半导体设备位于整个半导体产业链的上游,在新建晶圆厂中半导体设备支出的占比普遍达到 80%。一条晶圆制造新建产线的资本支出占比如下:厂房 20%、晶圆制造设备 65%、组装封装设备 5%,测试设备 7%,其他 3%。其中晶圆制造设备在 半导体设备中占比最大,进一步细分晶圆制造设备类型,光刻机占比 30%,刻蚀 20%,PVD15%,CVD10%,量测 10%,离子注入5%,抛光 5%,扩散 5%。
17 年全球半导体设备市场总量约为 566 亿美元,同比+37%,2018 年预计在 600 亿美元规模。中国是全球半导体设备的第三大市场,17 年中国半导体设备 82.3 亿 元,增速 27%。
1.我国半导体行业政策历史演变
1956 年国务院制定的《1956-1967 科学技术发展远景规划》中,已将半导体技术列为四大科研重点之一,明确提出“在 12 年内可以制备和改进各种半导体器材、器件”的目标。同期教育部集中各方资源在北京大学设立半导体专业,培养了包括王阳元院士、许居衍院士等第一批半导体人才。
半导体产业链复杂、技术难度高、需要资金巨大,且当时国内外特定的社会环境,中国在资金、人才及体制等各方面困难较多,导致中国半导体的发展举步 维艰。(图表 1、2 为半导体产业链图)
直到 70 年代,中国半导体产业的小规模生产才正式启动。原电子工业部部长在其 著作《芯路历程》中回忆这一阶段历史,提到发展中第一个误区“有设备就能生产”, 70 年代从日本、美国引进了大量二手、淘汰设备建立了超过30 条生产线,但引进 后无法解决技术、设计问题,也没有管理、运营能力,第一批生产线未能发挥应有 的作用,就淡出了市场。
90 年代,国家再度启动系列重大工程,为改变半导体行业发展困境,最知名的为 908、909 工程,中国半导体人从中获得较多宝贵的经验教训,收获了两家较为成功的案例,分别为华虹及海思。908 工程在 1990 年启动,投资20 亿元建设国际 领先的 1 微米(1000nm)制程工艺的晶圆制造产线。由于中国彼时整体经济力量还在蓄积,因此经费、设备引进、建厂等环节仍然阻力较大,直至1998 年产线得以 竣工。此时国际工艺节点达到0.18 微米,中国生产线刚建成就落后两代。在 1996 年国家启动了“909”工程,整体投资约 100 亿元,并且做出很多打破审批的特事特 办,参与其中的公司如今只剩两家,一个是 909 工程的主体华虹集团,另一个则是 完全自筹 1.355 亿元资金的华为设计公司,也就是后来的海思。
2012 年之后,国家领导层逐渐认识到“政策在发改委、科研在科技部、产业在工信部、资金归财政部”的格局,导致半导体行业政出多门、相互牵制、难以统筹等 现实困难,因此积极调整发展思路,设立集成电路产业领导小组、发布《集成电路产业推进刚要》、筹建大基金等举措,进一步自上而下的理顺了半导体行业发展框架。在产业领导小组成立之后,各方面的政策、资金及配套资源得以集中,为半导 体行业的攻坚克难奠定良好的基础。
近年来国家层面发布的政策较多,其中最重要目标性政策有:
1、2012 年国务院主导,科技部印发“02专项”即《极大规模集成电路制造技术及 成套工艺》项目,也标志着集成电路成为国家级重点优先战略目标。“02 专项”核 心要点为开展极大规模集成电路制造装备、成套工艺和材料技术攻关,掌握制约产业发展的核心技术,形成自主知识产权;开发满足国家重大战略需求、具有市场竞争力的关键产品,批量进入生产线,改变制造装备、成套工艺和材料依赖进口的局 面。
2、2014 年 6 月国务院颁布《国家集成电路产业发展推进纲要》。纲要明确提出,到2020 年,集成电路产业与国际先进水平的差距逐步缩小,全行业销售收入年均 增速超过 20%,16/14nm 制造工艺实现规模量产,封装测试技术达到国际领先水平,关键装备和材料进入国际采购体系,基本建成技术先进、安全可靠的集成电路 产业体系。
3、2015 年发布国家 10 年战略计划《中国制造2025》。计划提出,2020 年中国芯 片自给率要达到 40%,2025 年要达到 70%。
4、2016 年,国务院印发《“十三五”国家战略性新兴产业发展规划。规划提出, 到2020 年,战略性新兴产业增加值(含半导体产业)占国内生产总值比重达到15%。
2.中国半导体设备现状
半导体设备具备极高的门槛和壁垒,全球半导体设备主要被日美所垄断,核心设备如光刻、刻蚀、PVD、CVD、氧化/扩散等设备的 top3 市占率普遍在90%以上。
目前光刻机、刻蚀、镀膜、量测、清洗、离子注入等核心设备的国产率普遍较低。经过多年培育,国产半导体设备已经取得较大进展,整体水平达到 28nm,并在 14nm 和7nm 实现了部分设备的突破。
具体来讲,28nm 的刻蚀机、薄膜沉积设备、氧化扩散炉、清洗设备和离子注入机 已经实现量产;14nm 的硅/金属刻蚀机、薄膜沉积设备、单片退火设备和清洗设备已经开发成功。8 英寸的 CMP 设备也已在客户端进行验证;7nm 的介质刻蚀机已被中微半导体开发成功;上海微电子已经实现 90nm 光刻机的国产化。在中低端制程,国产化率有望得到显著提升,先进制程产线为保证产品良率,目前仍将以采购海外设备为主。
光刻机:高精度光刻机被ASML、尼康、佳能三家垄断,上海微电子是国内顶尖的 光刻机制造商,公司封装光刻机国内市占率 80%,全球 40%,光刻机实现90nm 制程,并有望延伸至 65nm 和 45nm,公司承担多个国家重大科技专项及 02 专项 任务。 刻蚀设备:前三家厂商 LAM、东京电子、应用材料市占率超过 90%,国产刻蚀机 市占率仅 6%,中微半导体是唯一打入台积电 7nm 制程的中国设备商,北方华创的8 英寸等离子蚀刻机进入中芯国际,封装环节刻蚀机基本实现国产化,国产化率近90%。
镀膜设备:分为 PVD 和 CVD,其中 PVD 前三大厂商AMAT、Evatec、Ulvac 占 比96.2%,CVD 三大厂商 AMAT、TEL、LAM 占比 70%,国内厂商北方华创实现 28nm PVD 设备的突破,16 年国内市占率已经有 10%,封装设备中国产 PVD 市 占率接近 70%。CVD 中的 MOCVD 是国产化最晚的领域,目前已有 20%的国产化率。
量测设备:主要包括自动检测设备(ATE)、分选机、探针台等。前端检测前三甲厂商科磊、应材、日立占比 72%,后道测试设备厂商美国泰瑞达、日本爱德万占 全球份额 64%,分选机厂商科林、爱德万、爱普生等市占率高达 70%,而探针台 基本由东京精密、东京电子、SEMES 垄断。国内厂商长川科技测试设备主要在中 低端市场,主要在数模混合测试机和功率测试机。
清洗设备:主要设备厂商 SCREEN、东京电子、LAM 合计占比88%,目前国内的 盛美半导体的 SAPS 产品已经进入一流半导体制造商产线。北方华创整合 Akrion 后提供单片清晰和槽式清洗设备,已经进入中芯国际产线。至纯科技已经取得湿法 清晰设备的批量订单,未来五年超过 200 台的订单。
离子注入设备:应用材料占据粒子注入机的 70%以上的市场,高端离子注入机前三家包揽 97%市场份额,行业高度集中。目前国内只有凯世通和中科信有离子注 入机的研发生产能力,17 年凯世通已经销售太阳能离子注入机15 台。
3.中国半导体设备的政策支持
从政策上看,随着《国家集成电路产业发展推进纲要》《中国制造2025》等纲领的 退出,国内针对半导体装备的税收优惠、地方政策支持逐步形成合力,为本土半导体设备厂商的投融资、研发创新、产能扩张、人才引进等创造良好环境。
财政部先后于 2008、2012、2018 年出台税收政策减免集成电路生产企业所得税,对 2018 年以后投资新设企业或项目:
1)线宽<130nm 且经营期在10 年以上的,第 1~2 年免征企业所得税,第 3~5 年减半征收企业所得税;
2)线宽<65nm 或投资 额>150亿元,且经营期在15年以上的,第1~5年免征企业所得税,第6~10年减半征收企业所得税。2015 年财政部等四部委针对集成电路封测企业、关键材料和设备 企业出台税收优惠政策,自获利年度起第1~2年免征企业所得税,第3~5年减半征收 企业所得税。
从地方产业政策来看,多地退出集成电路产业扶持政策及发展规划,从投融资、企业培育、研发、人才、知识产权、进出口以及政府管理等方面退出一系列政策,对符合要求的企业给予奖励和研发补助。
4.中国半导体设备的问题、不足与解决方案
半导体设备门槛高,投入期长,属于典型技术和资本密集型行业,技术差距大。打破垄断、提高国产化率是当务之急。
我国半导体设备行业面临以下几个主要问题:
1、 研发投入有限,技术差距追赶缓慢。
近年我国半导体设备虽已取得长足进步,在各个领域已经实现 0 的突破,但是整体 研发投入相对海外依然较低,此外先进工艺节点的不断推进,使得国内的技术追赶之路困难重重。企业虽然持续加大研发力度,但随着摩尔定律演进,越先进的工艺制程研发成本就越高,能投入资金跟上脚步的半导体设备厂商已经越来越少,无形中增加了技术追赶的难度。
解决方案:技术难点的攻克可以通过国家重大专项的推进完成,企业和政府共同承 担高端设备的技术攻克,减轻企业端的研发投入压力,同时继续鼓励国内新建晶圆厂推动设备的国产化替代,给国内半导体设备厂商试错与提升的机会。针对不同的半导体设备制定国产化替代节点时间,对企业研发投入进行补贴,并积极利用国内各种融资途径扩大规模。
2、高端人才引进不足,核心人才流失,后备人才不足
人才已经成为中国半导体设备产业成长的瓶颈点,半导体人才的培养是一个漫长的 过程,尤其是在先进工艺、先进技术方面,更是花钱可能也达不到效果的。行业人才薪资相比海外偏低,保证新进人才是延续强劲成长、打破半导体设产业成长瓶颈的关键。2018 年全国本硕博毕业生数量超过800 万人,但集成电路专业领域的高校毕业生中只有 3 万人进入本行业就业。
解决方案:积极通过人才引进,股权激励,政府补助等方式进行高端人才的引进,政府牵头推进半导体行业的人才培养,通过产学研结合的方式,同时对半导体行业人才的住房等问题上进行政策倾斜。
科学布局,政府引导合理规划。集成电路产业发展的初期必须由政府来主导,当前集成电路的产业投资主体分散, 管理主体也非常分散,这对产业发展非常不利。到了目前阶段,制定规划,确立战略,科学布局,制定政策可能非常重要。政府要管理,但不能管理过度。管理一过度就管死,条条框框增多,政策多门,可能导致效率低下。
5.半导体材料现状、问题及应对措施
半导体材料产业分布广泛,门类众多,主要包括晶圆制造用硅和硅基材、光刻胶、高纯化学试剂、电子气体、靶材、抛光液等。以半导体产业链上下游来分类,半导体材料可以分为晶圆制造材料和封装材料。2016 年全球晶圆制造材料和封装材料市场规模分别为 247 亿美元和 196 亿美元。我国是全球最大的半导体消费国,也是全球最大的半导体材料需求国。2016 年全球半导体材料市 场规模为 443 亿美金,其中中国大陆市场销售额为 65 亿美金,占全球总额的 15%,超过日本、美国等半导体强国,仅次于***、韩国,位列全球第三。
同半导体设备等配套设施一样,我国半导体材料也面临着自给率不足、规模小、高端占比低等问题。与国外企业相比,我国半导体材料企业实力较弱,但随着 国家政策的支持、国内企业研发和产业投入增加等,各种材料领域均已取得突 破,在逐步实现部分国产替代。下面我们集中就几种核心的半导体原材料的现状、面临的问题以及应对措施进行分析。
1、硅片:
硅单晶圆片是最常用的半导体材料,是芯片生产过程中必不可少的、成本占比最高的材料。制造一个芯片,需要先将普通的硅原料制造成硅单晶圆片,然后 再通过一系列工艺步骤将硅单晶圆片制造成芯片。从市场规模上来看,2016 年 全球半导体硅片市场规模为 85 亿美元,占半导体制造材料总规模比重达 33%;2016 年国内半导体硅片市场规模为 119 亿元人民币,占国内半导体制造材料 总规模比重达 36%。无论是全球还是国内市场,硅片都是半导体制造上游材料中占比最大的一块。
全球最大的 5 家厂商(主要是德国及日本厂商)几乎囊括了全球 95%的 300mm 硅晶圆片、86%的 200mm 硅晶圆片和 56%的150 mm 及以下尺寸硅晶圆片。这一领域主要由日本厂商垄断,我国 6 英寸硅片国产化率为 50%, 8 英寸硅片国产化率为10%,12 英寸硅片尚未量产,完全依赖于进口。2017 年全球的集成电路硅片企业中,日本信越化学份额 28%,日本 SUMCO 份额 25%,***环球晶圆份额 17%,德国 Siltronic 份额15%,韩国 LG 9%。这五 家合计占了全球的 94%的份额。
2、光刻胶:
半导体光刻胶的市场较大,国产替代需求强烈。2015 年中国光刻胶市场的总 需求为 4390 吨,为 2007 年的 5.7 倍,目前半导体光刻胶的供应厂商要集中 在美国、日本、欧洲以及韩国等地。中国的光刻胶供应厂商多集中于 PCB 光 刻胶、LCD 光刻胶等低端领域。当前国内能够生产半导体光刻胶的厂商有北京科华微电子和苏州瑞红等。
3、靶材:
高纯溅射靶材主要是指纯度为 99.9%-99.9999%(3N-6N 之间)的金属或非金 属靶材,应用于电子元器件制造的物理气象沉积(PVD)工艺,是制备晶圆、面 板、太阳能电池等表面电子薄膜的关键材料。溅射是制备薄膜材料的主要技术 之一,它利用离子源产生的离子,在真空中经过加速聚集而形成高速的离子束流,轰击固体表面,离子和固体表面原子发生动能交换,使固体表面的原子离 开固体并沉积在基底表面,被轰击的固体是用溅射法沉积薄膜的原材料,称为 溅射靶材。
在晶圆制作环节,半导体用溅射靶材主要用于晶圆导电层及阻挡层和金属栅极的制作,主要用到铝、钛、铜、钽等金属,芯片封装用金属靶材于晶圆制作类 似,主要有铜、铝、钛等。
4、湿电子化学品
湿电子化学品(Wet Chemicals)指为微电子、光电子湿法工艺(主要包括湿法刻蚀、湿法清洗)制程中使用的各种电子化工材料。湿电子化学品按用途可分为通用 化学品(又称超净高纯试剂)和功能性化学品(以光刻胶配套试剂为代表)。
其中超净高纯试剂一般要求化学试剂中控制颗粒的粒径在 0.5µm 以下,杂质含量低 于 ppm 级,是化学试剂中对颗粒控制、杂质含量要求最高的试剂。功能湿电子化学品是指通过复配手段达到特殊功能、满足制造中特殊工艺需求的配方类或复配类化学品。功能性湿电子一般配合光刻胶用,包括显影液、漂洗液、剥 离液等。
2016 年全球湿电子化学品市场规模约为 11.1 亿美元。湿电子化学 品作为新能源、现代通信、新一代电子信息技术、新型显示技术的关键化学材 料,其全球市场规模自 21 世纪初开始快速增长。根据 SEMI 数据显示, 2016 年全球湿电子化学品市场规模约为 11.1 亿美元。
应对措施
随着我国半导体产业制造能力的提升,配套原材料的国产化继续提上日程。集成电路对原材料纯度等要求非常高,因为集成电路产品的价值非常高,导致原 材料供应商的选择非常严谨。我们建议对半导体原材料产业加大资源、人力等 投入的同时,可以在政策方面对下游制造企业使用国产化原材料进行补贴,推动下游企业与上游原材料企业共同进步,进口实现产业链的全国产化。同时在 新材料研发方面,国家在政策上给相关企业、人才等给予引导和支持。
免责声明:本文内容根据国信证券相关报告整理,著作权归作者所有。本文任何之观点,皆为交流探讨之用,不构成任何投资建议,也不代表本公众号的立场。如果有任何异议,欢迎联系国际第三代半导体众联空间。
-
半导体
+关注
关注
334文章
27351浏览量
218572 -
封装
+关注
关注
126文章
7895浏览量
142946 -
光刻机
+关注
关注
31文章
1150浏览量
47397
发布评论请先 登录
相关推荐
日本半导体设备出口暴增82%!一半买家来自中国
长江存储正加速转向国产半导体设备
中国半导体行业迎来黄金发展期,预计五年内产能将激增40%
日本半导体设备出口激增:中国需求引领行业复苏
半导体市场震动:中国预计将领衔全球晶圆设备支出
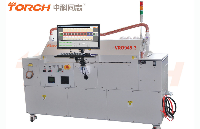
评论