树脂传递模塑(RTM)技术属于复合材料液体成型技术的范畴。RTM具有产品质量好、生产效率高、制造成本低,易于生产整体复合材料构件等突出特点,已经广泛应用于航空航天、建筑、通讯、交通、卫生、体育器材等领域。尤其在航空领域,RTM工艺凭借高减重和低成本优势,在先进飞机的承力和非承力结构中得到了广泛的应用。
树脂传递模塑(RTM)的工艺过程:首先在膜腔中铺放好与制件结构形式一致的增强材料预成型体,然后,在一定的温度、压力下,采用注射设备将低黏度的液态树脂注入闭合膜腔中,树脂在浸渍预成型体的同时,置换出膜腔中的全部气体,在模具充满模腔后,通过加热使树脂固化,然后脱模获得产品。
RTM树脂传递模塑工艺的优点
1、生产效率高:制造过程可实现机械化或自动化;能成型从小型精密到大型整体复杂的多种复合材料制件;对于带有夹芯、加筋和预埋件的大型、复杂构件,可通过一步浸渍、固化成型,代替传统成型工艺2步或多步成型的过程。
2、产品质量高:制件的表面质量、尺寸精度高,能制造具有良好表面质量、高尺寸精度的复杂部件,在大型部件的制造方面优势更为明显。
3、经济效果:RTM模具制造和材料选择灵活性强,根据不同的生产规模,设备的变化也很灵活,制品产量在1000-20000之间,采用RTM成型工艺可获得最佳生产经济效益。
4、环保:RTM成型工艺属一种闭模操作工艺,工作环境清洁,成型过程苯乙烯排放量小,有利于环保。
RTM成型工艺对原材料、生产过程工艺参数控制要求严格,要求增强材料具有良好的耐树脂流动冲刷和良好的浸润性,要求树脂黏度低,高反应活性,中温固化,固化放热峰值低,浸渍过程中黏度较小,注射完毕后能很快凝胶。一般来说,RTM成型工艺所选用模具材料应具备导热快、比热容低、热稳定性好、热膨胀系数小、加工工艺性好、质量轻、使用寿命长、成本低、使用和维护方便等优点。
RTM工艺设备主要包括模具、注射设备和固化设备3个部分,且各部分均会对整个研制生产过程具有决定性影响。
RTM成型工艺属于一种闭模操作工艺,成型中的树脂流动过程、压力和热传递过程及固化过程均发生在模具内部,成型模具的质量会直接“复制”在构件上,因此模具选材和设计是获得高质量、高精度、良好表面质量制件的前提。对于大批量或表面质量要求高的RTM制件,一般选用钢、锌铝合金或镀镍钢壳模。不同的成型方法对模具结构形式有不同的要求。
与传统的热压罐成型工艺相比,RTM成型工艺所用模具除要满足刚度和传热要求外,还对上、下模具的配合精度、模具表面质量、注射口和溢料口的设计,模具密封以及制件脱模装置等要求较高。成功的RTM成型模具应具有以下特点:结构精巧、温度场均匀、系统密封性好,合模、脱模等操作简单易行,所成型制件的内部质量和外形尺寸精度满足技术条件要求等。
对于传统的RTM工艺来说,通常采用注射设备进行树脂的注射,该设备一般包括树脂储料罐,树脂供给系统(恒压注射和恒流注射)、树脂输送管路、计量泵以及各种自动化仪表。注射设备按混合方式可分为单组分式、双组分式(加压式和泵式)和加催化剂泵式3种。产品的生产效率取决于成型设备的自动化程度,为提高注射效率,尽可能地节约树脂的用量,实现对产品的质量控制。
相对于注射,树脂的固化可以在不同的设备,比如一般在烘箱、压机、整体加热模具中进行。选择模具加热方式时,要综合考虑各加热方式的加热效率,加热系统温度均匀性,升、降温速率的可控范围,以及温度的控制精度、运行成本和环境保护等因素。对于烘箱加热来说,还要考虑烘箱的尺寸和内、外轨道的承载能力能够满足制件的需求。
随着RTM技术的发展,越来越多的复合材料企业采欧能机械智能模温机加热系统配合RTM成型生产线替代传统的大功率烘箱加注射设备的RTM工艺设备。欧能机械专注复合材料行业温控设备整体方案提供,研发有冷热切换、PLC智能控制模温机、阶段性控温模温机,满足碳纤维、玻璃钢、芳纶等复合材料成型模具控温,推动国内复合材料行业温控设备的进步。
RTM成型平台系统主要由预定型模具/模架、RTM模具/模架、模温机加热控温单元、液压系统、控制系统和RTM注射系统等部件构成。
整套自动化系统可同时实现模具加压/加热、树脂注射和固化等RTM成型工序,不仅能简化操作过程,提高生产效率、降低能耗、缩短制造周期,而且能降低RTM成型模具的设计刚度和制造成本,并可显著提高零件的成型质量。
自动化生产线按照RTM工艺将反应釜、真空设备、注射排气系统、加热系统、保压系统、模具等多种设备有机融合起来。上、下模单独移动、翻转、合模、合模翻转均采用自动化处理,整个过程动作连续,定位准备。模具加热、保压、注射均采用人机控制,操作简单。该套设备符合RTM成型工艺的要求,满足复合材料生产企业RTM生产自动化的要求。
责任编辑:gt
-
机械
+关注
关注
8文章
1590浏览量
40637 -
通讯
+关注
关注
9文章
907浏览量
34952 -
自动化
+关注
关注
29文章
5592浏览量
79394
发布评论请先 登录
相关推荐
探讨金刚石增强复合材料:金刚石/铜、金刚石/镁和金刚石/铝复合材料
复合材料的机械性能测试详解
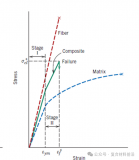
粉末涂料在复合材料部件上的应用
石墨烯化学镀铜对放电等离子烧结石墨烯增强铝基复合材料组织和性能的影响
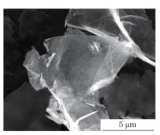
碳/碳复合材料的优点有哪些
高绝缘散热材料 | 石墨片氮化硼散热膜复合材料
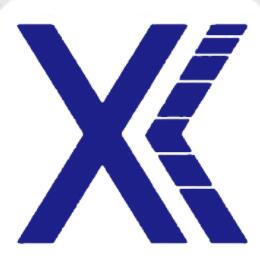
射频功率放大器在纺织复合材料研究中的应用
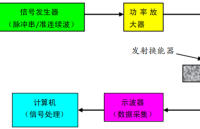
搪瓷釜脱瓷严重漏介质,用高分子复合材料轻松修补
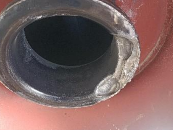
用量占比超90%,碳纤维复合材料成打造eVTOL首选
用于制造紫外超构表面的定制化高折射率纳米复合材料
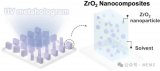
电子封装用金属基复合材料加工制造的研究进展
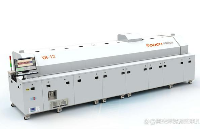
电子封装用金属基复合材料加工制造的研究进展
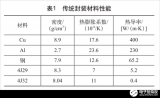
评论