随着5G网络的快速发展,5G天线模块的需求越来越多,为满足其特殊性能,部分天线模块设计厚度已达到11.5mm以上;针对此类超厚板,在层压、钻孔、线路及CNC等工序均面临较大的技术瓶颈。本文从叠层设计优化入手,采用两次分压子部件并提前做好线路及表面处理,然后总压钻孔,再采用二次内定位成型等技术,有效实现了11.5mm超厚板的批量加工,满足了客户特种需求。
5G网络作为第五代移动通信技术,其最高理论传输速度可达每秒数10Gb,这比目前4G网络的传输速度快数百倍;由于其高速率、低时延、低功耗的特点,未来将渗透到物联网及各行各业,与工业设施、医疗仪器、交通工具等深度融合,有效满足工业、医疗、交通等垂直行业的多样化业务需求。同时随着5G网络时代的快速来临,其核心部件5G天线模块的需求也越来越多,为满足其特殊性能,部分天线模块设计厚度已达到11.5mm以上;针对此类超厚板,在层压、钻孔、电镀、线路及CNC等工序均面临较大的技术瓶颈。本文从叠层设计优化入手,采用两次分压子部件并提前做好线路及表面处理,然后总压钻孔、再采用二次内定位成型等技术,有效实现了11.5mm超厚板的批量加工,满足了客户特种需求。
超厚5G天线模块加工工艺分析
该产品的关键技术难点涉及5大块,包括:(1)超厚板盲埋孔+背钻+树脂塞孔技术;(2)超厚板层压技术;(3)超厚板二钻精度控制技术;(4)超厚板表面处理工艺;(5)超厚板外形加工技术。
针对这些难题,需要对产品结构优化以满足可制造性。客户设计线路为6层,使用4张高频材料对压,成品板厚为11.44mm,考虑到天线模块的设计指标,各层介质厚度无法降低。
客户原设计金属化通孔+背钻,考虑到11.5mm超厚板压合后在沉铜/电镀/线路/蚀刻/阻焊等工序的困难度,经分析网络连接后,建议客户将原L36+L13背钻取消,更改为L13+L46盲孔互连,结构优化后两次分压厚度为6.7mm+4.3mm,其电镀难度大大降低,且盲孔设计比背钻更利于高频信号传输,如下图1所示。考虑到总压后阻焊及表面处理制作困难,特将流程优化到分压后制作完成,即总压后无需再做阻焊及表面处理。
经上述工艺优化后,11.5mm天线模块加工基本有了可制造性。
图1 优化为两次盲孔分压再总压结构
产品制程设计
超厚板两次盲孔分压
对两次盲孔分压流程设计如下:
①盲孔L1/L3+背钻+树脂塞孔(使用X公司高速板材与高速PP,子部件板厚6.7mm)
流程:内层L10+L23制作→L1/L3分压→钻孔→等离子→沉铜→一铜
背钻→树脂塞孔→内线酸蚀→内层蚀检
②盲孔L4/L6制作+树脂塞孔(使用X公司高速板材与高速PP,子部件板厚4.3mm)
流程:内层L5/6常规流程制作→L4/L6分压→钻孔→等离子→沉铜→一铜
→树脂塞孔→内线酸蚀→内层蚀检
考虑到总压后整体板厚达到11.5 mm左右,在此厚度下制作阻焊及表面处理非常困难,为此特将流程优化到分压后/总压前制作完成,即总压后无需再做阻焊及表面处理。
此外层压的板边还要设计两组铆合定位孔,便于后续压板可进行精确对位,如下图2所示。
图2 板边两组铆合定位孔设计
总压前还要进行沉边处理,沉边后用8mm长度铆钉即可满足铆合要求。
①L1/3板厚6.7mm,从顶层长边沉边深度3.2mm,余厚3.5 mm。
②L4/6板厚4.3mm,从底层长边沉边深度2.3mm,余厚2.0mm。
完成总压后进行切片分析,可见切片层间偏移在4.0mil以内,符合客户要求,效果如下图3所示。
图3 总压后对位切片图
-
pcb
+关注
关注
4326文章
23159浏览量
399542 -
天线模块
+关注
关注
0文章
9浏览量
8901 -
5G
+关注
关注
1356文章
48503浏览量
565718
发布评论请先 登录
相关推荐
移远通信推出八款天线新品,覆盖5G、4G、Wi-Fi和LoRa领域
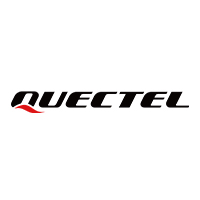
最常见的三种RFID标签天线制作工艺介绍
服务于低频带5G频谱以及传统频带的宽带天线
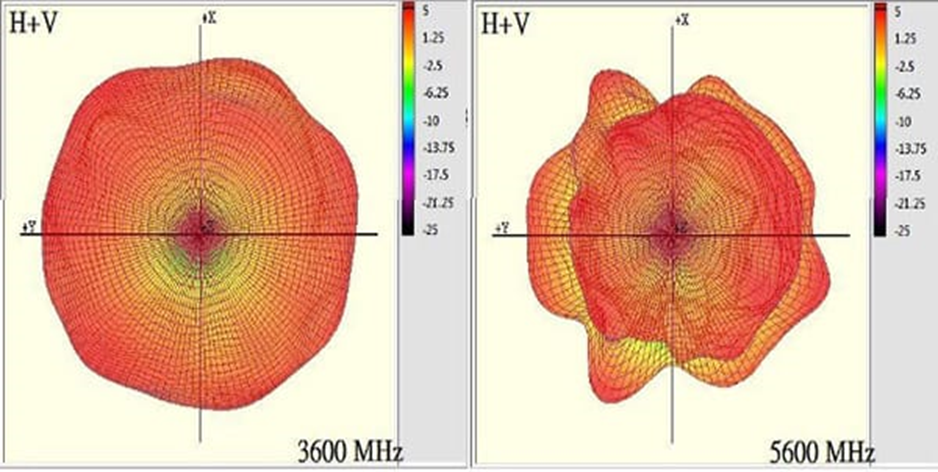
嵌入式设备中的4G/5G模块管理
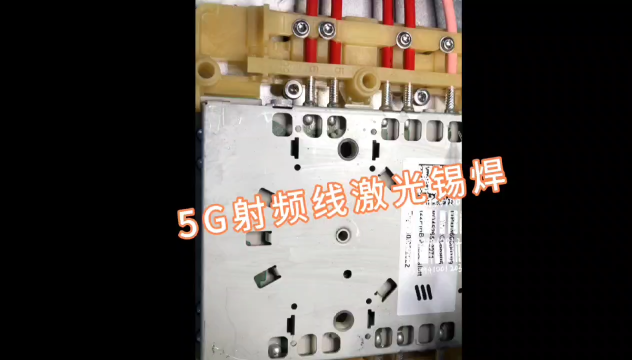
请问mx880 5G数据终端可以设置优先5G网络吗?
HDI多层板制作工艺
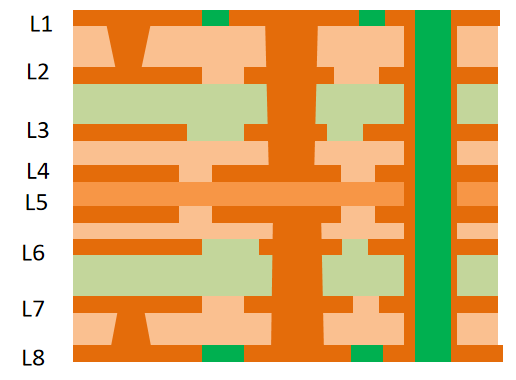
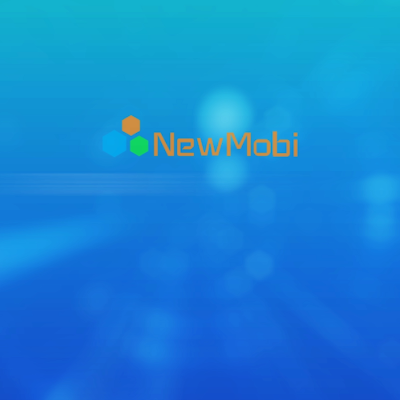
MPI 5G手机天线新材料的应用及焊接制造
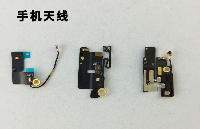
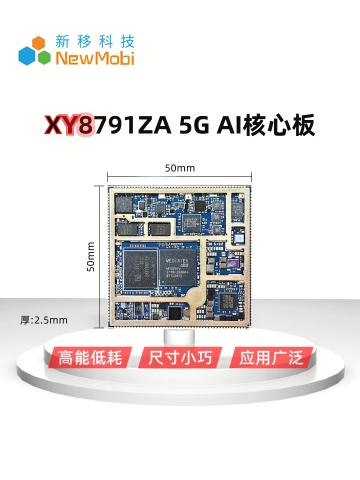
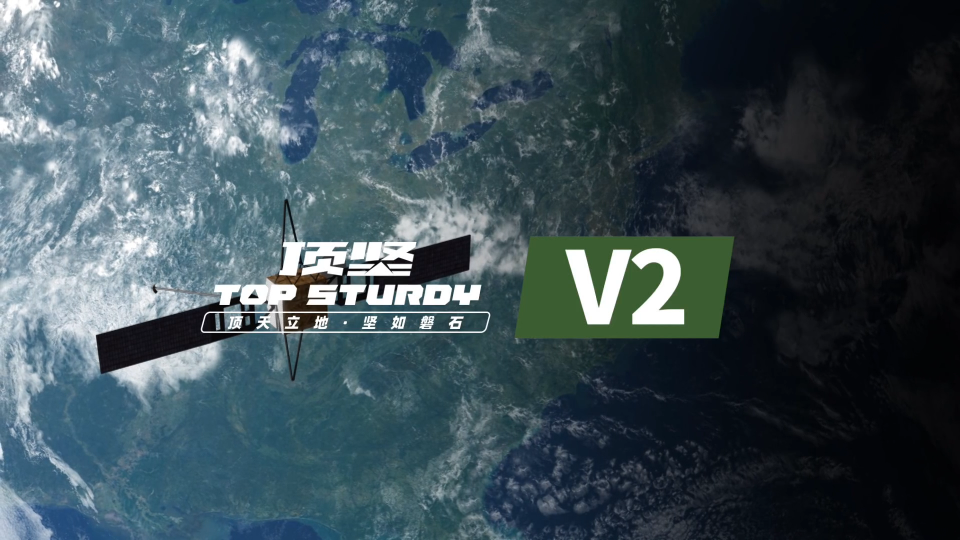
评论