微波功率模块是雷达收发组件的重要组成部分,其焊接质量和装配效率对有源相控阵雷达的性能及研制速度非常重要。本文介绍了微波功率模块焊接所采用的分步焊接、阶梯焊接和一次性焊接等三种工艺方法的特点,分析了工艺控制的关键参数和控制要点。以某型号雷达微波功率模块的装焊为对象,分别利用3种工艺方法对微波功率模块进行焊接,从生产效率、焊透率以及生产工艺性等方面对工艺方法进行对比分析。试验结果表明,对于器件数量较多的微波功率模块,优选一次性焊接工艺,次选阶梯焊接或分步焊接,对于器件数量较少的微波功率模块,优选分步焊接。
发射/接收(T/R)组件是广泛应用于机载、舰载、星载和弹载等新一代固态有源相控阵雷达的核心部件。其中,微波功率模块实现发射信号的合成和放大,是T/R组件中非常重要的组成部分。由于微波功率模块数量多、体积小、集成度高、电性能要求高、可靠性要求高和电磁兼容问题突出,采用传统的制造手段已无法满足整机小型化、集成化和高可靠性的需求。比如,微波功率模块装配质量的优劣、微波性能的一致性,对确保T/R组件的高性能起到了关键作用,同时还需要兼顾考虑生产周期和产能等要素。因此,微波功率模块的焊接工艺对T/R组件的性能以及研制进度具有重要影响,是有源相控阵雷达研制过程中的重要研究方向。
本文介绍微波功率模块的三种焊接工艺,并通过分析比较,确定了各自的应用条件。
一、微波功率模块焊接方法 微波功率模块由金属基板、微波介质板和元器件构成,见表1。其焊接内容包括微波介质板大面积焊接和元器件焊接两部分。微波功率模块焊接工艺主要有分步焊接、阶梯焊接和一次性焊接等三种方法,每种方法都能实现微波功率模块器件的焊接,但是它们存在各自的优缺点,需要依据产品的结构特点、器件类型及数量、产能要求、微波性能要求、可靠性要求以及生产设备的能力等选择合理的焊接工艺。
表1:功率模块主要组成 分步焊接 分步焊接工艺是指微波功率模块采用回流焊接和手工焊接分步实施的工艺方法,工艺流程如图2所示。该工艺一般分成两大工序:首先采用大面积焊接工艺,实现微波介质板与金属基板的高可靠连接,确保满足散热性能要求和微波接地要求;然后采用手工焊接工艺,实现阻容贴片元件、集成电路QFN和功率管等所有元器件的手工装焊。
图2:分步焊接工艺流程
该工艺主要适用于元器件数量较少且易于手工焊接的微波功率模块。它的优点是操作简单方便,不需要大型生产设备,工装设计简单。不过,手工焊接存在一定的缺陷:一方面,容易存在元器件的错焊和漏焊等问题,需要做好器件符合性检查;另一方面,针对一些接地的焊点,由于印制板已经与底板焊接,导致印制板的接地焊点热容较大,焊接难度大。
阶梯焊接 阶梯焊接工艺是指微波功率模块采用低温焊料焊接元器件和常温焊料焊接微波介质板与壳体的工艺技术,两种焊接工艺相结合使用。阶梯焊接的工艺流程如图3所示。首先采用表面贴装技术(SMT)工艺,实现元器件与微波介质板可靠高精度焊接;然后采用大面积焊接工艺,实现微波介质板与金属基板的高可靠连接,确保满足散热性能要求和微波接地要求。
图3:阶梯焊接工艺流程
该工艺主要适用于元器件适合表贴,并且数量多、类型复杂的微波功率模块。它的优点是自动化程度高、装配效率高、模块焊接一致性好、可靠性高;缺点是两种焊料体系梯度焊接,工艺窗口小,温度控制难度大。
一次性焊接 一次性焊接工艺是指将SMT工艺和大面积焊接工艺相结合,实现微波功率模块元器件、微波介质板和壳体同步焊接,其工艺流程如图4所示。一次性焊接工艺先进行SMT工艺,完成微波介质板焊膏印刷和元器件贴装,再进行大面积焊接工艺,完成壳体点涂焊膏以及微波介质板、金属基板和工装的装夹,最后进行一次性回流焊接。
图4:一次性焊接工艺流程
一次性焊接工艺主要适用于适合表贴,并且元器件数量多、类型复杂的微波功率模块。它的优点是自动化程度高、一致性好、可靠性高,而且只需一次回流焊接工序,使得工序简化,但该方法对工装设计要求较高。
二、微波功率模块焊接工艺的控制要素 微波功率模块三种焊接工艺有五个关键工艺技术要素,分别为大面积焊接阻焊技术、焊接温度窗口控制、大面积焊接工装设计、壳体内焊膏点涂技术和自动化焊接工艺。 大面积焊接阻焊技术
在大面积焊接过程中,阻焊剂(胶)会阻止焊料从焊接区渗透到非焊接区,并且焊接后,可轻易去除。焊料的流淌主要与炉温、工装施加到印制板的压力、焊料涂覆与非焊接区域的距离以及印刷网板的占空比等因素有关。经过大量的工艺试验和产品应用表明,以上四个因素控制得当,可以不用阻焊剂(胶),同样可达到控制焊料从焊接区流淌到非焊接区的效果,并且工艺过程中,减少了涂覆阻焊胶的工步,提高生产效率。
焊接温度窗口控制
阶梯焊接工艺在器件的封装和集成电路封装中已得到了广泛应用,同时也可应用于微波电路功能模块的焊接应用。微波介质板先经过SMT焊接(采用常温焊膏),后经过大面积焊接(采用低温焊膏)。在大面积焊接时,需要监测印制板表面器件焊点处的峰值温度,不能高于甚至接近首次焊接所用焊料的熔点,否则,器件会重熔。所以,在大面积焊接过程中,需要对再流焊炉的性能进行跟踪监测,操作比较繁琐。
针对焊接质量要求较高的产品,需掌握再流焊炉温度变化特性。首次生产时,每间隔一个小时监测一次炉温变化;当了解了炉温的情况后,每周跟踪两次,监测炉温是否发生变化。如果炉温比设定好的温度曲线偏离±5℃,需要重新调整温度曲线。
由此可见,阶梯焊接工艺的难度较大,需要控制工艺窗口,而分步焊接和一次性焊接则不涉及该问题。 大面积焊接工装设计
大面积焊接中工装设计是非常关键的技术,需要考虑工装材料(铝合金、石墨和不锈钢等)、压力分布均匀性、工装透气性、工装热容大小、印制板受压方式及压力大小。
针对压力位置,分步焊接工艺中,微波介质板表面平整,工装的施压位置不受限,只需考虑受力均匀;而阶梯焊接和一次焊接工艺中,微波介质板的受力位置不能干涉焊好的元器件,如果无法避免器件干涉问题,那么该器件的焊接工序需要调整到引脚器件焊接工序中,同时,在网板设计时,考虑该器件不设计焊膏印刷区域。
壳体内焊膏点涂技术
壳体点涂焊膏技术是通过选择合适黏度的针筒焊膏和针头内径,同时配合自动化点涂设备,在壳体内自动涂覆并居中均匀分布焊膏。在分步焊接与阶梯焊接工艺中,大面积焊接工序的焊膏通过印刷机印刷在微波介质板的背面;而在一次性焊接工艺中,微波介质板上表面印刷焊膏后,下表面无法印刷焊膏,此时采用壳体点涂焊膏的技术,可以实现焊膏的涂覆。
自动化焊接工艺
生产的智能化要求全设备能够联网运行。微波功率模块的分步焊接工艺无法实现自动化生产,而阶梯焊接工艺和一次性焊接工艺中,可实现微波功率模块焊接全自动化生产。
通过三种工艺方法所涉及的工艺技术比较,得出生产过程的实现难度由低到高分别为:分步焊接、一次性焊接和阶梯焊接。
三、微波功率模块焊接工艺对比研究 以某型号雷达中的功放模块为例,抽样数为3,000只功放模块,物料类型及数量见表2,分别采用三种工艺形式,各生产1,000只,进行生产效率、焊透率和焊接工艺性对比分析研究。
表2:试验件器件类型及数量 生产效率比较 采用三种微波功率模块焊接工艺分别生产1,000只模块,根据统计,人员配置及产能见表3。
表3:三种工艺的人员、时间和效率比较
通过表3可见:
1)从产能比较,使用阶梯焊接工艺方式的产能大约是分步焊接工艺方式的4倍,而阶梯焊接工艺与一次性焊接工艺相当。可见,阶梯焊接工艺和一次性焊接工艺效率较高。
2)与其他焊接方式比较,分步焊接的手工焊接工序占用工时多,并且比例较高,严重影响了生产效率。 焊透率分析 三种工艺方式下生产的微波功率模块,分别抽取了5只模块,观察基板空洞率,计算焊透率并进行对比。试验结果见表4。
表4:不同焊接工艺中微波功率模块基板焊透率
通过表4的比较分析得出,三种焊接方式的焊透率都满足大于80%的指标要求,并且焊透率大小相当。
工艺性评估
三种微波功率模块焊接工艺使用的工艺技术类型有所差别,具体见表5。
表5:微波功率模块焊接工艺对比 通过表5的比较得出,三种焊接方式的工艺难度系数由高到低依次为阶梯焊接、一次性焊接和分步焊接。
四、结论 从微波功率模块的生产效率、模块的焊接质量和加工难度等方面,对三种工艺方式进行综合性比较,从而得出各自的适用场合,以指导生产。
1)分步焊接工艺中器件通过手工焊接,焊接一致性差,容易造成错焊和漏焊等问题。该工艺适用于器件量少的模块,同时不需要较复杂的工装设计和大型生产设备。
2)阶梯焊接和一次性焊接可以实现全自动化生产,器件焊接的一致性好,漏焊和错焊的概率低,都适用于器件量大的模块。只是阶梯焊接的技术难度大于一次性焊接。
综上所述,微波功率模块的贴片器件数量较多的情况下,优选一次性焊接工艺,次选阶梯焊接工艺,最后选择分步焊接工艺;贴片器件数量较少的情况下,优选分步焊接工艺。
作者:杨海华,杨涛,张玮
-
元器件
+关注
关注
112文章
4716浏览量
92289 -
微波
+关注
关注
16文章
1044浏览量
83698 -
功率模块
+关注
关注
10文章
467浏览量
45107
原文标题:微波功率模块焊接工艺研究
文章出处:【微信号:Mouser-Community,微信公众号:贸泽电子设计圈】欢迎添加关注!文章转载请注明出处。
发布评论请先 登录
相关推荐
智能化多通道焊接控制器:实现高效精准的焊接工艺控制技术解析
焊接机器人焊接工艺了解吗?管道焊接机器人可视焊缝追踪系统介绍
手持式电阻焊电源在现代焊接工艺中的应用与优势探析
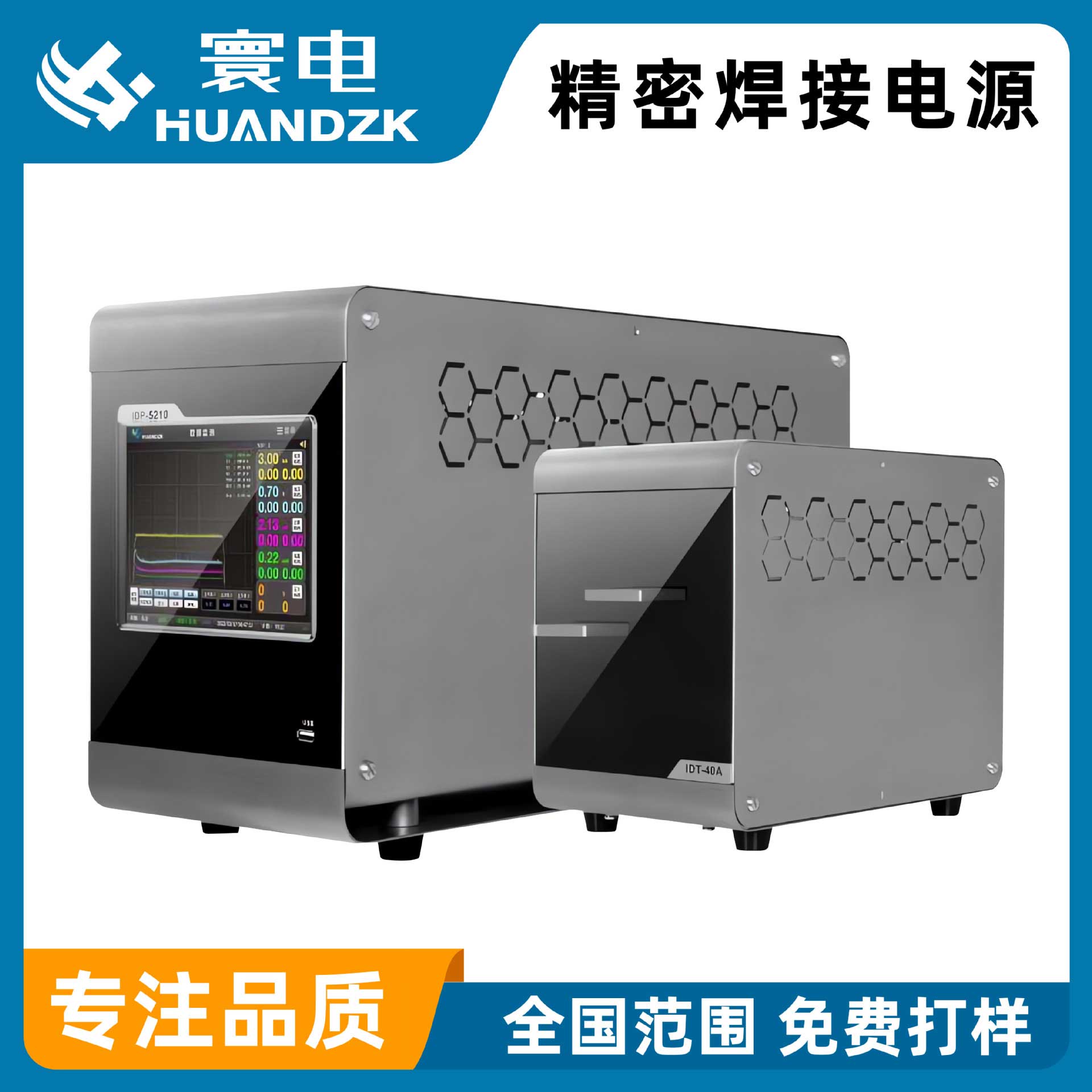
探究自动化焊接工艺中的核心设备:逆变电源技术在现代焊接领域的应用与发展
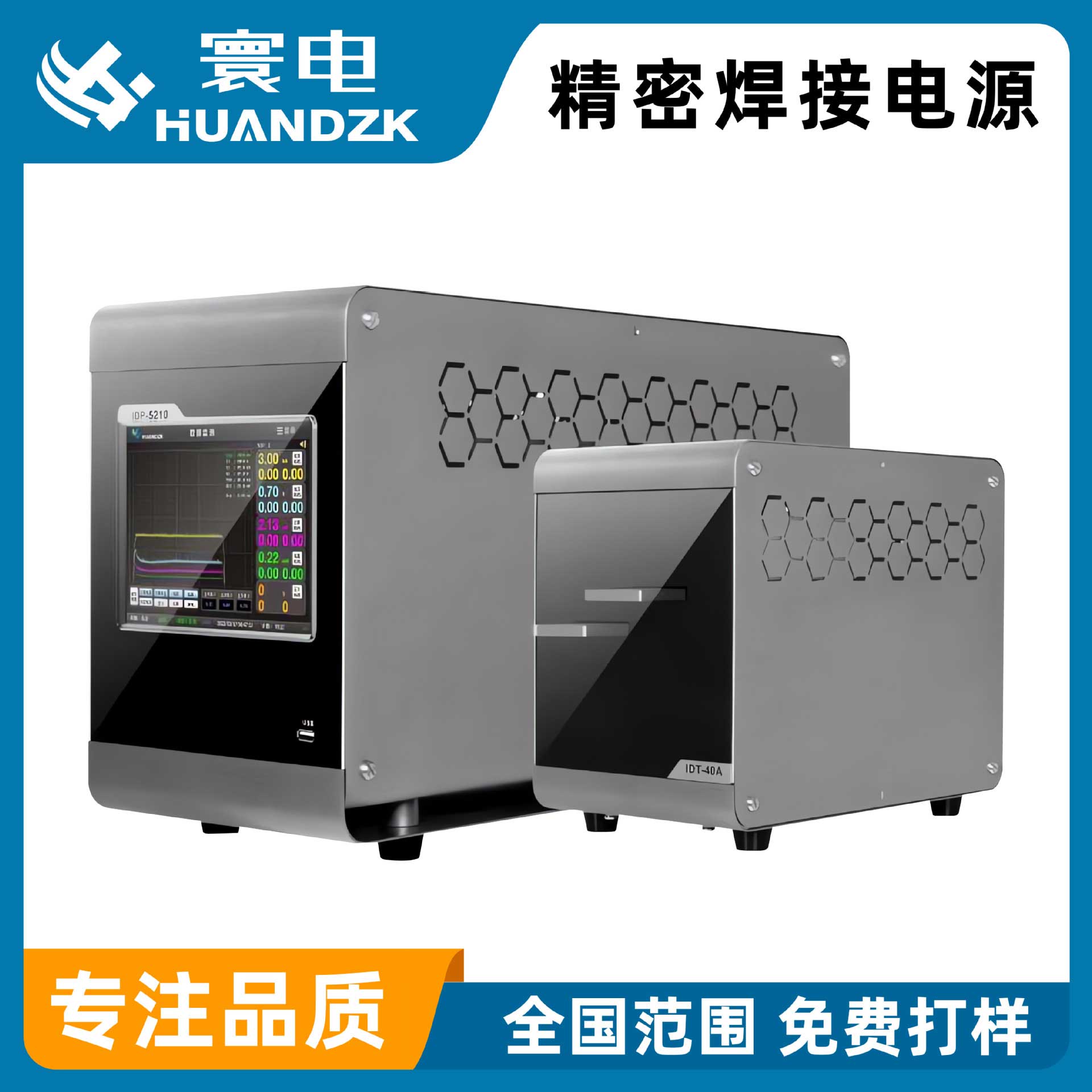
薄板拼焊激光焊接工艺
激光焊接工艺有哪些?
焊接工艺对机器人的要求有哪些
光纤激光焊接机:现代焊接工艺的变革引领者
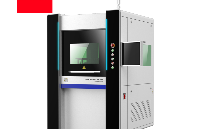
评论