据外媒报道,日产研发了一种新制造工艺,能够将用于飞机、火箭和跑车的材料用于更加大众化的汽车。
该项新工艺加快了碳纤维增强型塑料(CFRP)汽车零部件的研发。此种材料虽然重量轻,但是非常坚固,可以用于制造出更安全、更省油的汽车。此外,当将该材料用于车身上部分时,可以降低汽车重心,从而实现更灵活、更令人兴奋的驾驶体验。
日产计划利用该项新工艺大规模量产CFRP零部件,并在更多汽车中使用。与传统方法相比,该项创新技术可以将此类零部件的开发周期缩短一半,成型周期缩短约80%。
虽然碳纤维的益处早已为人所知,但与钢铁等其他材料相比,此种材料的价格比较昂贵。此外,CFRP零部件的成型很难,这也阻碍了利用此种材料大规模制成汽车零部件。
日产公司在现有生产方法的基础上找到了一种新方法,称为压缩树脂转移成型(compression resin transfer molding)。现有的方法包括让碳纤维形成正确的形状,并将其放置在一个模具中,而上层模具与碳纤维之间会有一个微小的间隙。然后,将树脂注入该纤维中,并让其变硬。
日产的工程师研发了技术,可以精确地模拟树脂在碳纤维中的渗透过程,同时利用模内温度传感器和透明模将树脂在模具中的流动行为进行可视化展示。成功模拟的结果是制成了一个高质量的组件,而且开发时间更短。
责任编辑:tzh
-
传感器
+关注
关注
2551文章
51097浏览量
753514 -
制造
+关注
关注
2文章
510浏览量
23996 -
汽车零部件
+关注
关注
0文章
275浏览量
16989
发布评论请先 登录
相关推荐
3D打印汽车零部件模型定制服务,多种材料、快速打印-CASAIM

三品PLM系统在汽车零部件行业的解决方案及应用
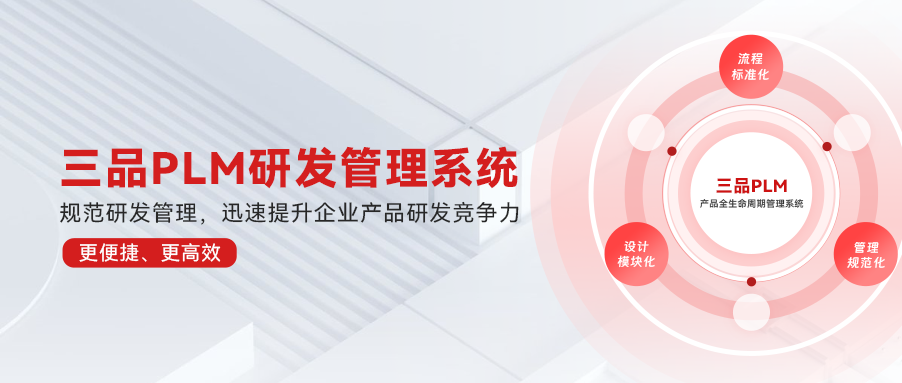
如何解决汽车零部件清洁度问题
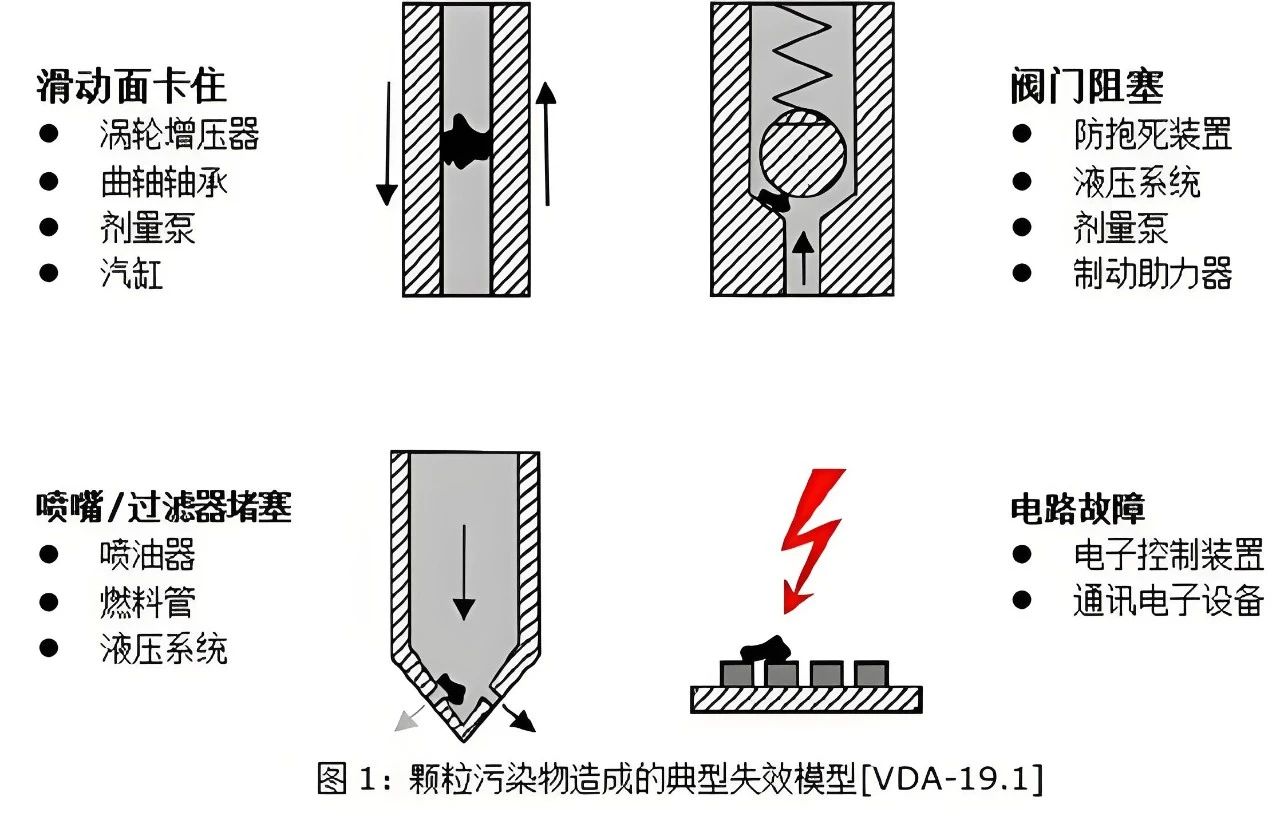
激光淬火技术在淬火发动机零部件的工艺应用
3D扫描仪为民航零部件制造精准护航!
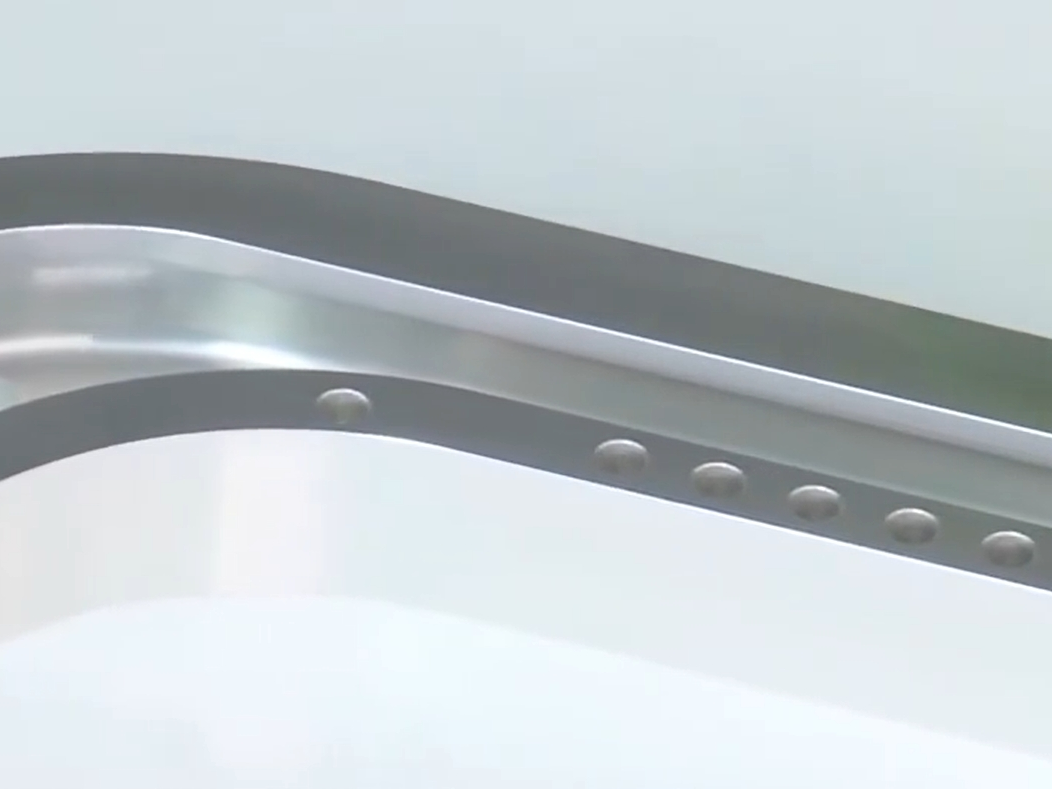
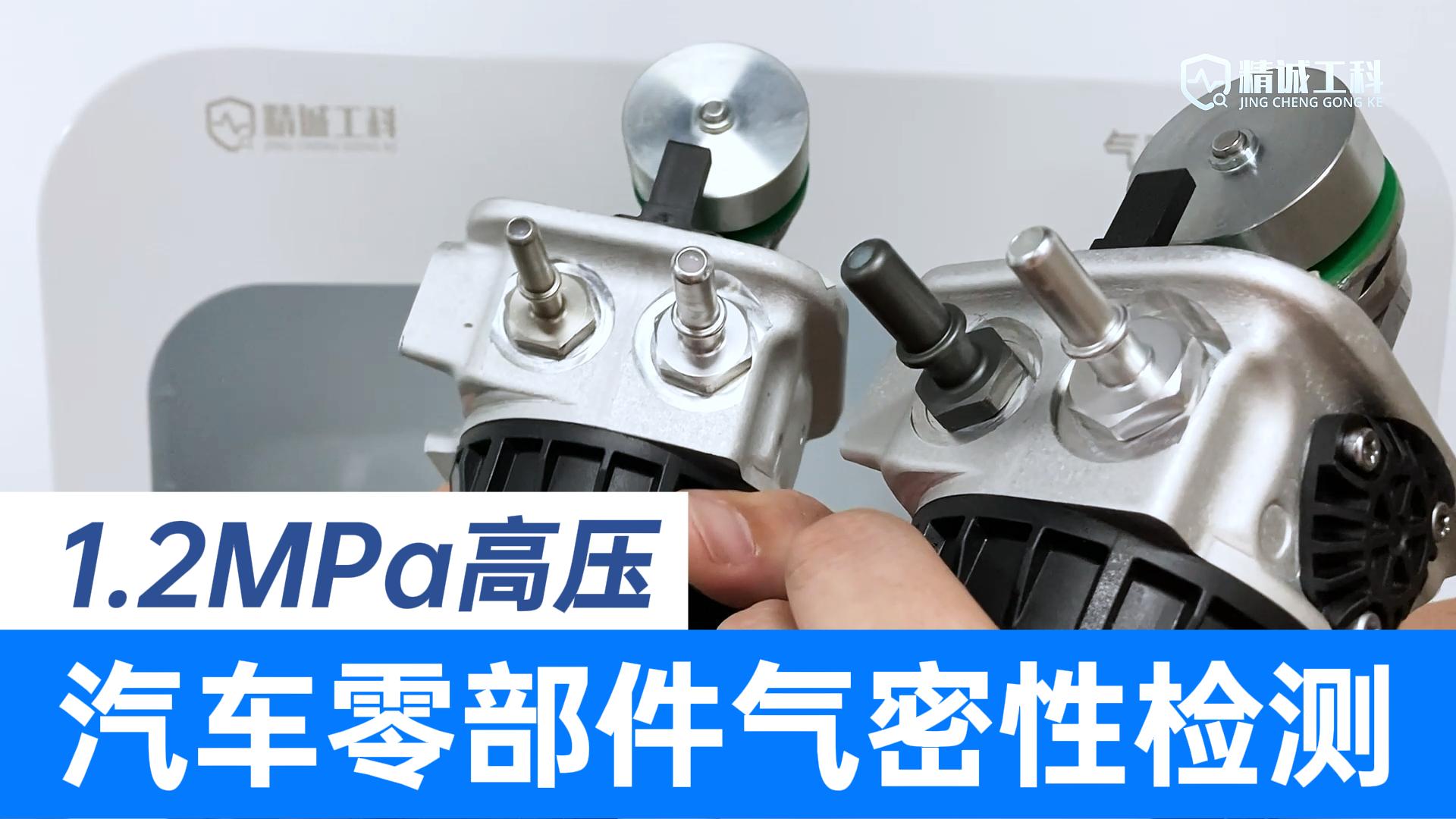
三坐标CMM三次元用于测量电子零部件
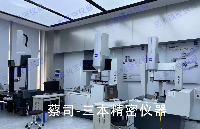
三坐标测量机在汽车零部件质量控制中的应用
汽车零部件MES系统功能
海康威视助力汽车零部件制造企业数字化转型
汽车零部件需要做哪些环境试验?
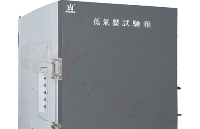
评论