直线振动筛激振器轴承座的紧固安装方式改造实践
激振器松动问题导致振动筛故障频繁,而激振器轴承座的安装缺陷又使日常的检查与维修工作强度和难度增大,进而制约了整个生产系统的正常运行。
本文以某选矿厂生产线中的振动筛为例,讨论激振器轴承座的紧固方式。
1、激振器轴承座问题分析
1.1 激振器轴承座的安装方式
该生产线中直线振动筛振幅为8~11mm,工作频率为16Hz,驱动电机功率11~22kW,转速970r/min。该筛机采用双电机自同步原理驱动,驱动电机通过强力型胶带联轴器(软连接)直接驱动装在筛机侧帮板上的激振器(图1),使筛机工作运转。
激振器轴承座5按照图2中的安装方向,穿过开在振动筛侧帮板1、3上的安装孔后,把激振器轴承座压盘7套装在图2相应位置;转动激振器轴承座及压盘,使其标记孔与振动筛侧帮板的标记孔相对应,而后绞孔螺丝4先后穿过激振器轴承座绞孔、振动筛侧帮板绞孔和激振器轴承座压盘绞孔。
然后紧固螺栓,使激振器轴承座安装法兰及激振器轴承座压盘贴于振动筛侧帮板的内外两表面;继续加大螺栓的紧固力矩,使激振器轴承座与压盘紧紧地夹住振动筛侧帮板,从而使激振器轴承座安装固定在振动筛侧帮板上;最后,安装激振器偏心块和护罩,直至完成振动筛激振器的整体安装工作。
1.2 存在的问题分析
振动筛在生产过程中始终处于振动状态,因此振动筛筛体上的各安装部件易发生松动,如激振器轴承座、激振器防护罩、筛板等,其中激振器作为振动筛的振源,其紧固螺栓更容易发生松动。
该紧固螺栓位于激振器防护罩内部,筛机停时,单凭眼观是无法判断其是否松动的,但是进行接触性检查就必须费工、费时地进行激振器护罩拆卸和安装工作;筛机运转时,更无法观察,只能根据筛机振动情况和声音来判断是否发生松动。
由于松动发现滞后严重,因此一旦松动现象发生,轻则停机紧固处理影响当班生产,重则导致激振器轴承座及压盘绞孔研磨受损严重必须更换,或使振动筛侧帮板上的受损绞孔很难修复,由于振动筛侧帮板一般无法更换,因此修复后安装的激振器无法恢复到原安装状态,更容易发生松动。螺栓松动不能及时发现,导致激振器轴承座的紧固和松动处理难度增大。
上述安装方式采用绞孔螺栓紧固连接,对激振器轴承座起到定位和紧固作用。但在实际使用过程中,安装紧固螺栓松动时有发生,分析其主要原因有:
(1)激振器轴承座的外径与振动筛侧帮板上的安装孔内径间隙大,径向尺寸3~4mm,形成了惯性振动距离。
(2)激振器在振动筛运转过程中,始终处于振动状态,特别是在筛机启动、停止时,瞬间驱动力矩和振幅加大,增大了激振器轴承座紧固螺栓的承载负荷。
(3)激振器安装后,偏心块和轴承座紧固螺栓处于安全护罩内,日常检查维护不便。
2、解决方案
针对以上问题,该选矿厂制订了如下解决方案:
首先,将激振器轴承座准确定位安装,然后,将自制的定位子台焊接在振动筛侧帮板上,子台横截面以20mm×20mm为宜,子台与被定位件间隙以0.3~0.5mm为宜。这样,绞孔螺栓主要起到螺栓的轴向紧固作用,定位子台则起到控制轴承座径向跳动的作用,从而实现了对激振器轴承座的轴向、径向双约束。
所使用的定位子台选用35优质碳素钢板,车削加工成圆环状。加工时,圆环内径尺寸应大于轴承座及压盘外径尺寸0.3~0.5mm,以使其在安装时形成间隙配合方式,而圆环断面尺寸可根据轴承座及压盘的外径尺寸和厚度尺寸确定。该选矿厂激振器轴承座及压盘外径600mm,厚度40mm,因此确定子台横截面尺寸为20mm×20mm。
该技改方案施工简单,一台激振器可在1h内完成。施工时,将准备好的圆环套装在已安装好的激振器轴承座及压盘的外径,使用塞尺确保其与轴承座及压盘同轴度,同时确保圆环轴向端面与振动筛侧帮板紧密接触,这样圆环的外径面与振动筛侧帮板面就形成一个焊角,便于施焊和确保焊接强度,内径面便成为激振器轴承座的安装子台。
3、实施效果
采用上述方案对激振器轴承座进行改造后,生产实践表明,该方式有效延缓了轴承座紧固螺栓松动现象的发生:原绞孔受损的激振器轴承座及压盘按技改方式安装后,激振器的紧固螺栓松动发生时间由技改前的一周左右延长到3~6个月。
而绞孔未受损的轴承座通过加装定位子台可使螺栓紧固的时间长达一年,大大减少了设备维护与检修量,从而确保生产的正常运行。并且,该技改方案成本低廉,实施简便,可有效地防止振动筛激振器发生松动现象,同时也为该厂其他振动设备部件的紧固提供了一个解决思路。
正确适当拆卸振动筛轴承
不当的拆卸振动筛轴承,可能造成轴承内部的损坏。污染物可能进入轴承或再安装时可能产生的错误。因此,拆卸振动筛轴承必须十分小心,轴心必须有适当的支撑,否则拆卸力量可能伤及轴承。
1、外圈的拆卸
拆卸过盈配合的外圈,事先在外壳的圆周上设置几处外圈挤压螺杆用螺丝,一面均等地拧紧螺杆.一边拆卸.这些螺杆孔平常盖上盲塞,振动筛圆锥滚子轴承等的分离型轴承,在外壳挡肩上设置几处切口,使用垫块,用压力机拆卸,或轻轻敲打着拆卸。
2、振动筛圆柱孔轴承的拆卸
内圈的拆卸,可以用压力机械拔出最新简单。此时,要注意让内圈承受其拔力。
大型振动筛轴承的内圈拆卸采用油压法。通过设置在轴上的油孔加以油压,以使易于拉拔。宽度大的轴承则油压法与拉拔卡具并用,进行拆卸作业。
NU型、NJ型圆柱滚子振动筛轴承的内圈拆卸可以利用感应加热法。在短时间内加热局部,使内圈膨胀后拉拔的方法。
3、锥孔轴承的拆卸
拆卸比较小型的带紧定套轴承,用紧固在轴上的档块支撑内圈,将螺母转回几次。
(运转世界大国龙腾 龙出东方 腾达天下 龙腾三类调心滚子轴承 刘兴邦CA CC E MB MA)
振动筛激振器轴承频繁损坏,从这3个方面找原因
振动筛激振器轴承频繁损坏,从这3个方面找原因
1设计原因
1)轴承选型不合理。
振动筛滚动轴承在工作过程中由入料带来的冲击载荷较大,由偏心块高速旋转产生的离心力及离心加速度也较大,加之工作环境中粉尘较多,所以对轴承的使用类型、极限转速、安装配合尺寸、游隙、自润滑性能等要求较高,普通轴承在此恶劣工况下工作易损坏。如果设计初期对轴承选型不当,轴承使用寿命就会较短。
处理方法:
选用振动筛专用轴承。常用的振动筛轴承一般有圆柱滚子轴承和调心滚子轴承2种形式。圆柱滚子轴承具有较大的径向承载能力,承受极限转速也较高,对动静载荷的承载能力强,但对轴承座孔的同轴度要求较高。
调心滚子轴承不但具有较大的径向承载能力,而且能承受任方向的轴向载荷,调心性能良好,能补偿因轴承座孔加工造成的不同轴问题,但不能承受纯轴向载荷。
由于振动筛使用环境较为恶劣,许多轴承生产厂家为振动筛生产专用大游隙轴承,轴承材料采用特殊材料,结构也较普通轴承有较大区别,具有承载能力强,耐冲击性能好,润滑性能好的特点。
2)润滑密封结构设计不合理。
激振器工作过程中轴承受偏心块高速旋转产生较大的径向力,由于润滑密封结构设计不合理,轴承润滑不充分,是导致轴承受热产生变形,最终烧损的主要原因。目前国内许多激振器轴承主要采用脂润滑方式,密封主要采用迷宫密封结构。密封间隙一般在1~2mm。
但在实际使用过程中随着激振器内轴承温度的升高,润滑脂黏稠度逐渐降低,激振器主轴高速旋转,迷宫盖内润滑脂从迷宫盖处不断泄漏,最终导致轴承因缺少润滑而损坏。
处理方法:
采用稀油润滑方式,改善润滑通道,润滑油循环流动,使轴承得到充分润滑。
振动筛激振器轴承频繁损坏,从这3个方面找原因
3)轴承与轴承座孔配合选择不当。
轴承与轴承座孔配合公差是设计时的重点。轴承与轴承座孔如果选择较大过盈配合,会迫使轴承滚道形状产生几何变形,导致轴承运转时产生异常振动;如果选择较大的间隙配合,会使轴承外圈在轴承座孔内产生相对滑动,导致轴承温度急剧升高。最终轴承损坏。
处理方法:
选择合理配合公差。由于激振器工作时轴承内圈所受径向力相对激振器偏心力来说是静止的,设计时轴承内圈往往又被轴向定位。故轴承内圈与轴的配合应采用较松的过渡配合或间隙配合公差。
轴承外圈所受径向力相对于激振器偏心力圆周旋转。为防止外圈滑动,同时确保轴承滚动体在保持架中灵活转动,外圈与轴承座孔的配合设计时要采用较紧过渡或稍小的过盈配合公差。
4)设计时未考虑轴的伸缩量。
激振器运行温度一般都在60~85℃。由于热胀冷缩引起轴的伸缩量不可忽视。
处理方法:
设计过程中将一端轴承设计成过渡或间隙配合,以便使激振器轴在热胀冷缩时可以相对于内圈进行滑动,避免轴承受到因热胀冷缩产生的轴向力作用。
2工艺原因
1)轴承座孔的加工精度不够,同根轴两轴承座孔不同心。
处理方法:
采用加工精度较高的设备进行加工,保证两轴承孔的同心精度。在数控镗铣床或加工中心,两轴承孔一次切削完成。
振动筛激振器轴承频繁损坏,从这3个方面找原因
2)轴承装配时用力不均。
如在冷装配过程中对轴承内圈施力不均,导致轴承内圈相对轴产生一定偏斜量,从而使轴承的外圈磨损加快。
处理方法:
轴承在装配时制作专用工装,使轴承装配过程中内圈或外圈均匀受压组装到位。防止装配过程中内、外圈受力不均。
3)轴承安装时未清洁干净,或润滑油不清洁,导致轴承滚道磨损,滚动体摩擦力增大,温度升高,最终损坏轴承。
处理方法:
轴承装配前清洗干净。激振器在使用过程中,按规定定期更换润滑油脂。首次换润滑油在设备使用150h之后,之后设备每运行1000h之后必须更换润滑油。
4)成组偏心块质量差别大或成组偏心块安装角度误差较大,引起振源中心颤动,造成轴承发热。
处理方法:
调整偏心块质量及角度,使其质量及角度对称一致。如果激振器两组的配重块夹角不同或质量不同,所产生的振动方向角和振动力就会不同,就会产生筛体扭振等现象,致使激振器受到异常载荷。
因此在制作偏心块时,应保证偏心块为同等材质、密度相同的材料。同时为保证偏心块质心一致,对偏心块的几何形状制作时也要严格要求。另外在安装或调整激振力时,要使同一根轴上的偏心块角度一致,平行轴上的偏心块角度对称。
3使用及维护原因
1)因基础不平或弹簧座安装不正确,引起筛体的不正常运动,致使振动筛产生转动或扭曲,引起激振器轴承发热受损。
处理方法:
振动筛安装调整时,首先用水平仪测量基础是否水平。如果发现基础不平可以通过在基础上加垫板的方式进行调整,反复测量及调整直至基础水平为止。
2)振动筛重心误差大,引起筛体的不正常运动,致使激振器轴承发热受损。
处理方法:
激振器受到非正常载荷,致使轴承发热受损。因此只有在设计、制造、安装过程中严格控制产品制作安装精度。才能保证激振力重心位置不偏移。同时在振动筛使用时,要尽量做到入料均匀。
振动筛激振器轴承频繁损坏,从这3个方面找原因
3)激振器的固定螺栓松动或未加防松弹簧垫圈,引起振源中心颤动,致使激振器轴承发热受损。
处理方法:
激振器连接时加弹性垫圈,激振器初次使用,运行2h和50h后要重新检查紧固激振器的安装螺栓,发现松动立即紧固。激振器螺栓螺母只能使用一次,紧固后拆下必须换新。
4)润滑油选择不当,填充过多或过少,导致激振器轴承发热受损。
处理方法:
润滑脂加注过多,造成发热,正常应加注润滑腔的2/3为宜,并一定使用排气螺栓排气。但缺少润滑脂或润滑脂老化、干枯同样会引起轴承的发热。一般在不漏油的情况下激振器0~100h加注一次润滑油,一次加注不超过1kg,要观察油的多少加注,并及时排出废油,以便轴承得到正常润滑。
-
轴承
+关注
关注
4文章
2116浏览量
31188 -
故障
+关注
关注
6文章
387浏览量
29398 -
振动
+关注
关注
0文章
130浏览量
20341
发布评论请先 登录
相关推荐
提升机电机轴承温度及振动监测装置
轧机轴承的FC型和FCD的区别损坏原因分析
基于BQ76952的电池包短路保护DSG FET损坏原因及优化方法
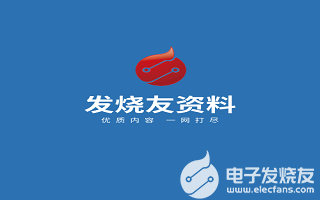
评论