屏式铠装热电偶爆管原因
1、设备检查
利用内窥镜对屏式铠装热电偶上联箱进行仔细检查,发现12组集箱24块隔板中的13块存在倾倒和裂开的情况,隔板在安装施工时为单面焊接,强度低,锅炉投运后,启停次数多,导致隔板在热胀冷缩的环境中,产生热交变应力,一旦其大于焊缝处的屈服极限应力时,焊缝开裂,并产生压差,随着运行时间的增加,隔板就有裂开角度增大甚至倒掉的情况发生,隔板的损坏,导致“U”型弯处管子内部蒸汽流量越来越低,最后蒸汽短路,造成管路干烧,也使得屏式铠装热电偶管子温度超温爆管。
前2次爆管采取掐管措施后,隔板倾倒导致同组集箱没有掐断的管子由于蒸汽短路,管路干烧,再次发生爆管。另外,根据爆口特征分析,屏式铠装热电偶管子也是由于长时间超温导致爆管。
2、管壁温度检测点工作异常
(1)屏式铠装热电偶管壁测温点热电偶固定块小,使用长0.5mΦ4mm的K型热电偶,由于铠装热电偶管壁温过高和存在振动,导致热电偶有烧爆、固定块脱焊和热电偶从固定块脱落的情况出现,使得铠装热电偶管壁温度测量不准确。
(2)热电偶接线盒位于铠装热电偶管子之间,热电偶补偿导线全部铺设在铠装热电偶管子中间的桥架,走向铠装热电偶平台西侧。铠装热电偶保温棉外白铁皮温度特别高,导致热电偶的补偿导线绝缘层烧坏,也会导致铠装热电偶管壁温度测量不准确。
桥架所在位置空间狭小,温度太高,屏式铠装热电偶管壁温度监测显示异常时,检修人员无法进入检修。只有到冬季锅炉停炉时,才能进行检修。由于爆管管壁温度测点测量不准确,岗位人员无法对其进行监控,就失去了参考依据,无法对铠装热电偶的运行状况做出调整和判断,导致屏式铠装热电偶一直处于没有监控的状态下超温运行爆管。
3、减温水不能投自动
一级减温水作为粗粗略调节,喷水量决定于减温器前的蒸汽参数,并保证屏式铠装热电偶管壁温度不超过允许值;二级减温水作为精细调节,控制铠装热电偶的出口汽温在额定值。一、二级减温水4个电动执行机构采用英国诸伊特公司的电动执行机构,型号为:JTV-64/S1825,水平安装,由于太重,电动执行机构重心和阀门重心不同心,下垂,导致一、二级减温水调节阀投自动时,由于动作特别频繁,经常出现卡死,调节阀不能动作的现象,减温水流量不能调节的问题,使得铠装热电偶的一、二级减温水调节系统失去控制功能,导致铠装热电偶温度不能得到有效控制。
屏式铠装热电偶爆管的改进措施
(1)对屏式铠装热电偶13块损坏的隔板,更换为新隔板,然后对24块隔板全部加装三角形限位挡板,并进行加固处理。对隔板倾倒的2组的换热管进行全部更换,以消除由于之前超温已经老化的钢管发生爆管的隐患。
(2)确保铠装热电偶温度测点准确。制作12个固定管璧测温点的热电偶固定块,孔径为Φ6mm,安装有夹紧热电偶的螺丝,用以替换原来的8屏式铠装热电偶壁温和4个一级铠装热电偶热端出口壁温的热电偶固定块。用6米或3米的热电偶代替原来0.5米热电偶。另外,对一级铠装热电偶冷端进口、出口和热段进口的8个蒸汽温度测点全部更换为长热电偶,把热电偶的接线盒就近分别固定在铠装热电偶平台的东西两侧。用耐高温补偿导线代替普通补偿导线,并更改线路走向,绕平台外侧走线,使补偿导线远离高温区域。消除了由于铠装热电偶温度高,导致补偿导线烧坏的隐患,达到随时可以对铠装热电偶温度进行检修的目的。铠装热电偶多个温度测点测量准确可靠,互为参考,实现岗位对铠装热电偶日常运行状态的准确分析和判断,一旦出现温度出现异常情况,可以及时做出调整。
(3)一、二级减温水4个调节阀进行移位改造;把阀门移位到水平直管段上,电动执行机构由水平安装改为垂直安装,解决了阀门和电动执行机构重心不同心,调节阀经常发生卡死的问题,实现减温水调节阀可以投自动,铠装热电偶不超温的目的。
-
热电偶
+关注
关注
5文章
939浏览量
75569 -
铠装热电偶
+关注
关注
0文章
21浏览量
8467
发布评论请先 登录
相关推荐
【热电偶测温】何为热电偶?
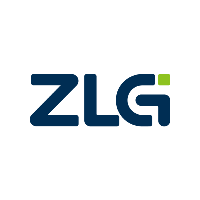
评论