固态激光器、光纤激光器和超快激光器继续向微电子加工应用领域进军,特别是半导体工业中的硅晶圆切割应用,以及光伏产业中的各种基于激光的切割和光刻应用。
然而,大多数基于激光的切割方法都依赖于激光光束沿衬底的线性移动。美国镭富电子设备公司(Electro Scientific Industries,ESI)开发出了一种生产就绪(production-ready)系统,该系统将其新的基于激光的“零重叠”技术应用于超薄(厚度小于50μm)硅晶圆切割。通过保持较高的脉冲能量和高重复频率,该系统沿划片槽对脉冲进行空间分离。与基于激光的线性切割技术或传统的机械切割方法相比,ESI公司提供的整体加工系统可以提高切割产量和超薄晶圆的断裂强度,同时也能保证较高的投资效益。
图:基于激光的“零重叠”技术在空间上对高能激光脉冲进行分离,可以更有效地切除材料(a)。通过调整激光参数可以选择性地优化不同层的材料切除速率。激光加工后热影响区的少量残留材料可用干式刻蚀法去除(b)。
超薄晶圆的挑战
摩尔定律的不断向前发展,正在推动着半导体工业向三维(3D)集成的方向发展,同时也在推动着诸如堆栈存储与逻辑、以及硅穿孔(TSV)互连等先进封装架构技术的发展。随着晶圆变得越来越薄,机械晶圆切割技术由于会产生开裂、剥落以及其他产量和质量问题,已经不能满足晶圆切割的要求。ESI公司的ESI9900系统使得在一个集成系统中能够实现超薄晶圆的完全切割和划片逻辑或片上系统(SoC)的芯片贴装薄膜。由于这些晶圆的最上层往往有精细、脆弱、低k值的绝缘材料,因此切割这些材料时,不对晶圆造成损伤是至关重要的。
“零重叠”技术
ESI 9900系统的零重叠技术使用一种基于检流计的定位系统,可以迅速将商用355nm 紫外激光器(光斑尺寸大约为8μm)产生的热能,分配到晶圆上沿着所需的划片槽方向的空间分隔点上。激光重复频率大约为240kHz,激光能量通过多个空间上独立的脉冲传递,避免了残留物、热累积和基于激光的线性划片槽方法产生的羽流相互作用。空间分离允许利用更高的激光能量密度,以实现比利用激光束的线性移动所能达到的速度更快的晶圆切割速度(每秒数米)。此外,可对激光图案进行选择性优化,以控制不同半导体层的材料移除速率(见图)。
“ESI 9900系统可以对机器人夹持晶圆进行顶部器件层切割、硅晶圆层和随后的DAF层切割,干法刻蚀,以及清洗,所有步骤都是在一个完全自动化的过程中完成的。”ESI公司的产品市场经理Matthew Knowles介绍说。
尽管ESI公司已经展示了这种技术能够最大限度地减少被加工衬底的热影响区(HAZ),但是他们承认,任何基于激光的加工过程都是一个热过程,都会存在一些热影响区。为了最大限度地提高芯片强度,最小化割缝宽度,“零重叠”加工之后还要进行传统的干法刻蚀。目前,在激光切割和刻蚀处理后,ESI公司可以实现割缝宽度为20μm的洁净切割。ESI 9900系统的软件包含根据加工材料所设定的独有的、为客户定制的激光切割参数。
“目前我们正在与客户一道优化激光加工和刻蚀过程,对于我们正在看到的较高的芯片断裂强度和高产量,我们备受鼓舞。”ESI公司半导体生产部门的生产经理David Lord说道,“我们的目标是为客户降低拥有成本,使我们的客户能够在大批量制造环境中充分采用三维集成。”
编辑:hfy
-
半导体
+关注
关注
334文章
27254浏览量
217939 -
摩尔定律
+关注
关注
4文章
634浏览量
78986 -
激光器
+关注
关注
17文章
2512浏览量
60322 -
晶圆
+关注
关注
52文章
4884浏览量
127921 -
光纤激光器
+关注
关注
12文章
178浏览量
20043
发布评论请先 登录
相关推荐
激光先进制造技术
叠层电感-叠层陶瓷电感-贴片叠层电感-片式叠层电感
高重频半导体激光驱动电路设计
小功率激光填丝焊接技术研究
11 BGA封装激光重熔钎料凸点制作技术
线性卷积重叠保留能否舍去前两个混叠值不要?
激光显示技术的特点
纳秒紫外激光器在汽车按键激光镭雕应用技术
激光雷达系统中激光器高重频优化研究
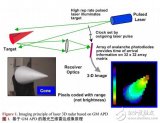
叠层模具的基本结构组成及具有哪些应用优势
叠层电感的优点和应用
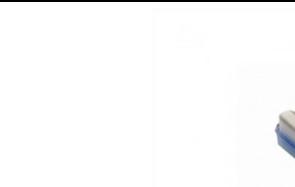
Z型全自动叠片机:锂电池叠片双张重叠丨单双张检测解决方案
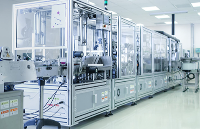
锂电池叠片机双张检测方案-阿童木双张检测传感器
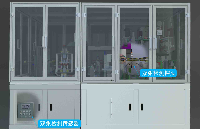
评论