汽车已经从纯粹的机械结构发展到电子零件的参与。早在20世纪70年代,汽车含电子零件的平均值约为$ 100,而在2000年这个数值已经达到$ 1500和它已经攀升到 $ 2013年,全球汽车电子市场已突破1500十亿美元到2020年,这一数字预计将超过2400亿美元。
此外,据估计,到2020年,市值为1910亿美元的汽车电子系统将猛增至3144亿美元的市场,平均复合增长率为7.3%。顶级汽车可能包含150个电子控制单元,其中大部分是驾驶舱内的传感器和处理器。根据一些报告,电子产品的实际价值的65%在于动力系统,汽车车身和底盘,并且大多数与数字电源有关。电动汽车的电子价值将超过70%。
装有电子设备的汽车中一定要使用电路板。2014年,全球汽车PCB占46亿美元,到2020年,这一数字估计将超过70亿美元。
汽车系统中的应用是提高汽车性能,为现在显示在三个方面了:
a.改善环境是指节省燃料和减少排放,即从汽油,天然气和生物燃料到混合动力和纯电力的过程。电动汽车已成为主要的发展趋势。
b.安全性提高指的是交通事故的减少,范围从安全气囊到雷达监控,立体摄像机,夜间红外监控,自动避撞和自动驾驶。据估计,自动驾驶汽车将在三年内实现商业化。
c.方便舒适从专用于汽车的音频,视频和空调到计算机,移动通信,互联网,导航和电子收费的范围,所有这些都必须更加方便和用户友好。
汽车PCB的基本要求
•质量保障要求
汽车PCB制造商应遵守ISO9001的规定。PCB制造商完全符合ISO9001:2008质量管理体系,并致力于在制造和组装方面遵守最严格的标准。
汽车产品有其特殊性。1994年,福特,通用汽车和克莱斯勒一起,在汽车行业建立了质量控制体系QS9000。在早期的21日世纪,随着ISO9001标准兼容,在汽车行业的新的质量控制体系发表,也就是ISO / IATF16949。
ISO / IATF16949是全球汽车行业的一组技术法规。基于ISO9001,加上汽车行业的特殊要求,它更侧重于缺陷预防,减少质量波动和在汽车零部件供应链中容易产生的浪费。在实施ISO / IATF16949时,必须特别注意以下5个主要工具:
PPAP(生产零件批准流程),规定产品在批量生产之前或修改后应获得客户的认可;APQP(高级产品质量计划),规定在生产之前应先进行质量计划和先前的质量分析,然后进行FMEA(故障模式和影响分析)分析并提出防止产品潜在故障的措施,MSA(测量系统分析)必须分析测量结果的变化以确认测量可靠性,SPC(统计过程控制)掌握生产规程并使用统计技术来改变产品质量。因此,PCB制造商进入汽车电子市场的第一步在于获得IATF16949证书。
•性能的基本要求
a.高可靠性
汽车可靠性主要来自两个方面:寿命和耐环境性。前者是指可以在使用寿命内保证正常运行的事实,而后者是指当环境变化时PCB功能保持不变的事实。
1990年代汽车的平均寿命为8-10年,目前为10-12年,这意味着汽车电子系统和PCB都应在此范围内。
在应用过程中,汽车应承受气候变化的影响,从极冷的冬天到炎热的夏天,从阳光到雨,以及由于自身行驶导致的温度上升所引起的环境变化。换句话说,汽车电子系统和PCB必须承受多种环境挑战,包括温度,湿度,雨水,酸雾,振动,电磁干扰和电流浪涌。另外,由于PCB是组装在汽车内部的,因此主要受温度和湿度的影响。
b.重量轻,体积小
轻巧,微型的汽车有利于节能。轻质源自减轻每种成分的重量。例如,某些金属零件被工程塑料零件代替。此外,汽车电子设备和PCB都应微型化。例如,ECU的体积(电子控制单元)中的汽车应用是大约1200厘米3在2000年开始,而小于300厘米3,通过四次下降。另外,起点枪械已经从通过导线连接的机械枪械转变为通过柔性导线连接且内部带有PCB的电子枪械,体积和重量减少了10倍以上。
PCB的轻量化和小型化源自密度的增加,面积的缩小,厚度的减小和多层化。
汽车PCB的性能属性
•多种汽车PCB
汽车将机械和电子设备结合在一起。现代汽车技术融合了传统技术和先进的科学技术,例如手动内部装饰部件和先进的GPS。在现代汽车中,存在着在不同位置具有不同功能并且不同类型的PCB衍生出不同功能的电子设备。
根据基板材料,汽车PCB可以分为两大类:无机陶瓷基PCB和有机树脂基PCB.陶瓷基PCB具有耐高温性和出色的尺寸稳定性,使其可以直接应用于高温电机系统。但是,它具有陶瓷制造性差和成本高的特点。目前,随着树脂基板材料在耐热性方面的发展,基于树脂的PCB已被广泛应用于具有不同性能应用于不同位置的基板材料的汽车中。
一般而言,柔性PCB和刚性PCB用于通常的仪表中,以指示车速和行驶里程以及空调设备。双层或多层PCB和Flex PCB用于汽车内的音频和视频娱乐设备。对于通信和无线定位设备以及安全控制设备,应用了多层PCB,HDI印制电路板和Flex PCB.对于汽车电机控制系统和动力传动控制系统,应使用特殊的板。
例如金属基板和刚柔性PCB.对于微型汽车,应用组件嵌入式PCB.例如,微处理器芯片应用于电源控制器中,直接嵌入电源控制器PCB中。再例如,嵌入元件的PCB也被用于自动支持系统的导航设备和立体成像设备中。
•不同位置的PCB的不同可靠性要求
就公共安全而言,汽车属于高可靠性产品类别,因此,汽车PCB必须通过一些可靠性测试,而尺寸,尺寸,机械和电气性能等一般要求除外。
a.热循环测试(TCT)
根据根据汽车的不同位置分类的五个等级,PCB热循环温度总结在下表1中。
b.热冲击试验
汽车PCB越来越多地应用于高温环境中,这对于必须处理外部热量和自发热的厚铜PCB尤其如此。结果,汽车PCB对耐热性有更高的要求。
c.温湿度偏差(THB)测试
由于汽车PCB处于多种环境中,包括雨天或潮湿的环境,因此有必要对其进行THB测试。测试条件包括以下要素:温度(85℃),湿度(85%RH)和偏置(DC 24V,50V,250V或500V)。
THB测试必须考虑PCB的CAF迁移。CAF通常发生在相邻的过孔,过孔和线,相邻的线或相邻层之间,从而导致绝缘降低甚至短路。相应的绝缘电阻取决于通孔,线和层之间的距离。
汽车PCB的制造特征
•高频基板
汽车防撞/预测制动安全系统起着军事雷达设备的作用。由于汽车PCB负责传输微波高频信号,因此需要将介电损耗低的基板与普通基板材料PTFE一起使用。与FR4材料不同,PTFE或类似的高频基体材料在钻孔过程中需要特殊的钻孔速度和进给速度。
•厚铜PCB
由于高密度和高功率以及混合动力,汽车电子产品带来了更多的热能,而电动汽车往往需要更先进的动力传输系统和更多的电子功能,从而对散热和大电流提出了更高的要求。
制作厚的铜双层PCB相对容易,而制作厚的铜多层PCB则困难得多。关键在于厚铜图像蚀刻和厚度空位填充。
厚铜多层PCB的内部路径都是厚铜,因此图形转印光致干膜也相对较厚,需要极高的抗蚀刻性。厚铜的图形蚀刻时间会很长,并且蚀刻设备和技术条件处于最佳状态,以确保厚铜的完整布线。当进行外部厚铜布线制造时,可以先在层压相对较厚的铜箔与图形化厚铜层之间进行组合,然后进行膜空隙蚀刻。图形电镀的抗电镀干膜也相对较厚。
厚铜多层PCB的内部导体与绝缘基板材料之间的表面差异较大,普通的多层板层压无法完全填充树脂,并产生空腔。为了解决该问题,应尽可能地使用树脂含量高的薄的预浸料。某些多层PCB上内部布线的铜厚度不均匀,并且可以在铜厚差较大或差异较小的区域中使用不同的预浸料。
•组件嵌入
为了增加组装密度和减小元件尺寸,嵌入式元件的PCB被大量应用于移动电话中,这也是其他电子设备所需要的。因此,组件嵌入式PCB也被应用在汽车电子设备中。
根据不同的元件嵌入方法,有许多用于元件嵌入式PCB的制造方法。用于汽车电子产品的元件嵌入式PCB主要有4种制造方法,如下图1所示。
在这些制造类型中,开挖类型(图1中的a型)遵循以下过程:开挖,然后通过回流或导电胶进行SMD组装。叠层类型(图1中的b型)是通过内部电路上的薄SMD组件通过回流实现的,或者是指薄部件制造。陶瓷类型(图1中的c型)是指印刷在陶瓷基板上的厚膜组件。模块类型(图1中的d型)遵循以下步骤:通过回流和树脂封装进行SMD组装。模块型元件嵌入式PCB具有相对较高的可靠性,更适合汽车对耐热性,耐湿性和抗振性的要求。
•HDI技术
汽车电子的关键功能之一在于娱乐和通信,其中智能手机和平板电脑需要HDI PCB.因此,HDI PCB中包含的技术(例如微孔钻孔和电镀以及层压定位)被应用在汽车PCB制造中。
到目前为止,随着汽车技术的迅速变化和汽车电子功能的不断升级,PCB的应用将成倍增加。对于工程师和PCB制造商,必须将注意力集中在新技术和新内容上,以便他们能够满足更高的汽车要求。
编辑:jq
-
pcb
+关注
关注
4318文章
23069浏览量
397096
原文标题:评估汽车PCB制造商可靠性的5种可靠方法
文章出处:【微信号:gh_ad43aef0e0b3,微信公众号:树根互联VS物联网VS数据应用】欢迎添加关注!文章转载请注明出处。
发布评论请先 登录
相关推荐
不同制造商TOPCon光伏组件的老化测试:性能、稳定性与可靠性
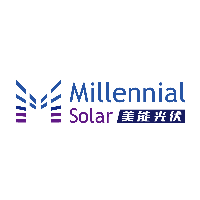
新思科技助力汽车制造商加速推进SDV开发
PCB高可靠性化要求与发展——PCB高可靠性的影响因素(上)
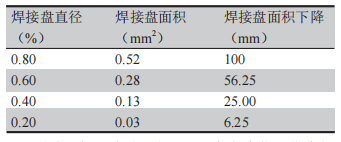
基于可靠性设计感知的EDA解决方案
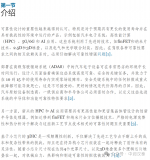
汽车功能安全与可靠性的关系
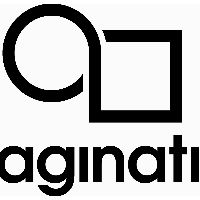
TIDA-00971.1-汽车负载短路可靠性和精确电流检测 PCB layout 设计
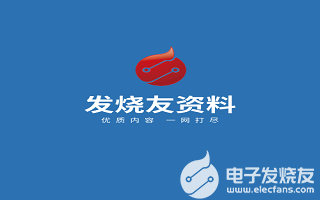
如何确保IGBT的产品可靠性
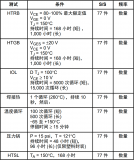
IGBT的可靠性测试方案

如何判断工业交换机的可靠性和稳定性?
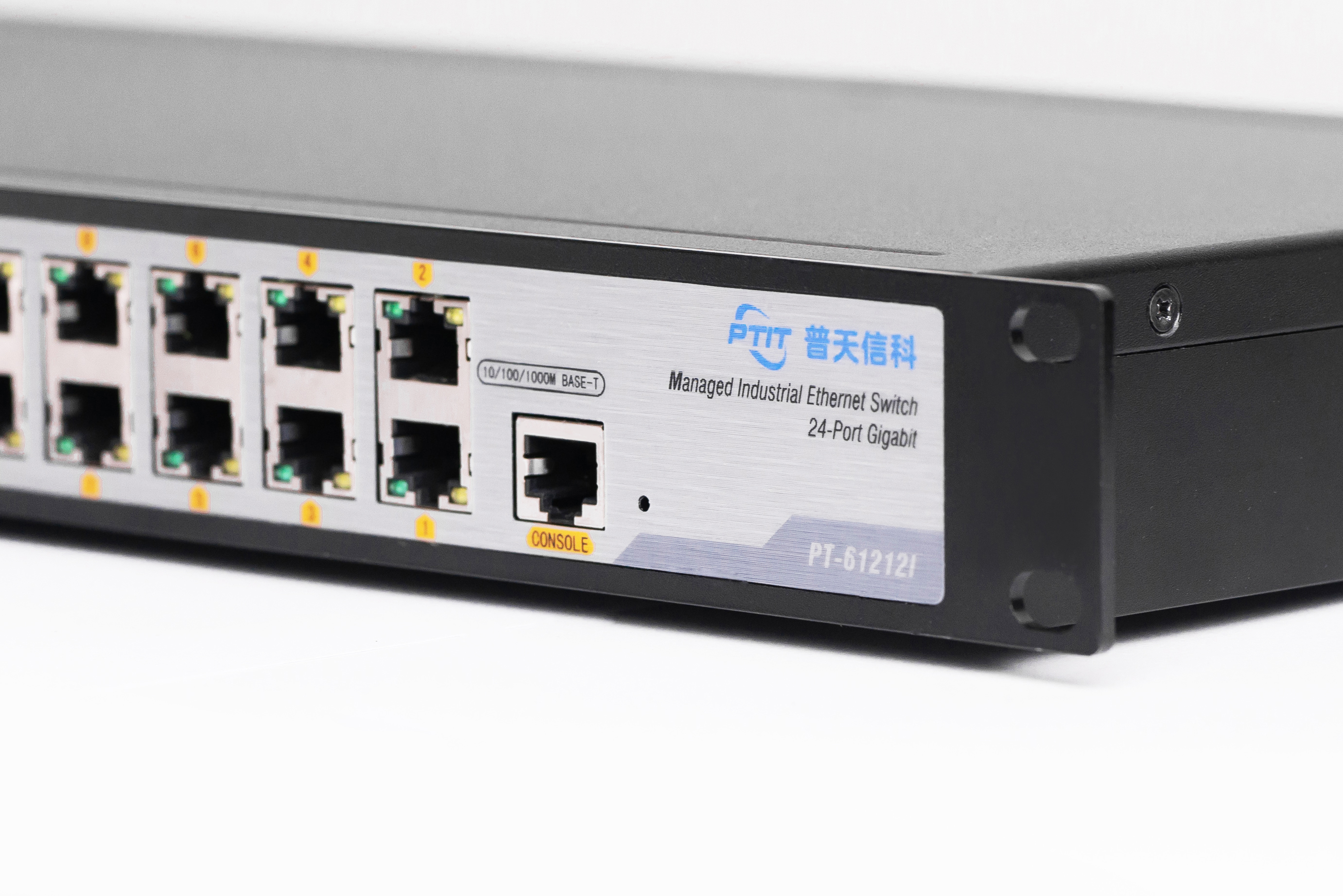
评论