 变速器传动比 | 发动机转速与车速比 | 变化百分比 | ||
发动机类型 | 基准发动机 | 降速增压发动机 | 基准发动机 | 降速增压发动机 | - |
传动比 | 4.333/3.250 | 4.063/2.955 | - | - | - |
1档 | 3.267 | 3.267 | 115.7 | 108.4 | -6.3% |
2档 | 1.931 | 1.794 | 68.4 | 59.6 | -12.9% |
3档 | 1.696 | 1.542 | 45 | 37.2 | -17.3% |
4档 | 1.276 | 1.176 | 33.9 | 28.4 | -16.2% |
5档 | 1.027 | 0.921 | 27.3 | 22.2 | -18.7% |
6档 | 0.829 | 0.732 | 22 | 17.7 | -19.5% |
与2.4 L自然吸气汽油机的基准车辆相比,对车辆进行了仿真以验证降低传动比不会影响车辆性能。相反,车辆性能与采用3.3 L V6汽油机的性能相当,甚至在有些情况下还更好些。图8为3款发动机的2项加速指标。其中1项代表在城市路况下2档从40 km/h加速到80 km/h的时间;另1项代表在高速路况下6档从80 km/h加速到120 km/h的时间。
采用发动机模型预测了在联邦试验规范(FTP)城市和高速公路(未经调整)工况下行驶循环的燃油经济性,并逐项评估所有各项技术。其中,降速变速器的引入对改善总的燃油经济性贡献最大。采用机械增压器是有可能大大改善量产车辆性能唯一可行的办法。如不加强低转速工况扭矩,发动机性能较差,不能为顾客所接受。图9为改善燃油经济性的步骤。
4 设计
在发动机仿真的同时,一旦确定机械增压器尺寸和带轮升速比,发动机的设计工作就可以开始。采用CAD软件进行进气歧管的集成设计,包含增压器安装法兰、悬置系统、增压空气中冷器,以及旁通阀。采用铸造技术获得复杂的内部结构,从而使外部总体尺寸更加紧凑。
4.1系统布置
机械增压器的外形设计不得超出原2.4 L发动机进气歧管的外轮廓,以使其可以顺利装入意欲匹配的试验车辆中。机械增压器外壳安装在进气歧管和发动机缸体之间的下部。增压空气向上流动,经过增压室,再通过中冷器。而后,进气气流通过气道进入发动机,或者部分通过旁通回流机械增压器进气口。图10和图11表示机械增压器和进气歧管总成的其他主要部件。
4.2机械增压器
如上文所述,机械增压器为1台Eaton TVS系列R900“罗茨”容积式增压器。增压器采用第6代标准TVS系列转子组,为扭转160°的4齿设计。增压器进气量为 900 mL/r。Eaton R系列增压器更关注空气流量而非容积效率和等熵效率。该设计项目还包括向机械增压器附加1个离合器,当不需要增加进气空气流时,能够完全消除与转子组和齿轮组相关的摩擦和驱动扭矩。离合器采用+12V运行,为避免不同的转速变化率和扭矩冲击,也可与脉冲调制相匹配。通过严格控制运行速度、循环数和热量积聚,耐久性达到16万km(10万英里)。
4.3进气歧管
考虑到机械增压器质量,进气歧管采用铝合金砂铸件。为减小铸件质量,进气歧管壁厚减薄为3 mm。进气歧管采用斜面式组合布局中冷器内的滑板,分别用法兰安装到气缸盖、增压器旁通阀。
4.4增压空气中冷器
采用集成水冷式增压空气中冷器减少节气门体后的增压空气体积,缩短节气门响应时间。空气中冷器经改进以适应空间环境。摒弃了传统的安装法兰,进气口和排气口直径增加到19 mm。核心容积约为1.1 L,其为两通道设计。进气歧管带有中冷器检视孔盖板,从而便于中冷器的安装和拆卸,采用发泡密封件阻止气流围绕在冷却器芯周围。
4.5旁通阀
再循环旁通阀是1个直径为50 mm的蝶形阀。采用可变执行器,调节范围在0~90°之间,位置误差不超过0.5°。执行器响应时间不超过50 ms。在离合器分离、所有空气气流都必须旁通增压器(因为增压器转子不转时为无流动状态)的条件下,大直径旁通阀能够为增压器提供充足空气。最初使用旁通阀是为了EGR系统。其控制算法是现成的,众所周知它具有很好的可靠性,便于各种用途的控制。旁通阀的安装位置也很重要,要防止不必要的冷凝水积聚。
4.6液体冷却回路
水冷式中冷器液体冷却回路包括1个永磁叶片式冷却液泵和1台安装在车辆悬置架上的低温散热器。采用1个组合式铝制冷却液储存箱作为回路系统的加注点。冷却液储存箱安装在车辆左前角的前保险杠后。冷却液泵直接与冷却液储存箱相连。加注点为铝制加注口,连接承压0.1 MPa的冷却液加注盖。系统的回流点在加注口内。1对冷却液线路从冷却液泵出口经中冷器,到低温散热器。加注冷却液中水和乙二醇的比例为1:1。
4.7皮带传动系统
为降低发动机额外轴向长度,机械增压器采用二级带传动系统驱动。为延长保养周期,增压器采用6峰或6筋剖面的蛇形带。二级皮带传动的曲轴力矢量与一级带传动力矢量相反。这样使作用在1号曲轴主轴承的力降低14%。图12表示带传动系统布置。图中蓝色箭头代表原一级蛇形带的力矢量,红色箭头代表机械增压器系统二级传动带的力矢量。
为将上张紧轮悬置架、张紧轮臂和发动机悬置架安装在接近理想的位置,设计了1个很大的桥式悬置系统。标准的发动机前盖均无这些安装点。二级带传动张紧轮为新设计的线性动态张紧轮。外张紧轮可很快适用不同的张紧力而不必作很大的变动。
上线性张紧轮悬置架连接到1个偏心轮,其在1个孔内旋转在末端安装位置实现+/-6 mm变动。偏心轮和带长度变化相结合能在任意负荷点均能获得所要求的张紧力。
5 发动机测试
在成功完成发动机硬件设计和安装后,机械增压发动机被安装在发动机试验台架上。第1项测试为带有再循环阀的无离合器R900增压器。发动机压缩比不变,保持在11.3:1。第2项测试为升级到带离合器的R900增压器,压缩比12:1的活塞和米勒循环进气凸轮。图13表示增压器带有离合器的发动机。发动机测试使用牌号为RON 91的燃油,其乙醇含量达到10%。
5.1试验布置和软件执行
对涡轮增压直喷汽油机的控制单元进行了修改,以控制机械增压器离合器和再循环旁通阀。标准ECU控制涡轮废气旁通阀以控制增压压力,相较于自然吸气发动机,涡轮增压发动机可通过使用再循环旁通阀更好地控制负荷水平。
5.2发动机标定
利用A&D ORION自动绘图功能进行虚拟环境标定和所有基准值的标定工作。采用基于Matlab模型的正交试验响应模型生成凸轮相位、点火正时旁通阀开度设定,以及EGR率的最优标定。标定过程的主要目标是给定负荷目标下的比油耗最小化。同时进行ETAS“ASCOM”试验设计和标定生成。标定过程如图14所示。
标定工作完成后,即将进行瞬态增压响应试验,并在发动机测功机上模拟0~97 km/h车辆加速。还将在测功机上进行瞬态行驶循环FTP试验以验证标定的适应性,为车辆试验做准备。5个稳态点的初步测试结果与GT-Power软件的仿真结果基本一致。这5个稳态点是带有标准不降速变速器的中型客车的发动机具有代表性的转速和负荷点。离合器分离和增压器旁通阀全开,压缩比提高到12.0(原压缩比为11.3),米勒循环进气门晚关时,5点平均燃油耗降低了5.4%。燃油经济性的大部分收益来自因进气凸轮持续时间较长,降低了泵气损失。部分负荷运行不需增压压力时,增压器离合器对降低附加损失起了重要作用。图15为离合器分离、旁通阀开启发动机与基准发动机的比油耗对比。
带有机械增压器、无离合器,以及旁通阀全开的发动机总摩擦(包括泵气损失)与2.4 L基准发动机大体一致(图16)。较低的拖动摩擦值归因于进气门晚关,以及米勒循环凸轮减少泵气损失。
6 试验设计
基于MatLab软件,自动统计标定建模工具ETAS“ASCOM”被用来生成全因子试验设计(图17)。该统计软件可以为生成标定用的低误差模型只需较少的数据点。试验设计只需要2组数据,每组250个数据点,总共需要不超过500个数据点。随机设定试验的附加因素,包括不同增压水平下的进排气凸轮中心线、空燃比和增压器旁通设定点,使转速和负荷变化。点火提前角达到最佳最大扭矩的最小提前角(MBT)或爆燃极限。MBT常见指标选择为已燃质量百分数(MFB)50,上止点后8°CA。利用AVL公司Indiset软件进行燃烧分析。
发动机自动绘图软件ORION控制试验室环境,标定工具快速分配500个数据点,并行控制7个输入变量。由仪器(热电偶、压力传感器,以及发动机爆燃和早燃的Indiset燃烧数据)和发动机电控单元ECU的数据所创造的基本试验室和发动机的安全性使发动机可以全天24小时无人运行。
7 响应模型建立
对测量数据进行了处理并用标定工具中的统计算法建模。快速识别并清除异常数据。特别需要注意不能过度预测各模型的响应情况。图18为扭矩和比油耗生成的响应模型。无论对扭矩还是比油耗,低误差(RMSE)和R2值接近1在统计上都是理想的。
8 标定生成
从比油耗和扭矩模型中提取进排气凸轮中心线、增压器旁通(进气歧管绝对压力设定点),以及点火提前角的标定。利用一种类似于MatLab标定生成的标定工具CAGE,尽可能优化标定,使燃油耗最小化,然后获得最大扭矩。通过一种“平顺”工具进一步改进标定,然后将其直接输入INCA以评估发动机。进气凸轮标定的实例如图19所示。曲面图稳定、平滑和精确的标定有利于车辆加速过程中的工况过渡。
9 结语
满足未来排放和燃油耗目标需要动力总成技术进一步改善发动机效率。汽油直喷和增压缩缸强化技术具有发展前景。采用降速变速器和增压装置提供额外的低速扭矩,以获得降速优势。本文利用机械增压实现低速扭矩的提升。通过降速和缩缸强化改善燃油经济性,本研究在提高发动机效率方面具有进步意义。
-
机械
+关注
关注
8文章
1586浏览量
40597 -
离合器
+关注
关注
0文章
111浏览量
14607 -
汽油机
+关注
关注
0文章
58浏览量
11550 -
增压器
+关注
关注
1文章
31浏览量
11350
发布评论请先 登录
相关推荐
基于DSP的汽油机点火参数自动测试系统
电感储能式汽油机点火器总成技术条件
关于3缸1.0 L增压直喷式汽油机性能分析
关于3缸1.0L增压燃油分层喷射汽油机性能分析
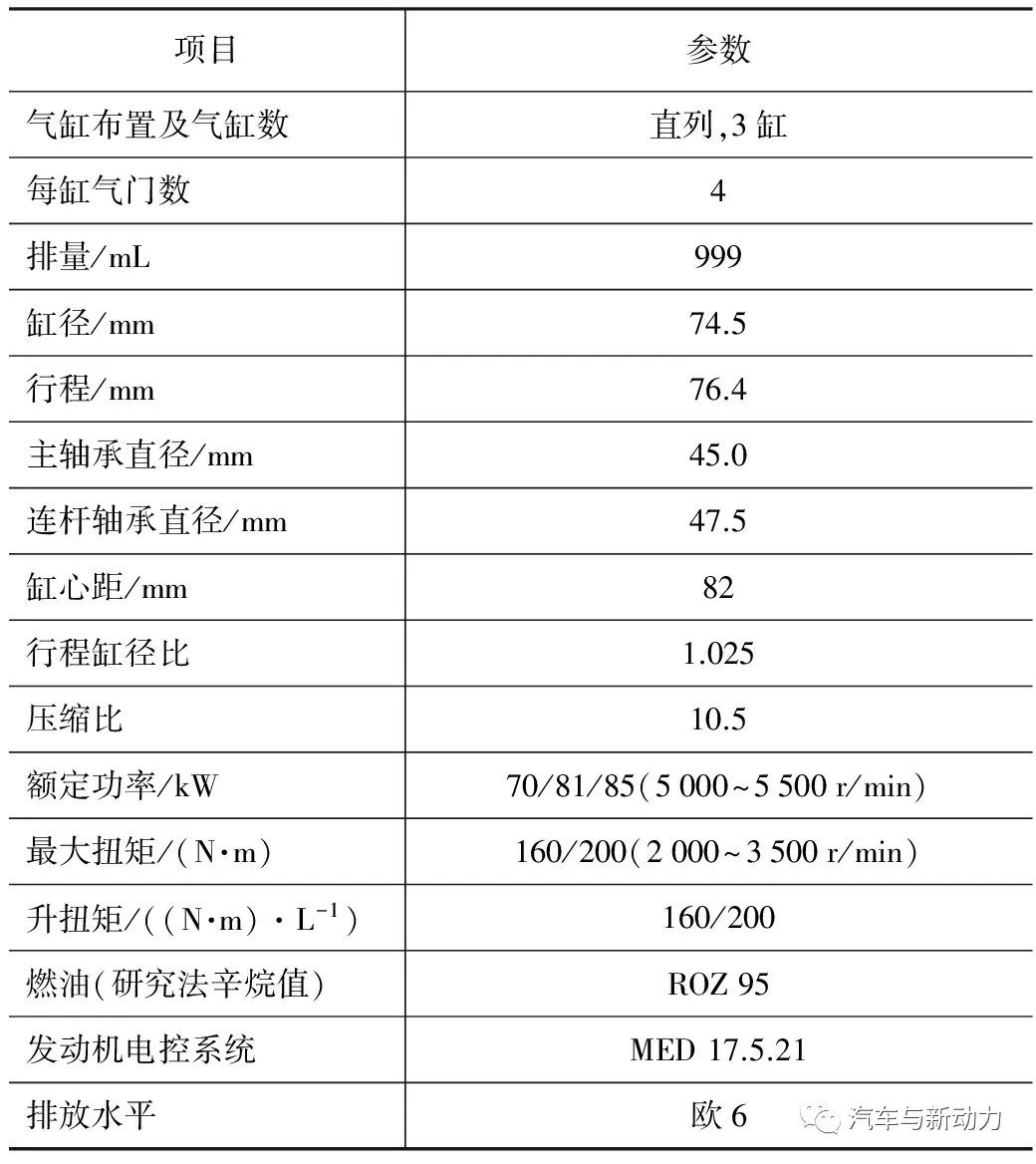
关于直列6缸直喷式汽油机性能分析
关于欧6直喷汽油机性能分析和可行性解决方案评价
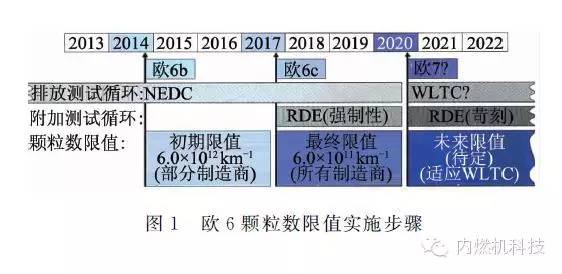
关于Volkswagen3缸1.0 L-TSI汽油机性能分析
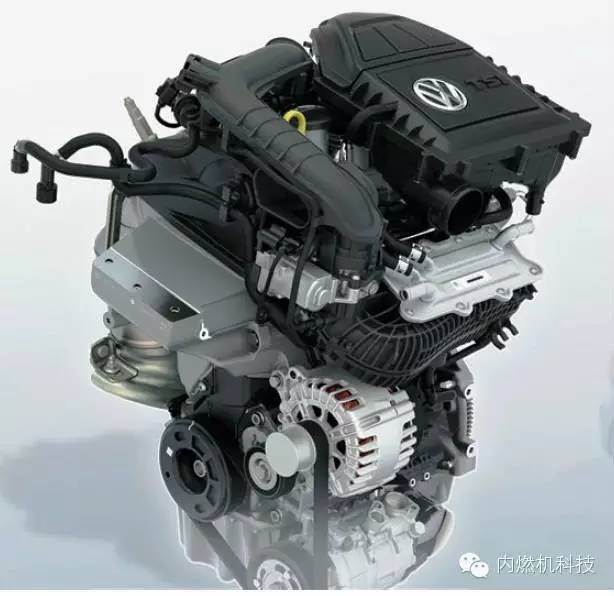
评论