5月5日,《自然》期刊发表一项氮化镓单晶的激光减薄新技术,其作者包括诺贝尔得主天野浩。
据介绍,该技术可以将氮化镓衬底产能提升3倍,同时可以省去衬底抛光工艺,因此有助于帮助降低氮化镓单晶器件制造成本,该技术也有望应用于碳化硅单晶切割。
根据文献,名古屋大学和日本国家材料科学研究所等组成的研究团队,新开发了一种 GaN衬底减薄技术——激光减薄技术。
此前,他们已证明可以用激光对GaN单晶进行切割,且切割后的GaN衬底经过抛光可以重复使用。
而此次他们通过实验证明,该技术同样适用于GaN-on-GaN HEMT器件制造,即在器件制造之后采用激光工艺进行减薄,该技术可显著降低 GaN 衬底的消耗。
损耗大 良率低 传统技术局限多多
众所周知,GaN是一种十分理想的制作功率器件的材料。但是,GaN衬底价格昂贵,在GaN衬底上制造的 GaN 基器件尚未在广泛的领域实现商业化。因此,为了尽可能地减少昂贵的GaN衬底的消耗,衬底切片越薄越多,良率越高,是切割技术所追求的目标。
但是传统的技术却有着诸多局限。
首先,损耗大。传统技术无法避免切片过程中的切口损耗,且衬底面无法抛光重复使用,需耗损较多的GaN衬底来能得到一个器件层。
再者,良率低。传统技术的一般流程是先切片,再键合相应的晶体,才能进行后续制造。那么则需考虑键合器件层等一系列问题,如化学和热效应等。而在此过程中,增加了出现次品的可能性。
传统技术绝大部分都是先在GaN晶体上切割出GaN衬底,再从衬底中进行切片,以进行后续制造。但不可避免的,会造成较大耗损及良率低下的问题。
以前,每400微米厚的GaN衬底只制作一个器件层。
新技术: 减少300%GaN衬底耗损
为突破上述技术的局限性,该研究团队新开发了一种基于激光技术的减薄GaN衬底的方法,可以最大限度地减少昂贵的GaN衬底的消耗,每100微米厚的GaN衬底可以制作一个器件层,相比以往减少了300%的损耗。
该技术已被证明可以在器件制造之后进行减薄,实验过程中被减薄的器件没有观察到明显的断裂,也没有观察到对电气特性的不利影响。
这项技术还有一个值得注意的亮点:器件制造后进行减薄,所消耗的GaN衬底的量将仅为切片器件层的厚度,并可以通过抛光去除以重新使用。换句话说,使用该新技术有望实现GaN衬底0耗损!
此外,在器件制造后进行减薄,也更便于获得薄型GaN层。器件越薄、散热越好,性能也就更优越。
文献中提及,该新技术和传统的Smart Cut技术有相似之处,Smart Cut技术采用的是离子注入法切割,可切割出亚微米厚度的非常薄的GaN层。但激光切割技术很难切出如此薄的GaN层,因为GaN在激光切割过程中会被分解。 为此,该团队开创了背面激光照射法来剥离器件层。
实验结果表示,通过激光技术将GaN-on-GaN HEMT减薄至50 μm厚度,其仍可以正常工作,切片前后器件的电特性变化不大。这意味着即使在器件制造之后也可以应用激光减薄工艺。它还可以用作半导体工艺,用于制造厚度约为10 μm的薄器件,而无需抛光GaN衬底。
审核编辑 :李倩
-
晶体
+关注
关注
2文章
1339浏览量
35364 -
功率器件
+关注
关注
41文章
1727浏览量
90304 -
GaN
+关注
关注
19文章
1917浏览量
72940
原文标题:产能提升300%,GaN又有新技术
文章出处:【微信号:SiC_GaN,微信公众号:行家说三代半】欢迎添加关注!文章转载请注明出处。
发布评论请先 登录
相关推荐
公共建筑、大型物业能耗在线监测系统,助力能源减排减碳
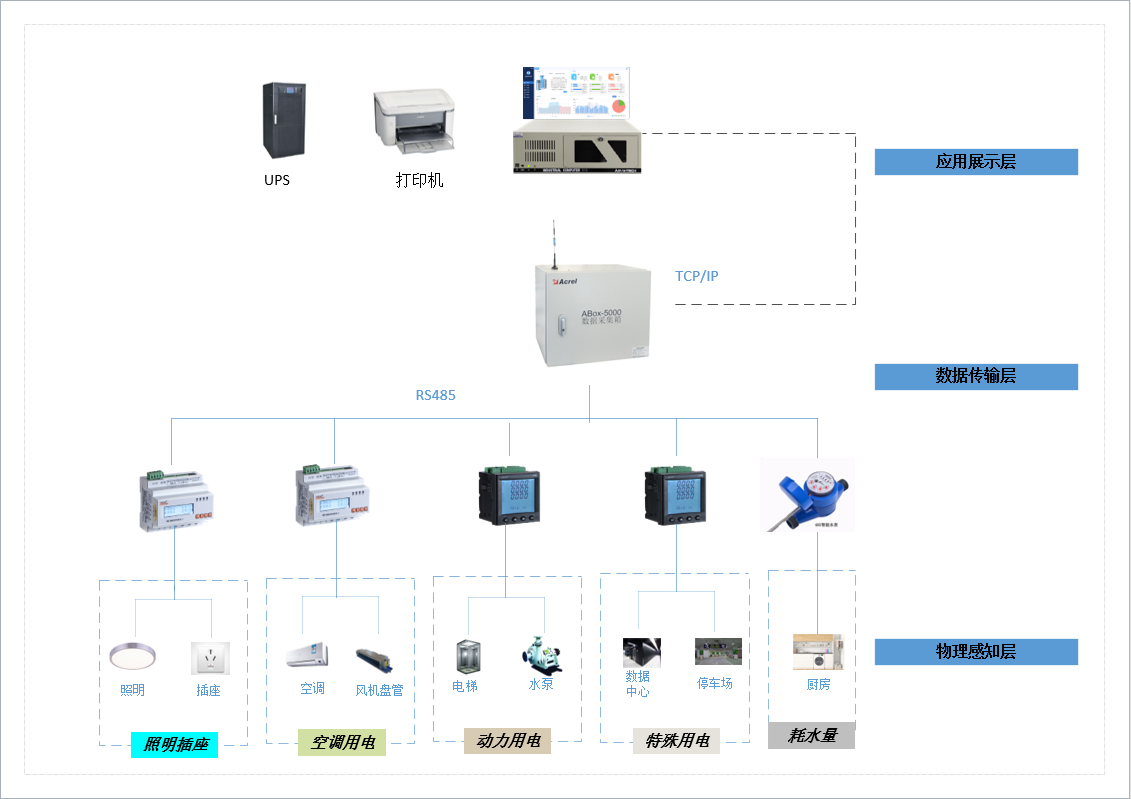
芯丰精密第二台12寸超精密晶圆减薄机成功交付
光学减反膜的工作原理和制作工艺
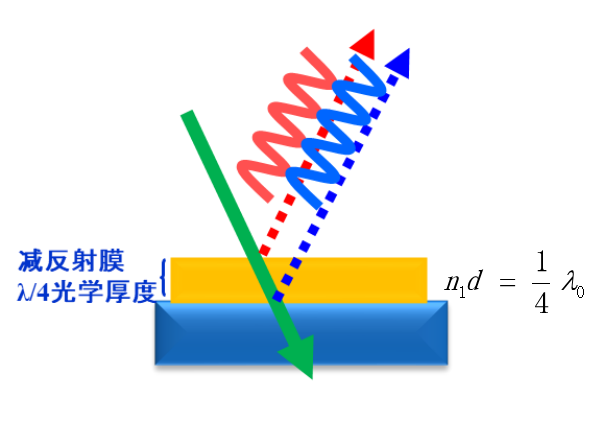
一种供电总线技术POWERBUS二总线
荣耀引领折叠屏轻薄革命:青海湖电池技术再突破
激光全息无损检测技术原理以及应用
吉利控股减持沃尔沃股份,仍掌握重要股权
韩国研究团队开发了一种在石墨烯层上生长柔性GaN LED阵列的方法
韩国开发了一种在石墨烯层上生长柔性GaN LED阵列的方法
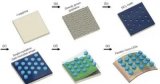
评论