随着市场竞争的日益激烈,产品低价格、高质量、交货周期短已成趋势,在电子制造业中,躺着赚钱的日子一去不返,越来越多的企业开始重视DFX,然而DFX如何快速融入企业及产品开发中呢?
传统的产品开发与生产制造各有各的流程及理念,你研发我制造,这种模式的结果往往是1+1《1的,产品量产后需花费大量的成本去改善设计问题。
DFX的理念要求研发和制造相互协同,在产品开发阶段就将DFX的思想融入到产品开发中,实现1+1》2,以DFM来说,就要在产品开发过程中考虑产品的可制造性,然而研发与制造毕竟是两个不同的领域,正所谓隔行如隔山,这时候,可能很多DFM的工程师就开始给研发制定各种DFM设计规则,要求研发被动的执行,往往很多的规则就形同虚设。
无论是产品的功能开发,还是生产的工艺改善,最先需要想的问题是为什么要这样做,制造与研发要达成共识,有共同的设计理念才行,而不是一开始就考虑怎么做,制定设计规则其实就是在考虑怎么做。往往“为什么做”比“怎么做”更重要,设计规则/标准只是基础,DFX理念才是核心!
1、研发与DFX跨界学习,DFX工程师学习产品功能开发相关知识,研发人员熟悉生产制造
互相学习,跨界思考,推动产品设计创新,相互了解各自的难点痛点,针对性思考及攻关,将生产的经验及理念融入到产品开发中,研发代表公司最核心的竞争力,除了产品性能强,同时也要具备最优的可制造性,共同设计出低成本、高质量、周期短的产品。对于DFX引入初期,想要改变一个企业整个研发团队的理念,其难度可想而知,这就需要DFX人员在日常工作中透过优秀案例、良好的收益与研发沟通交流,一点一滴的改变,从而相互协同促进,建立良好的信任关系。
所以一个企业好的DFX体系,也是需要时间及经验慢慢沉淀。在这过程中,DFX人员起到关键性、决定性的作用,千万少出问题,要求研发反复修改设计,从而降低研发对DFX的信任及认同感,也绝不是简单的制定设计规则要求研发执行如此简单。
针对研发设计人员,要实际到生产线学习,了解整个生产制造过程,不然自己设计的产品是如何生产出来的都不知道,实践与理论相结合,才能设计出理想的产品。
2、产品概念阶段,提出DFX需求,产品开发阶段DFX要积极投入,参与到产品设计中,提出建设性意见,并积极参与技术自检与技术评审(以IPD流程为例)
这就是之前文章中提到的并行工程,在产品研发阶段,参与的人员越多,提出的意见越多,考虑的问题越全面,修改的越多,产品的DFX越强,“我们”永远比“我”更强大。
当DFX在企业形成一种文化,从研发到产线员工全员参与,公司随处可见“DFM改善”等字样的时候,公司产品的DFX能力会达到什么样的水平?曾有人说,在PCB发版前进行评审,太耽误时间,影响开发周期,我想说,或许就评审的这几个小时,发现了问题并进行修改,就可减少一次改版呢?进行一次改版,影响的时间周期肯定不是几个小时就能弥补的,这还不考虑其他成本。
3、设计标准制定,迭代更新
…………
编辑:jq
-
DFM
+关注
关注
8文章
465浏览量
28425 -
DFx
+关注
关注
0文章
35浏览量
10594
发布评论请先 登录
相关推荐
三品PLM研发管理系统干什么用的:赋能企业创新,加速产品上市进程
充分考虑设备的体验性易用性 蓝鹏设计部将这一理念贯穿于整个研发过程
深度揭秘!观测云产品核心理念
戴森新款吹风机HD16发布对国内厂商的启示
如何在AMD Vivado™ Design Tool中用工程模式使用DFX流程?
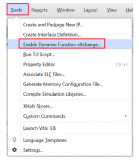
护肤市场新浪潮来了!绿展科技用一片抗衰电子面膜撬动千亿“她经济”?
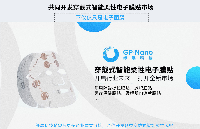
长电科技全面贯彻DFX理念,提供全方位的设计支持
Samtec制造理念系列一 | 差异变量的概念
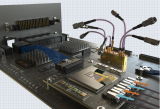
评论