随着大屏多屏的应用发展趋势,触感好、光学性能优异的玻璃盖板更能展现一种高级感,现已成为车载显示盖板材质的主流选择之一,市场前景广阔。
从近年的各车展或是全触展等大型展览会现场我们可以看到,曲面显示屏具有更好的设计性,整体观感更酷炫等极大优势,未来几年,相关产品的应用与出货或将稳定增长。今天我们就来简单聊聊车载显示3D玻璃盖板。
3D玻璃盖板的优势
延锋XIM21 概念车中的曲面显示屏,截取自延锋官网 目前的车载显示屏之所以采用曲面设计,其实不仅仅是酷炫好看,更是有着其存在的独特意义所在: 1.设计自由度的提升。对于设计师来说,曲面的屏幕能够更好的实现设计想法,且更具设计感与科技感。2.OLED、Micro LED、mini LED等应用将推动曲面屏发展。未来车内,3D柔性显示屏将越来越多3.更符合人体工程学。3D曲面屏幕可实现更好的显示效果4.辅助提升触觉反馈。曲面的变化能辅助带来触觉反馈
三种3D玻璃成型工艺
3D玻璃成型最早应该是从日本起源,后经韩国发展,再到国内。小编通过艾邦粉丝了解到,目前车载显示玻璃盖板的加工有三种工艺:康宁的冷弯贴合工艺、用于手机盖板加工的热弯(热压工艺,代表旭硝子)、之前用于家电领域的热弯(传统热弯,利用玻璃自重成型,代表:旭信达等)。 目前来看,这三种工艺各有优劣,而目前3D玻璃盖板的应用也基本都处在打样阶段,最终哪种工艺将会胜出,还是一个未知数。下面,小编带大家一起来简单了解下这三种工艺。 01 传统热弯工艺 这种成型工艺是由用于电视机、大尺寸电脑显示屏等产品玻璃盖板加工的工艺转到车载显示盖板成型上。
通过将玻璃加热到接近融化(6-700℃),利用玻璃自重,玻璃在长时间的软化后贴覆在模具上,再通过冷却固化处理即可得到3D玻璃。 整体工艺大致如下:
优势:由于是利用玻璃自重成型,产品不受外力明显作用,因此表面光滑,CNC无需进行抛光处理。制程相对缩短,良率会有提升。另外在热弯过程中,会在一定温度恒温一定时间,让玻璃内应力充分释放,确保玻璃不会自爆; 缺点:产品升温/冷却周期长,整个成型周期持续数小时,生产效率有限。适合小批量生产。 02 热压成型 热压工艺目前在手机盖板加工上面已经非常成熟,但由于车载显示相较于手机盖板尺寸更大,设备投入大、工艺成熟度不足。
热压工艺是通过将玻璃加热到软化点(6~700℃),产品放入光滑模具内,通过上模具向玻璃施加作用力使其弯曲成型,然后经过冷却后固定形状。 整体工艺大致如下:
优点:成型周期短,具有更高的成型效率,基本上在6-7min即可完成一个循环。这一技术适用于大规模量产。 缺点:由于是通过压力使其成型,因此产品表面一般会留下模印,需要经过抛光处理才能达到产品要求。
进阶:热吸工艺
目前热压成型的一大难点就是要针对模印进行抛光,因此,厂商在此热压的基础上升级工艺,以减轻甚至消除这一问题,热吸工艺由此应运而生。
热吸工艺,是当玻璃加热至软化点后,通过下模具抽真空将玻璃吸在模具上,最终贴合模具形态成型。整个过程中产品不会受到上模具的压应力,因此,最终产品将会消减模印。热吸工艺作为热压的一种升级工艺,正在验证之中。
03 冷弯工艺(ColdForm)
京东方精电联合康宁开发曲面显示解决方案 冷弯贴合(cold form)工艺是由康宁提出的工艺。顾名思义,即实现汽车内饰显示玻璃在室温下弯曲成型,无需传统的热成型工序。这一工艺是利用康宁大猩猩玻璃超薄、高韧性的性能优势,直接通过机械力作用使其弯曲,后经过贴合胶水固化而固定在产品表面。具体流程大致如以下:
简单点说,就是将做好各种处理的超薄玻璃通过外力,最终3D贴合在产品表面。 优势:与热成型工艺相比,极大的减少了加工流程,同时还提升了加工良率; 劣势:冷弯的核心在于超薄、高韧性的玻璃,这种高性能玻璃的成本一般较高;另外玻璃非永久变形。 除康宁外,国内电子玻璃的领先企业中国南玻集团,也开发除了这种超薄高韧性、可用于冷弯加工的玻璃。
以下是,识别南玻集团对其化学冷弯玻璃的介绍: 化学冷弯玻璃 化学冷弯是一种在常温条件实现玻璃弯曲的技术,其曲率半径R能够达到600-4000mm,可加工成“C型”、“V型”、“S型”、“U型”和“W型”。相比热弯工艺相,化学冷弯生产成本更低,表面品质更好,无应力集中现象。 化学冷弯玻璃适用于中大尺寸曲率玻璃的成型。化学冷弯玻璃可以和抗菌功能,AG功能有机结合,可应用于车载显示盖板、汽车用玻璃、曲面电视和曲面显示器等。
对比 下面根据小编收集到的信息,这里从原料、技术、整体工艺来对这三种工艺进行简单对比:
对比项目 | 传统热弯 | 热压 | 冷弯(coldform) |
成型温度(℃) | 600~700 | 600~700℃ | 室温 |
原材料 | 高铝玻璃 | 高铝玻璃 | 超薄、高韧性玻璃 |
设备尺寸 | 最大 | 大 | 小 |
设备成本 | 较高 | 高 | 小 |
成型周期 | 3H/24片(根据尺寸,每次成型数量会有变化) | 6~7min/片 | 用时最短 |
良率 | 高 | 一般 | 高 |
工艺难点 | 1.黄光工艺 2.镀膜难(AR) 3.曲率小 | 1.抛光处理 2.黄光工艺 3.镀膜难(AR) | 依靠贴合胶水粘接固定形变,玻璃非永久变形等 |
小结:
1、现有应用于车载显示屏市场的3D玻璃盖板一遍是一些简单形状,如C型、V型、Z型。一方面,这是受限于玻璃加工的成本及良率,而另一方面,曲面盖板的贴合加工难度也会极大的限制复杂形状3D显示屏的规模性应用。
2、当下车载显示3D玻璃的生产工艺其实各有优劣,并不能简单的说今后工艺走向如何。综合考虑成本与品质、效率,是大部分主机厂的惯有逻辑。
3、除了工艺上的研发门槛,在车载显示3D玻璃盖板的生产中,热压、热弯都需要极大的设备等硬件方面的投入;而冷弯则会受制于玻璃厂家。因此,目前业界有做车载3D盖板生产的厂家还是少数,且一般都实力较强。
审核编辑 :李倩
-
车载显示
+关注
关注
1文章
101浏览量
20839 -
3D玻璃
+关注
关注
5文章
58浏览量
11598
原文标题:车载显示3D玻璃盖板三种成型工艺介绍
文章出处:【微信号:ZHISHIKU-Pro,微信公众号:知识酷Pro】欢迎添加关注!文章转载请注明出处。
发布评论请先 登录
相关推荐
SLA立体光固化成型:一项实现3D打印领域高精度数字模型实体化的先锋技术
TGV玻璃基板主流工艺详解
3D封装玻璃通孔技术的开发
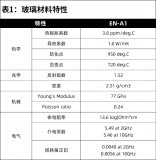
韩国JNTC为三家芯片封装企业供应新型TGV玻璃基板
物联网行业中3D打印工艺——SLA(立体光固化成型技术)
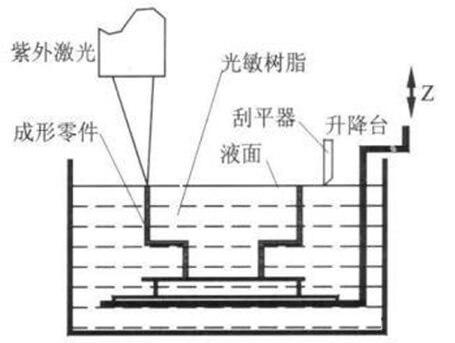
物联网行业中3D打印工艺——FDM(熔融沉积成型技术)工艺
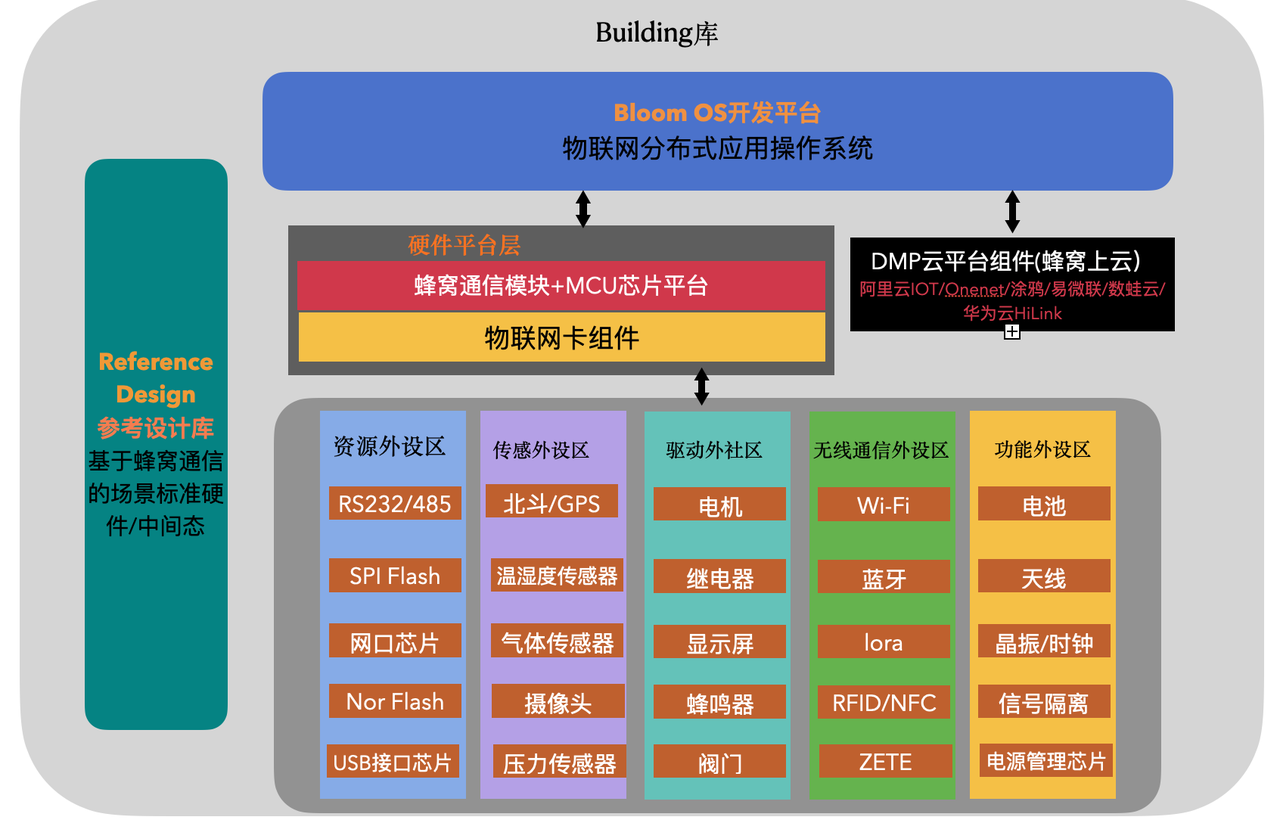
评论