锑化铟焦平面器件是通过倒装互连工艺来使锑化铟芯片的每个像元与读出电路的相应单元之间实现电连通的。该器件采用背光照结构,即目标辐射从焦平面器件的背面入射,由芯片的每个像元转换为电信号,再经过读出电路的读取、放大和输出。图1为红外焦平面混成芯片的成像测试示意图。为了提高光吸收量子效率,需要将锑化铟衬底的厚度减薄至少子空穴的扩散长度以下,这样才能实现高灵敏度探测。
图1 红外焦平面混成芯片的成像测试示意图
与其他半导体材料相比,锑化铟的表面硬度更软(其硬度为223 Knoop,硅的硬度为1150 Knoop),所以在抛光时更容易产生表面划伤,导致粗糙度增大,表面复合速率加快,造成电性能下降,从而影响器件的性能。因此需要选择合适的腐蚀液对锑化铟背面进行腐蚀以减少划道,然后采用非接触式清洗方法清洗表面,进而得到洁净表面。本文针对锑化铟背面减薄后的腐蚀和清洗方式进行研究,并提出一种新的锑化铟背面减薄后的表面处理方法。
1试验
用蜡将倒装互连后的锑化铟焦平面器件粘接在玻璃板上,用光刻胶保护好焊盘,并用非接触式测厚仪测量器件衬底的厚度;用抛光机通过粗磨、抛光、精抛分步将锑化铟衬底去除至设计厚度。利用不同的酸处理器件表面,去除损伤层;采用非接触式表面处理方法,以避免清洗时产生划道。基于红外成像测试系统进行成像测试,观察红外成像结果中是否有划道,并对表面处理的效果进行评估。图2所示为现有技术中的常规背面减薄工艺流程与本文提出的新方法的对比情况。
图2 现有技术中的常规背面减薄工艺流程与本文提出的新方法的对比图
2结果与讨论
2.1用不同酸处理时的影响
2.1.1测试图像
图3为锑化铟器件的红外测试图像。其中,图3(a)为未经过酸腐蚀的器件样品的红外成像图,图3(b)为该器件样品的显微照片(局部图)。从中可以看出,器件表面上存在明显的划道痕迹。图3(c)为经过初始腐蚀液处理的器件样品的红外成像图。虽然没有划道,但由于表面腐蚀速率不均匀,测试时部分区域的电平较高,所以在测试图像上出现了亮斑。图3(d)为用改进过的腐蚀液处理后的器件样品的红外成像图。可以看出,器件表面上没有划道,且图像均匀。
图3 (a)未经酸处理的器件样品的红外成像图;(b)未经酸处理的器件样品的显微照片(局部图);(c)经初始腐蚀液处理的器件样品的红外成像图;(d)用改进过的腐蚀液处理后的器件样品的红外成像图
2.1.2表面形貌
图4所示为基于扫描电镜拍摄的用改进过的腐蚀液处理后的锑化铟器件的表面形貌。与未经过腐蚀液处理的锑化铟器件表面相比,它没有明显的划道痕迹,且表面光亮、整洁。
图4 用改进过的腐蚀液处理后的锑化铟器件表面的扫描电镜图
2.2表面清洗方法优化
传统的清洗方法为手工操作,其主要步骤如下:
(1)去蜡。用镊子将器件夹住,同时用酒精棉球擦拭器件背面和四周。
(2)清洗焊盘。将酒精棉球制作成空心球状,擦拭器件正面的电路焊盘。
(3)清洗器件表面。将器件放入装有丙酮的培养皿中,然后将长丝棉制作成空心球状,并用其擦拭器件表面。
(4)镜检。将器件吹干,无沾污、无水痕即为合格。
传统清洗方法存在的问题是,在用长丝棉擦拭器件表面时,棉花容易在表面上带入划道;清洗工艺对操作人员的手工要求高,工艺重复性差。
我们对其进行优化的思路是减少长丝棉与器件表面的接触,即在器件精抛后,用光刻胶将表面覆盖。调研可去除蜡但对光刻胶没有影响的有机试剂。表1列出了蜡、光刻胶与去蜡液及石油醚的互溶试验结果。从中可以看出,去蜡液和石油醚对蜡均有较好的去除效果,而且都不会对光刻胶产生影响。
表1 蜡、光刻胶与有机试剂的互溶试验结果
由于经过去蜡液或石油醚浸泡的芯片表面会有试剂残留,需要进一步对去除去蜡液或石油醚进行试验。表2列出了去蜡液、石油醚与无水乙醇的互溶试验结果。从中可以看出,石油醚在10 min内完全溶解于无水乙醇试剂中。
表2 去蜡液、石油醚与有机试剂的互溶试验结果
通过上述试验可以确定非接触清洗工艺:在器件精抛后,用光刻胶覆盖表面;待光刻胶干燥后,从玻璃板上取下器件,用石油醚浸泡20 min(去除蜡),然后用无水乙醇浸泡10 min(去除残留的石油醚)。
3结束语
本文针对器件经过背面减薄后的表面处理进行了研究。通过腐蚀液腐蚀去除划道,并采用基于石油醚和无水乙醇的非接触式清洗方法,有效降低了器件表面上产生划道的几率,同时避免了由于表面腐蚀速率不均匀导致测试时部分区域电平较高、在测试图像上出现亮斑等情况;另外还提高了工艺的重复性,使锑化铟器件的红外成像均匀且没有划道,从而提高了该器件的成品率。在后续研究中,由于仍有相关工艺与表面接触,需要采取有效措施,以减少由人为失误导致的划道。
-
元器件
+关注
关注
113文章
4760浏览量
93205 -
电信号
+关注
关注
1文章
841浏览量
20771
原文标题:锑化铟焦平面器件背面减薄后的表面处理方法研究
文章出处:【微信号:MEMSensor,微信公众号:MEMS】欢迎添加关注!文章转载请注明出处。
发布评论请先 登录
相关推荐
详解14种常用产品表面处理工艺
晶圆为什么要减薄
特瑞仕超薄电源IC的薄型解决方案
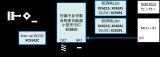
基于相变材料的可重构超构表面用于图像处理
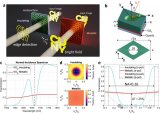
揭秘PCB板的八种神秘表面处理工艺
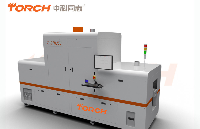
评论