伴随着更多承载MinLED的新产品推出,该技术正处于落地的关键时点,在包括芯片、封装和基板选择等方面,均出现诸多新技术与新变量。本文将从这几个角度详细阐明。
MinLED芯片:仅需通过优化工艺来提升良率和产量即可实现从常规尺寸到Mini尺寸的跨越
LED芯片制造流程主要包括前道外延片制造、中道磊晶和后道晶片切割,涉及具体流程多达数十项,制造难度较高。
但由于LED产业的多年的发展,传统LED芯片制造设备与工艺已经较为成熟,且MiniLED对切割精度和转移设备的要求还未达到MicroLED那么严苛的程度,因此MiniLED芯片制造难度相对MicroLED较低,芯片厂仅需通过优化工艺来提升良率和产量即可实现从常规尺寸到Mini尺寸的跨越。
在转移技术方面,相比于Micro LED,MiniLED有较大的尺寸和更加硬质的衬底。
因此其转移过程有更高的精度容忍度和更多的灵活性。
当前主流厂商均有开发Mini LED相关的转移技术,主要包括以下三种:
1)方案一是对现有的抓取设备进行改进,通过设置多个的手臂来增加拾取和放置的效率。这种方案技术难度较低,因此更容易实现量产,不过其存在产能上的限制,无法实现数量级上的增加。
2)方案二是将芯片和背板相对放置,再使用顶针将芯片顶出,从而放置于基板上。相比于方案一,这种方案减免了摆臂的反复移动,从而提升了转移效率。而且,若芯片在蓝膜上放置位置同最终背板的控制电极位置一致,再配合多顶针,即可实现巨量转移,从数量级上提升转移效率。
3)方案三类似于方案二,芯片放置于UV膜上,通过UV光把LED芯片选择性地转移到背板上。该方案能实现真正的巨量转移,但是对芯片分选及其在UV膜上的摆放精度有较高的要求。
MinLED封装:全倒装+COB的新封装趋势
LED封装技术正在经历从传统的支架型封装(如SMD技术)向新型无支架型集成封装(如COB技术)的过渡。传统的LED封装技术主要为SMD(Surface Mounted Devices)技术,意为表面贴装器件。
SMD技术采用平面支架+点胶成型,并用表面贴装技术进行组装,采用合金铜材质扁平引脚,可组装在铝基板或PCB上。其工艺流程包括固晶、焊线、成型、切割、分光和带装入库。
SMD技术最小可以做到稳定像素间距在1.2-1.5mm区间,拥有技术成熟稳定、制造成本低、散热效果好和维修方便等优势,是十分成熟的LED封装技术。
不过,随着LED向Mini/Micro方向发展,SMD技术应用开始受限。其技术防护等级低、寿命短等缺陷开始暴露出来,尤其是在制造像素间距P1.2以下的显示产品时,SMD封装技术开始出现诸多无法克服的技术瓶颈。例如SMD技术无法满足Mini LED显示产品的面板级像素失控率要求。
COB(Chip On Board)封装技术是一种无支架型集成封装技术,这种技术通过将LED芯片直接贴装于PCB板上,在PCB板的一面做无支架引脚的COB高集成度像素面板级封装,在PCB板的另一面布置驱动IC器件,而不需要任何支架和焊脚。
与传统的SMD技术相比,COB技术能显著地降低LED显示面板的像素失效问题,同时还可以做到更小的点距,拥有更高的排列密度。
因此COB技术可以显著提升LED显示屏系统的像素密度和整体可靠性,为LED显示的4K、8K超高清视频显示产品、Mini LED显示产品提供底层高阶面板制造技术,是当前LED显示走向百万级的必然选择。
此外,在SMD和COB之间,还有多种支架型有限集成封装技术,主要包括2in1、4in1、Nin1封装技术。这种技术本质是SMD和COB的混合体封装技术,减少了支架引脚的数量,体现COB封装集成化的思想,但无法真正摆脱万级或十万级的面板级像素失控,在Mini LED 的1.2-0.9mm像素区间,会遇到与SMD封装技术相同的技术瓶颈问题。
图28:传统SMD封装与COB封装对比
除了COB技术外,封装端还创新性的引入了倒装工艺来实现更高发光效率、排列密度和可靠性。
传统的正装技术存在着电极遮挡影响发光效率以及焊线较多工艺流程复杂等缺点。而倒装技术通过将芯片倒置,使发光层激发出的光直接从电极的另一面发出,在封装工艺上实现无电极遮挡、无焊线,因而可以最大程度提高发光面积、散热面积,并能够避免金属虚焊和接触不良引起的问题。同时,无焊线还可以提升芯片排列密度,助力LED进一步提升显示像素密度。
目前在1.2mm以上像素间距范围,还可以使用正装芯片,在1.2-0.7mm像素间距范围内,有红光正装、蓝绿光倒装的解决方案,在0.7-0.3mm像素范围内,RGB都要使用倒装芯片。
未来随着LED向Mini/Micro方向加速演进,倒装技术将迎来快速渗透。
综上,对MiniLED产业来讲,SMD封装技术是目前工艺较为成熟、成本更低的封装搭配,其将在中低端MiniLED产品推广中使用。而倒装COB技术,则是面向未来的新型封装技术,长期来看,其发光效果优势、可靠性优势和高密度排列优势将被进一步放大,有望实现对SMD技术的替代。
MiniLED基板选择:PCB VS 玻璃基
基板是LED芯片的载体,MiniLED基板包括PCB方案和玻璃基方案。
其中,PCB是最常用的LED基板,具有技术成熟、成本低等优势,主要由LED产业链厂商推广使用。
而玻璃基板是LCD的关键物料之一,后经面板厂推广至LED基板。
随着MiniLED应用不断深化,基板被提出了更高的要求,相关产业格局也有望迎来转变。
1. 成本方面,从材料角度来看,PCB基板的价格是玻璃基板的几倍,因此如果规模化生产,玻璃基板的物料成本其实更低。
但是从综合成本来看,由于玻璃基板走线需要开光罩,所以前期投入成本较高,若是规模化程度不高,可能平均成本反而会超过PCB基板。
此外,从良品率来看,我国目前封装厂对于PCB基板的技术要更加成熟、可靠性更强,良品率也更高,因此成本的可控性更强。而玻璃基板由于玻璃的易碎性,良品率较低。
因此综合来看,当前PCB基板仍具成本优势,但长期来看,随着玻璃基板规模化程度和良品率提升,玻璃基板成本有望大幅下降,甚至低于PCB基板。
2. 性能方面,PCB基板散热性弱于玻璃基板,且在芯片焊接中由于热量密度较高,所以容易导致翘曲变形的问题,尤其在大尺寸的应用中,在多组背光单位拼接过程中容易产生拼缝问题。
而玻璃基板受热膨胀率低,散热性强,因此平坦性更高,更有利于Mini LED的焊接,因此玻璃基板可以满足高精度需求。
3. 应用前景方面,PCB基板是国内目前技术工艺条件下的首选,其被当前绝大部分LED产品使用。
而对于散热要求更高、平坦度要求更高或者高密度组装的情况,玻璃基板将是更好的选择。
2020年CES展上,TCL正式推出了采用玻璃基MiniLED方案的“MLED星曜屏”。
该产品拥有超高亮度,在逆光情况下也能出众地成像;其对比度高达100万比1,相比传统LCD有指数级的提升;同时其在HDR及动态背光分区等细节也有不俗表现。
综上,我们认为现阶段对于Mini LED产品,PCB基板是终端厂商在市场需求量较小时,综合成本和性能后的选择。放眼未来,随着MiniLED需求放量,玻璃基板有望形成规模化出货,其成本也将被摊薄。届时,玻璃基板竞争优势将充分展现,并有望实现对PCB基板的替代。
本文综合整理自未来智库官网 电子技术设计
责任编辑:pj
-
芯片
+关注
关注
456文章
50886浏览量
424180 -
pcb
+关注
关注
4319文章
23111浏览量
398243 -
LED封装技术
+关注
关注
0文章
15浏览量
6756
发布评论请先 登录
相关推荐
SMD元件的应用领域 SMD芯片与传统芯片的区别
SN74ALVC164245与SNALVC164245-EP区别在哪里呢?
SMD电阻器与传统电阻器的区别
揭秘LED三大封装技术:SMD、COB、IMD的全面解析
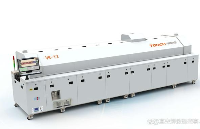
先进封装与传统封装的区别
ai大模型和传统ai的区别在哪?
erase before programing和blank check before programing在下载时区别在哪?
什么是PWM和SPWM波形?两者的区别在哪?
传统封装和先进封装的区别
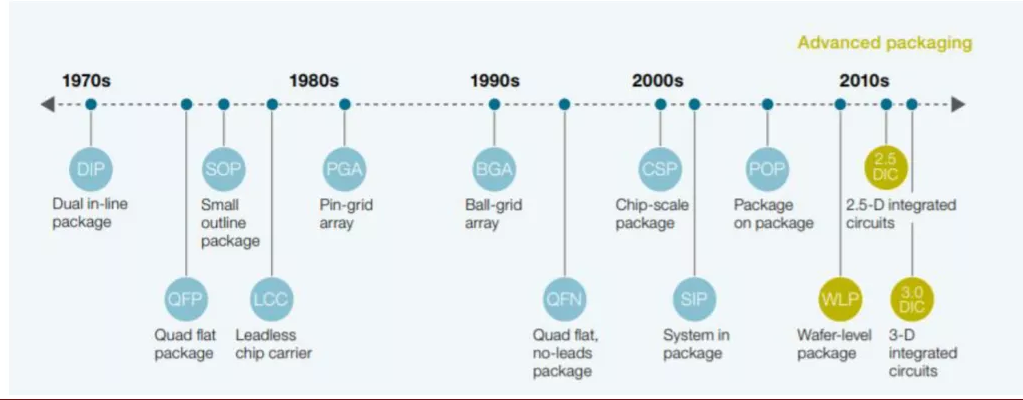
评论