从156.75 mm到166 mm,大尺寸硅片已经悄然进入市场,硅片尺寸增大在电池片制造、组件封装等环节能够实现成本节约,据了解M6电池片各制程的工艺时间与M2制程时间相差不大,因此在电池制造过程中每片大约可降低0.05元成本。
在白城等地,光伏电站中标电价已经接近平价甚至低价,大尺寸电池片投产会使光伏平价运营更近一步,2019年新建产线最基本的要求就是设备兼容大尺寸硅片的生产。更令人振奋的是今年8月中环推出了M12硅片,边长210 mm,比M2硅片面积增加80%,单瓦生产成本将会进一步降低,M12硅片的推出是颠覆性的,大尺寸硅片终将是光伏行业的未来。
但我们也要认识到现有的设备可能无法兼容大尺寸的硅片,硅片增大后又会给设备制造商带来新的需要解决的问题,整个制造环节都需要技术升级和突破,在这里以管式PECVD设备(如图1所示)为例讨论M6、M12硅片镀膜时需要做哪些准备和考虑。
图1. 管式PECVD
图2. 单台管式PECVD设备产能提升情况
PECVD是电池片产线上重要的镀膜设备,制备得到的减反钝化膜可以有效减少电池片表面反射率,增加光的吸收,同时对硅片表面和体内的复合中心起到钝化作用。PECVD从结构上可分为管式和板式两类。如表一所示,与板式PECVD相比,管式PECVD优点是开机率高、维护周期长、退火和钝化效果好。综合成本投入、后期维护等因素,新产线基本都选用管式PECVD制备减反钝化膜。如图2所示,从08年到19年,单台管式PECVD的产能快速增加,未来可能出现单台6000片以上的单小时产能。此外管式PECVD的工艺整合能力也很强,目前有些生产线已经采用背面二合一PECVD设备,将背面氧化铝和氮化硅膜集成在同一机台甚至同一管内进行,缩短了制程时间,减少了设备投入成本。
表一. 板式、管式镀膜设备对比
硅片尺寸的增大一定程度上限制了单管载片量的增加。目前国内外老产线开始生产M6硅片,在改造管式PECVD设备时遇到了部分问题:
1、石英管尺寸限制
石英管尺寸的限制本质在于石墨舟尺寸的变化。在软着陆机台中,166 mm硅片石墨舟的高度较高,进出舟的空间位置非常小,容易发生刮蹭舟脚等问题。为了解决该问题,只有减少石墨舟的载片量或者切除一部分舟脚,改变舟结构可能会影响石墨舟的使用寿命,因此多数产线选择了降低石墨舟载片数量的方式。
2、温区长度限制
搭载166 mm硅片的石墨舟在高度和长度两个方向上都有增加,长度方向上大概增加了80 mm,相当于石墨舟头的硅片向炉口方向移动了80 mm。尽管目前从工艺结果上看影响并不明显,但是越靠近两端炉体的封口效果越差这是不争的事实,炉口中心的硅片有发红的危险。
总体来讲,M6硅片镀膜设备在M2的基础上仅从石墨舟进出空间上做出了相应改动,干泵、流量计,射频电源等部件并不需要相应扩大升级;那如果是M12设备呢?
图3. 石墨舟尺寸及重量变化(从M2到M12)
为了能够承载M12硅片,石墨舟尺寸及总重量均会发生较大改变(图3所示)。石墨舟的总长度由156机台的1600 mm增加到至少2100 mm。高度从200 mm增加至250 mm以上,带片的重量从30 kg左右增加至~45 kg。超大的石墨舟需要配套超大的石英管,需要考虑水平运送机构的承重能力。现在市面上有两种结构的管式PECVD设备——悬臂结构和软着陆结构。如果采用悬臂结构在考虑进出舟空间的同时更要重点关注重量的增加,尤其是热状态下负重悬臂结构的变形,这会是悬臂M12设备的一个技术难点;软着陆设备石英管的直径需要设计的更大,用来保证桨的升降进出空间,相对而言,软着陆的负重压力较小,可以在石英管内增加支撑梁。尽管悬臂和软着陆设备的石英管直径在设计上有差别,设备的总高度相差并不大,当然现在的厂房高度是不能承载5管M12设备的,厂房高度需要增加~50 cm。
石墨舟的长度增加了500 mm左右,温区长度至少要增加500 mm,温区的长度至少要覆盖住整个石墨舟,加长之后如果采用五点控温可能更不容易控制工艺结果,需要增加一个控制和监测点,温区的分布也需要根据硅片的位置做出相应规划,尽量保证硅片不处在两个温区交界位置。
除了空间位置上,配套部件也需要进行升级。首先是射频电源的选择问题,镀膜设备从单舟308片升级到单舟416片时,射频电源的最大功率提升了50%,更大的射频功率保证了镀膜时石墨板间的电场能量密度,也就保证了大舟的镀膜速度,从石墨舟的增量上推算,432片M12的石墨舟使用的射频电源功率不应低于20kw。还需要注意的是,射频功率加大后,镀膜时的射频电流提升非常明显,射频功率的计算公式为:
P=U×I×Cos(相位角)
决定射频电压值的主要是石墨舟同轴电缆的阻抗和石墨板间气体的容抗,这在气体比例相同的情况下一般是一个相对固定的值,射频功率增加一倍,电流值也接近增加一倍。单片石墨舟和硅片上流经的电流也会增大近一倍,这种情况下可能造成射频功率波动、卡点烧焦等一系列射频问题。防止这种情况出现应当重新考虑石墨舟卡点的设计,增加插片机插片精度,减少在石墨舟运动输运过程中发生的掉片翘片情况。
类似的情况同样适用于通入流量的选定,目前镀膜时使用的特气流量大约在10 slm左右,按照硅片的有效面积增量来估算,M12设备的流量总通入量应该18 slm以下,基本达到了现有流量计配置的极限,如果想要给工艺调整提供余量,或者是更好的控制特气流量精度,现有的流量计量程应增加50%左右。
通入气体增加必然涉及到干泵的选择,在通入大量气体时是否还能正常调压是问题的关键。我们以国内某型抽速为1000 m3/h的干泵现场的使用情况为例,统计不同抽速下通入气体流量能够稳定的压力值,结果如表二所示。镀膜的工艺压力基本上要高于1500 mtorr,因此该抽速的泵完全能够保证调压成功。
表二. 流量、抽速与压力的关系
最后讲两点大尺寸硅片设备的隐忧。首先,硅片增大后,片内的膜厚均匀性更不容易保证。从M6硅片的镀膜情况来看,硅片几何中心点的膜厚较低,如表三所示,随机挑选一舟硅片测试五点的膜厚折射率,上下左右距离中心点位置约为20mm,测试结果显示中心点位置膜厚普遍偏低1-2nm。硅片增大到M12后,中心点到硅片边缘的膜厚差距会进一步拉大,会给工艺优化和工艺控制带来一定难度。另外一点是增大硅片后,单片硅片的净产出增大80%,不良的比例因为硅片面积的增加也相应增加了80%。例如原产线上碎片率为0.02%,改为生产M12硅片时,碎片率依然是0.02%,但是碎片的成本因为硅片尺寸的增大而变大了,这就要求,产能越大的设备,其设备及工艺稳定性必须提高。
表三. NAURA机台M6硅片工艺结果
综上所述,大尺寸硅片是当前晶硅电池行业发展的重要趋势,也是产业制造进一步降本的必然选择。无论是变化较为缓和的M6还是更为激进的M12,都对包括管式PECVD在内的所有设备、工艺提出了许多新的挑战,相应参与者需要在设计环节就全面考虑尺寸变化带来的诸多新问题新需求,才能更有效地服务行业,更好地带动产业发展。
责任编辑:gt
-
光伏
+关注
关注
44文章
3131浏览量
69541 -
电池
+关注
关注
84文章
10711浏览量
131736
发布评论请先 登录
相关推荐
PECVD中影响薄膜应力的因素
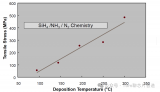
7纳米工艺面临的各种挑战与解决方案
半导体微电子硅片制备离不开全氟过滤PFA材料
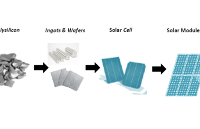
产业"内卷化"下磁性元件面临的机遇与挑战
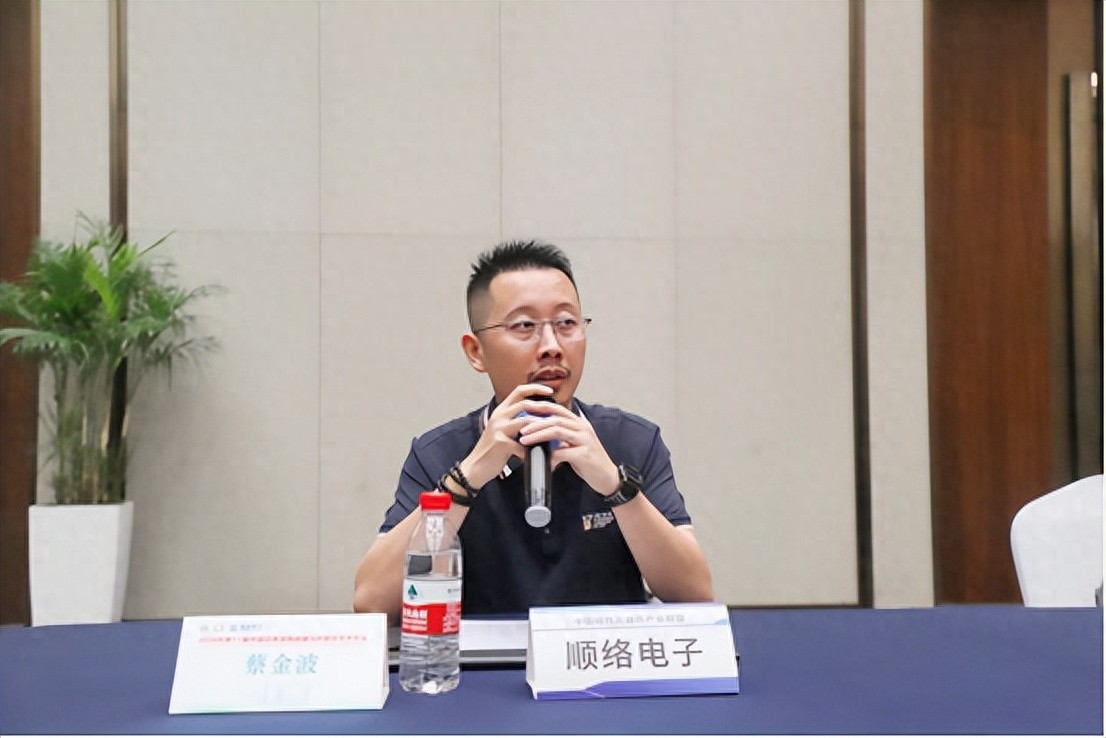
节能回馈式负载技术创新与发展
【⌈嵌入式机电一体化系统设计与实现⌋阅读体验】+磁力输送机系统设计的创新与挑战
CMOS晶体管的尺寸规则
苹果AI时代面临挑战,需对战略进行重大改变
全光网应用面临的挑战
人工智能芯片在先进封装面临的三个关键挑战
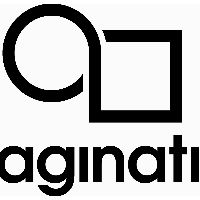
汽车雷达系统设计面临的挑战
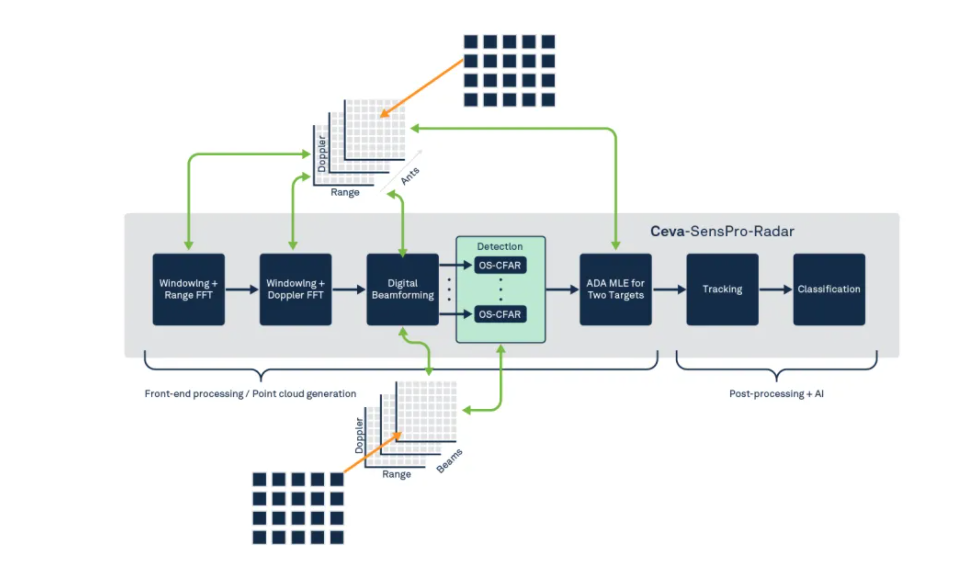
硅片分选设备上的智能传感器
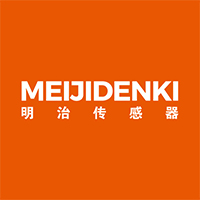
突破行业难题,硅片分选解决方案再升级!
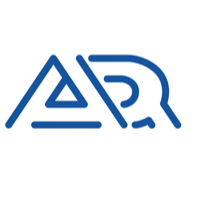
评论