轴承套圈的金属流线
目前,生产中小型轴承套圈主要有冷挤压、钢管车削、热锻和冷辗扩4种方法,而使用常规的金相检测手段根本无法区分这4种方法生产的轴承套圈。通过研究发现,这4种工艺生产的轴承套圈的流线存在一定的区别,可以通过观察流线来区分轴承套圈的生产途径。
1观察轴承套圈流线的方法
观察轴承套圈的流线需要在纵向试样上进行,将套圈纵切面经抛光后用5%的苦味酸酒精溶液进行浸蚀,用放大倍数为10~20倍的显微镜对切面进行直接观察,可以很清晰地看到其流线。
2各加工工艺制造的轴承套圈的流线
流线是金属中的低熔点成分和带状组织偏析在轧制或挤压时伸展而形成的[1]。流线形成后,用一般的热处理方法不能消除。以下介绍这4种不同生产方式加工的轴承套圈的金属流线。
2.1冷挤压
冷挤压,又称冷锻,是把金属毛坯放在冷挤压模腔中,在室温下,通过压力机上固定的凸模向毛坯施加压力,使金属毛坯产生塑性变形而制得零件的加工方法。其特点为:
(1)比切削加工和其他锻压生产节约材料。
(2)可以高效率地加工形状复杂的零件。
(3)冷挤压件的尺寸和形状精度高,表面质量好,且提高了力学性能。
轴承套圈毛坯冷挤压一般采用套料单圈复合挤压工艺,其生产流程如图1所示。外圈采用复合挤压原理生产,内圈用单圈反挤压原理生产,所以外圈和内圈的流线也不相同。复合挤压时坯料上的一部分金属顺着凸模运动方向流动,而另一部分的流动方向则相反,外圈毛坯经车削后的流线如图2所示。单圈反挤压使金属的流动方向与凸模的运动方向相反,内圈毛坯经车削后的流线见图3。
2.2钢管车削轴承套圈的流线
由于轴承钢管内、外径精度较高,总脱碳层深度浅,有利于少切削或微切削工艺制造轴承套圈,也有利于精密辗扩轴承套圈[2]。钢管本身的流线是沿拔制方向延伸,经车削后沟道部分的流线被切断。钢管车削轴承套圈的流线见图4。
2.3钢管冷辗扩轴承套圈的流线
冷辗扩可使套圈毛坯的形状极大限度地接近成品的形状,从而显著地提高材料利用率和零件的精度,节省部分车加工、磨加工工序,提高磨削效率。同时由于采用了无切削辗扩加工工艺,使零件内部金属流线得到改善,大大提高了轴承的使用寿命,因此轴承套圈冷辗扩技术作为一种无切削加工工艺越来越受到轴承制造业的重视[3]。钢管经过冷辗扩加工后,其内部的流线按工件表面形状延伸。经冷辗扩后轴承套圈的流线见图5。
2.4热锻→车削轴承套圈的流线
热锻是生产轴承套圈毛坯的传统工艺。国内目前普遍采用中频感应对坯料进行加热,再经截料,墩压,冲孔,扩孔等工序生产轴承套圈。中频感应加热用于热锻主要有省电节能;安装、操作方便;快速透热,减少表面氧化,节省材料;可避免表面脱碳,提高锻件质量;提高模具寿命;极大地改善工作环境;生产成本低等优点,因此近几年得到了迅速发展。热锻件经车削后流线见图6。
2.5热锻→车削→冷辗扩轴承套圈的流线
热锻件经车削后再进行冷辗扩也是生产轴承套圈的途径之一。热锻件经车削再进行冷辗扩后的轴承套圈的流线如图7所示。
-
结束语
实践证明,采用观察流线的方法可以有效地分辨出各种不同的套圈成形方法,有利于进行产品的失效模式分析,且简便可靠。
(运转世界大国龙腾 龙出东方 腾达天下 龙腾三类调心滚子轴承 刘兴邦CA CC E MB MA)
热处理工艺对轴承尺寸稳定性的影响
轴承是一种精密的机械基础件,内圈及外圈尺寸的精度直接影响着安装质量、轴承的各种性能.因存储条件引起的尺寸变化,会造成轴承在使用时,出现早期失效[1]。为此,笔者通过改变轴承热处理工艺路线的方法,对影响轴承尺寸稳定性的因素,做了下列研究。
1试验方法
1.1试验工艺方案
以车加工后的6204、6209轴承内圈为例,各取40件样品进行试验.改变热处理工艺路线的淬、回火工艺参数,分4组进行试验,每1组10件,工艺方案见表1。使用的设备为:振底式淬回火自动生产线。
1.2热处理质量
四种试验工艺方案经热处理后,其硬度平均值均在62~63HRC,硬度值和淬火、回火组织均符合JB/T1255标准规定,测量结果见表2。
2试验结果及分析
2.1试验结果
两种轴承内圈,分别按照四种试验工艺方案,经过磨削加工之后(其中第4种工艺方案,经过附加回火处理)存放四个月。轴承内孔尺寸,每月测量一次,为了减小测量误差,每次测量均使用同一台仪器和标准件,且测量前标准件和被测工件一起恒温4h。实际测量的内孔尺寸数据整理后,与存放之前的初始尺寸之差的平均值如表3,变化曲线如图1所示。
2.2试验结果分析
(1)从表3和图1、图2可以看出,随着存放时间的增加,两种轴承的内孔尺寸总的变化趋势是增大。这说明,尽管热处理后的硬度及金相组织合格,但是,轴承钢在低温回火过程中残余奥氏体不可能完全转变,在奥氏体化温度为840℃,工件冷却至室温时,残余奥氏体含量可达12%,这些残余奥氏体随着时效逐渐转变为马氏体,从而引起工件尺寸涨大。
(2)第2种工艺方案,其尺寸变化量最大。这是由于淬火油温较高,使轴承钢淬火过程中组织不能充分转变,因而残余奥氏体含量较高.而延长回火时间对薄壁零件的组织转变没有明显的影响。所以造成回火后工件尺寸变化比较大。
(3)第3种工艺方案的尺寸稳定性效果非常明显,这说明轴承钢在淬火后、回火前经过充分冷却能起到减少残余奥氏体的作用。
(4)工件的直径和横截面积的大小同样影响残余奥氏体的含量,直径和横截面积越大,残余奥氏体含量也越大,造成工件尺寸膨胀越大。
(5)第4种工艺方案的工件粗磨之后进行附加回火处理,尺寸稳定性很明显,这是因为附加回火能够消除部分磨削应力,能够起到进一步稳定组织的作用。
4种工艺方案中,工件随存放时间的变化是跳跃式的,这说明工件在淬回火后马氏体和奥氏体的组织转变都是不充分的,而是随着时效逐渐转变。当残余奥氏体转变占主导地位时,工件尺寸就变大;而马氏体回火转变占主导地位时,工件尺寸就收缩。
3结语
(1)回火前的清洗冷却工序,要根据不同的工件类型,制定相应的清洗时间和温度,特别是夏天淬火、回火自动生产线上的循环清洗系统应增加冷却装置。
(2)工件粗磨之后,应进行附加回火处理,能够起到稳定尺寸的作用。
(3)对于尺寸稳定性要求较高的精密轴承和中大型薄壁轴承必须采用附加回火或冷处理工艺。
审核编辑:符乾江
-
轴承
+关注
关注
4文章
2109浏览量
31149 -
金属
+关注
关注
1文章
592浏览量
24304
发布评论请先 登录
相关推荐
轴承结构生产工艺流程柴油机轴承的结构与安装
凤凰动力舵轮驱动轮的稳定性如何影响AGV的运行效率和稳定性
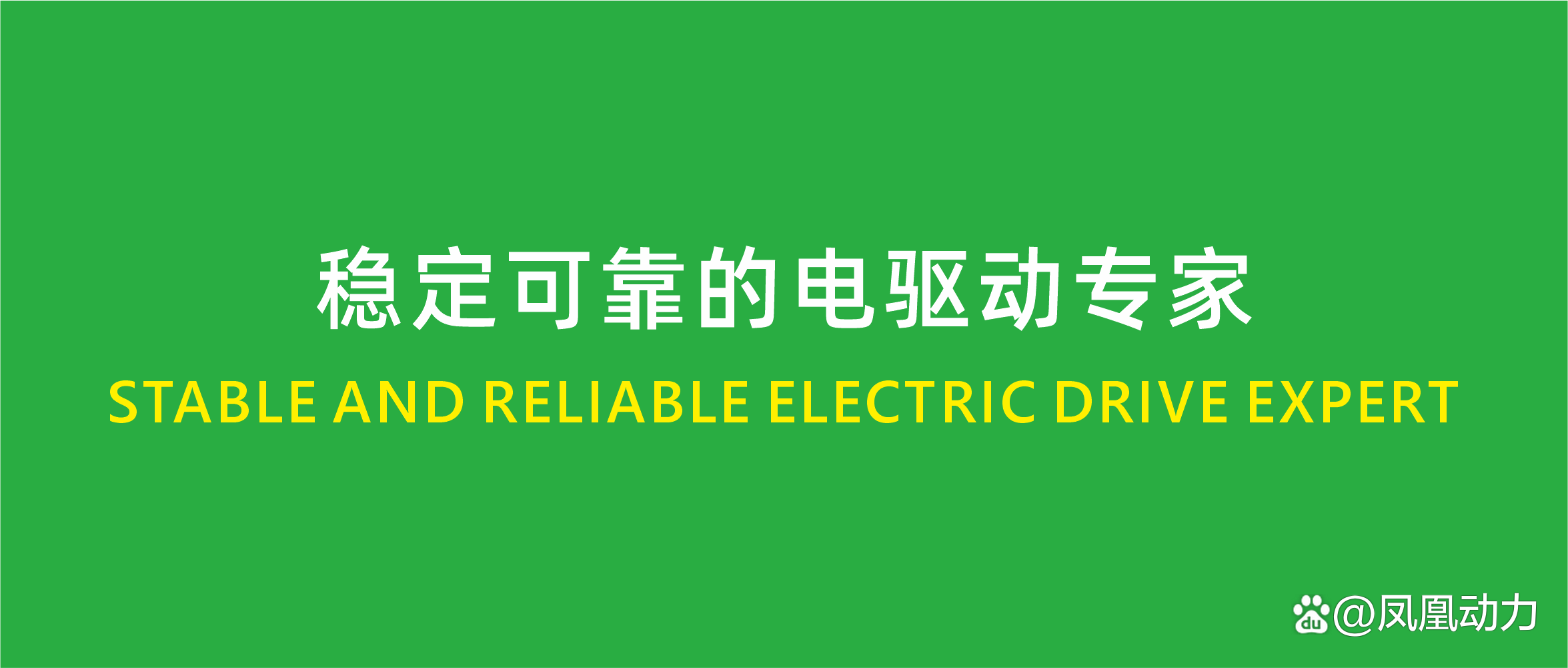
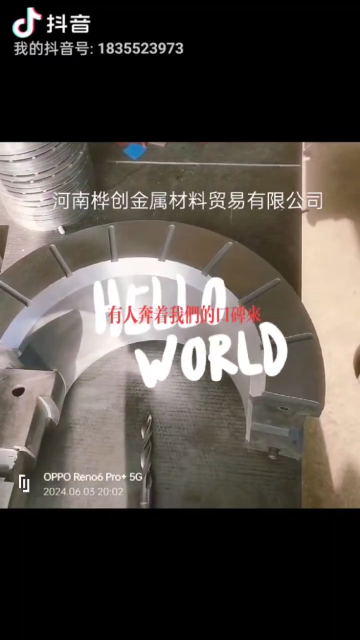
评论