核心观点:
短期看下游需求复苏。受下游诸如汽车、3C 等行业影响,自 18 年 9 月起我国工 业机器人产量进入负增长,行业持续低迷,但从 19 年 10 月开始,增速首次转正 并保持上涨趋势至今,今年年初虽受到新冠疫情影响但并没有改变这种趋势。最新 数据显示,11 月份中国工业机器人产量为 23635 套,创下历史单月产量新高。1- 11 月份,国内工业机器人产量累计 20.68 万套,同比增长 22.2%,行业已经基本 摆脱低谷,进入新一轮的景气周期。
长期看机器换人加速。根据 IFR 数据统计,2019 年我国每万名产业工人所拥有的 工业机器人数量仅为 187 台,远低于日本、德国等传统制造业强国的水平。近年 来,一方面人口红利的逐渐消失使我国人工成本的快速上升,另一方面工业机器人 产业链上国产化率的不断提升又降低了企业进行自动化改造的资金门槛,二者将共 同推动机器换人的进程,带动工业机器人行业的发展。
人机协作是行业的发展趋势。当前,工业机器人的应用场景愈加广泛,苛刻的生产 环境对机器人的体积、重量、灵活度等提出了更高的要求,工业机器人正向着小型 化、轻型化、柔性化的方向发展,类人精细化操作能力不断增强。随着机器人易用 性、稳定性以及智能水平的不断提升,机器人的应用领域逐渐由搬运、焊接、装配 等操作型任务向加工型任务拓展,人机协作成为工业机器人研发的重要方向。
1. 工业机器人行业持续复苏,机器换人与国产替代双重驱动
1.1. 工业机器人行业拐点已到,疫情不改复苏趋势
根据国家统计局数据显示,我国工业机器人产量增速从 2017 年年底开始逐 渐放缓,自 2018 年 9 月起我国工业机器人产量进入负增长,行业持续低迷,这主 要是因为工业机器人作为典型的通用设备,具有一定的周期性,受下游诸如汽车、 3C 等行业景气度的影响较大。但从 2019 年 10 月开始,我国工业机器人产量增 速首次转正,并保持上涨趋势至今,增幅屡创新高,2020 年年初虽然受到新冠疫 情影响但并没有改变行业上行的趋势。
最新数据显示,11 月份中国工业机器人产量为 23635 套,创下历史单月产量 新高,同比增长 31.7%,虽然相比上月 38.5%的增速有所放缓,但仍是今年第三 高增速。今年 1-11 月份,国内工业机器人产量累计 20.68 万套,同比增长 22.2%, 长期来看,整个工业机器人行业已经摆脱了前两年的低谷,进入新一轮的景气周 期。
从短期看,我们认为本次工业机器人行业的爆发主要是受益于两点:一是国 内疫情结束后下游制造业的快速复苏,二是疫情后各生产企业自动化升级需求的 进一步增强。
首先,在其他各国因疫情影响停工停产时,中国作为目前疫情控制最为得当 的国家,大量承接了来自世界各地的生产制造需求,这部分因为国外疫情而承接 的订单促使国内制造业形成了一个小高峰,间接带动了工业机器人行业的增长。 凭借着对新冠疫情采取的有效应对手段,国内整体经济得以快速恢复,使得中国 成为目前世界主要经济体中唯一保持 GDP 正增长的国家。
此外,经过本次疫情,各个生产企业在复工复产的过程中逐渐认识到自动化 生产、减小人员依赖的重要性,开始尝试提高自己的自动化率,同时国家出台的 各类免税政策也让这些企业有了富余资金去购买相关设备,这也是疫情以来工业 机器人下游需求持续增长的重要原因之一。
我国疫情后制造业 PMI 的变动情况也有所体现。11 月份,中国制造业 PMI 为 52.1%,比上月上升 0.7 个百分点,连续 9 个月位于枯荣线以上,且仍在继续上升 中,表明我国制造业的恢复性增长有所加快,整个工业机器人行业也有望跟随下 游制造业的景气同步增长。
1.2. 政策驱动下工业机器人市场迎来迅速发展
自德国首先于 2011 年提出以智能制造为核心的“工业 4.0”战略之后,各国 纷纷开始制定相关政策大力发展制造业,以智能化为标志的第四代工业革命正在 全球范围内蓬勃展开。其中,工业机器人作为工业化和信息化的完美结合,以其 天然的数字化特性,打通了单个生产设备到整个生产网络的连接,进而支撑起第 四次工业革命丰富多彩的应用场景。如果说,过去二十年互联网的发展联通了我 们每一个人,那么未来二十年工业互联网的发展将会联通每一台工业机器人,从 而带来生产效率乃至生产方式的全面革新。
工业机器人在国内的发展最早可追溯到科技部的 863 项目,对机器人相关技 术研发给予扶持。2006 年 2 月,国务院印发了《国家中长期科学和技术发展规划 纲要(2006-2020 年)》,智能机器人首次被纳入前沿技术中的先进制造技术,之后 随着 2015 年《中国制造 2025》战略出台并实施,各级地方政府积极推进地区规 划政策落实,中国工业机器人产业也迎来了迅速发展。
当前,工业机器人在汽车、3C 电子、金属制品、塑料及化工产品等行业已经 得到了广泛的应用,并且随着性能不断提升,以及各种应用场景的不断明晰,我 国工业机器人产业呈现出不断深化、不断扩大应用的态势,目前我国工业机器人 市场约占全球市场份额的三分之一,是全球第一大工业机器人应用市场。2019 年 全年,全球共新增工业机器人 36.5 万套,亚洲地区的安装量占到了全球总安装量 的三分之二,其中中国以 14.05 万台的安装量遥遥领先,几乎是第二名日本的三 倍。
根据中国电子学会及 IFR 数据统计,在 2014 年到 2017 年的 4 年间,我国工 业机器人市场规模几乎实现了翻倍增长,年均复合增速接近 30%,2018 年虽然受 到宏观环境的影响增速放缓至 5.9%,但仍然高于全球增速 5.3 个百分点。此外, 与发达国家相比,我国制造业自动化水平仍然比较低,我国生产制造智能化改造 升级的需求日益凸显,工业机器人需求依然旺盛,预计到 2023 年,我国工业机器 人市场规模将突破 100 亿美元。
1.3. 人口红利逐渐消失 倒逼自动化进程加速
改革开放以来,大量劳动力涌入城市,以低廉的劳动力成本为特征的劳动密 集型产业推动中国逐步成为世界工厂,拉动过去中国经济高速增长。然而近年来, 人口红利的逐渐消失与人工成本的快速上升对制造业未来的发展带来了极大的挑 战。
根据国家统计局数据显示,我国人口结构中 15-64 岁所占的比例自 2010 年 以来就呈现出逐渐下降的趋势,2019 年占比为 70.7%,较 2018 年下降 0.5 个百 分点,并且降幅还有进一步扩大的趋势。
同时,企业的用人成本也在不断攀升,2019 年制造业生产工人平均年薪达到 了 58356 元,同比增长 8.21%。劳动力人口的不断下降与人工成本的不断上升倒 逼企业进行自动化改造,“机器换人”将会成为未来十年我国制造业转型升级的主 旋律。
另一方面,我国工业机器人的密度相比发达国家仍有较大差距。根据 IFR 数 据统计,2019 年我国每万名产业工人所拥有的工业机器人数量仅为 187 台,而韩 国、日本、德国、美国、意大利等传统制造业强国的数据分别为 855 台、364 台、 346 台、228 台和 212 台,从渗透率的角度来看,相比我国世界工厂的地位,我 国自动化水平还有极大的提升空间。
从增长率来看,2019年我国每万名产业工人所拥有的工业机器人数量较2018 年有 33.6%的提升,大幅超过韩国、日本约 10%左右的增速,而德美意等国同期 的增速仅为 5%左右。乐观预计,未来 3-5 年,随着产业转型升级与自动化进程的 不断推进,我国工业机器人密度有望逐渐追平日本、德国的水平。
1.4. 工业机器人产业链一览
工业机器人产业经过 30 余年的发展,已经形成了一条完整的产业链。工业机 器人产业链上游是核心零部件,包括控制器、伺服系统和减速器三大部分,这三 种部件是工业机器人中核心技术之所在。产业链中游是机器人本体制造,发那科、 ABB、库卡、安川四大家族具有明显优势,占据了全球工业机器人市场份额的 40%, 而国产厂商因为起步较晚,还处在追赶阶段。下游是系统集成,目前主要集中在 汽车制造和 3c 电子行业,二者几乎占据了整个工业机器人下游应用的半壁江山, 但在食品饮料、物流、光伏、锂电等长尾市场增速较快。
从整个产业链来看,上游核心零部件是一台工业机器人成本中占比最高的部 分,约为 70%左右,系统集成硬件成本较低,比较偏向服务,提供解决方案,而 中游机器人本体厂商或采购核心零部件或使用自家的核心零部件,因此成本相差 较大,二三线品牌因为不掌握核心零部件盈利水平较低。
从盈利能力来看,产业链上游核心零部件、中游本体和下游集成的毛利率水 平基本符合“微笑曲线”,上游、下游毛利较高,中游本体毛利最低。上游核心零 部件的高毛利主要来源于技术壁垒,下游集成高毛利主要来自于品牌溢价及客户 资源壁垒。
2. 工业机器人核心竞争力
2.1. 工业机器人的大脑-控制器
控制器相当于工业机器人的大脑,负责控制整台机器人的运动,核心技术集 中于软件算法。控制器最能体现各个厂商的调教水平与风格,一般由机器人厂家 自主设计研发,是各个机器人厂商的“软实力”。
工业机器人控制器的主要任务是接收来自视觉、力觉等传感器的检测信号, 根据操作任务的要求驱动机械臂中的各个伺服电机,进而控制机器人在工作空间 中的运动位置、运动姿态、速度、轨迹、操作顺序及动作的时间等,同时控制器也 具有各类输入输出接口、人机交互界面等,拥有编程简单、在线操作提示、使用软 件菜单操作和使用方便等特点。
控制器与机器人本体一样,一般由机器人厂家自主设计研发。目前主流机器 人厂商的控制器均为在通用的多轴运动控制器平台基础上进行自主研发,各品牌 机器人均有自己的控制系统与之匹配,因此控制器的市场份额基本和机器人市场 份额保持一致,发那科、库卡、ABB、安川分别占据前四名,国内企业控制器尚未 形成市场竞争优势,占比仅为 16%左右。
近年来,国内运动控制技术也有了较快的发展,一些传统 CNC 设备的生产厂 家凭借着已有的数控技术基础开始研制具有运动控制特征的产品,使得通用运动 控制产品开始扩展开来。其中机器人专用运动控制产品的开发和行业应用的推广 也逐渐走向成熟和产业化,这类企业以广州数控、埃斯顿等为代表,他们不只开 发出机器人专用的控制系统,还借此进入机器人行业,并成为国产机器人企业中 的代表。
此外,国内也诞生了一批专注于运动控制产品的企业,为无力研发自主控制 器的小型工业机器人厂家提供解决方案,这类企业以固高科技为代表,固高科技 是国内较早实现六轴机器人控制系统产业化的企业之一,目前主要向工业机器人 集成商提供控制系统平台。
目前国产控制器与国际先进水平相比还存在较大差距,主要体现在核心底层 算法上,例如参数自整定,抑震算法,转矩波动补偿等等,导致国产工业机器人精 确性、稳定性、故障率和易用性等关键指标不如发那科、ABB、安川、库卡“四大 家族”的产品,这也和国内厂家重硬件、轻软件有关。当前工业机器人需要实现的 动作愈加复杂,想要在高速的运动中实现精准的控制,其背后需要的是长期的多 轴联动控制技术积累,控制器必须足够“聪明”,而先进核心算法的缺失使国产控 制器要想从“能用”到“好用”还有很长的路要走。
2.2. 工业机器人的执行机构-伺服系统
当控制器发出运动指令后,需要相应的机构部件去精确执行,这就是伺服系 统的主要作用。伺服系统可以看作是工业机器人的小脑,根据控制器的命令为机 器人关节的运动提供精准的位移、速度与力矩,一个典型的伺服系统包含有伺服 驱动器和伺服电机两部分。
伺服驱动器中主要包括整流部、逆变部、控制部等部分,伺服电机一般包含 电机和编码器两个部分,编码器可以将精确测量的转子位置与电机转速反馈至驱 动器,从而形成一个完整控制回路。商用电经过整流、逆变,接收控制部得到的指 令信号与编码器的反馈信号,最终输出合适的 SPWM 波形驱动伺服电机运转。当 前交流伺服驱动器设计中普遍采用基于矢量控制的电流、速度、位置 3 闭环控制 算法,对闭环系统的设计、调试要求都很高,这也是伺服系统中核心难点所在。
伺服系统的下游行业应用主要集中在电子及半导体制造设备、机床、工业机 器人、锂电制造设备等领域,其中在工业机器人上的应用大概占据整体应用的 9.4%,由于对位移、速度等的精度要求较高,应用在工业机器人上的多为伺服系 统中的高端产品。
从市占率来看,外资品牌占据了国内伺服系统市场的大部分份额。以三菱、 安川、松下为代表的日系伺服系统占据了市场的前三名,占比合计超过 30%,紧 随其后的是台系伺服的台达和欧系伺服的西门子,占比分别为 9.9%和 6.5%,而 以汇川技术和禾川科技为代表的国产伺服厂商虽然近年来发展十分迅速,但市占 率仍然较小,分别为 6.2%和 1.5%,还有很大的提升空间。
目前国产伺服系统与国际先进水平在动力输出功率方面大体相同,没有明显 差距,差距主要体现在响应速度、大小和稳定性等方面。在运动控制性能方面,西 门子的产品具备 2kHz 的速度环频率响应能力,安川为 1.5kHz,多摩川和汇川则 都为 1.2kHz,欧系产品优势更为明显,尤其在要求高速度和精度的领域。日系伺 服产品的稳定性较好,可以满足大部分应用领域的需求,尤其是小功率电机,优 势明显。在伺服系统大小方面,为了配合机器人的体形,伺服系统必须体积小、质 量小、轴向尺寸短,相比国产伺服系统,日系、欧系产品更加紧凑。
2.3. 伺服系统的搭档-减速器
虽然有了控制器发出的指令、有了伺服系统去执行,但是这样输出到终端还 是不够。以安川的小型伺服系统为例,最高转速为 3000r/min,力矩为 0.016~ 0.16N.m,而机器人上各个轴的工作转速每分钟不过一百转左右,所需转矩却远远 超出伺服电机的工作范围,这时就需要搭配减速器使机器人每个轴的输出参数达 到所需要求。
如果工业机器人使用伺服电机直接驱动,在低频运转下容易出现发热和低频 振动,不利于其精确、可靠地运行。而减速器能够使伺服电机在一个合适的速度 下运转,并精确地将转速降到工业机器人各部位需要的参数,提高机械体刚性的 同时输出更大的力矩。例如,使用一个减速比为 50:1 的减速器就能轻松将额定扭 矩为 0.1Nm 的电机扭矩提升到 5Nm,使其能够承受更高的负载,并且适当减小 输出转速,提高控制分辨率和闭环精度。
在工业机器人领域使用的减速器主要有 RV 减速器和谐波减速机两类。其中 RV 减速机拥有更高的精度和承载能力,但体积重量较大并且结构复杂,一般放置 在机座、大臂、肩部等重负载的位置;而谐波减速器结构简单紧凑,但承载能力不 高,多用在小型机器人和大型机器人的小臂、腕部、手部等低载荷的部位。两种减 速器使用场景不同,是互补的关系,并不存在相互替代的竞争。
减速器的核心难点主要在于精密加工、齿面热处理、装配精度、大规模生产 与检测等工艺环节上,恰恰是我国制造业基础配套体系中最薄弱的部分,需要长 期的经验积累。与国外产品相比,国产减速器主要在使用寿命及稳定性上有较大 差距,刚刚投入使用时各项性能接近国外产品,但随着一段时间的使用后磨损加 剧,出现漏油,精度、刚度等指标有所下降,这种不稳定性使得国产减速器大多只 能应用于中低端市场,很难进入国际一线工业机器人品牌的供应链。
减速器作为纯粹的机械零件,核心技术与工业机器人并不相关,因此包括 ABB、 发那科、安川、库卡在内的工业机器人巨头也均不自研减速器,全部向外采购。目 前 RV 减速器和谐波减速器市场基本由日系厂商垄断,以纳博特斯克、住友、哈 默纳科、新宝为代表,占据了全球机器人减速器市场的大部分份额,其中纳博特 斯克与哈默纳科分别在 RV 减速器领域和谐波减速器领域处于垄断地位。
国产减速器厂商近年来有一定的进步,主要以谐波减速器领域的绿的谐波为 代表,产品性能已经和哈默纳科达到同一水平,近年来逐步开始进入国际主流机 器人厂商进行测试,有望在未来 1-2 年内实现快速放量。而在 RV 减速器领域, 由于其复杂且精密的机械结构,加工难度较大,国产 RV 减速器厂商与日系品牌 还有很大差距。
3. 工业机器人的多应用场景
3.1. 工业机器人概览
工业机器人自诞生以来,演变出越来越多样的机械结构,应用场景越来越广 泛,当前,工业机器人可以分为多关节机器人、SCARA(水平多关节)机器人、 坐标机器人、协作机器人、Delta(并联)机器人、AGV(工厂物流仓储机器人) 等。
2019 年,多关节机器人在国内工业机器人市场销量约为 10 万台,是应用最 为广泛的工业机器人,占比达到 69%,SCARA 机器人销量约为 3.5 万台,占比 23%,协作机器人销量约为 0.6 万台,占比 4%左右,并联机器人销量约为 0.5 万 台,占比约为 3.4%。
从品牌结构来看,2019 年国内工业机器人市场前四名仍然被发那科、ABB、 库卡、安川所占据,占比分别为 12%、11%、8%、7.6%,“四大家族”仍然是工 业机器人领域的第一梯队,爱普生、雅马哈、那智等二线品牌凭借着 SCARA 以 及小六轴等技术水平要求不高的机器人也抢占了一定的市场。而国产厂商虽然近 年来进步明显,但市占率仍然较低,埃斯顿作为出货量最高的国产工业机器人厂 商市占率仅为 2.4%,汇川、众为兴和埃夫特等市占率均不到 2%。
3.2. 不同种类的工业机器人
3.2.1. 多关节机器人
多关节机器人一般指六轴机器人,拥有 6 个可以自由旋转的关节,提供的 6 自由度可以使其在三维空间中自由活动,可以模拟所有人手能实现的动作,通用 性极高,应用也最为广泛,但同时控制难度也最高,价格最为昂贵。
搭配不同的末端执行器,多关节机器人可以实现不同的功能,较高的自由度 使得多关节机器人可以灵活的绕开目标进行作业,适用于包括搬运、装配、焊接、 打磨抛光、喷涂、点胶等几乎所有的制造工艺。
2019 年,国内多关节机器人市场前四名分别是发那科、ABB、库卡和安川, 市占率合计超过 50%,与其他二线品牌拉开了较大差距。国产品牌虽然也有一定 的市场份额,但除埃斯顿外产品主要集中在 20kg 以下的中小负载多关节机器人 市场,高于 20kg 的大负载多关节机器人市场还是外资品牌的天下。
从出货量上来看,由于多关节机器人凭借其强大的性能,多应用于汽车工业, 而随着传统汽车行业近年来需求逐渐触顶,固定资产投资的下滑对多关节机器人 的出货量也造成了一定影响,18 年后增速逐渐放缓。但随着未来新能源汽车需求 的崛起与小六轴机器人在一般制造业应用的不断扩展,多关节机器人的出货量增 速有望回升至 8%左右。
3.2.2. SCARA 机器人
SCARA 机器人,即水平多关节机器人,与多关节机器人不同的是 SCARA 机 器人一般只有 4 个可以自由活动的关节,前 3 个关节使得 SCARA 机器人只能在 二维平面内自由活动,第 4 个关节连接末端执行器,只能沿 Z 轴上下移动,提供 了受限的三维活动能力。但与此同时,较少的自由度意味着需要更少的伺服电机 和减速器,控制算法也会更加简单,体积也可以做的更加小巧,相比多关节机器 人成本得以大幅降低。
SCARA 机器人可以看作是只能处理部分限定工作的特化型机器人,比如在 平面上的挑拣、装配、点胶、锁附、贴标等,并且较小的体积也减小了生产线空间 的占用,非常适合 3C 电子等产品体积不大的行业。
从市场结构来看,2019 年国内 SCARA 机器人市场主要由爱普生和雅马哈占 据,合计占比约 45%,三菱、众为兴、汇川、台达紧随其后,市占率均为 7%-8% 左右。由于 SCARA 机器人技术门槛不高,各厂商之间价格战较为激烈,毛利率 显著低于多关节机器人,因此包括 ABB、发那科、库卡和安川在内的“四大家族” 均不把 SCARA 机器人作为重点产品,市场主要由各二线机器人品牌占据。
从出货量上来看,SCARA 机器人除 2019 年受到宏观环境影响出现短暂负增 长,其余时间均保持着较快增长,并且受益于近年来 3C 行业可穿戴设备、TWS 耳机等产品的火爆,SCARA 机器人未来仍有望维持较高的增速。
3.2.3. 并联机器人
并联机器人,可以定义为动平台和定平台通过至少两个独立的运动链相连接, 机构具有两个或两个以上自由度,且以并联方式驱动的一种闭环机构,一般以 3 轴 最为常见。并联机器人的特点为无累积误差、精度较高,驱动装置可置于定平台 上或接近定平台的位置,这样运动部分重量轻,速度高,动态响应好。 并联机器人在生产线上一般用于对轻小物件的分拣、搬运、装箱、贴标、检测 等工作,广泛应用于食品、制药、电子、日化等行业。
并联机器人问世之初的应用 对象主要是大型乳企以及液体袋装药和药片的生产药企,大多负载都在 3kg 以下, 后续的增长主要来源于乳制品行业之外的食品行业,如糖果、巧克力、月饼等生 产企业,以及医药、3C 电子、印刷以及其他轻工行业。
2013 年及以前,国内并联机器人市场主要由 ABB、发那科等少数几个品牌开 拓,但随着 2012 年 ABB 公司 Delta 并联机器人专利解禁,国内市场上涌现出 了一大批并联机器人企业,基本都直接开拓市场,并且涉及众多应用行业,较大 程度拓宽了市场应用范围。从市场结构来看,2019 年国内并联机器人市场主要由 ABB、天津晨星、上海勃肯特和发那科占据,占比分别为 16.8%、11%、10%和 9%,国产并联机器人厂商市占率较高。
从出货量上来看,相对于多关节型工业机器人,国内并联机器人当前市场需 求明显偏小,占整个工业机器人市场的出货量不足 5%。预计 2020 年并联机器人 全年出货量可以达到五千余台,随着下游应用细分行业的进一步扩展以及使用场 景的进一步丰富,未来两年并联机器人行业年均增速预计可达 10%左右。
3.2.4. AGV 机器人
AGV (Automated Guided Vehicle) 机器人,一般称为 AGV 搬运机器人或 AGV 小车,是以电池为动力源的一种自动操纵行驶的工业车辆。区别于固定安装 在流水线旁的传统工业机器人,AGV 机器人主要功能集中在自动物流搬转运,通 过特殊地标导航自动将物品运输至指定地点,因此要实现自主移动,导航系统是 AGV 机器人的关键,常见的引导方式为磁条引导,激光引导,磁钉导航、惯性导 航等。
AGV 机器人的应用可以实现高柔性和可拓展性的自动化物流,从而达到降低 成本、提高效率、缩短产品生产周期的效果。AGV 机器人无需人的参与,就可以 实现 24 小时连续运转,大大提高产品物料等的搬运效率,并且 AGV 系统可与工 厂内部现有 MES、ERP 等系统对接,实现全数字化管理,有效规避人为因素,提 高生产质量水平。
随着工厂自动化、计算机集成制造系统技术逐步发展、以及柔性制造系统、 自动化立体仓库的广泛应用,AGV 作为联系和调节离散型物流管理系统使其作业 连续化的必要自动化搬运装卸手段,其应用范围和技术水平得到了迅猛的发展。
从下游行业应用分布来看,随着近年来智能仓储物流的兴起,京东、亚马逊、 阿里巴巴、申通、顺丰等电商巨头和快递业龙头对分拣机器人、AGV、无人仓等 大幅度加码,智慧物流已成为物流行业的大势所趋。电商快递是 AGV 机器人的第 一大应用行业,占比 34.5%,汽车、家电行业分列二、三名,占比分别为 21.2% 和 18.5%。
近年来,AGV 机器人正处于市场繁荣期,其行业的快速发展带来了与之相关 的整个产业链的竞相涌入,传统叉车厂商、物流系统集成商、其他类别的工业机 器人企业乃至应用企业都进入了 AGV 行业。
2019 年,国内 AGV 机器人市场集中度较低,北京极智嘉、上海快仓、华晓 精密、杭州海康、沈阳新松等出货量排在市场前列,并且由于 AGV 机器人核心技 术与传统工业机器人并不一样,技术门槛不高,国内外技术水品无明显差距,因 此国内 AGV 机器人市场大多都被国产品牌所占据。
从出货量上来看,近年来国内 AGV 机器人增长速度较快,15 年到 19 年的 4 年间的年均复合增速达 57.7%,即使是 19 年整个工业机器人行业遇冷 AGV 机器 人也保持了 16.7%的增速。在中国制造 2025、智慧物流等各项政策的保驾护航, 以及电商快递、新能源、医疗等新兴行业市场需求的持续释放下,未来两年我国 AGV 机器人销售量预计仍将维持接近 20%的增长速度。
3.3. 长尾市场将成为未来工业机器人的增长点
按应用行业分,汽车行业仍然是工业机器人下游应用占比最高的行业,约占 整个工业机器人市场出货量的 35%,其中在汽车零部件和汽车整车中的应用分别 占比 23%和 12%。3C 电子行业紧随其后,占比 23%,排在第二位。金属加工行 业排在第三位,占整个市场出货量的 12.2%。工业机器人在食品饮料行业、锂电 行业、家电行业、光伏行业等长尾市场的占比仍然较小,分别只有 5.9%、5.6%、 5%和 3.1%,但他们的增速远高于汽车、3C 电子这些较为成熟的市场,随着下游 行业应用场景的进一步丰富,这些长尾市场未来将有更大的增长空间。
从行业占比变动来看,2019 年工业机器人在汽车行业的应用占比同比下滑 0.8%,这主要是因为汽车行业近年来市场需求逐渐触顶,造成行业固定资产投资 降低,从而影响了工业机器人在汽车行业的出货量,虽然汽车行业目前仍然是工 业机器人的第一大应用行业,但其已经趋于一个存量市场,不再会像过去十年一 样成为工业机器人行业的增长点。
2019 年工业机器人在 3C 电子行业的应用占比同比略微上升约 0.4%,与汽 车行业相似,3C 电子行业的下游需求也出现了饱和的趋势。以行业内最主要的产 品智能手机为例,跟随着移动互联浪潮不断普及,智能手机高速增长的阶段已经 过去,近年来国内市场智能手机的出货量也呈现出下滑的趋势,工业机器人在 3C 行业中的应用增速也逐渐放缓。
2019 年我国工业机器人下游行业应用中占比增长较快的行业分别是食品饮 料、光伏和锂电,同比增速分别为 127%、55%和 24%。对食品饮料行业来说, 随着近年来图像识别和抓取等技术有了进一步的发展,使得机器人逐渐具备了处 理精致而多样化产品的能力,在食品行业中使用机器人进行挑拣、包装和检测越 来越常见。此外,随着食品安全的要求越来越严格,使用机器人替代人工,降低生 产过程中的人为干扰也可以降低污染的风险。
随着近年来国家新能源战略的逐步推进,光伏和锂电行业逐渐受益,预计十 四五期间我国将以更大的决心、力度和举措推进能源革命,加快构建清洁低碳、 安全高效的能源体系。2020 年中国光伏发电累计装机预计将达 2.4 亿千瓦,保守 估计未来五年年均光伏新增装机规模也将在 0.7 亿千瓦左右。2020 年前 11 个月, 我国新能源汽车产量仅占汽车总产量的 5.1%,而根据规划,到 2025 年新能源汽 车新车销售量将达到汽车新车销售总量的 20%。光伏和锂电行业的持续景气将释 放更多的自动化需求,带动未来工业机器人的进一步增长。
3.4. 人机协作与小型化是未来工业机器人的发展趋势
当前,工业机器人的应用场景愈加广泛,苛刻的生产环境对机器人的体积、 重量、灵活度等提出了更高的要求,工业机器人正向着小型化、轻型化、柔性化的 方向发展,类人精细化操作能力不断增强。此外,随着机器人易用性、稳定性以及 智能水平的不断提升,机器人的应用领域逐渐由搬运、焊接、装配等操作型任务 向加工型任务拓展,人机协作也成为工业机器人研发的重要方向。
传统的工业机器人必须远离人类,一般在保护围栏或者其他屏障之后安装部 署,以避免人类受到伤害,这极大的限制了工业机器人的应用效果,在很多需要 人类介入的工作中就无法采用机器人来实现较高程度的自动化。人机协作将人的 认知能力与机器人的效率结合在一起,从而使人可以安全、简便的与工业机器人 进行配合,达到 1+1>2 的效果。
协作机器人是近年来兴起的一种新型工业机器人,从多关节机器人的基础上 发展而来,最早的协作机器人仅仅是在传统多关节机器人外部包裹一圈柔软材料, 以减小对人体的伤害。随着技术的发展和相关规范的完善,协作机器人慢慢转向 了区别于传统机器人的外形设计,并且借助表面力感知器、关节力矩传感器、电 流估算力反馈模型等方式搭配特殊的安全算法,协作机器人可以在碰到人体后自 动停止,大幅增强了工业机器人的安全性,使人机协作变为可能。
从市场结构来看,2019 年国内协作机器人市场主要由优傲(Universal Robots) 和傲博占据,市占率分别为 32%和 23%,合计占比超过 50%。其中 Universal Robots 是全球范围内的协作机器人霸主,08 年推出全球首款协作型机器人,全球 累计销售达 5 万台,傲博作为国产厂商,是中国首家实现全国产化的协作机器人 研发企业,是国产协作机器人龙头。
从出货量上来看,近年来国内协作机器人实现了爆发性的增长,16 年到 18 年的两年间年均复合增速高达 93%。不同于其他工业机器人的是,协作机器人因 为要与人进行配合,2020 年受疫情影响较其他工业机器人更为严重,出现了较大 的负增长,但随着全球疫情逐渐受到控制,生产逐渐恢复,协作机器人仍然有望 凭借人机协作的进一步加深实现快速增长。
当前,工业机器人的应用场景愈加广泛,苛刻的生产环境对机器人的体积、 重量、灵活度等提出了更高的要求。除了人机协作以外,工业机器人正朝着更小、 更轻、更灵活的方向发展。
以六轴机器人为例,六轴机器人最开始是大规模应用在汽车行业,多以负载 大于 20kg 的重负载型号为主,而随着近年来六轴机器人逐渐向 3C 电子、金属加 工、食品饮料、新能源等行业扩展,负载小于 20kg 的小六轴越来越受到市场的偏 爱。
2016 年至今,小六轴机器人的增速一直高于大六轴机器人,尤其是近两年在 大六轴机器人负增长的情况下,这种差距还有进一步扩大的趋势。可以看到,小 六轴在六轴机器人中的占比一路上升,预计 2020 年小六轴机器人出货量的占比 将接近 60%,而小六轴机器人技术门槛低于大六轴机器人,这也将利好国产机器 人厂商,削弱外资工业机器人厂商的优势。
4. 风险提示
4.1. 下游行业景气度下降风险
工业机器人所处行业与制造业的发展和国家宏观经济运行趋势的关联较为紧密,因此,工业机器人行业景气度将受到宏观经济波动以及下游行业周期性变化 的影响。2017 年至 2019 年,我国国内生产总值(GDP)增长率分别为 6.9%、 6.6%及 6.1%,宏观经济增速有所放缓,制造业的固定资产投资受到一定影响。如 果未来汽车、3C 电子等行业景气度下降,将会对工业机器人行业造成较大影响。
4.2. 行业竞争加剧风险
随着整个工业机器人产业链的国产化进程推进,国内外工业机器人核心零部 件差距逐渐缩小,技术门槛进一步降低,越来越多的国产工业机器人厂商加入到 市场竞争中来,我国工业机器人市场集中度或将更加分散,无序竞争现象可能会 更加明显,行业整体面临竞争加剧的风险,价格战等因素或将对整个工业机器人 行业的利润造成一定的负面影响。
4.3. 疫情控制不及预期的风险
从去年年初开始的新冠疫情在全球范围内仍在持续,将会对全球经济带来怎 样的连锁反应仍然难以预计,如果未来全球疫情控制仍然得不到控制、国内外宏 观经济出现较大的波动或下游行业的复苏不及预期,将会对工业机器人市场需求 造成一定的影响,导致工业机器人行业景气度出现下滑的风险。
编辑:hfy
-
工业机器人
+关注
关注
91文章
3367浏览量
92694 -
协作机器人
+关注
关注
2文章
492浏览量
30155 -
智能制造
+关注
关注
48文章
5570浏览量
76372 -
工业 4.0
+关注
关注
0文章
34浏览量
4314
发布评论请先 登录
相关推荐
宜科荣登工信部工业机器人行业规范企业榜单
高工年会 守正创新开新局 助力国产机器人竞争力
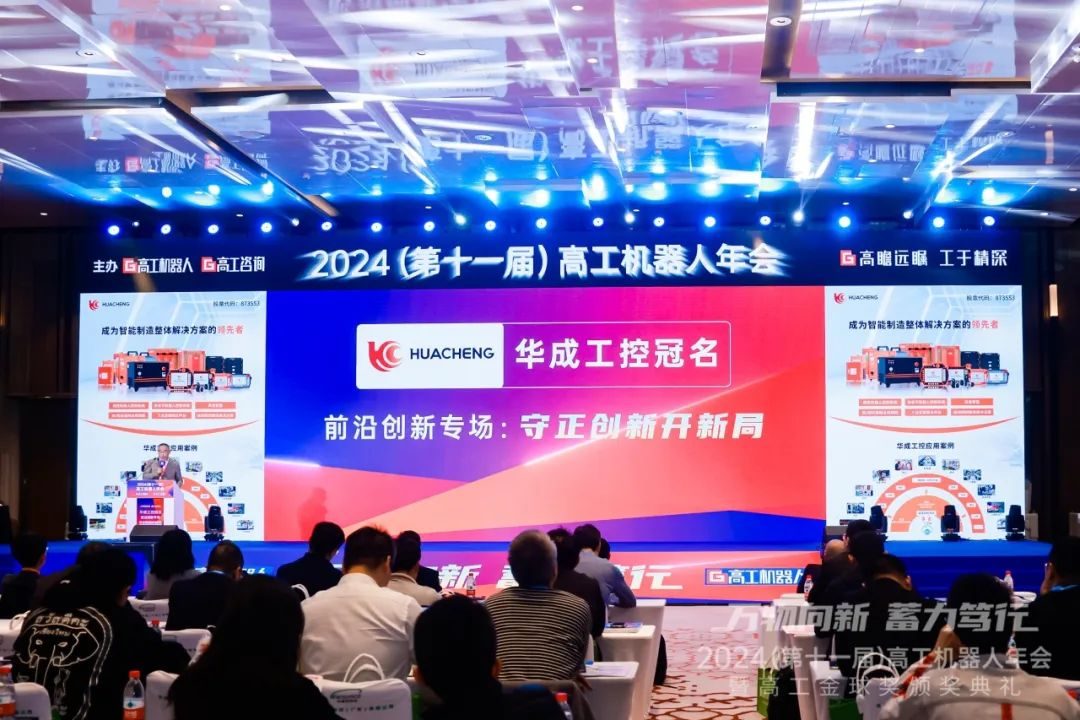
华数机器人再次入选工信部《工业机器人行业规范条件》企业名单
江智公司持续沉淀增强机器人产业关键技术核心竞争力
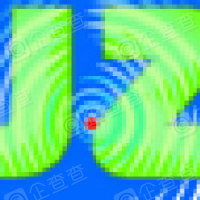
鲸启智能机器人入选多项金融银行机器人行业报告
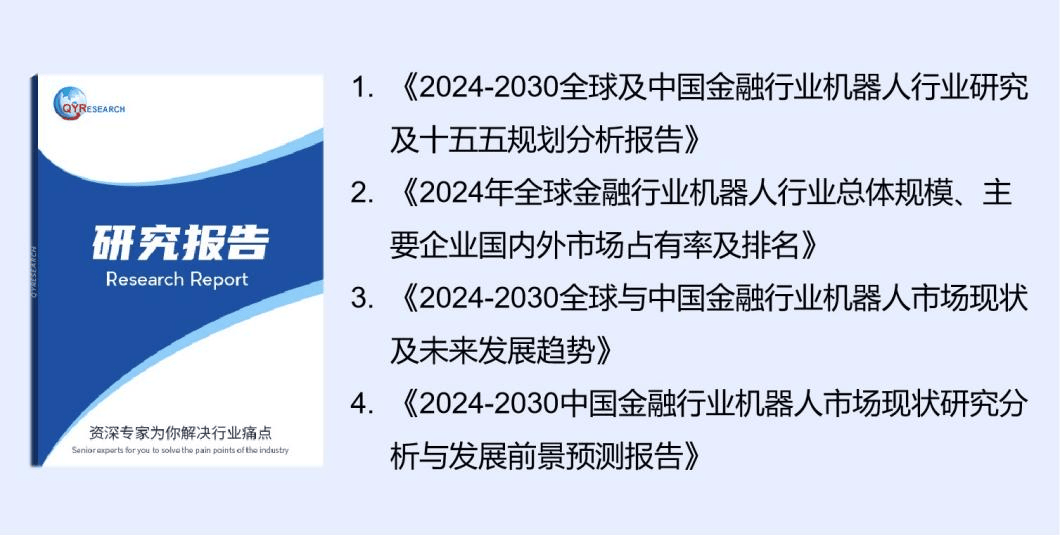
工业机器人常用的编程方式
abb工业机器人的编程语言是什么
基于飞凌嵌入式RK3568J核心板的工业机器人控制器应用方案
其利天下技术·搭载无刷电机的扫地机器人的前景如何?
工业4.0中的机器人向协作机器人演进
工业智能机器人以其卓越的技术和创新能力,正引领着行业的升级与变革
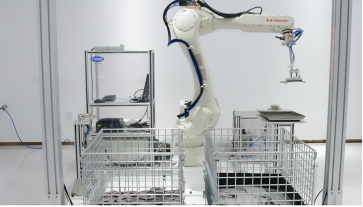
评论