在内燃机的各种损耗中,冷却损耗占比较大。因此,为改善燃烧室硬件并降低冷却损耗,研究人员做了大量研究及试验工作。提出了1种创新的隔热技术,克服了以往传统隔热技术的诸多弊端,并在内燃机中得以成功应用。对这项隔热技术及其涂层特性、验证结果进行了总结,并对其未来发展前景进行了探讨。
0 前言
_
为防止全球变暖,保护现有资源,近年来,各国改善汽车燃油经济性的呼声越来越高。为满足这一要求,电动车是1种非常不错的选择,但要将传统内燃机汽车完全换成纯电动车(EV)或燃料电池车(FCV),在成本或基础设施等方面仍有着较高要求。因此,最有希望的方案仍然是提高内燃机及内燃机与电机组合的混合动力车的效率。
作为一次动力源的内燃机,其内部损失一般包括:冷却损失(气缸壁热损失)、排气损失、机械损失、未燃燃气损失等几大类。图1示出了柴油机在高负荷和低负荷工况下的热平衡情况。如图1所示,在低负荷工况下,内燃机的机械损失占比较大;
在高负荷工况下,内燃机的排气损失占比较大。相较于这些损失对负荷的高依赖性,不论是在哪种负荷工况下,内燃机的冷却损失都占比较大。即使是在高负荷工况下,其冷却损失也达到了20%~30%。
图1 轿车增压柴油机热平衡情况示意图
研究人员总结了降低冷却损失的方法主要有:(1)降低传热系;(2)缩小燃烧室表面积;(3)降低做功燃气温度;(4)提高燃烧室壁温度。本文主要针对第4条,提高燃烧室壁表面温度,缩小其与燃气的温差,进而降低冷却损失的隔热结构进行研究介绍了这项技术过去的研究成果、现状及未来发展趋势。
1 早期研究
_
1978年,KAMO等人提出了隔热发动机的概念。这种概念的主要内容是利用高耐热陶瓷制造柴油机燃烧室,通过取消冷却功能来降低冷却损失,并利用涡轮回收增加的排气能量,将这一有用功返回动力输出轴,进而提高热效率(图2)。KAMO等人认为,由于取消了冷却机构,降低了冷却损失,因此发动机的燃油经济性预计可改善23%,动力装置可减少质量22%。该观点在当时获得了广泛关注。
根据KAMO等人的研究成果,全球汽车制造商都认为隔热发动机可有效改善燃油经济性,纷纷投入到研究开发的进程中,在当时形成了研究热潮。
但是,在当时研发出来的隔热发动机并没有完全实现降低冷却损失并提高热效率的目标。如图3所示,WOSCHNI等人利用耐热材料制成活塞燃烧室,并在其背面设置了气隙,形成了隔热结构。之后,WOSCHNI等人在实际发动机上进行了评估试验,得到了燃油经济性全面恶化的结果。
在高负荷工况下,活塞表面温度接近600 ℃,按照预期,燃气温度与燃烧室壁温度之间的温差应该缩小,冷却损失会减少,进而改善燃油经济性。但是WOSCHNI等人研究发现,此处的冷却损失几乎没有减少。
原因是高温活塞加热了进气行程中的新鲜空气,通过压缩、燃烧行程,工作循环中燃气温度升高,结果燃烧室壁温度与燃气温度温差并没有缩小,冷却损失也几乎没有减少。因此,“发动机燃烧室隔热弊端极大,没有任何益处”的说法几乎成了定论,相关的研究热潮也随之退去。
2 近年来的技术发展情况
_
2.1 新的隔热概念
1995年,WONG等人利用仿真方法改变了隔热涂层厚度及其热物理特性(散热率),燃油经济性也随之改变,因而得出了涂层厚度存在最佳值的结论。这一认知在现在看来是非常重要的发现,但是在当时并没有研究人员继续深入研究或展开应用的记录。
当时各国正处于因大气污染严重而迫切需要强化柴油机排放法规的时期,相关企业及高校把资源都集中在研究排气净化技术等方面。总之,在这之后的十几年间,有关发动机燃烧室隔热的文献只是零星出现,几乎处于被遗忘的状态。
在进入2000年后,随着柴油机颗粒过滤器(DPF)及选择性催化还原(SCR)等后处理系统逐步进入实用化阶段,相应的技术目标也日趋明了。为此需要在降低CO2排放的同时也能改善热效率,部分研究人员再次将过去的隔热发动机作为降低冷却损失的手段,并针对其技术瓶颈问题及解决手段展开了探讨。
如上所述,隔热发动机最大的问题在于高温燃烧室壁会加热进气。作为解决对策,研究人员提出了涂层概念,这是1种仅在燃烧、膨胀行程中使温度升高,而在排气、进气行程中可使燃烧室壁温度急剧下降,并且不会加热进气的方法。
为实现这一目,,研究人员需要找到1种不易导热、又极易实现升温及冷却的隔热材料。由于无法在短期内获得这样的材料,因此研究人员只能先利用仿真方法,对其使用情况及效果进行预测。
藤本等人为抑制伴随高压缩比化而增加的冷却损失,在燃烧室表面涂覆了1层1 mm厚的假想隔热材料,其传热系数及比热分别设置为铝的1/1 000~1/10,及1/100~1/10之间,并进行反复计算。
计算结果显示,热传递系数及比热越低,冷却损失降低效果越大。高压缩比提高循环效率及随之增加的冷却损失(机械损失)之间的平衡决定了最高效率压缩比。藤本等人发现,若想通过隔热来降低冷却损失,最高效率点就会向高压缩比侧偏移,其效率也可以得到改善。
小坂等人通过仿真方法计算了隔热涂层热物理特性,以及涂层厚度对燃烧室壁表面温度变化过程、发动机性能及热效率的影响,给出了应用这一概念时不同曲轴转角下燃气温度及燃烧室壁表面温度变化的情况。
这种隔热材料要求的热物理特性包括低传热系数、低体积比热。如表1及图5所示,小坂等人在增压柴油机活塞及气缸盖处涂覆了隔热涂层,并预测涂层厚度变化时温度的变化幅度及燃油经济性的改善情况。
在此计算条件下,研究人员发现涂层厚度为100 μm时,燃油经济性改善效果最明显。图6示出了基础金属气缸壁对进气加热的情况,给出了铝活塞选择合适隔热涂层厚度及涂层热物理特性后,可减少进气被加热的可能性,并推测出该方案也适用于汽油机。
2.2 隔热涂层材料的开发
为得到温度随燃烧室壁温度变化的隔热涂层,研究人员需要开发出可同时满足低导热率、低体积比热及高温强度的材料。脇坂、川口、西川等人研究开发出了铝合金“阳极氧化膜”。通常加工阳极氧化膜的目的是防腐及耐磨,其膜厚从几微米到十几微米不等,非常轻薄致密。
研究人员通过调整薄膜制备条件,将膜厚调整到了100 μm左右,成功得到了高达40%的孔隙率的材料。这种高孔隙率通过2种不同尺寸的孔隙实现,包括铝合金阳极氧化膜本身纳米尺寸孔隙的扩大,以及铸造铝合金中硅、铜等的结晶,以此妨碍阳极氧化膜主要成分铝的生长,进而得到了纳米级别的孔隙。
为了使该氧化膜可以承受柴油机200 MPa以上的高喷油压,,研究人员在阳极氧化膜表面涂覆了1层甲醛硅烷封孔剂,使之浸渗到孔隙中,并转化为SiO,从而可在提高强度的同时,防止高温高压燃气侵入涂层表面孔隙中。其结构示意图如图7所示。
这种温度可波动变化的隔热涂层材料被称为SiO2强化多孔阳极氧化膜(SiRPA)。该涂层的热物理特性如图8所示,其导热率为铝合金的1/100,体积比热为1/2,与以往隔热发动机所用的氮化硅(Si3N4)等耐热材料相比,性能有大幅提升。
2.3 在发动机上的应用
(1)在柴油机上的应用
2015年,丰田汽车公司将SiRPA作为温度波动变化隔热涂层材料,首次在量产发动机上进行了应用(图9),这一技术被称为“燃烧室壁温波动变化隔热技术(TSWIN)”。
如图10所示,在应用TSWIN 技术后,发动机冷却损失降低,净功率及排气损失增加,实现了燃烧室隔热的目的。
福井等人利用激光诱导荧光法测量了运行中发动机缸内隔热涂层的表面温度。在燃烧行程中,基础铝合金活塞表面温度在45 K左右波动,与此相比,SiRPA涂层可在140 K左右波动,呈现出随燃烧室壁温度波动的现象。
同时,福井等人确认了这一波动幅度与利用近似SiRPA涂层热物理特性进行的仿真预测结果大致一致(图11)。测量值包括了从极限测量值到发动机中等负荷运行工况值,在高负荷工况下波动可达到200 K左右。
(2)在汽油机上的应用
山下等人通过在汽油机活塞顶部采用恰当厚度的多孔阳极氧化膜,在发动机性能及敲缸都没有恶化的情况下改善了燃油经济性。此时,燃油经济性改善最大的区域为汽油机燃油经济性的最佳点,即与中高速负荷工况基本一致,非常适合较多在这一工况下运行的混合动力车型。本技术在2020年普锐斯发动机中得到了应用并开始量产。
(3)与壁温波动隔热的应用
从发动机缸内燃气与燃烧室壁温变化及热传递的观点来看,20世纪80年代的“隔热发动机”与其说是隔热,不如说是“耐热材料发动机高温运行”更为贴切。“隔热”一词意味着隔断热的传递,而当时的“隔热发动机”在进气行程中,由高温燃烧室壁将大量的热量传递给了进气。
在燃烧行程中,相对于数百摄氏度的燃烧室壁,通常温度为数千摄氏度的燃气会使进气高温化,由于温差非常大,这与常规发动机流失热量几乎相同,因此这种发动机绝对不能称为“隔热发动机”。
对燃烧室壁温度波动隔热而言,且不论隔热率大小,在进气行程或燃烧行程中,燃烧室壁温度都会跟随燃气温度进行变化,温差缩小,传热量也会减少,这与“隔热”定义的“不输出热,也不接收热”更为贴近。
3 燃烧室隔热技术未来展望
_
燃烧室内壁温度波动隔热技术是近年前获得的实用化技术,其应用效果与概念计算预测的效果相比,仍然差距较大。今后的研究须在以下几方面展开:(1)开发更高性能的隔热涂层材料;(2)扩大燃烧室隔热范围,优化隔热部位;(3)明确燃气与各种燃烧室壁表面特性之间的热传递机理。
在此期待各国研究人员能针对上述3方面应用场景对燃烧室壁隔热技术进行持续优化,并改善其应用效果。特别是第3方面,需要产业界和学术界的研究人员共同努力,加速低冷却损失燃烧技术的开发进程,为进一步提高内燃机效率作出贡献。
编辑:jq
-
发动机
+关注
关注
33文章
2470浏览量
69259 -
内燃机
+关注
关注
1文章
158浏览量
21446 -
气缸
+关注
关注
2文章
53浏览量
13566
原文标题:干货 | 发动机燃烧室隔热技术的发展与展望
文章出处:【微信号:汽车与新动力,微信公众号:汽车与新动力】欢迎添加关注!文章转载请注明出处。
发布评论请先 登录
相关推荐
航空领域发动机传感器的应用
ECU与发动机噪音的关系
全柴发动机和云内发动机哪个好
直喷发动机的优缺点有哪些
电控发动机的优点与工作原理
发动机电子控制系统的优点有哪些?
汽车发动机上的电控技术主要包括什么
使用KURO高性能sCMOS相机进行燃烧气体的高光谱和多维CARS测量
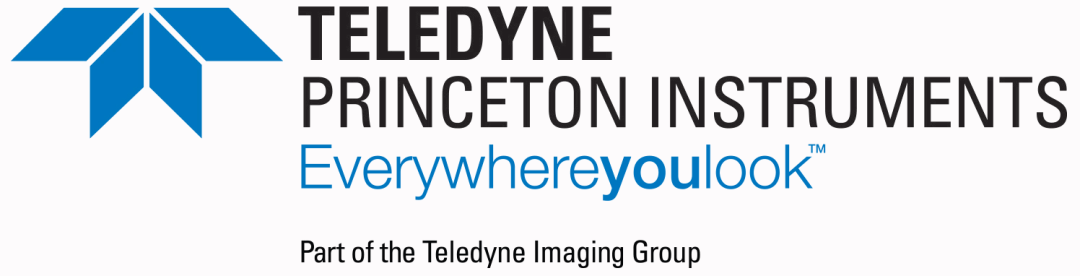
提升发动机热效率的方法有哪些?
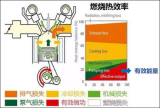
发动机故障灯亮是什么原因 发动机故障灯闪烁是什么问题
发动机故障灯亮是什么原因 发动机管理系统主要由哪三个组成
飞机发动机盘点:飞机发动机类型有哪几种
发动机内部构造解析
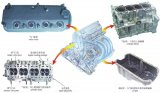
汽车发动机:六冲程发动机工作原理
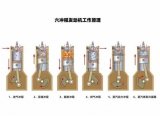
评论