引言
化合物半导体处理通常使用高密度等离子体蚀刻来建立通孔金属接触,该通孔金属接触通常在诸如金(Au)的惰性金属上停止。蚀刻工艺可以从正面或背面穿过衬底和/或有机电介质,例如聚酰亚胺或双苯并环丁烯(BCB)。蚀刻工艺的固有副产物是形成蚀刻后残留物,该残留物包含来自等离子体离子、抗蚀剂图案、蚀刻区域的物质混合物,以及最后来自浸渍和涂覆残留物的蚀刻停止层(Au)的材料。普通剥离剂对浸金的蚀刻后残留物无效,需要在去除残留物之前对金属进行单独的KI浸出。本文描述了一种使用普通fab制造工具在单一工艺中同时去除蚀刻后残留物的简单快速的技术。
介绍
小通孔技术的发展满足了许多器件对热传导和接触的需求。其中包括用于军事和卫星通信的30-75微米功率GaAs MMIC,以及用于低成本MESFET的高功率、高频GaAs pa,用于手机和VSAT应用的HBT和pHEMT。[3]虽然这些过孔中的大多数都是“钻”穿晶圆衬底,但它们也存在于电介质中,如BCB [4]或聚酰亚胺[5],器件性能处于较低频段,因此可以使用非晶材料,而不会产生谐振频率效应。此外,将正面电介质层与背面镀金相结合增加了衬底强度,这有利于减薄< 75um,背面处理,以及从切割带中拾取和放置非常薄的芯片。
为了有效的蚀刻速率和可接受的各向异性控制,可以通过使用包含Ar和BCl3/Cl2的气体混合物的反应离子蚀刻(RIE)或电感耦合等离子体(ICP ),在GaAs介质中“钻孔”。在蚀刻过程中有四个主要的变化参数:室压、RF功率、BCl3/Cl2比率和Ar流速,并且已经公开。[6,7]对于蚀刻成有机层,如BCB,CF4/O2/N2混合物通过分别富集O2或N2,提供了高通量和各向异性蚀刻之间的平衡。[8]在N2富集的情况下,有机碳的再沉积和石墨化将有助于将活性物质集中到基质介质中并提高分辨率。
大多数情况下,蚀刻停止层是惰性金属,例如金。尽管金层可以溅射或电化学沉积(ECD ),但出于经济和产量的考虑,主要的做法是ECD金。溅射和ECD Au的定义从光滑到不规则的地形变化,如图1中蚀刻后的SEM照片所示。
残留物分析
在具有侵蚀性气体的等离子体蚀刻工具中执行通孔钻孔和槽切割以产生孔和线。制备蚀刻步骤通常使用高温烘烤来去除抗蚀剂中的气体,提高其Tg以改善粘附,并无意中促进交联。等离子体蚀刻会在整个晶片上从抗蚀剂和衬底上再沉积副产物。这一直持续到检测到不同的材料或金属(蚀刻停止),从而终止蚀刻。该残留物主要由来自抗蚀剂、衬底以及在该表面上的蚀刻停止材料的物质组成。在图2中,背面GaAs蚀刻过孔的侧壁EDS结果显示了衬底(GaAs)、碳/氧(抗蚀剂)和Au(蚀刻停止层)的存在。
结论
在III-V族晶片制造的正面和背面工艺中进行通孔蚀刻。清洗是可能的用一种或两种化学物质进行的单一过程。化学成分的变化取决于残留物的组成,进而取决于被蚀刻的衬底。对于BCB蚀刻通孔,需要两种化学物质来溶解和去除被认为是BCB相关的物质。对于GaAs蚀刻通孔,单一化学物质是可能的。与任何清洗过程一样,用超声波或喷嘴搅动是主要的好处。进一步的工作应该探索与多工艺KI蚀刻相比的镀液寿命。
审核编辑:符乾江
-
半导体
+关注
关注
334文章
27390浏览量
219028 -
刻蚀机
+关注
关注
0文章
52浏览量
4221
发布评论请先 登录
相关推荐
芯片湿法刻蚀方法有哪些
芯片湿法刻蚀残留物去除方法
三元锂电池组装过程中的焊接工艺有哪些注意事项?
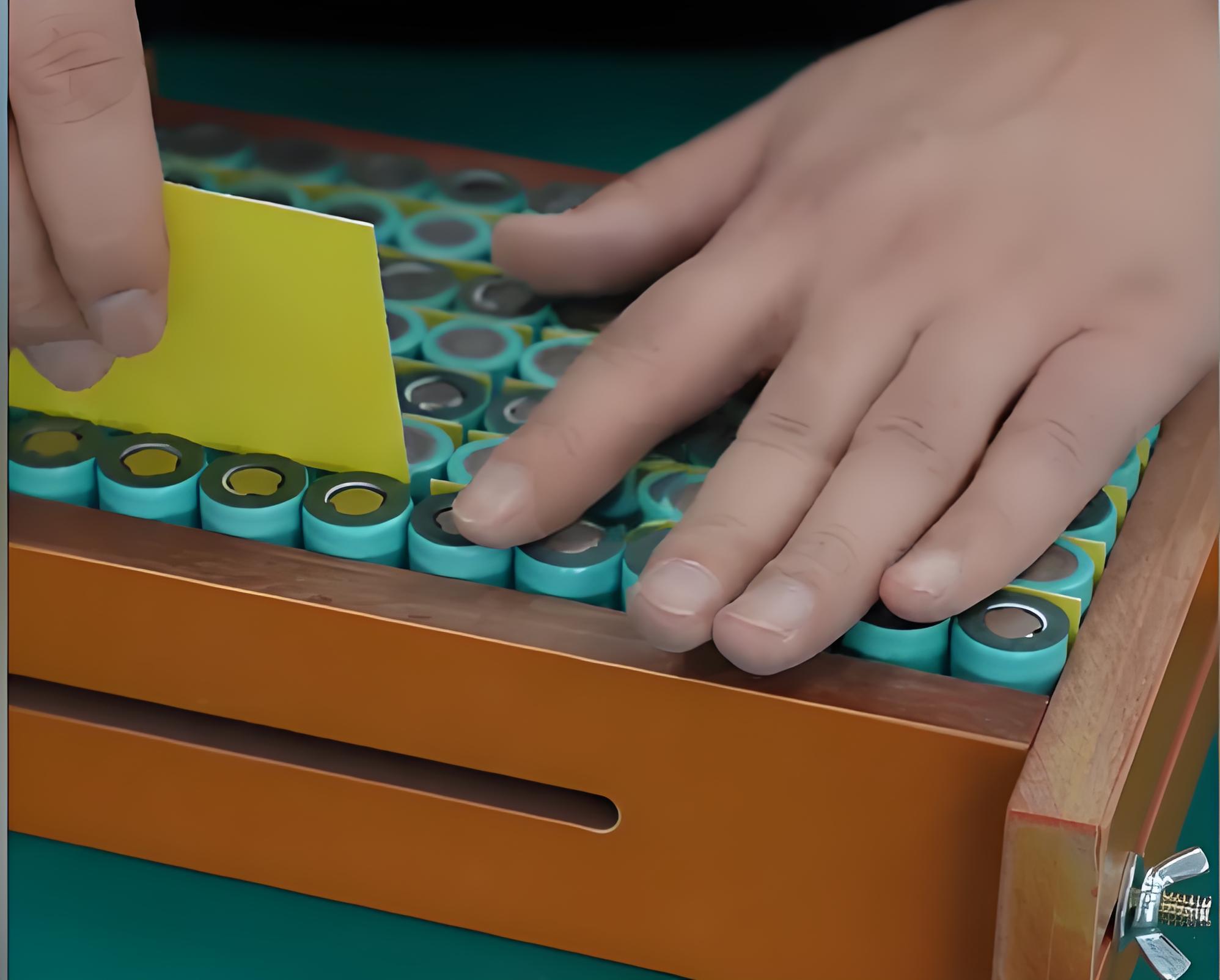
晶圆湿法刻蚀原理是什么意思
半导体湿法和干法刻蚀
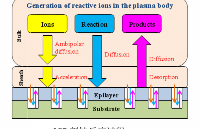
芯片制造中的湿法刻蚀和干法刻蚀
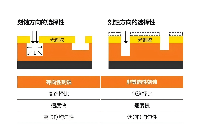
PDMS湿法刻蚀与软刻蚀的区别
锡膏焊接后残留物如何清洗?
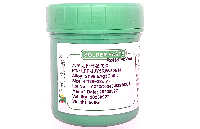
评论