最近,热评估已成为电源管理系统中的热门话题。随着许多应用对功率要求的提高,应考虑热管理以避免过热。尤其是在芯片中集成了功率MOSFET的DC-DC转换器产品,其功耗面临着封装尺寸和PCB布局面积有限的挑战。因此,热评估应包含在项目预览中。Flotherm 是一款专业的热模拟工具,用于模拟热系统的真实情况,有助于减少不必要的试错过程成本。在本应用笔记中,将讨论电源管理系统热模型的建模和验证。
1. IC 热模型建模
根据不同的应用和要求,有多种 IC 封装。封装尺寸、结构、材料、裸片尺寸和功耗曲线等几个参数都会影响 IC 的热阻。一般这些参数可以由IC产品工程师(PE)提供,根据上述参数开发热模型。以下是一些适用于 DC-DC 降压转换器和 PMIC 的常见 IC 封装。
1. 不同类型的 IC 封装
图2. 热模型构建示例
图 2 是安装在 PCB 上的芯片的热模型构建示例。IC 的热模型由 die、die attach、lead-frame die pad 和焊膏组成,它们各自具有不同的热导率,这取决于它们的材料。一般管芯的材料是硅,其电导率为117.5 W/(K·m)。其他材料特性例如可以参考下表1。导热系数可能会随着不同的材料而变化。请注意,物体的(绝对)热阻(以 K/W 为单位)取决于热导率、热路径的长度和横截面:
其中 θ 是绝对热阻,Δl 是热路径的长度, A 是热路径的横截面积,k 是材料的热导率。
表 1. IC 热模型的热导率
2. 电感热模型建模
除 IC 外,电感可以看作是开关电源变换器系统中的第二大热源。因此,电感热模型的开发是必不可少的。与 IC 的模型类似,建立准确的电感器热模型需要一些信息。首先,我们可以在数据表中找到电感的外形尺寸,包括长度、宽度和高度(见图 3)。其次,由于外部障碍,内部结构是不可见的。有两种方法可以获取所需的参数。一种是拆掉电感,测量内部布线配置,如线材粗细、匝数等。另一种更温和的方法是向电感器制造商询问信息。然后您可以按照信息建立电感器的热模型,如图 4 和图 5。
图3. 电感器外形尺寸
图 4. 制造商提供的电感器内部结构
图5. Flotherm 开发的电感器热模型
电感材料的导热系数如表 2 所示。需要注意的是,大部分热量会通过铜线传递到外部电源走线。这是因为铜的热导率高于铁氧体,所以大部分热量会通过热导率最高的路径流动。
表2. 电感热模型的热导率
3. PCB热模型建模
在对主要热发生器(IC 和电感器)进行建模后,下一步是开发散热器。在大多数使用 SMD 组件的电源转换器中,PCB 对功耗起着重要作用。传热有三种方式:传导、对流和辐射。当产生温差时,热量将开始从高温区向低温区流动。大多数热量将选择热阻最小的路径,即通过焊料到铜的 PCB 传导。图 6 显示了安装在 PCB 上的 IC 的热阻网络示例。
图6. 热阻网络示例
花一些时间在 PCB 布局安排上是至关重要的。一般来说,PCB走 线越宽越厚,热阻越小。但是,如果 IC 封装尺寸较小,PCB 走线宽度也会受到限制。在传热和布局规则之间会有一个权衡。例如,开关节点的 PCB 走线应始终足够大以维持电流,但也应足够小以减少噪声耦合。在具有多层设计的 PCB 中添加热通孔是改善热传递的一种解决方案。在 Flotherm 仿真工具中,建议将圆形 Vias 转换为矩形 Vias,以减少收敛周期。使用公式(1)和(2)来完成转换很简单。图 7 演示了转换示意图。
图7. 圆形过孔到矩形过孔的转换
4. 电源管理系统热模型验证
建立每个组件的热模型后,就可以进行台架测试以验证热模型的准确性。验证分为两个步骤。第一步是一次只用一个热源检查每个组件的准确性。第二步是使用热模型检查整个电源管理系统的准确性。
图 8 给出了 RT6228 的 IC 热模型。RT6228 是一款 HV 单 Buck 转换器,封装类型为 UQFN-12HL 3x3-56B (FC)。倒装芯片的设计可以降低引线键合阻抗以提高效率,同时也会降低芯片到IC引脚的热阻。需要注意的是,IC 热模型的发热区域将位于内部功率 MOSFET 的区域。在这种情况下,发热区域位于芯片的下半部分。如果一个芯片中有多个导轨,比如 PMIC,就会有多个热源。在这种情况下,应根据每个导轨的位置将加热区域分开。
图8. RT6228 的 IC 热模型
RT6228 EVB 的热模型如图 9 所示。热模型的布局是根据实际 EVB 完成的(图 9 左侧)。它是 1oz 四层设计,EVB 尺寸为 100mm x 72mm。许多热通孔放置在 IC GND 和 VIN 平面中,以改善向其他层的热传递。由于电源层和接地层是影响热传递的主要因素,因此可以在 PCB 热模型中简化其他控制回路走线。
图9. PCB 的热模型
由于IC在没有外部元件的情况下无法工作,因此芯片上产生的热源是一个问题。另一种方法是通过内部功率 MOSFET 的体二极管注入恒定电流。为了确认不同功耗下热模型的准确性,有三种不同级别的注入电流来加热芯片。表 3 显示了 IC 热模型的验证结果,以及仿真和实验的外壳温度比较。本实验中,电流注入高边MOSFET的体二极管产生功率耗散,环境温度约为25°C。结果表明,仿真与实验之间只有2%的温度偏差。
表3. IC 热模型验证
电感器热测量如下所示。与IC热模型验证类似,电感放置在PCB上,发热源为电感铜线。功率耗散是由电感绕组的 DCR 通过将电流注入导线而产生的。电感器的功率损耗可以通过将电感器两侧的差分电压乘以注入电流来计算。最后验证结果如表4所示,测量与仿真的温度偏差在3%左右。
表4. 电感热模型验证
此外,以下是使用热像仪 (Fluke Ti450) 测量电感器外壳温度时需要注意的一些技巧。由于电感封装的反射系数高于IC封装,因此IR测量会不准确。为了降低电感的反射系数,在电感表面贴一块黑色电工胶带,有助于提高发射率。图 10 是电感温度测量的示例。EVB放置在密封箱内,用于静止空气状态,热耦合器用于监测箱内环境温度。使用热像仪进行测量时,正确调整焦距对精度至关重要。此外,在每个测试条件下等待热平衡至少 15 分钟。
图10. 电感温度测量的实验设置
在前面的步骤中,验证了每个组件的热模型精度。在下一步中,所有这些组件将被组合起来,以确认完整的电源管理系统。通过调整输出反馈电阻,RT6228 可支持 0.6V 至 5V 的输出电压。为了验证不同功耗的热模型,有两个实验案例来验证热模型。详细的仿真和实验参数列于表 5 和表 6。在每个测试条件下,功耗被分为三个分量:IC 的功耗、电感的功耗和 PCB 走线的功耗。因此,仿真设置将取决于功耗的分布。此外,所有情况都是在 25°C 的环境温度下完成的。仿真和实验结果如图 11 和图 12 所示。对于案例 1,输出电压为 3.3V,负载条件为 6A。IC的功率损耗,PD_IC为 1.73W,电感器的功率损耗 P D_L为 0.93W,PCB 的功率损耗 P D_PCB为 0.3W。电感的功率损耗包括铜损和磁芯损耗,其中铜损通过I L 2 xDCR 计算,磁芯损耗可以在电感制造商的数据表中找到。在这种情况下,电感器 DCR 为3.3m W,铁损约为 0.81W。PCB的功率损耗通过I PCB 2 xR PCB计算,其中PCB走线电阻可分为两部分:一是输入电容到VIN管脚的走线电阻,约为4m W, 另一个是 SW 脚到输出电容的走线电阻,大约8m W。然后根据 (P D_IC = P D_TOTAL – P D_L – P D_PCB )计算 IC 功率损耗。仿真结果与实测实验结果对比,IC外壳温度几乎相同,电感温度偏差小于5%。对于案例 2,输出电压为 1V,负载条件为 6A。IC 的功率损耗 P D_IC为 1.53W,电感器的功率损耗 P D_L为 0.286W,PCB 的功率损耗 P D_PCB为 0.3W。在这种情况下,电感器 DCR 为 3.3m W铁损约为0.167W。PCB 走线电阻与案例 1 中的相同。仿真结果与实验结果对比,IC外壳温度偏差仅为2%,电感温度偏差小于5%。
表5 案例一的仿真和实验参数
图11. 案例 1 的仿真和实验结果
表6 案例 2 的仿真和实验参数
图12 案例 2 的仿真和实验结果
五、总结
在本应用笔记中,对电源管理系统热模型的建模和验证进行了说明。报告中描述了 IC、电感器和 PCB 热模型的开发。验证结果显示仿真和测量之间的偏差很小。最后,通过精确的热模型仿真,可以预测应用的热行为,防止过热等热问题。这将有利于缩短开发时间并避免因反复试验而产生的额外成本。
-
建模
+关注
关注
1文章
313浏览量
60931 -
电源管理系统
+关注
关注
0文章
59浏览量
16461
发布评论请先 登录
相关推荐
IGBT模块及散热系统的等效热路模型
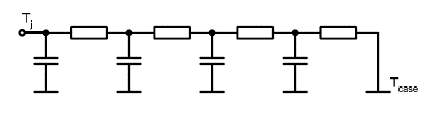
评论