1、编程不当,产生撞刀
1.1车削孔时的进、退刀
内孔车刀加工孔时,进刀方式应为单坐标方式,如图1(a)所示工件中,若直接X、Z轴联动快速移动刀具至目标点(G00 X Z),刀具势必会如实线所示那样与工件发生碰撞;为防止刀具与工件发生碰撞必须单坐标分步使刀具移动至目标点,在编程时应该使刀具先走z方向(留2mm安全余量),然后走x方向定刀,再走z方向切削加工孔,如虚线所示,这就有效避免了刀具与工件之间的碰撞。
内孔车刀加工孔时,退刀方式应为单坐标方式,如图1(b)所示工件中,若直接x、z轴联动快速移动刀具退至目标点(G00 X Z),刀具势必会如实线所示那样与工件发生碰撞;为防止刀具与工件发生碰撞必须单坐标分步使刀具移动至目标点,在编程时应该使刀具先走x方向(退出1~3mm),然后走z方向时刀具从孔里退出来,再走x方向使刀具移动至目标点,如虚线所示,避免了刀具与工件的碰撞。
1.2 车削槽时的进、退刀
切槽刀加工槽时,进刀方式应为单坐标方式,如图2
(a)所示工件中,若直接x、z轴联动快速移动刀具至目标 点(G00 X z),刀具势必会如实线所示那样与工件端面发 生碰撞;为防止刀具与工件发生碰撞应单坐标分步使刀 具移动至目标点,在编程时应该使刀具先走z方向,然后 走x方向定刀(留2ram安全余量),再走x方向切削加工 槽,如虚线所示,这就有效避免了刀具与工件之间的碰 撞。 切槽刀加工槽时,退刀方式也应为单坐标方式,如图 2(b)所示工件中,加工完槽若直接x、z轴联动快速移动 刀具至目标点(G00 X Z),刀具势必会如实线所示那样与 工件端面发生碰撞;为防止刀具与工件发生碰撞应单坐 标分步使刀具移动至目标点,在编程时应该使刀具先走x 方向退出,然后再走Z方向退至目标点,如虚线所示,能 有效避免刀具与工件的碰撞。
1.3 起刀点与换刀点
起刀点是刀具以切削进给速度开始车削加工的加工 起点(或循环起点)。起刀点设置在所加工毛坯外面,在 x、z两个方向离工件应有一定距离,如图3(a)所示。起刀点分别表示在X、Z两个方向离工件的距离一般取1— 3mm,起刀点离工件太远增大G01进给的空行程,降低加 工效率;起刀点离工件太近会增加撞刀隐患。 换刀点是指刀架转动换刀时的位置,设在工件及夹具 的外部,换刀点离工件的距离以换刀时不与工件及其他 部件发送碰撞为准,并力求换刀移动路线最短,换刀点的 设置距离工件太远,将延长G00的移动时间,降低加工效 率,如图3(b)所示。编程时换刀要特别注意留给镗孔刀 足够的空间,因镗孔刀刀柄伸出较长,如换刀空间不够, 就会造成换刀时刀具与卡盘或工具碰撞。另外,如因工具 较长有后顶尖支撑,在确定换刀点位置时,还必须确定刀 架向尾座方向移动时的极限位置,避免换刀时刀架与尾 座发生碰撞造成刀具损坏。
2、对刀不当,产生撞刀
2.1 手轮进给倍率
数控车床对刀方式常用的有试切法和对刀仪自动对 刀法,试切法对刀是学生在数控车床实训中普遍采用最 多的一种对刀方法。学生在对刀之前,通常要在换到点位 置换到所需对刀的车刀,车刀通过刀架旋转到位,这时车 刀到被车削加工工件的距离较远,学生就会用手轮0.1方 式将刀具快速靠近工件,然后用手轮0+01方式继续靠近 工件,用0.001方式切削工件。但是,学生在操作过程中往 往忘记手轮进给倍率快慢的改变,很多初学者在对刀时 用手轮0.1方式将刀具快速靠近工件,继续用手轮0.1方 式靠近工件和切削工件,车刀以较大的进给速度与工件 接触,造成车刀与工件发生碰撞。 初学者在上数控车床操作之前,首先在机房内利用数 控仿真软件进行大量的对刀练习,熟练对刀步骤和操作 要领。其次,在数控车床上进行对刀操作时,安排同小组 的成员在傍边进行辅助,对操作不正确的学生进行及时 指正,避免车刀与工件发生碰撞。
2.2 数据输入
学生在数控车床对刀操作时,经常发生数据输入位置 不对或数据输入不对。比如,学生在对刀试切外圆后,x 轴不动,刀具沿+Z原进给速度退出,退出后按下停止按 钮停车,用外径千分尺量得试切部分的外圆直径,进人刀具偏置寄存器的形状补偿,把测得的数据输入到相对应 的刀补号中,在数据输入过程中,学生往往把数据输入错 误。另外,学生把测得数据输入到刀具偏置寄存器的形状 补偿中错误的刀补号中,还有学生把测得数据没有正确输入在显示刀具几何形状补偿界面里。由于对刀数据不 正确,造成不能够获得正确的工件坐标系,在运行数控车 床切削加工工件时就会造成车刀与工件或机床发生碰 撞。 学生在对刀结束后,应该对每一把对过的车刀进行检 验。检验方法是:首先按下POS键,显示出刀具当前的位 置坐标,分别摇动手轮到X0和z0,观察刀具与工件之间 的误差是否超差。如果对刀的x数据不正确,当摇动手轮 移动到位置坐标x轴显示为零时,刀具的刀尖就不在工 件端面的中心处。
3、操作不当,产生撞刀
3.1 刀具补偿值设定错误
学生操作数控车床加工工件时,对刀误差或刀具磨损 会影响工件尺寸精度,所以要对刀具进行补偿,刀具补偿 应注意补偿方向及补偿量大小。要定期检查刀具补偿值 是否正确。在输人刀具补偿值时,如将“+”号输出“一”号, “X0.08”输成“X8”,就可能会出现执行程序后刀具直接冲 向工件或卡盘,造成工件报废,刀具损坏,卡盘撞毁等事故。
针对这种撞刀情况,学生可以在仿真软件上进行练 习,熟练掌握在输入刀具补偿值时,“+”号和“一”号之间的 区别。此外,初学者在操作时如出现不确定的情况要及时 询问实训指导教师,要得到实训指导教师的确认后方可 继续操作机床。
3.2 加工过程中误停车
数控车床执行程序正常加工过程中,由于操作者误操 作使程序停下来,如果操作者按“RESET”复位后,立即进 行循环启动,此时容易造成刀具与工件发生碰撞。因为运 行的默认值与程序的设定值发生变化,按“RESET”复位, 则把数控系统复位到初始状态,清除了保存在DRAM内 的预读程序信息,会改变刀具移动指令及主轴转速。 在自动运行程序过程中,如出现误停车导致程序停止 运行,此时将模式改为编辑方式,按“RESET”复位程序,再 重新运行程序。
-
数控车床
+关注
关注
2文章
78浏览量
16293 -
数控加工
+关注
关注
0文章
58浏览量
9938
发布评论请先 登录
相关推荐
数控加工中心刀具换刀系统
基于840D和PLC的数控加工中心控制系统
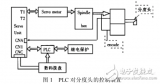
评论