电子组件向无铅焊料的转变促使制造商在电子元器件或电路基板上使用纯锡或软金等材料来替代锡-铅可焊端接精饰。金有焊点脆裂风险,这就可能会降低焊点的机械寿命。对于脆裂材料及其机理,我们采用了特写和横截面图片,并显示其在SEM/EDS组成成分信息。文中还给出了金的重量百分比为3.0%和4.0%的焊料量和金的量的表,并探讨了脆裂问题的成因及确保可靠性的解决方案。这些数据对改进镀金工艺、避免焊点脆裂具有启发意义。
1 引言
可靠的雷达电子硬件的制造有赖于在电子元器件和互连基板上生成高质量的表面镀层。可焊性和引线锚固强度是生产中评判表面金属镀层质量高低的两项参数。为了增强可焊性和引线的锚固强度,金和钯广泛地应用于表面镀层的设计中。增强引线的锚固强度可以采用厚的纯金镀层。不过,可充分满足引线锚固强度要求的金镀层厚度对于可焊性而言又可能显得太厚,导致焊点脆裂。此外,表面的金属镀层可能会被用作元器件的插合表面或磨损表面,这会导致金镀层设计得过厚或杂质过多,难以达到理想的焊接效果。
在液相焊料合金转化形成焊点的过程中,如果过多的金或钯溶入焊点,那么,所形成焊点的元素组成和机械性能与原来的焊料合金相比就会大不相同。通常需要依照电子组件的设计,用特定焊料合金将它们焊接起来才能使它们正常地工作。因此,焊点元素组成的变化会影响其机械性能,并将导致其耐用性下降或发生未知的变化。
无论是按照完工状态原样保存还是让其受到环境应力的作用,焊接好的电子产品都有可能产生逐渐劣化的现象。如果金或钯金属在焊接过程中的溶解并不完全,那么在所残留的金镀层或镀钯层和焊点之间就会发生固态扩散,在硬件的使用寿命中产生冶金学范畴的变化,并带来可靠性方面的隐患。
在理解了上述内容的基础上,焊点脆裂现象就可以定义为焊点耐用性因为表面镀层(金或钯等)溶解和/或与焊点组分产生反应而产生的变化。在使用锡基焊料进行焊接过程中,金或钯镀层上会相应出现AuSn4或PdSn4的金属间化合物。这种化合物可能会大量出现在焊点或在表面镀层的界面上,或两者兼有。与软焊料合金相比,这些金属间化合物更脆,故在承受机械应变时,焊点的牢固度就会下降。在焊点成型过程中,随着焊点中金属间化合物成分的增加,诸如冲击强度和应变率敏感度等焊点的基本机械性能也会相应发生变化。
如果在富含金属锡的焊点中所产生的金属间化合物并不是上述含锡最多的Sn4型的金锡化合物或钯锡化合物,那么,这表明焊点在其成型的过程中尚未到达平衡的状态。因此,该焊点在冶金学范畴上的可靠性仍然存疑。焊接点性能会随着其在电子硬件使用寿命中逐渐趋向平衡状态而发生改变。
2 问题的描述与方法
由于人们担忧锡铅表面镀层中的铅(Pb)会从废弃的电子产品渗入到供水系统中,因此禁止在诸如电话和照相机等关键性较低的应用中使用这种表面镀层。
这种禁令促使人们更多地使用金和纯锡作为表面镀层。但是,缺少了阻止晶须生长的铅元素,纯锡的表面镀层会生长出晶须状的细丝,并因此导致短路或熔断。
而使用金、钯和金属铜的挑战则是这些元素会导致软焊点发生脆裂。因此,为了避免过多产生这样的脆裂,我们需要知道表面金镀层的最大厚度。同样,我们还需要确定金镀层的最小厚度,以免产生过多的孔隙,影响焊接质量。图1显示热氰化镀金工艺中孔隙率和金镀层厚度的关系。
图1 孔隙率与金镀层厚度(11.4~80微英寸)关系图
在通常情况下,金镀层被视作高度可焊的表面镀层。接下来本文给出了焊点脆裂的多种主要原理,并对各项原理的焊点脆裂提出了基于已有的行业标准和其他有报道的研究工作的、制造或设计层面的解决方案。
我们将常见的镀金、镀钯和焊料的量输入重量百分比计算公式中得到相应的结果,并对重量百分比计算公式进行了回顾和总结,然后提出了一些对标准的改进建议。
本文旨在避免焊点脆裂,并使表面金镀层和表面镀钯层在焊接和导线键合过程中的使用变得简单方便起来。
3 案例研究1-金锡化合物在界面上析出
3.1 案例研究1-数据
这里使用到的连接器插针的表面镀层设计是先镀镍然后再镀金,镀后再将这样的连接器插针蘸上熔融状态下的Sn63Pb37焊料合金。根据相关文献,金镀层很快就在熔融的锡铅焊料中溶解了。
将插针以侧面焊接至电路板上的、同样是先镀镍再镀金镀层设计的焊盘上。由于焊盘的金镀层很薄,完全可以避免在焊点中产生过多的脆裂,因此焊盘没有蘸上热熔的焊料。接点在焊接后在插针处开裂的情况如图2所示,对该焊点进行失效分析,其横截面如图3所示。
图2 从针到表贴电路板焊盘的焊点显露出一条裂缝
图3 金从电路板基底的焊盘上溶解,并且在接点(请参见椭圆部分)和插针(顶部黑色层)上可见
对电路板焊盘进行检查,发现存在如图4所示的、缺少镀镍扩散边界层的周缘部分。需要说明的是,按照对镀层的设计,镀镍层是用来完全覆盖住一层较厚金镀层的,在这样的镀镍层上还涂覆一层较薄的可焊金镀层。
图4 电路板焊盘俯视显示镍镀层并未覆盖住厚金层周边
3.2 案例研究1-结果
基底焊盘的表面镀层设计是外表面的金镀层覆盖住下面的镀镍层,但是镀镍的区域并未完全盖住镀镍层下的、较厚的金镀层。厚金层的边缘与焊点发生了接触。
在焊接过程中,边缘区域的金大量溶解到熔融焊料中并形成金锡化合物。当焊料固化时,大量金锡化合物在焊点靠插针的那一面析出。随着焊点开始冷却和凝固,AuSn4(凝固点为217℃)首先在插针上和焊点中析出,然后锡铅焊料(凝固点为183℃)在AuSn4上析出,并在插针上形成强度较低的界面。
在插针上析出的金锡化合物使焊点的强度较低,并在插针处开裂。图5显示我们在理解了上述原理后对总结出来的经验的应用。我们用镀镍层完全覆盖住焊盘上的厚金层。结果,焊点强度很高,并且没有发生脆裂现象。
图5 左边是改进后焊盘电镀设计的横截面,右边是特写图
如图5右边的箭头符号所示,当厚金层的边缘被图中暗灰色的镍薄镀层完全遮盖时,在焊点中就看不到金锡金属间化合物的出现;而根据Bester的观测结果,在Sn63Pb37焊料合金中至少要有重量百分比为1%~2%的金元素,才会看得到针尖状或薄片状的金锡化合物。
我们通过改进焊盘的设计解决了焊接界面在插针处发生分离的问题。采用新的设计后,焊盘处不再形成大量的AuSn4,在插针上或焊点中也检测不到AuSn4的存在。最重要的是,插针处不存在强度较低的界面。
4 案例研究2 - 软焊接接头中金过多
4.2 案例研究2-数据
焊接上的表面贴装连接器并不是总能顺利插拔。图6所示的连接器在图7所示的情况下会遇到插针焊点失效的问题。
图6 表贴连接器中心插针有时无法插入插孔或从插孔中拔出
图7 失效插针焊点的横截面
图9是图8左边角焊缝的特写图片。图10显示类似的特写图片,并使用SEM/EDS测量该区域元素构成。这一批的检视包括了焊点区域的绝大部分,这其中含有重量百分比为10%的金元素;此过程所使用的焊料合金为SnAg3.7。对另一处焊点区域进行的类似测量显示其中含有重量百分比为11%的金元素。
图8 插针焊点横截面图片
图9 图8左侧角焊缝特写图
图10 与图9类似的角焊缝,显示金(Au)、锡(Sn)和银(Ag)的分布形态
依照不同的焊点预成型体的量、浸锡过程和三种焊接工艺温度因素,我们进行了32组试验。各组试验对插针焊点组件的制造过程所涉及的独特设备和工艺都有针对性。
4.2 案例研究2-结果
在各项因素最优化之后,插针拉拔强度显著提高,数据见图11,实际效果见图12~14所示。
图11 减少插针和电路板上的金,增加电路板上的焊料量,良好地相互作用以增加插针的拉拔强度(克)
图12 在插针拉拔试验中,插针到电路焊点的强度很高,使得电路焊盘和电路板材料也被扯出电路板
图13 从金含量的减少和气泡的减少来看,焊点质量的改善得到了验证
图14 图13中焊点的特写图片显示在采用试验性设计的最优化设置后,去除了焊盘和插针上残留的、未溶解的金镀层
按照一种预定的试验,我们通过一项试验性设计(包括预装配除金步骤)除去了软焊点中过量的金元素,并进行验证。
5 案例研究3 - 高温手工焊接
5.1 案例研究3-数据
对如图15所示的焊接安装的表面贴装连接器的一项失效分析显示焊点开裂与原本组成为Sn63Pb37的焊料合金中过多的金和镍元素有关。对图15前景中水平方向上的开裂的接点进行切横截面检查,结果如图16所示。此外,我们还用SEM/EDS对横截面某些微观结构金相进行了分析。
表1显示图16所示的焊点在总体上的元素组成。在进行测量时并没有将如图16位点Spectrum 1所示的界面区域包括在内,这是为了避免其附近的镍元素信号致使测量出现误差。我们对不同的横截面进行了4次测量,测量结果如表1所示。其中,金元素平均重量百分比为3.6%,镍元素平均重量百分比为1.3%。表2显示图16中标记为Spectrum 2的中灰色金相的组成成分。这样的金属间化合物金相按其原子百分比数据确定为(Au0.45Ni0.55)Sn4。图16中标记为Spectrum 3和Spectrum 4的位点分别确定为富锡金相和富铅金相。
此外,还获得了连接器的制成金镀层厚度。它的金镀层厚0.70微米(28微英寸)。电路板表面处理方式为化学镀镍浸金。
图15 焊接上的表贴连接器,其接点有裂痕。箭头指向横截面所在位置
图16 开裂接点横截面,焊料与电路板焊盘相接处特写图
表1 图16中整个焊点组成成分
表2 图16中标为“光谱2”的金相组成成分
5.2 案例研究3-结果
一个多功能小组按照如下所示的类目检查了可能的失效原因:
(1)材料;
(2)加工设备;
(3)工艺;
(4)环境;
(5)人员;
(6)方法。
在材料类目下有两项原因,在工艺和方法类目下各有一条原因。材料类目下的两项原因是金镀层厚度和所使用的助焊剂。金镀层过厚导致焊点中金元素的重量百分比达到了规范IPC-AJ-820A所规定的3%到4%的金元素重量百分比上限。在手工焊接过程中,助焊剂的使用会使产品在焊接高温下的持续时间更长。
工艺类目下的原因是比预期低的产出量,这就导致其返工量高于预期。方法类目下的原因是散热不足的焊接安排,这样的焊接安排导致手工焊接时的温度更高。手工焊接温度过高的结论是从已确定的含镍金相(Au0.45Ni0.55)Sn4推导出来的。与化合物AuSn4常见的针尖状或薄片状结构相比,图16中标记为Spectrum 2所示的(Au0.45Ni0.55)Sn4的形态就显得很不规则。
手工焊接温度过高问题可以通过四项改进措施来修正:
1)使SMT连接器的表面金镀层更薄;
2)使手工焊接用的助焊剂更适用于批量生产;
3)改进焊接工艺使加工零件一次性通过、产出量也更高;
4)改进返工流程、采用散热效果更好的焊接工艺。
目前,对手工焊接过程中焊接温度过高问题的分析显示,过高的焊接温度不仅使金镀层发生溶解,还让镀镍层的很大一部分也发生了溶解。现在,业界认可金锡化合物会导致焊点脆裂,并对金元素的重量百分比上限进行了规定,用以避免此类脆裂现象的发生;但对于金镍锡化合物而言,业界目前尚未有类似规定。
6 案例研究4-表面硬金镀层
6.1 案例研究4-数据
图17显示一枚表面镀镍后再镀硬金的插针用成分为Sn63Pb37的焊料合金焊接到电路板的电镀通孔中。图18显示在角焊缝处出现了一条裂纹。对焊点的横截面进行分析,发现在角焊缝区域中插针上的金镀层在焊接的过程中并未完全溶解。对一个类似的焊点进行更严格的检查,发现开裂处特定地出现在插针上所金镀层的残留物和AuSn2金属间化合物层之间,如图19所示。在AuSn2旁边是连续的AuSn4层。在整个角焊缝中都分布有典型的AuSn4化合物。
图17 插针在电镀通孔焊点中的横截面视图
图18 与针脚分离状况的角焊缝裂缝特写图
图19 裂缝的微观结构显示在角焊缝中有残存的金镀层、裂缝和AuSn2/AuSn4双组分化合物层
表3所示的焊料和化合物的熔点作为参考资料十分有用。在焊接的过程中不会达到AuSn2的熔点。有人提出,高熔点的AuSn2化合物是通过固态扩散形成的。与此相对,在焊料仍处于熔融状态时,金镀层溶解并与锡产生反应,形成AuSn4。在焊点凝固成型并冷却下来的过程中,在金镀层的残留物与AuSn4之间发生了快速扩散。这种扩散形成了与金镀层的残留物相邻的AuSn2层。注意:AuSn2只在金镀层的残留物和AuSn4之间产生,是AuSn2/AuSn4化合物界面层的一部分,并不散布在整个角焊缝中。
这样的扩散减弱了金到AuSn2界面的强度,而因此被集中起来的角焊缝的收缩产生了足以导致角焊缝裂开的剥离应力。鉴于镀层可能会包含高达20%的空缺,这样的固态扩散可能会使这样的空缺进一步加剧,并因此导致镀层强度下降或出现中空现象。此外,我们知道,固态扩散和反应速率取决于表面镀层在电镀过程中所形成的应力状态。
表3 焊料和化合物熔点(℃)
6.2 案例研究4-结果
分析确定AuSn4在焊接的过程中形成,并与金镀层的残留物相接触。在焊点固化后的冷却过程中,在AuSn4和金镀层的残留物之间的界面上形成了新的金属间化合物AuSn2,并因此导致开裂。形成AuSn2(及由此所致的开裂)的原因可能是硬金表面镀层;这不仅因为这是金镀层,同时还因为这样的硬金镀层含有镍或类似的硬化元素。如表4所示,硬金的杂质水平比软金要高出3到10倍。尽管硬金中的杂质也能以一定的速率在熔融的焊料中溶解,但其速度比金的溶解速度要慢得多。
如图20所示,在230℃、组分为Sn60Pb40熔融的焊料浴中,金属镍的溶解速率为0.05微英寸每秒,金的溶解速率则高达100微英寸每秒。金的硬化降低了金的溶解速率,并在焊点固化后致使更多的/残留的金镀层形成,固体扩散出更多的金元素,形成了更多的AuSn2,并由此导致开裂。
表4 金硬度和纯度的规范
图20 熔融Sn60Pb40合金中径向浸出率与金属引线温度关系
因此,针对硬金表面镀层的解决方案就应当是以一种受控方式来让插针蘸上热熔的焊料以达到完全溶解硬金表面镀层的目的。这样,插针就有了一层可焊且基本不含金的表面镀层,脆裂的问题也因此得到解决。在此项案例研究中所得到一个经验是,对焊点进行横切面检查以确认金镀层在焊点成型的过程中完全溶解的试验手段是很有帮助的。
特别是当金镀层的硬度和纯度均未知时,这样的横切面检查就显得更重要了,因为要确保避免焊点的脆裂问题,有必要先确定在焊点成型的过程中金镀层已完全溶解。
8 总结
J-STD-001F主张金镀层脆裂应当被视作焊接制成电气和电气组件的一种缺陷,凸显我们对以下内容有清晰理解的需要:
(1)焊点脆裂的机理;
(2)经过实践验证的解决方案;
(3)确立具体标准的可行性。
本论文阐述了针对焊点脆裂问题的四项案例研究;其中,三项使用了Sn63Pb37合金,一项使用了SnAg3.7合金。
本论文在每项案例研究中都给出了解决方案,并提出了这些解决方案对无铅合金和标准的适用性问题。
在第一项案例研究中,一种金锡化合物被现实析出在原本不含金的表面安装引线接头上。覆有厚金镀层的基底本应被镀镍层完整包被住,但厚金镀层的周边并未被包被住,导致金在焊接的过程中大量溶解。这一案例研究阐释了金溶解、接着形成AuSn4金属间化合物、并向界面和焊点块上析出的常见脆裂机理。简单地重新设计镀镍包被层就能解决这一问题。
在第二项案例研究中,焊接在一起的表面贴装连接器插针和基底焊盘都含有太多的金,焊料体积又太小,导致金的重量百分比过高。我们通过带能量分散光谱的扫描电子显微成像测量了焊点中的金含量,显示不必总是得依靠计算来获取这一数值。我们通过一项重复了32次的试验来为某特定制造设备优化除金过程工艺、焊料体积和三项温度设定。验证样品的横截面显示试验成功。
第一项和第二项案例研究显示通常所致的脆裂机理,第三项和第四项案例研究则提供了一些不同的信息。
在第三项案例研究中,对表面贴装连接器的焊接是手动进行的。在进行电气试验时,焊点有开裂现象。多功能小组进行了因果调查,发现了四项成因。微观结构分析显示手工焊接的温度过高。金和镍脆裂导致形成了与AuSn4形态不同的(Au0.45Ni0.55)Sn4金属间化合物。我们通过配备更好的散热结构降低了焊接温度。此外,我们还改进了熔剂,并使用了金镀层更薄一些的连接器。
在第四项案例研究中,插针上的硬镀金表面导致电镀通孔应用中的焊点发生开裂。横截面图像分析显示在角焊缝区域中,并不是所有的金都自插针上溶解掉。AuSn4开始时附着于金镀层的残留物上。AnSn2在扩散后形成,导致产生AuSn2/AuSn4双组分化合物层;该双组份化合物层从金镀层上脱落。与纯金相比,硬化后的金在焊料中的溶解速率十分缓慢。对金的硬化降低了金的溶解速率,导致了焊点硬化后金镀层的残留和AuSn2的形成,并因此成为开裂的一项成因。
【作者简介】
闻春国,译审,西南科技大学外国语学院特聘产业教授。
编辑:hfy
-
电子元器件
+关注
关注
133文章
3350浏览量
105769
发布评论请先 登录
相关推荐
SMT来料质检:确保电子生产质量的关键
电子产品结构与导热材料解决方案
解析PCBA加工中焊点拉尖的成因与解决方案
不得不知的pcba加工规则:确保元器件安全可靠
基于可靠性设计感知的EDA解决方案
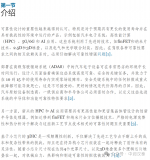
DCAC电源模块:效率与可靠性兼备的能源转换解决方案
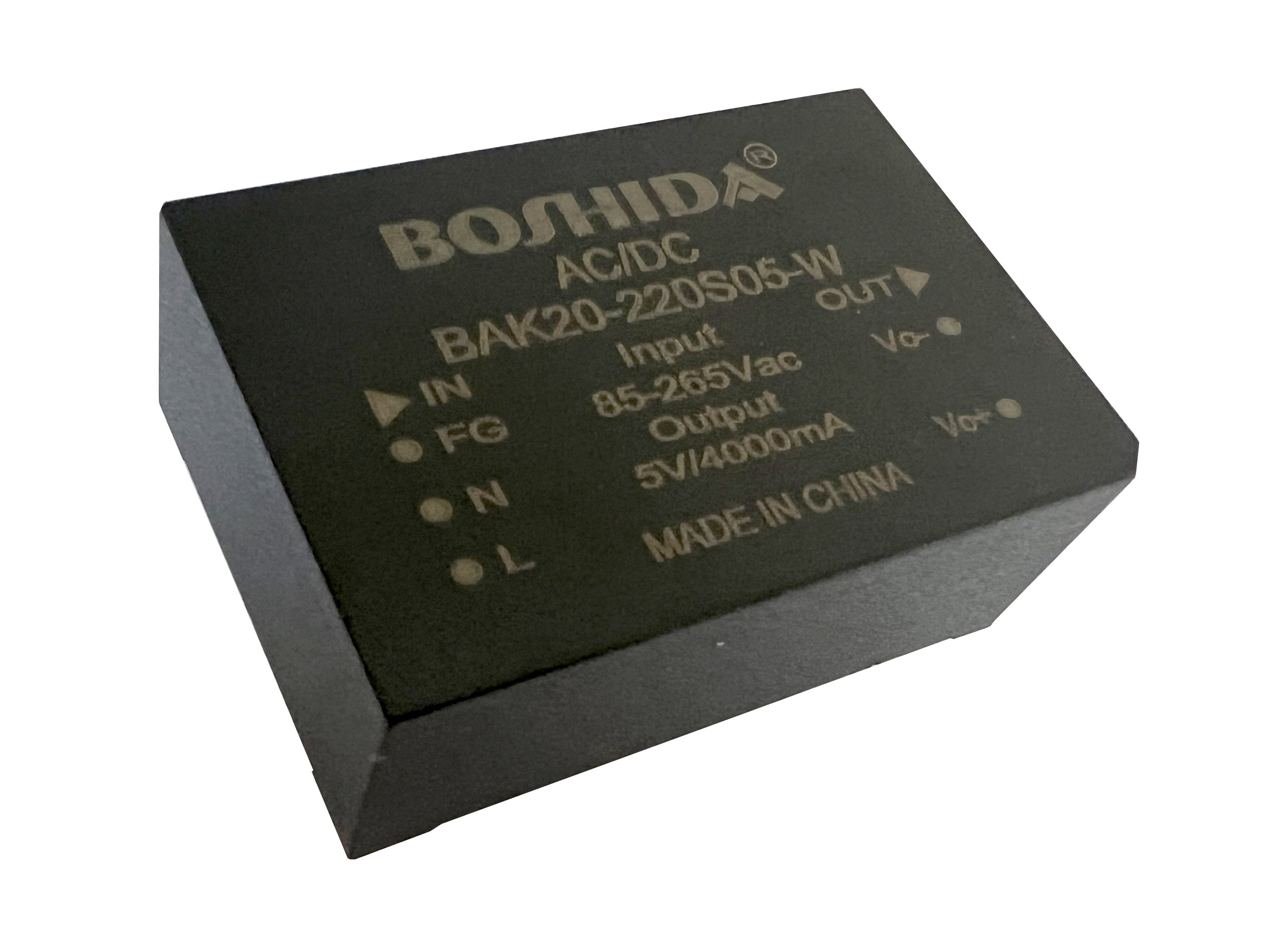
涨知识:元器件失效之推拉力测试,附推拉力测试机的应用!
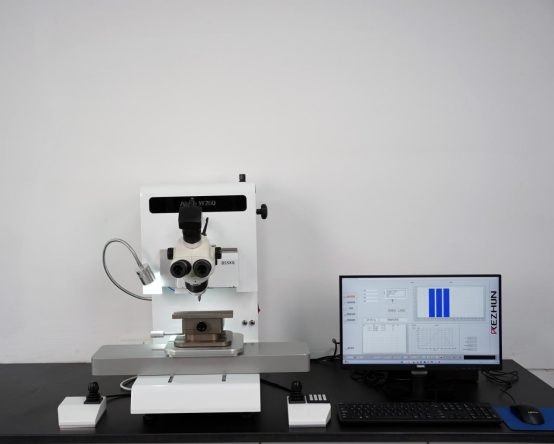
通过精心选择并使用无源器件来确保汽车系统的可靠性
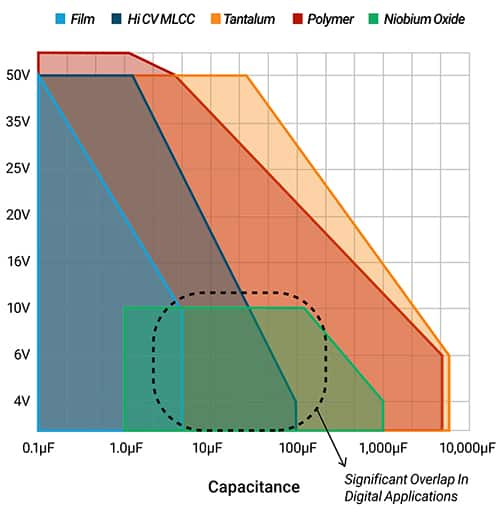
如何确保IGBT的产品可靠性
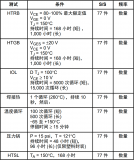
电子元器件的选用原则
IGBT的可靠性测试方案

评论