1、NVH 性能开发的挑战
NVH 性能开发面临的挑战众多,其中最为重要的就是成本和开发周期的挑战。
在节省成本方面,近年来汽车行业整体下行,竞争日益激烈,对整车开发成本的控制也日益严格;随着每个零部件成本目标的严格控制,NVH 设计方案要求越来越精准。消除 NVH 后期整改造成的模具重新开发、工艺装备重新排布等浪费问题对节省 NVH 开发成本具有重要的意义。
NVH 性能开发过程也面临着周期性的挑战:整车开发周期不断缩短,从 36 个月缩减至 24 个月;详细设计阶段仿真分析和优化的周期压缩;ET 至 SOP 实车阶段 NVH 问题排查和整改的时间大大减少。
为应对更短周期、更低成本的整车开发,需要将 NVH 开发工作的重心再往前移,前移到概念策划阶段,减少设计和实车阶段的返工;提升 NVH 分析和设计方案的精准度,实现 NVH 的精细化开发;建立和完善整车级仿真分析能力,在早期对目标进行准确预测。
2、NVH 开发前置的具体策略与方法
NVH 业务前置的具体举措
设计提案:在产品设计之前,考虑对 NVH 性能的影响,对产品结构的选型、布置、尺寸空间等向产品部门提出设计建议,作为设计的参考;
应用阶段:方案预研
设计提案:选型类提案 - 轮胎型号参数选取
(1)不同扁平率的轮胎选择
(2)不同扁平率对轮胎振动特性影响;
设计提案:选型类提案 - 副车架选型
换代车型前后副车架与车身连接形式,刚性连接、柔性连接;
前后副车架连接形式对整车 NVH 性能的影响识别;仿真 or 试验
前后副车架柔性、刚性方案适用性分析。
柔性连接方案 | 刚性连接方案 | |
前副车架 | 对 150Hz 左右 路噪影响较大, 其它频段基本 没有影响; | 更利于操稳与加 速性能; |
后副车架 | 对路噪多个频 段影响大,有 效降低路噪水 平; | 利于操稳; |
选型方案 | 结合仿真验证,确认:前副车架采用刚性连接方案;后副车架采用柔性连接方案; |
设计提案:后悬架拉杆布置
拉杆结构形式 | 拉杆长 (mm) | 拉杆模态(Hz) | 拉杆模态(Hz) |
车型 1(横置) | 220 | 7.3 | 110 |
车型 2(横置) | 187 | 11.6 | 148 |
车型 3(竖置) | 75 | 77.4 | 230 |
设计车(竖置) | 110 | 34.1 | 201 |
设计车(竖置) | 120 | 28.5 | 195 |
表:不同方案对指标的影响
方案 1 | 方案 2 | |
优点 | Z 向隔振好 | 拉杆模态高 |
缺点 | 拉杆模态低 | Z 向隔振差 |
适用于 | 利于怠速振动 | 利于加速轰鸣 |
表:不同方案对 NVH 性能的影响
设计提案:布置类提案 - 转向系统布置
拉杆结构形式 | 原状态 | 悬距缩短 30mm | 模态变化 |
车型 1 | 36.8HZ | 39.6Hz | 2.8Hz |
车型 2 | 36.9Hz | 40.2Hz | 3.3Hz |
表:仿真验证分析
设计提案:布置类提案 - 驱动轴角度布置
普通节型驱动轴,夹角在大于 X 度时滑移力开始突变。因此驱动轴夹角需控制在 X 度内,或采用高成本的节型, 如 AAR 节型。
测量值 | 测量空载 | 测量半载 | 测量满载 | 节型 |
车型 1 | 6.8° | 5.5° | 4.8 | GI |
设计车 | 设计空载 | 设计半载 | 设计满载 | 节型 |
车型 1 | 4.97° | 设计半载 | 2.51° | GI |
图:不同方案对指标的影响
设计提案:布置类提案 - 进气系统布置
概念仿真:基于基础车,根据初版收集构想,完成设计方案的概念模型及性能仿真验证;
应用阶段:设计构想
图:怠速振动概念仿真:利用基础车车身振动作为边界, 仿真方向盘振动,并识别问题区域。
图:鼓噪路噪概念仿真:利用基础车的变形车身 配合底盘预研方案,识别路噪问题,并验证初版衬套效果。
图:中高频结构辐射噪声概念仿真:电机及减速器台架振动为边界,利用底盘感念方案配合基础车车身传函测试数据,对电机 / 减速器低阶结构辐射噪声进行仿真,评估方案可行性及问题点。
图:声学包概念仿真:利用基础车或标杆的声源为边界,将整车声学 包目标分解到各系统,并验证不同声学包方案对系 统性能的影响,确定最终设计方案。
方案点检:对一些固化的、要件式的设计要求及方案进行点检确认;
应用阶段:设计构想、详细设计
SE :Simultaneous Engineering 同步过程;
应用阶段(设计研讨):设计构想、详细设计
所谓 SE 研发?从研发的初期阶段开始,全体相关部门参加,同时实施研讨,将各部门的所有要件都落实到计划中, 不发生返工, 制作完成度高的图纸 。
同时进行 Simultaneous 进行
台架测试:通过分析总结基础车电机、电机减速器总成、空压机、水泵等电器件台架及整车测试数 据,建立台架与整车性能的相关性,以此制定设计车的台架 NVH 目标,将 NVH 问题控制在台架阶段;
应用阶段:设计构想、详细设计。
系统优化:结合激励源和响应目标要求,通过仿真分析实现系统或部件设计参数的最优设计,不同于传统的系统、零部件 NVH 指标的仿真分析;
应用阶段:设计构想、详细设计
悬置支架仿真优化:
整车响应仿真:搭建整车仿真分析模型,输入路面、动力总成、外部流场等激励,分析车内路噪、动力总成噪声、风噪等响应,对 NVH 一级目标进行分析预测,并对设计参数进行优化。
3、小结
为了提高 NVH 开发质量,满足成本递减、周期缩短的整车开发需要,NVH 开发重心不断前移是今后 NVH 工作重要方向。
建立前期 SE 的组织和流程,将 NVH 的设计要求在概念方案阶段输入给产品设计部门,作为零部件详细设计的参考。需要建立 NVH 精准化分析和精细化方案设计的能力,建立和完善整车级仿真分析能力,在开发前期对 NVH 目标的达成进行准确预测。由此才能提高 NVH 开发质量,做到成本降低,周期缩短。
编辑:hfy
-
减速器
+关注
关注
7文章
399浏览量
23496 -
NVH
+关注
关注
2文章
71浏览量
10179
发布评论请先 登录
相关推荐
适用于 Microsemi® RTG4™ FPGA 的 TI 航天级电源解决方案应用手册
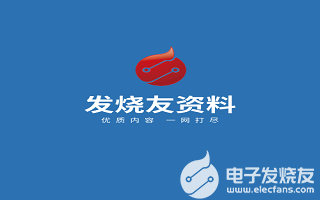
适用于TI超声AFE的模拟时间增益控制(ATGC)解决方案
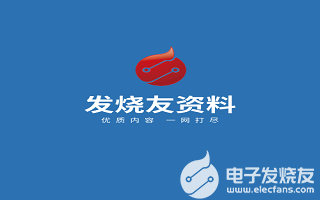
适用于模拟输出模块的双极Fly-Buck-Boost解决方案
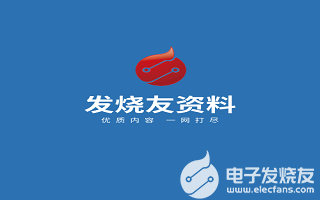
PMP21611.1-适用于仪表组应用的汽车前端电源 PCB layout 设计
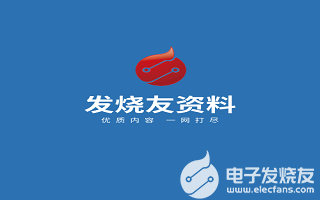
TIDA-020012-适用于车内照明的汽车像素化顶灯 PCB layout 设计
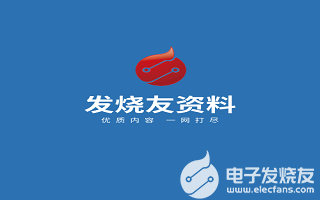
评论