Micro-OLED 以单晶硅芯片为基底,增加可靠性,实现轻量化
已具备量产能力的 Micro OLED,已成为现阶段 VR 头显厂商设计高端 VR 设备时的首选显 示技术。市面上的多数 VR 产品都采用 LCD 显示面板,VR 头显设备都略显笨重。
Micro OLED 显示器以单晶硅芯片为基底,像素尺寸为传统显示器件的 1/10,精细度远远 高于传统器件, 其区别于常规利用非晶硅、微晶硅或低温多晶硅薄膜晶体管为背板的 AMOLED 器件。单晶硅芯片采用现有成熟的集成电路 CMOS 工艺,不但实现了显示屏像素 的有源寻址矩阵,还在硅芯片上实现了如 SRAM 存储器、T-CON 等多种功能的驱动控制 电路,大大减少了器件的外部连线,增加了可靠性,实现了轻量化。
Micro-OLED 优点:与传统的 AMOLED 显示技术相比,Micro OLED 有以下突出特点:
1) 基底芯片采用成熟的集成电路工艺,可通过集成电路代工厂制造,制造良率更是大大高 于目前主流的 LTPS 技术。
2)采用单晶硅,迁移率高、性能稳定,寿命高于 AMOLED 显示器。
3)200mm×200mm 的 OLED 蒸镀封装设备就可满足制造要求(与 8 英寸晶圆尺寸兼容),而 不像 AMOLED 需要追求高世代产线。
4) OLED 微显示器体积小,非常便于携带,并且其依借小身材提供的近眼显示效果可以与 大尺寸 AMOLED 显示器相媲美。
优点:与其他微显示技术相比,Micro OLED 亦具有不少优点:
1 ) 低功耗,比 LCD 功耗小 20%,电池重量可以更轻。
2) 工作温度宽,LCD 不能在极端温度如 0℃下工作,必须额外加热元件,而在高温下又必 须使用冷却系统,所有这些解决方案都会增加整个显示器的重量、体积和功耗。而 OLED 为全固态器件,不需要加热和冷却就可以工作在-46℃~+70℃的温度范围内。
3 ) 高对比度,LCD 使用内置背光源,其对比度为 60:1,而 OLED 微显示器的对比度可以 达到 10,000:1。
4) 响应速度快,OLED 像素更新所需时间小于 1μs,而 LCD 的更新时间通常为 10~15ms, 相差了 1,000 到 1,500 倍,OLED 的显示画面更流畅从而减小视疲劳。
下表列出了不同微显示的性能比较,可以看出 Micro OLED (OLED on Silicon)在性能上有较 为明显的优势,其中亮度、综合发光利用率、对比度、色彩能力、像素点距性能都非常优 秀。
从未来市场角度来看:2021 年全球 Micro OLED 在中国产商推波助澜下开始放量,预计 2021-2027 年出货量实现 CAGR 65.21% 的增长。
Micro-OLED 工艺制程:CMOS 技术与 OLED 技术的紧密结合
Micro OLED 是 CMOS 技术与 OLED 技术的紧密结合,是无机半导体材料与有机半导体材 料的高度融合。CMOS 技术主要使用光刻工艺、CMP 工艺等,湿法制成较多,而 OLED 技 术则主要采用真空蒸镀技术工艺,以干法制程为主。两者皆专业且复杂,将两者集成于同 一器件之中,对于工艺技术要求非常严苛。
Micro OLED 器件制造主要通过以下四个步骤实现:
1)硅基 IC 设计与制造:主要涉及集成电路的设计和制造,分别由 IC 设计团队和 foundry 厂完成;
2)OLED 制程:主要包括 OLED 微腔顶发射技术,阳极材料技术,全彩化技术等;
3)OLED 封装制程:包括薄膜封装,玻璃 cover 贴合封装等;
4)显示驱动与系统:与第一部分设计制造紧密相连。
硅基 OLED 微显示器传统制程。a 为器件结构截面示意图,b 是制造流程。其 中流程 1~7 为大片制造。从流程 8 切割后,即为 dice 制造流程。流程 1 为硅基芯片的制 造过程,由集成电路晶圆代工厂按照客户的设计和要求进行生产制造;流程 2~7 为 OLED 的制造流程,在 OLED 工艺代工厂制作完成。其中,流程 2 和 3 为像素阳极的制备过程, 包括阳极材料的成膜及其图案化,涉及较多湿法制程。在传统的硅基 OLED 微显示器制造 工艺中,该制程由 OLED 工厂来制作完成;流程 8~9 由集成电路芯片封装厂完成;流程 10 为模组与系统开发,将硅基 OLED 制作成微显示器模组供用户使用。
Micro OLED 制造设备涉及微电子和光电子制造设备。其中阳极制造需要金属溅射成膜设 备,阳极图案化则涉及晶圆清洗设备、光刻胶涂覆设备、曝光设备、显影去胶设备、烘烤 等设备,这些均属半导体设备。OLED 制程段则需要 OLED 蒸镀设备、薄膜封装设备以及 玻璃贴合封装设备等,这些设备集成为一套系统,在一系列真空和惰性气体气氛内完成。
Micro-OLED 器件结构:驱动背板+OLED 显示前端组成
器件结构: Micro OLED 显示器件以单晶硅作为衬底,在单晶硅衬底上采用标 准的 CMOS 工艺制作显示驱动电路,以提供 OLED 显示所需的像素驱动部分、行列驱动部 分以及其它所需的 DAC 转换等功能电路。在单晶硅衬底上接着制作 OLED 发光单元,由于 硅片衬底不透明,需要制作顶发射 OLED 器件。首先在衬底上,制作高反射率的金属作为 阳极,阳极电极具有较高的反射率可以实现较高的出光效率。接着制作空穴注入层、空穴 传输层、发光层、电子传输层、电子注入层等有机半导体层,形成 OLED 主体发光单元。最后,为了实现光从顶部出射,需要制作半透明的金属层作为阴极。由于OLED 器件怕水 氧等破坏,在阴极上需要制作薄膜封装层,用于阻隔水氧,在封装层上,进一步贴合玻璃 进行器件强度保护。
驱动芯片架构:驱动芯片采用 0.18μm的 CMOS 工艺设计,驱动背板包括像素电路、行列 驱动、DAC、I2C、数据处理、电源模块、温度检测等功能模块。芯片采用 数字接口,针对高分辨率的应用要求,利用数据采样与比较完成数据传输,驱动芯片像素 采用电压型驱动方式。由于 OLED 器件在不同的温度条件下,器件亮度变化较大,因此在 芯片中集成了温度传感模块,可以实时监测芯片工作温度,实现芯片在高低温下精确调节 电压输出,来调节器件的显示亮度,保持器件显示的稳定和一致。硅基 OLED 器件包括控 制电路芯片部分和显示驱动芯片部分,为了方便用户使用芯片,在驱动芯片中集成了三路 电源模块,包括正压 DC-DC 模块、负压 DC-DC 模块和 LDO 模块。这三路电源模块,可 分别实现给像素整列、OLED 显示的公共阴极和芯片中的控制电路供电。
Micro-OLED 公司:我国视涯科技、京东方、梦显电子、奥雷德等从事研发和中试
目前全球从事硅基 OLED 研发生产的厂商不多,其中美国 eMagin 公司和法国 MicroOLED 公司的产品主要应用于军事领域,能成熟量产的 Micro-OLED 供应商只有索尼公司,在全球 市场处于垄断地位。
我国硅基 OLED 产业化尚处于初级阶段。我国合肥视涯科技、京东方、昆山梦显电子、奥雷德等公 司正在从事硅基 OLED 研发和中试,其中京东方在 2019 年实现了 8 英寸硅基 OLED 生产 线的量产,合肥视涯科技于 2019 年 11 月竣工投产 12 英寸硅基 OLED 显示项目,昆山梦显 电子正在建设一条 8 英寸硅基 OLED 生产线。目前国内硅基 OLED 的低温彩色滤光片工 艺、薄膜封装工艺、硅基数字化驱动技术、核心装备等高性能微显技术和大规模量产技术 等均处于初期阶段。
责任编辑:lq
-
存储器
+关注
关注
38文章
7494浏览量
163915 -
Micro
+关注
关注
2文章
263浏览量
34859 -
单晶硅
+关注
关注
7文章
191浏览量
28277
原文标题:解读近眼显示技术-微显示:Micro-OLED 成为终端的主流技术选择
文章出处:【微信号:WW_CGQJS,微信公众号:传感器技术】欢迎添加关注!文章转载请注明出处。
发布评论请先 登录
相关推荐
天马OLED技术论坛成功举办
OLED屏的技术原理与优势分析
三星与LG Display携手推动串联micro-OLED技术
苹果寻求LG显示和三星显示为更便宜的头显供应Micro-OLED屏
三星LEDos技术瞄准AR设备,Micro LED芯片厂商加码自研技术
小米与卢米蓝联手创立OLED关键材料与器件联合实验室
探寻未来显示技术:LCD、LED、OLED谁将引领潮流?
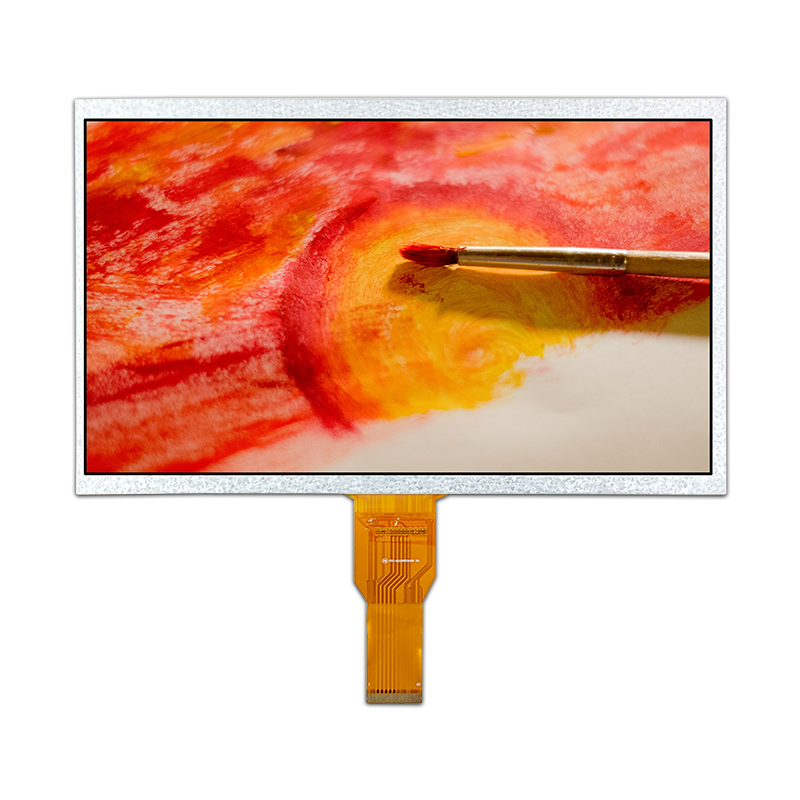
评论