2019年3月,全球复合材料领域顶级展会JEC组委会将2019年度增材制造(3D打印)创新大奖授予美国连续复合材料公司、空军研究实验室、洛克希德·马丁公司团队,以表彰其在连续纤维3D打印技术开发方面的创新成果。连续复合材料公司是连续纤维增强3D打印技术的先驱,2012年获得了全球最早的工艺专利。自美国于2014年推出首台连续纤维3D打印机以来,该技术正在快速发展并在航空领域取得应用。随着技术的逐渐成熟和大规模推广应用,该技术或将颠覆现有复合材料无人机、低成本复合材料航空结构的生产模式。
arevo 3D打印技术
连续纤维3D打印技术的优势
连续纤维3D打印技术综合利用工业机器人、3D打印末端执行器、原位检测、智能监测与机器学习等技术,快速输送、沉积连续纤维增强体,以及基体树脂并原位浸渍、固化,与传统的自动铺丝成形以及熔融沉积成形等工艺相比,自动化程度和柔性更高,对于典型的碳纤维/聚醚醚酮零件,研发周期可缩短至原来的1/30,生产速度可提高100倍。连续纤维3D打印机可以由多机器人组成柔性单元,机器人上还可添加多个3D打印末端执行器,同时打印头可支持碳纤维、凯夫拉、玻璃纤维甚至光纤和金属丝等材料,使该技术既可以用于大批量生产复合材料零件,也可以一次性打印高度复杂的几何形状或者需要极其精密制造的关键零件。
双机器人连续纤维3D打印机
连续纤维3D打印技术的发展方向
当前,美欧3D打印技术开发商与机器人制造商已共同开发了一系列先进的连续纤维3D打印设备与制造工艺,主要应用方向和发展情况如下。
低成本复合材料结构的大批量生产
美国阿瑞沃公司开发了可将热塑性预浸丝束打印成零件的直接能量沉积(DED)工艺,空客资本公司参与了对该公司的投资。DED工作单元由工业机器人、激光加热打印头和旋转构建平台组成,与传统3D打印相比,能够将生产速度提高100倍。除无人机机身、机翼等航空零件外,阿瑞沃公司还生产与无人机框架结构类似的自行车车架,连续纤维3D打印技术使其开发周期从18个月缩短到了18天。该公司于2019年2月投入使用的新工厂拥有8个机器人工作单元,可完成包括打印本身、后处理(如钻孔)以及用于喷涂的预打磨,每天共可生产8个大型零件。该公司正在测试每台机器人运行多个打印头以及每个工作单元运行多个机器人,以将生产速度再提高3倍。为了在整个提速过程中保持质量和可重复性,该公司采用了原位检测和机器学习技术,为打印头配装多个传感器(测量高度、压力、变形等), 系统软件使用这些传感器数据,根据需要实时调整工艺参数。这样,当工作单元需要更快运行时,就可以确保沉积速率、加热、固化和其他参数得到最优匹配。
McNair 3D打印技术旨在生产高度复杂且独特的结构
美国轨道复合材料公司开发了由并联机器人、模块化同轴挤出末端执行器组成的高度定制化的3D打印设备,挤出喷嘴通过其中心孔供给基体材料,通过周围的环形喷嘴供给纤维,并联机器人通过多台协作加快生产速度,可比传统3D打印快100倍。该技术的特点是可适应几乎任何复合材料:3-48K丝束的干燥和黏合纤维;包括热固性/热塑性塑料和碳化硅在内的塑料、陶瓷或金属基体;并且能够结合铜或铝线、纳米材料、导电油墨或其他有助于实现多功能结构的材料。这使其特别适合无人机类应用, 投资一种设备即可应用于所有结构和功能组件。
意大利莫伊复合材料公司开发的连续纤维制造工艺,旨在解决使用热固性树脂进行3D打印的挑战,并已成功用环氧树脂、丙烯酸和乙烯基酯打印连续玻璃纤维增强复合材料。除了适用于碳纤维应用的固化机制外,该工艺还可使用紫外线固化方式,所需固化时间小于1秒。目前, 该技术已开始用于航空结构件制造。
复杂或精密结构的快速研制和小批量生产
美国南卡罗来纳大学McNair航空航天创新与研究中心的研究团队开发了一种熔融长丝制造(FFF) 工艺,FFF系统使用配备有连续纤维沉积末端执行器的工业机器人平台,可提供7个自由度。该技术非常适合三类应用:一是模具或芯轴成本相对过高的小批量航空结构制造,如仅需一个特定高强度组件的无人机或小型航空器;二是利用其他制造方法无法产生所需强度质量比和刚度质量比的高度复杂的结构,如加强网格; 三是套印,这是一种在打印过程中插入组件并由此完全嵌入打印零件中的技术, 可以实现零件整合,如在打印零件中嵌入射频识别芯片或电子传感器。传统采用自动丝束铺放的航空结构集成度很低, 而该技术的亮点在于,如果使用热塑性塑料制造复合材料结构,每次就是通过套印重新熔化以增加新组件,消除铆钉、紧固件和黏结剂可显著改善这些结构。
荷兰CEAD集团于2018年11月推出其“优质”(Prime)大型连续纤维增材制造3D打印机,其尺寸为2米×4米×1.5米,是欧洲最大的3D打印机。制造过程中,打印机首先使用所需的热塑性树脂预浸渍连续玻璃纤维或碳纤维, 然后打印头将连续纤维与熔化的热塑性树脂颗粒结合,其中还可包括一定百分比的短切纤维,特别有利于小批量生产大型复杂产品。它还具有智能加热/冷却系统,可通过热感摄像头监测工艺,并根据需要实时进行调整。
俄罗斯初创企业阿尼索打印公司开发了基于复合纤维共挤出工艺的3D打印机,也是将增强长丝送入打印机之前对其进行预浸渍处理,不过长丝是采用特殊配方的热固性树脂预浸渍,而基体树脂通常是热塑性塑料,据称这是因为热固性聚合物比热塑性塑料更容易润湿单根单丝,能够提供更好的附着力,从而提升固化零件质量。
美国轨道复合材料公司的3D打印产品
将速度与精度相结合的复杂结构大批量生产
美国马克锻造公司开发的连续纤维系统使用两个打印头,一个用于基体树脂,另一个用于热塑性树脂预浸丝束。技术改进的重点是可靠性和可重复性。公司致力于实现工艺的完全闭环,并正为此开发一系列功能,如完全集成的材料跟踪和全面的自动报告功能。该系统的一个重要应用是打印工装夹具及组件, 与机加铝制组件相比,3D打印的热塑性产品同样坚固但更轻,不会像金属组件那样破坏零件,而且在同一天内就可以准备好,这可促进航空复合材料制造模具的发展。
美国Continuous Composites公司获得创新大奖的连续纤维打印(CF3D) 工艺,使用快速固化热固性树脂(工艺也适用于热塑性塑料),将增强纤维浸渍在打印头内,并在材料沉积后立即固化复合材料。热固性材料使该工艺能够在自由空间中执行高速打印,纤维体积含量可达到50%~60%。获奖项目中的重要进展包括更加自动化的工具路径生成手段;自动化的工具更换,从而可在同一部件上实现高分辨率单通道打印和高沉积率多通道打印;提高机器人准确性和精度等。该公司预计未来此技术将用于按需打印整个飞行器结构——无论是10件还是1万件。
连续纤维3D打印将多个结构作为单个组件进行打印,图为带有嵌入式角撑板的飞机翼
梁。使用Continuous Composite的3D工艺进行打印,随后通过手工沉积碳纤维复合材料进行蒙皮
瑞士9T实验室基于连续点阵制作工艺开发了“碳套件”(CarbonKit)系统,系统使用工业级廉价材料拉挤出复合材料棒,棒通过牵引单元进入可调节热量的挤出头,系统可以与一系列热塑性基体体系配合使用,纤维体积含量可达50%以上。该系统的另一个重要特征是能缩放挤出不同的横截面积,因此可以适应具有小丝束的高分辨率应用,以及具有大丝束的大幅面增材制造,如加筋壁板。一个已开展的项目证实,每年可生产约30000个零件。
启示建议
当前,连续纤维3D打印技术还存在两个主要问题:一是纤维含量低,且打印层之间的分层可能性高;二是缺乏标准化的连续工具路径生成商业软件。未来,随着这些问题的解决,该技术依托灵活开放、高速高效、低成本且生产完全自动化等优势,必将会与传统复合材料制造技术产生竞争。可以预见,随着该技术的成熟和大规模推广应用,将进一步促进航空制造业探索以3D打印方式批量生产无人机、复杂航空结构以及制造工装,开启航空复合材料发展的新浪潮。
面对国外技术飞速发展的势头,我国应加强情报跟踪研判,联合原材料、机器人、末端执行器、3D打印软件、传感器、机器学习、数控系统优势企业, 尽早开发和演示验证若干系列自主可控的工艺和装备,形成规模化的制造工艺和装备产业,支撑我国制造业提高生产效率和质量,以迎接未来航空复合材料结构设计制造面临的高速、低成本竞争, 并满足未来以无人机为代表的航空装备低成本大批量按需制造的需求。
责任编辑;zl
-
工业机器人
+关注
关注
91文章
3380浏览量
92957 -
3D打印技术
+关注
关注
4文章
221浏览量
32042
发布评论请先 登录
相关推荐
3D打印技术,推动手板打样从概念到成品的高效转化
有源晶振在3D打印机应用方案
3D打印技术应用的未来
3D打印汽车零部件建模设计3D打印服务
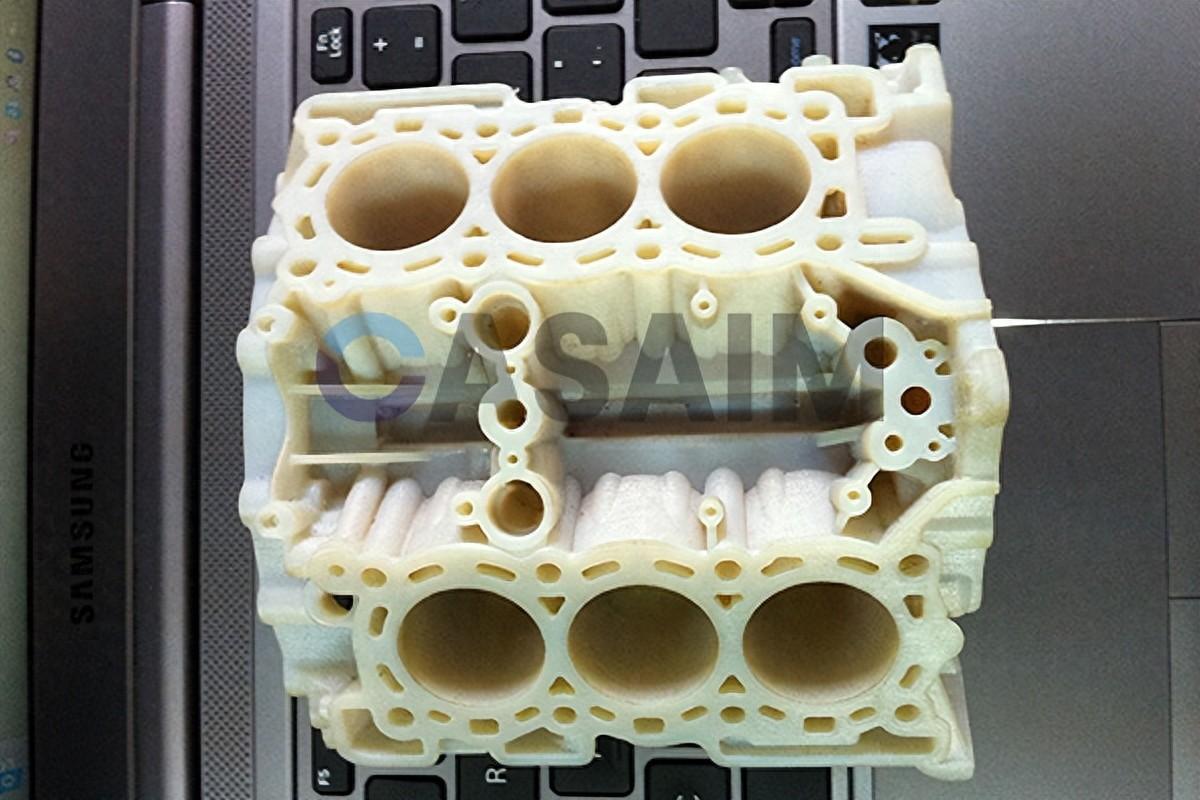
评论