电流从充电电路的输出端出来以后,总是要经过一段PCB铜箔、连接线以后才进入电池的正极,回流电流从电池的负极出来后又要经过连接线和一段PCB铜箔以后才能回到充电电路的电流回流端,这里的每一段连接都存在电阻,电流流过时就会形成电压降。如果连接中还使用了接插件,接触电阻又会成为新的问题,它们会与所用材质、结构有关,并有可能随着时间的变化而变化,机械振动都会带来影响。
除了线路电阻以外,正常设计的锂离子电池模组内部都应该有电池保护电路,它们通常由两只背对背连接的MOSFET构成开关电路,这些开关在导通时也是存在电阻的,也会成为电压降的源头。实际上,锂离子电池保护电路实现过流保护的方法就是通过测量流过MOSFET开关上的电流形成的压差来实现的,所以这些MOSFET开关的导通电阻还不能被做到无限小,否则就提高了对过流保护电路的设计要求,而且极小化的MOSFET导通电阻也会将其成本升到极高的程度,完全不符合经济化的原则。
实际的充电电路在测量它输出的充电电压时都测量的是它的输出端的电压,要对电池的实际电压进行测量不是不可以,只是那样的做法将造成电路的复杂化,至少也要增加两个测量端子才能实现,这对保持低成本是不利的,所以,充电电路看到的输出电压和实际的电池电压之间就总是存在一个差值,而这个差值就是线路总电阻和充电电流之间的乘积,它在实施大电流快速充电的时候就变得很大了,因而依靠测量输出端电压来决定充电进程的方案从恒流充电转入恒压充电的时间就会提前。恒压充电阶段的充电电流是不断降低的,系统已经不会再给电池更多的压力使之快速吸取电能,因而实际的充电时间就会延长,妨碍了快速充电的实施。
消除这种影响的做法是引入压降补偿,使得恒流充电阶段能够持续到电池电压真的达到预设的电压以后再转入恒压充电阶段:
改变以后的充电曲线如上图实线所示的样子,而电池上看到的充电曲线则如其中虚线所示,两者的差异带来的效果就是充电时间的缩短。
实际电路系统中的线路阻抗总是千差万别的,系统需要的充电电流也因具体的应用和工作状况而有不同,实际的补偿参数就会因为这些不同而有差异才是正确的设计,好在像RT9466这样的快充芯片均已实现智能化,只要把相关的参数写入它的内部寄存器就好了。
在RT9466的寄存器中可以选择的电阻补偿值在0-175mΩ之间,以25mΩ为步进量,应用时只要将实际系统的线路阻抗估算出来并写入就好了,芯片将在运行时自动进行补偿。
但是这种补偿其实也是有限制的,RT9466还同时设定了最大容许的补偿电压,这个数据可以在0mV-224mV之间进行设定。为什么要这么做呢?这可能和安全有关,过高的电压出现在电池上总是不好的,对寿命有比较大的影响,有了限制以后可以避免出现意外。下图是我很久以前收集的资料,它显示了不同的充电电压对电芯循环寿命的影响:
实际上,很多快充设计都会将充电电压有意降低,这样可以延长电池寿命,弥补大电流充电对电池寿命的负面影响。降低充电电压会使得电池充满时的实际容量降低,但由于可以快速充电,充电时间大大缩短,两者结合后的用户使用体验不会变得太差,相反的是用户可能会有某种成就感,因为它能感受到电池电能在充电时的快速增长,这会带来愉悦感。
从我个人的立场来说,我为快充的快速普及感到高兴,但是如果我的手机具备快充能力,我只会在必要时利用该能力,其他情况下则会选择慢充,因为我并不会急于去使用手机,让它慢慢地被充满总是要更好一些,可以兼顾到多方面的需求,但是作为普通的消费者恐怕不知道如何才能做到这一点,不知道读者你是否知道呢?这个问题就留给你作为思考题吧,方法有很多,答案将会在未来的文章中慢慢揭露,你需要自己去发掘,因为我可能不会直接回答这个问题,你需要综合利用各种知识来做思考,而这正是我对你的期望,如果不经历这个过程,你看我写的文章只是会多知道一些东西,能力和智慧并不会增长,那就很遗憾了,你何必要把宝贵的时间用来读这种浪费生命的东西呢?
-
锂离子电池
+关注
关注
85文章
3264浏览量
78132 -
充电电路
+关注
关注
32文章
243浏览量
53885 -
智能化
+关注
关注
15文章
5023浏览量
56243
发布评论请先 登录
相关推荐
供应智融SW6106支持PD的多协议双向快充IC
蓝牙音箱与PD协议快充
PD快充协议芯片详细介绍
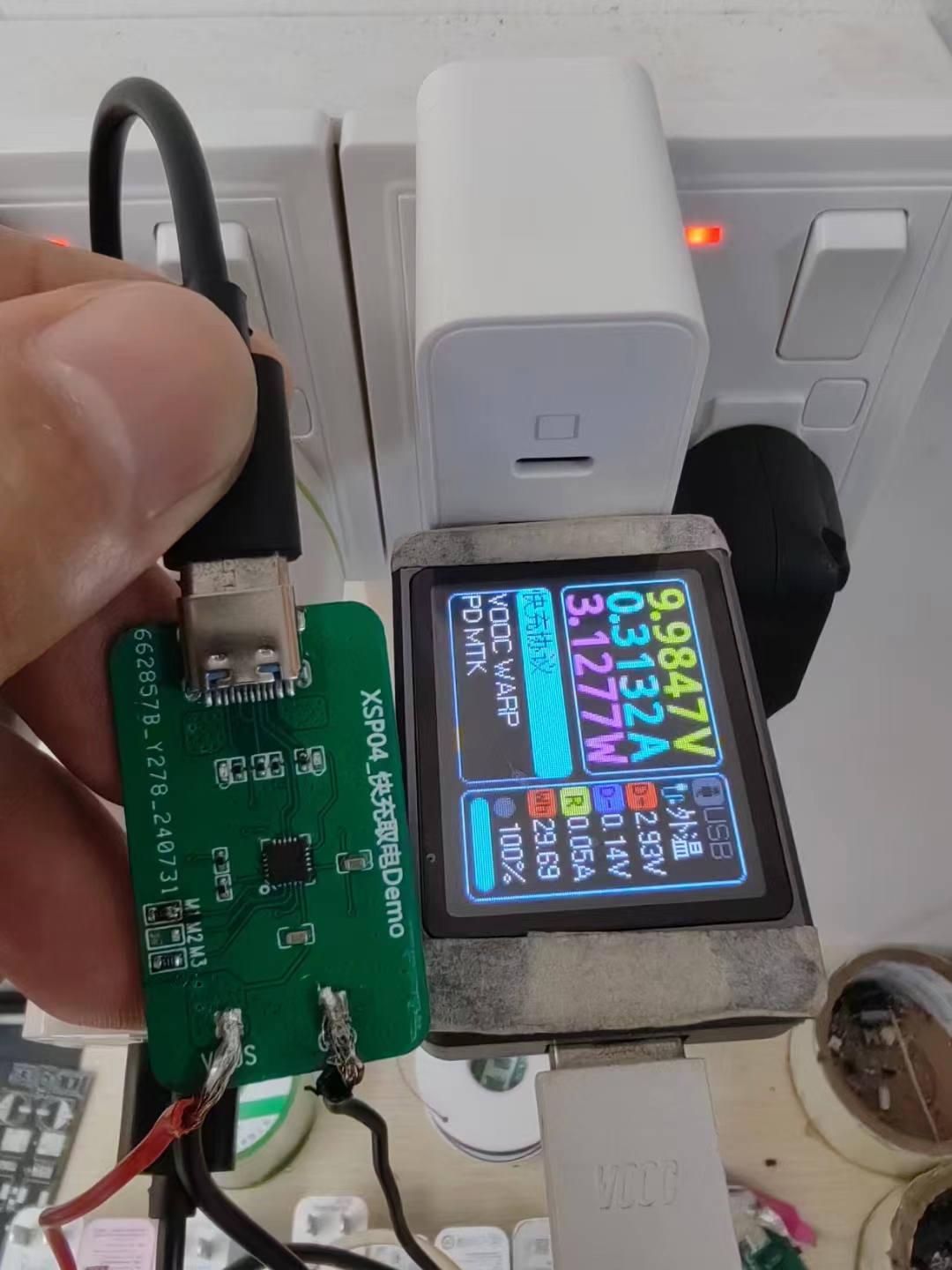
超级快充闪充协议
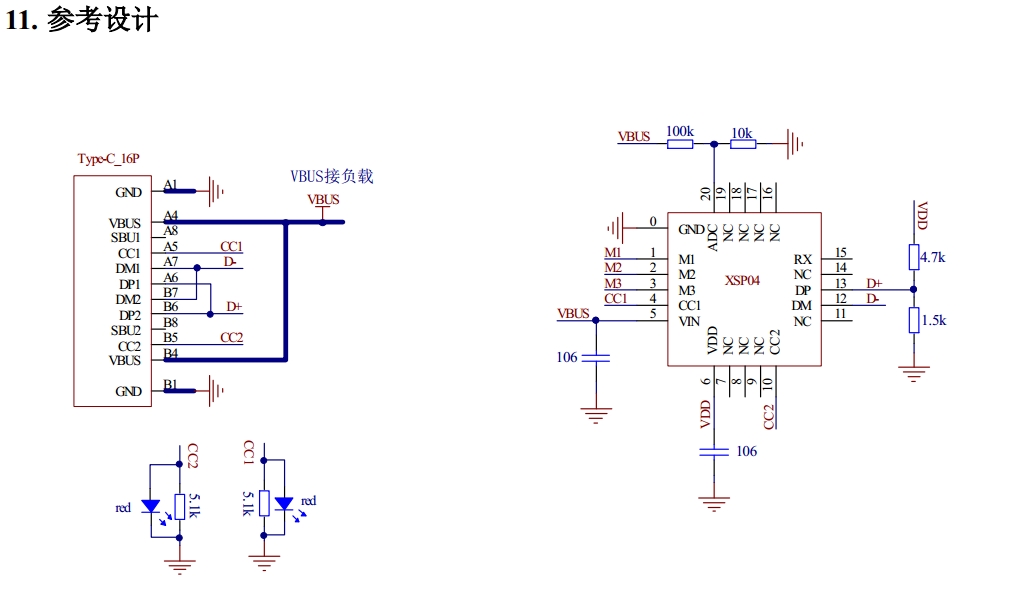
评论