摘要
IPG推出新产品YLS-AMB光束模式可调激光器及LDD-700焊接全过程监测系统,助力中国动力电池产品性能进一步提升。
2020年,一系列的新能源汽车起火召回事故再次引发关于动力电池安全的讨论。
通用、宝马、福特、现代四家国际车企合计召回了近20万辆主力电动汽车,召回原因直指动力电池。
在现代KONA EV召回事件中,韩国国土交通省汽车安全研究所KATRI给出的调查结果是,主要问题出在电池制造不良,正负极之间的隔膜由于制造过程中的质量差而损坏,可能会导致内部短路从而引起火灾。
宝马给出的召回原因是,三星SDI的电池组在生产过程中可能存在杂质。初步判断认为,部分电芯没有按照宝马的要求生产。而福特Kuga PHEV的召回,官方给出的结论同样是电芯生产过程中混入了杂质。
电芯内部混入杂质主要有两种可能,一是锂电池正负极等原材料中混入了杂质;二是电芯在焊接、切割、清洗等生产过程中混入了粉尘或异物,极端情况下可能导致电芯短路,引发动力电池热失控并产生起火风险。
事实上,激光焊接尤其是大功率焊接过程中,容易产生飞溅,这将对电池性能产生直接影响。消除飞溅也成为了电池企业对激光设备企业提出的迫切要求。
为进一步提升电芯制造的可靠性、一致性和产品良率,全球高功率光纤激光器和放大器的领导者——IPG,凭借其国际领先的光纤激光器研发技术,推出新产品YLS-AMB光束模式可调激光器及LDD-700焊接全过程监测系统,助力中国动力电池产品性能进一步提升。
目前,光纤激光技术主要应用于动力电池生产过程中的电芯、极柱、软连接、注液孔、防爆阀、模组、极耳等激光焊接;极耳、极片的切割和清洗、钻孔、雕刻等环节。
作为全球高功率光纤激光器和放大器的领导者,IPG的光纤激光器已经在锂电池制造过程中大规模应用。
从应用产品的类别来看,IPG研发量产的YLPN纳秒脉冲系列激光器用于极片切割、清洗;YLR及YLS系列连续激光器用于各焊接制程已经非常成熟。
值得注意的是,无论是从电芯的转接片焊接、顶盖密封焊接还是模组的BUSBAR焊接,激光焊接过程中产生的飞溅都可能造成电芯内部短路,从而对电池系统安全产生严重威胁。
此外,原有焊接过程中的质量监控和追溯采取抽检方式,无法实时检测电芯焊接全过程以及焊缝内在质量情况,这也给电芯制造留下了一些安全隐患。
在此情况之下,IPG推出了YLS-AMB光束模式可调激光器,瞄准激光焊接产生飞溅的痛点,大幅提升焊接质量。
IPG(北京)光纤激光技术有限公司应用部经理张婧博士对高工锂电表示,YLS-AMB光束模式可调激光器可有效抑制飞溅产生,提升整体焊接质量及良率,特别是在电池行业应用较多的铝、铜材料上效果非常明显。
据悉,IPG研发的YLS-AMB系列光束模式可调激光器可提供高达25 kW的总输出功率,可以根据材料加工要求,任意组合小光斑、高能量密度、高能量中心光束和较大环形光束。50μm中心功率高达9kW;100μm中心功率高达12kW。
与此同时,IPG可根据客户对不同输出功率的选择,可定制中心/环形光束输出功率以及相应的中心光纤和环形光纤芯径组合。
凭借创下行业纪录的输出功率,YLS-AMB系列光纤激光器可以通过同一激光器对不同厚度、多种材料进行优质加工。
在使用过程中,YLS-AMB通过将光束模式独立且动态调整的小光斑高能量密度的中心光束和较大环形光束任意组合,使得客户能够处理更为广泛的材料厚度范围,从而提高穿孔和切割速度及质量,并优化焊接性能。
在焊接方面,AMB通过产生稳定的匙孔和熔池,焊接时可降低90%飞溅。飞溅减少意味着工件少返工,停机时间减少且焊接区域污染少。AMB环形光斑激光器在提升焊接速度和稳定性的同时,对焊接的气密性和焊缝美观度上有着显著的作用。
IPG中国高功率焊接销售经理蒋宝文表示,IPG推出的AMB环形光斑激光器已经在头部电池企业中批量应用,可近乎实现无飞溅焊接,极大提升焊接效率以及质量,提升电池产品性能。
在减少飞溅的同时,为进一步降低成本、提升检测效率和可靠性,IPG还推出了基于相干干涉成像技术的LDD-700焊接全过程监测系统。
LDD-700焊接全过程监测系统入围2020 PRISM棱镜奖决赛。该解决方案可提供非破坏性实时多功能焊接监测,以此提供质量保障。焊前监测模式包括跟踪焊缝位置、检查到材料的工作距离并在加工开始前查找缝隙、不良固定或不良装配;在焊接过程中,在匙孔底部实时监测记录焊缝熔深以防过浅或过度穿透,以及工艺不稳定性;焊后检查是对焊缝表面高度、焊道宽度和表面缺陷(如深坑和爆裂) 进行检查。
具体来看,LDD-700可在每次焊前、焊中和焊后记录和发送各零件的实时数据。当零件发生损坏和焊接缺陷时,LDD-700 会向操作人员和系统发出警报,以便立刻采取措施更正,迅速恢复正常操作,确保向客户交付的都是良品。
通过提供更完整和更精确的测量记录,LDD-700焊接全过程监测系统使得每件产品可追溯,生产与安全相关的零部件时,避免因质量不确定造成工件大量报废,帮助制造商降低废品率且及早发现缺陷件。
蒋宝文表示,过去的一年,IPG与集成商一起合作,从软包电池开始进行了大量的LDD-700焊接全过程监测系统的推广验证。实践证明,LDD-700的测量数值与焊接熔池的实际形态非常接近,相比传统的金相切片检测方法,检测效率和精度更高。目前LDD-700已在软包电池焊接工位应用,在方形电池包的BUSBAR焊接工位,LDD-700也已取得成功案列。
全球6000名员工和专家团队,在多个国家建有生产、销售及服务基地,30年技术积累,专注工艺研发,凭借丰富的产品线和强大的技术与工艺团队支撑,IPG的光纤激光器已经在全球主流动力电池和主机厂中批量应用,助力电池企业产品质量提升和成本降低。
责任编辑:lq
-
电动汽车
+关注
关注
156文章
12096浏览量
231360 -
IPG
+关注
关注
0文章
8浏览量
8584 -
电芯
+关注
关注
14文章
726浏览量
25872
原文标题:【三木科技•技术π】 IPG杜绝焊接飞溅“秘籍”
文章出处:【微信号:weixin-gg-lb,微信公众号:高工锂电】欢迎添加关注!文章转载请注明出处。
发布评论请先 登录
相关推荐
浅谈半导体激光器的应用领域
VirtualLab Fusion应用:Ince-Gaussian光束产生涡旋阵列激光束的观测
电子科普!什么是激光二极管(半导体激光器)
高压放大器在高功率固体板条激光器光束实验中的应用
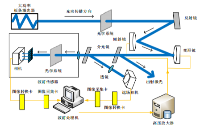
高质量激光光束光学系统中的空间滤波
近距离了解中红外可调谐光纤飞秒激光器 Femtum Ultratune 3400性能
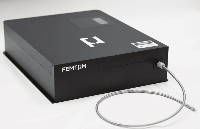
波长可调激光器中的增益芯片和SOA

评论