北达科他大学(UND)的研究人员获得了美国航天局75万美元的赠款,用于开发一种3D打印航天服。
与来自马歇尔、约翰逊和肯尼迪航天中心的工作人员一起工作,北达科他大学空间研究系教授兼主任Pablo de León将对这一概念的可行性进行为期三年的研发项目。这款增材服装将被设定为‘NDX-3’的带好,将使用柔性聚合物的组合进行制造,并最终通过动作捕捉测试与传统航天服进行对比。
“到目前为止,所有的抗压力和太空服都是使用传统的缝纫技术制造的,”León解释说。“它们需要非常熟练的缝纫工匠的数千小时来建造一件太空服,而且它们也非常脆弱。重新思考宇航服的制作方式是很重要的,我们已经潜在地发现3D打印可以帮助解决这个问题。”
“在我们进入低地轨道时,宇航员将需要一种可靠的方法来修理和调整他们的装备。”
从缝纫向制造转型
在过去的七十年里,宇航服基本上都是以同样的方式建造的,利用传统的缝纫技术将一块块聚氨酯尼龙、各种金属和可穿戴聚合物缝合在一起。这个过程需要熟练的缝纫工匠花费数千小时才能完成,与现代航天标准相比,即使是成品服装也是古老的技术。
更重要的是,这种太空服的性价比并不高,每件的制作成本在200万美元左右,而且由于是为每个宇航员量身定做,通常也不能重复使用。几年前,UND开始与NASA合作,改变宇航服的制作方式,目的是设计一种增强型的、更具成本效益的替代设计。
虽然德莱昂教授和他的教师们已经在这个项目上工作了一段时间,但他们最近选择将3D打印融入加压服的设计中。当团队考虑到深空探索的前景时,他们才改用快速成型制造,并因此获得了NASA的合同。
“在火星上和更远的地方,宇航员不会奢望在他们的行星栖息地有一支裁缝师或缝合师的军队来照顾他们的宇航服,向任务控制中心索取零件需要一年以上的时间。”德莱昂教授解释说。
“所以,我们将尝试做的,是主要使用3D打印来制造可加压的太空服,”他补充道。“美国宇航局已经决定资助我们的实验室,因为有可能这可以改变未来制造太空服的方式,并帮助减少 ”对地球的依赖“,这是航天局的目标之一。”
UND雄心勃勃的新型3D打印航天服
在为期三年的美国宇航局合同中,UND团队将通过开发和3D打印一件完整的服装,评估快速制造技术在太空服设计中的潜力。虽然研究人员仍处于设计过程的早期阶段,但他们已经对其理想的外观进行了建模,并进行了大量的材料评估。
起初,该团队的设计因 “过于绿色 ”而被拒绝,但他们改进了技术,使用一系列不同的柔性长丝打印和压力测试部件,现在NASA已经要求提供完整的原型。随着项目的进展,UND的空间部门将与NASA更紧密地合作,以汇集专业知识,并利用该机构的先进3D打印技术。
“过去,我们与NASA的中心关系非常密切,对于这个特殊的项目,我们将需要他们的专业知识、投入和专业设备,”León说。“几十年来,NASA一直是3D打印领域的先驱。它拥有一些最先进的设备和最好的专家,帮助我们解决这个项目中会发现的一些问题。”
“我们将与MARSHALL、JOHNSON和KENNEDY航天中心合作,因为他们在我们将用于开发原型,以及打印原型的设备等多个领域都有专长。”
一旦团队创建了他们的增材原型,他们将对其进行一系列的动作捕捉测试,以比较其与传统飞行服的性能。鉴于该服装是为了在火星上使用而设计的,运动捕捉测试将模拟外太空的条件,使研究人员能够准确测量其可靠性。
诸如宇航服的灵活性、机动性和行走运动学等因素都将在期间被密切监测,以确保宇航服尽可能地易于移动。在项目后期,将利用身体扫描技术制作定制化的原型,设计出 “完全适合 ”未来宇航员的太空服。
“我们觉得,对于长时间的太空飞行来说,拥有一套完全适合你的、为你量身定做的太空服,比采取‘一刀切’的方式更好。”德莱昂教授总结道。“如果采用传统技术,成本会很高,而且非常困难,但使用增材制造技术,你就可以做到这一点。”
NASA的3D打印前辈们
多年来,NASA委托了一些研究项目,研究3D打印在制造宇航服方面的潜力,并一路开发出各种原型。
早在2015年,NASA就宣布其Z-2原型宇航服将采用3D扫描和快速成型技术生产。该太空服本身的设计是由高耐久性复合材料制成,以实现更大的机动性,并保护穿着者免受太空恶劣环境的影响。
最近在2018年1月,奥地利空间论坛(OeWF),对宇航服进行了测试,作为为期一个月的模拟火星实地任务的一部分。作为评估的一部分,来自全球25个国家的科学家前往阿曼的一个贫瘠地区,模拟红色星球的条件。
在其他地方,美国宇航局喷气推进实验室的系统工程师劳尔-波利特-卡西利亚斯(Raul Polit-Casillas)概述了类似链式3D打印材料的潜在航空航天应用。根据这位技术人员的说法,添加剂织物既可以作为航天器的屏蔽装置加以利用,也可以缩小规模,以宇航服的形式为宇航员提供保护。
-
NASA
+关注
关注
0文章
427浏览量
30972 -
3D打印
+关注
关注
26文章
3551浏览量
109178
发布评论请先 登录
相关推荐
有源晶振在3D打印机应用方案
3D打印汽车零部件模型定制服务,多种材料、快速打印-CASAIM

3D打印技术应用的未来
物联网行业中的模具定制方案_3D打印技术分享
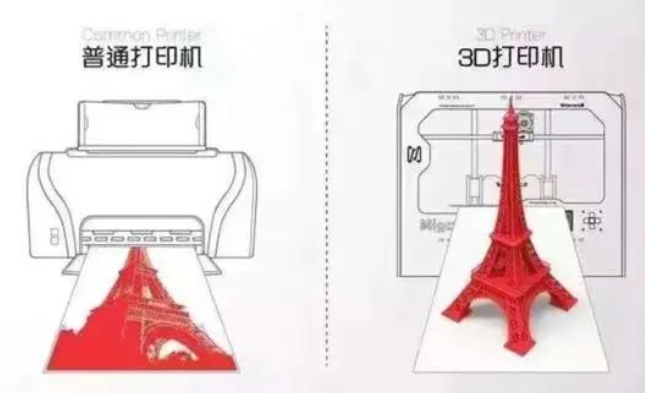
透明树脂材料3D打印服务全透应用案例
3D打印汽车零部件建模设计3D打印服务
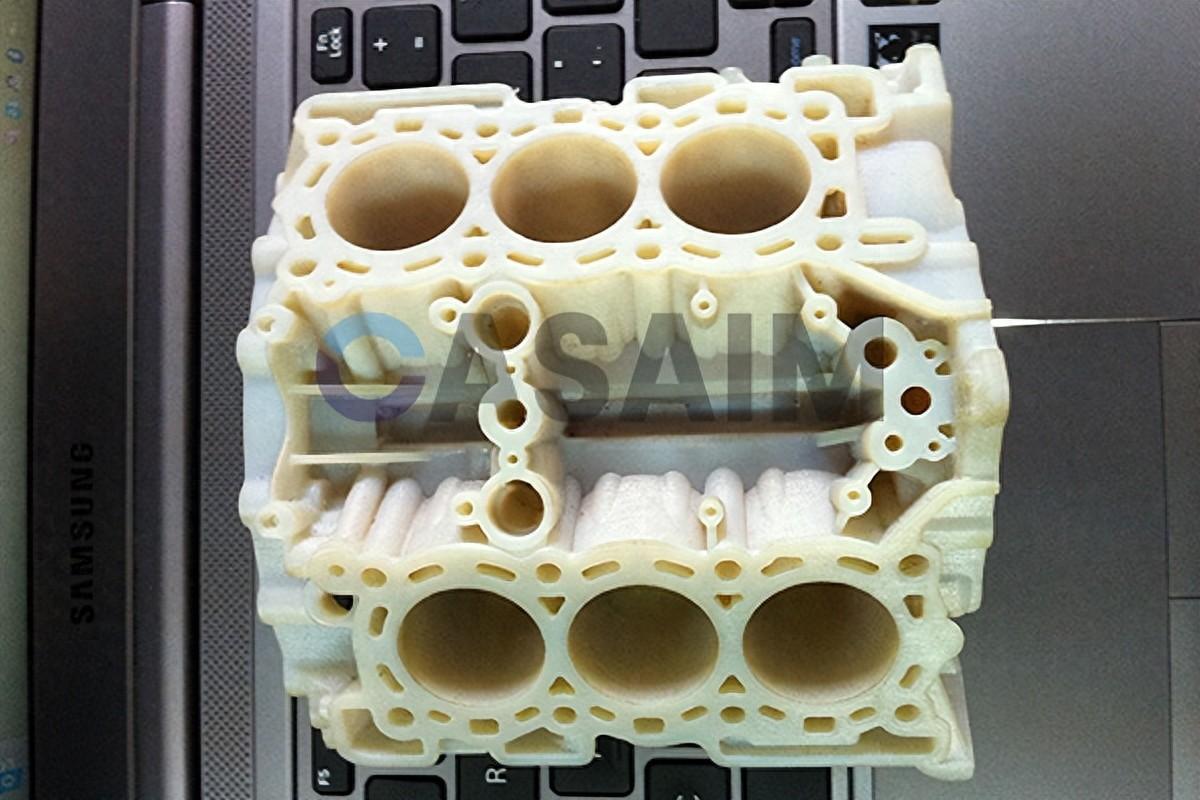
评论