汽车线束是汽车电子电气系统中重要的组成部分,也是整车故障的多发环节。如何在设计过程中提高汽车线束工作的可靠性,降低整车故障率,保证发生故障时在最短的时间内排除故障,成为汽车电气系统设计中关注的焦点。本文对整车电气线束布置过程中的设计原则进行了系统分析与探讨。
汽车电气系统设计从整车或总成项目启动开始,主要设计流程如图1所示。作为设计流程的关键阶段,电气系统原理设计与电气系统三维布置需要同步进行,假如将电气系统原理设计比作是灵魂,那么电气系统三维布置则是承载灵魂的躯体。电气系统三维布置完成的品质直接影响样车试制的品质,高效的三维布置可以减少试制过程出现的问题,降低试制费用,缩短整车设计时间。
电气系统三维布置主要是指利用CATIA、PRONE等三维软件对整车电器元件、电线束及相关固定结构在整车上进行布置,包括电器件三维布置以及电气线束三维布置两部分,其中电器件主要根据整车具体结构进行布置。本文根据实际汽车线束三维布置经验总结出了一些基本原则及注意事项,主要从线束装配性、线束可维护性以及线束安全可靠性等方面进行阐述,为汽车电气线束的三维布置设计提供了基本设计准则。
汽车线束三维布置的一般流程
汽车电气系统三维布置按照图2所示设计流程进行。将整车电气系统根据位置不同分成底盘、仪表板、发动机、变速器等不同模块,针对每个模块首先进行电气设备布置,此项工作由电气系统设计师与整车系统工程师共同完成。电气设备布置方案确定后,开始进行线束走向设计,按汽车电气线束布置的原则进行线束走向设计,并对走向方案进行校验,直至合理。完成电气线束走向设计后,根据线束走向确定固定方式及结构,并对固定方式及结构进行强度、干涉性校验,根据最终确定的设计方案绘制电气线束二维图、相关固定结构二维图。下面主要探讨汽车线束布置过程中的基本设计原则及注意事项。
汽车线束布置基本原则及注意事项
在对汽车线束进行三维走向设计时,一定要充分结合车身钣金、车架等线束依附体的具体情况对整车电气件进行综合全面的考虑。进行线束布置设计的同时也要考虑线束固定问题,根据钣金件结构、整车机械结构确定固定方式以及固定点的数量;控制器较多且需集中布置的情况下,对控制器的布置也要着重考虑。
2.1 易于装配在汽车线束布置装配性方面主要侧重考虑两方面内容:线束本身易于装配;线束固定结构易于装配。
2.1.1 线束总成本体易于装配汽车线束布置时要考虑尽量不给整车装配过程增加过多工序,对于整车的不同区域可采用分装方式,如仪表板、车门、顶棚、左右车身等。并且在设计过程中有针对性地考虑不同区域的特点,所设计的线束走向不得影响其他整车零部件的装配;在线束过孔时,所需过孔的外包络直径最大的插接器,其直径一定要小于饭金孔直径,否则会造成线束无法穿过。
2.1.2 线束固定结构易于装配在设计线束固定方式及固定结构时一定要考虑装配性,不能在追求固定可靠的同时给装配过程增加过多工序,根据实际设计经验总结出以下注意事项。1)尽量采用简洁的固定方式,尤其对于空间狭小区域,如车门内走线、白车身与内饰间走线,由于其空间狭小,尽量采用塑料卡扣或胶带固定。2)过孔橡胶护套应设计成在小于100 N安装力的情况下,即可完全装配于钣金孔内。3)对于需要用手指压装的固定件,操作力为45 N ;用手压装的固定件,操作力为75 N。4)在线束固定结构以及相关功能盒体设计过程中,尽量采用常用的标准件,并且标准件种类尽量少,通过前期设计减少装配及维修中专用工具的使用。5)对于装配时插接器或线束固定结构需要穿过驾驶室的情况,其紧固件如果采用普通六角螺母和螺栓,一个人很难独立完成,此时一般考虑采用焊接螺母或自攻钉进行固定。6)线束的固定孔要尽可能开在结构件的平面区域,在曲面上固定时,最好在结构件上做出小平面。7)在进行电气线束布置时,尽可能考虑大总成模块化装配,提高生产线装配速度。如变速器线束、发动机线束分别装配到变速器与发动机本体上,之后作为整体装配到底盘上。
2.2 良好的可维护性在整车电气线束布置时,要重视售后维护环节。良好的可维护性体现在出现电气系统故障时,在最短的时间内将故障排除,以及进行故障排除时避免维修操作对其他部件造成损坏。如果线束或电气件出现问题,拆卸要简单,同时拆卸时不影响其他无关的零部件,否则就会造成一些不必要的浪费,增加维修时间。因此,要保证整车电气系统具有良好的可维护性,电气线束布置时要考虑到以下几个方面。1)、线束插接件尽可能布置在触手可及的地方。2)、线束插接件如果只能用单手插拔,其对插端要被可靠固定。3)、同一部位的插接件要用颜色、大小、内部定位等方法进行区分,防止错插。4)、插接件末端的线束应该预留一定的长度,以便于插接件的插拔:对于开关端的线束建议预留80~100 mm,组合仪表、音响、空调面板、熔断丝盒等维修率比较高的电器件,其后端线束根据总成安装位置预留到容易插拔的长度。图3为某越野车仪表板功能开关线束,为便于功能开关拆卸、维修,在进行此处线束设计时,将功能开关分支预留了100 mm的余量。
2.3 线束具有良好的可靠性线束如何可靠工作也是汽车电气线束布置时需要着重考虑的问题,主要通过采取增加线束覆盖物对线束本体进行防护、对线束通过钣金孔处进行可靠防护、增加线束固定支架、在条件允许的情况下尽量减少线束分段等措施,提高线束一工作的可靠性。1)线束穿过钣金孔时,通过增加过孔护套避免金属件对线束的磨损。2)线束越过饭金件时,为了避免饭金件边缘对线束造成磨损,考虑采用异型扎带或在饭金件上增加橡胶条做防护。3)线束布置应沿边、沿槽,防止线束直接承受压力。4)电线束尺寸应符合QC/T 29106的规定,其中电线束基本尺寸极限偏差取值如表1所示。
5)线束直径过大需要弯折一定角度时要预留足够空间,一般线束弯折半径要大于线束直径的两倍,此问题在直头插接器根部要重点考虑,以免弯折空间过小对线束及插接器造成损坏。6)所有布置在运动件附近的线束,与运动件间应至少留有50 mm间隙。7)两个相对运动件上的线束,必须被固定到每个运动件上。8)运动件、开闭件(如车门)、间的线束要留足最大开度的长度,并考虑在部件最小开度时的堆积空间和固定方式。图4所示为某款轻型车车门与白车身间线束过渡情况,在进行该线束设计时要考虑车门的最大开度,并根据车门最大开度时车门与白车身间距离确定线束长度,线束长度确定后需要验证车门关闭时车门与白车身间隙大小,为避免关闭车门对线束护套及线束造成挤压,可在车门或白车身对应位置区域做下凹处理。
9)一段长线束相邻固定点间距离不能大于300 mm,当车体结构不能保证时相邻固定点间距离最大不能超过400 mm。10)线束弯曲处,弯曲点前后均应设置固定点。11)钣金结构件不允许开孔时,可考虑熔焊卡条或焊接凸起支架及凸焊螺栓(卡柱)、进行线束固定。12)需要在外面连接电器件插接件且需再塞回固定的线束,除为保证线束维修性而留足拉出操作时需要的长度,还要考虑固定后的线束堆积空间和线束固定方式。13)设计时线束分支必须有足够的松弛度(大于线束最小长度25 mm)、,使其不对所连电器件产生预应力。14)由于车辆差异化,装配时暂未用到的线束分支,按照100~200 mm理顺后按图5所示固定在主干线或支架上,捆扎线束时最小弯曲半径不能小于线束直径的2倍。比如某越野车底盘线束备胎升降开关分支的处理,由于该车备胎升降开关布置在车厢上,因而在进行底盘装配时需要将该段线束可靠捆扎于底盘线束主干上。
15)根据线束位置不同、工况不同,设计不同的线束防护形式,如车门线束以及内饰板内部的左右车身线束,由于空间狭小,一般考虑采用胶带防护;底盘与车体接触较多,且暴露在室外,一般采用具有防水性能的闭口波纹管防护;在整车温度较高部件(如发动机等)、附近布线,需要采取隔热措施。
2.4 电气回路尽可能缩短电气线束回路一定要尽可能缩短。考虑好拆装工艺后,就要考虑怎样才能尽量缩短电线回路,因为较短的回路有以下几点优势:①线路段消耗电压低,电压就可以匹配到电器件上,它们相应的信号强度较高;②减轻整车质量;③降低线束成本。
2.5 线束分段设计要慎重有些时候为了实现装配的工艺性,在进行汽车电气线束三维设计的时候可能会将原本可以是1段的线束分成2段,这样就势必增加线束插接件,在进行分段设计时针对插接件的增加一定要考虑以下几个问题。1)线束上总的电压降增加,电器件上的信号强度衰减。2)插接件的增加,势必会造成电气连接的不可靠连接点增加。3)为了固定增加的插接件,势必要增加支架或考虑其他固定方式。4)增加电线束组装工时和物料成本。鉴于以上几点,在条件允许的情况下,尽可能减少线束分段,采用贯穿式线束设计。
总结
随着整车电子电气技术的发展,车载设备也越来越多,因而对整车电气线束的可靠性提出了越来越高的要求。在电气系统开发阶段合理而可靠的电气线束布置可以缩短开发周期、降低车辆成本、提高电气系统工作的可靠性。如何利用三维软件对电气三维布置进行更加精确的设计需要我们继续探索。
-
电气系统
+关注
关注
1文章
354浏览量
24263 -
线束
+关注
关注
7文章
974浏览量
25983
原文标题:汽车电气线束布置要点浅析
文章出处:【微信号:Rosenberger_Auto,微信公众号:罗森伯格汽车电子】欢迎添加关注!文章转载请注明出处。
发布评论请先 登录
相关推荐
汽车线束布置的四大注意事项
导通线束测试仪应用过程中应注意哪些细节?
汽车线束设计原则
线束固定扎带的布置原则
汽车车门线束的连接布置原则
汽车线束布置设计与原则
新能源线束合理化设计与布置方案
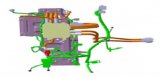
线束设计过程中的技术要点
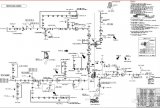
评论