本文介绍了我们华林科纳在半导体制造过程中进行的湿法蚀刻过程和使用的药液,在晶圆表面,为了形成LSI布线,现在几乎所有的半导体器件都使用干蚀刻方式,这是因为干法蚀刻与湿法蚀刻相比,各向异性较好,对于形成细微的布线是有利的。
湿法蚀刻是对膜进行各向同性蚀刻,因此不利于形成精细的布线,能够使用的布线有限,在最上层的Al系布线中使用的情况,这是因为与干法蚀刻相比,可以用廉价的装置形成。另外,在形成接触孔和通孔孔时,为了改善其后成膜时的覆盖范围,有的情况是首先用BHF药液进行湿法蚀刻;另一方面,在现在的半导体器件制造工艺中,作为最多的使用目的,还是去除布线形成后不需要的膜。
下面介绍半导体制造过程中的重要组成部分:清洗和使用药液,下列的表中。首先是粒子去除(清洗),通常使用的药液是氨和过氧化氢水的混合液,混合比例、液温、清洗时间等是各公司的专有技术,一般来说氨:过氧化氢:纯水=1:1-10:20-100,温度40-70℃,使用时间为30秒-4分钟。
接下来是金属去除(清洗),需要利用氧化溶解机制去除金属成分,一般情况下,使用盐酸和过氧化氢水的混合液(简称HPM)、硫酸和过氧化氢水的混合液(简称SPM)的情况较多,在60℃以上的高温下使用,以提高氧化和溶解效率,另外从高性能和降低成本的观点来看,具有仅次于氟的高氧化势的臭氧水(臭氧浓度约10 ppm,25℃以下)也被广泛采用。
下面就有机物去除(清洗)进行论述,除光刻胶外,作为附着在晶圆表面的有机物,几乎没有大的固体状物质,因此,粒子和金属不纯 通过用于清洗物体的APM和HPM(或SPM),有机物也被去除清洗。
最后,关于一般制造很多半导体器件的公司、研究机构所采用的清洁配方,按照APM→纯水护发素→HPM(或SPM)→纯水护发素→干燥的顺序进行清洁构成,通过该配方,粒子、金属·有机杂质几乎全部可以清洗。
下面介绍一下清洗装置;清洗装置分为总线式清洗装置和单叶式清洗装置两类。总线式清洗设备的优点,毕竟是与单叶式清洗设备相比,晶圆生产率更高,25片或50片晶片一次性投入浴缸内清洗;另一方面,缺点是粒子性能与枚叶式相比较差的情况较多,也就是说,在总线式中,附着在晶圆表面的粒子在清洗槽内暂时离开晶圆,该粒子存在于槽内的药液和纯水中,之后,将晶圆移动到下一个清洗槽时,晶圆被提升到槽内液的上部,此时,槽内的粒子再次附着在晶圆表面的情况较多。
为了除去槽内的粒子,使其通过过滤器进行液体循环,但是现在还不能完全用过滤器除去粒子,另外,其缺点是药液·纯水消耗量比单叶式装置大,而叶片式清洗设备的优点是粒子性能比总线式好,由于将通过过滤器预先除去液体中存在的粒子的药液·纯水施加到晶圆上,因此液体不会将过滤器直径以上的粒子附着到晶圆表面。其优点是药液·纯水消耗量比汇流式装置小;通常,每片晶圆使用纯水约为每分钟1升,劣势在于,与总线式清洗设备相比,晶圆生产率较小。因此,为了补充生产率,有时每个清洗装置设置10个左右的处理室,
这样,由于总线式清洗装置和单叶式清洗装置具有特点,制造半导体器件的各公司根据制造的半导体器件是哪种配线尺寸代(节点代)的产品,以及清洗目的和工艺,分别使用采用的器件类型
下面介绍晶圆表面的清洁度,清洗晶圆后,确认清洗性能的方法,首先,粒子当然是目视无法看到的小粒子,因此通常使用被称为激光式粒子检查装置的检查仪器,将氩等激光器扫描到晶圆表面,当存在粒子时,通过检测与粒子尺寸相关的散射激光量,将晶圆表面上的粒子位置和尺寸显示为晶圆图,现在,作为市场上销售的检查装置,可以检测到的最小粒子尺寸约为30 纳米左右。
接下来,对金属成分的测量方法进行阐述,在20多年前,主要采用寿命测量方法,这种方法是利用预先测量寿命和金属杂质量的数据作为标准,通过测量晶圆寿命的值,类推金属杂质的附着量,最近,许多半导体制造公司正在采用测量实际附着金属成分量的分析方法,而不是使用寿命时间方法,即ICP-MS(电感耦合等离子体质谱仪)TXRF(全反射荧光X射线反射)。
最后是有机物测量,GC/MS方法被普遍使用,在尖端半导体器件制造中,来自洁净室内存在的装置、构件、药液等构成物质的微量有机物气体,在制造过程中引起反应物的形成和异常生长,从而降低半导体器件的成品率。
对晶圆的湿法蚀刻法、清洗和清洁度进行了简单的描述,在半导体器件制造中,从创建期到现在,与粒子等杂质的斗争在将来也不会改变,在与粒子的战斗中最重要的工序是清洗,可以想象今后也会越来越受到重视,如果清洁技术不能日新月异地进步,那么总有一天,半导体器件会受到良率低下而无法制造的致命伤害。
审核编辑:汤梓红
-
半导体
+关注
关注
334文章
27335浏览量
218424 -
晶圆
+关注
关注
52文章
4903浏览量
127961 -
蚀刻
+关注
关注
9文章
413浏览量
15372
发布评论请先 登录
相关推荐
晶圆湿法刻蚀原理是什么意思
晶圆背面涂敷工艺对晶圆的影响
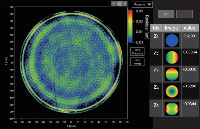
SMT中的离子污染检测:ROSE、离子色谱法(IC)与C3方法比较
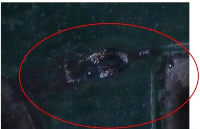
浅谈影响晶圆分选良率的因素(1)
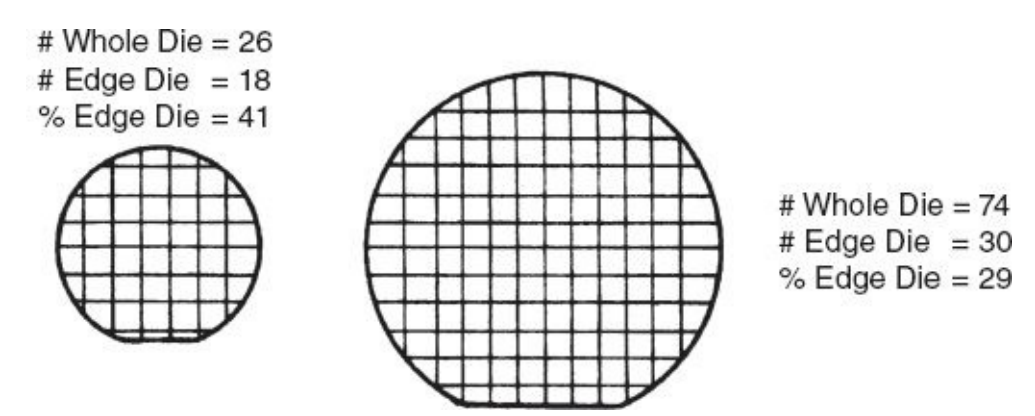
如何解决汽车零部件清洁度问题
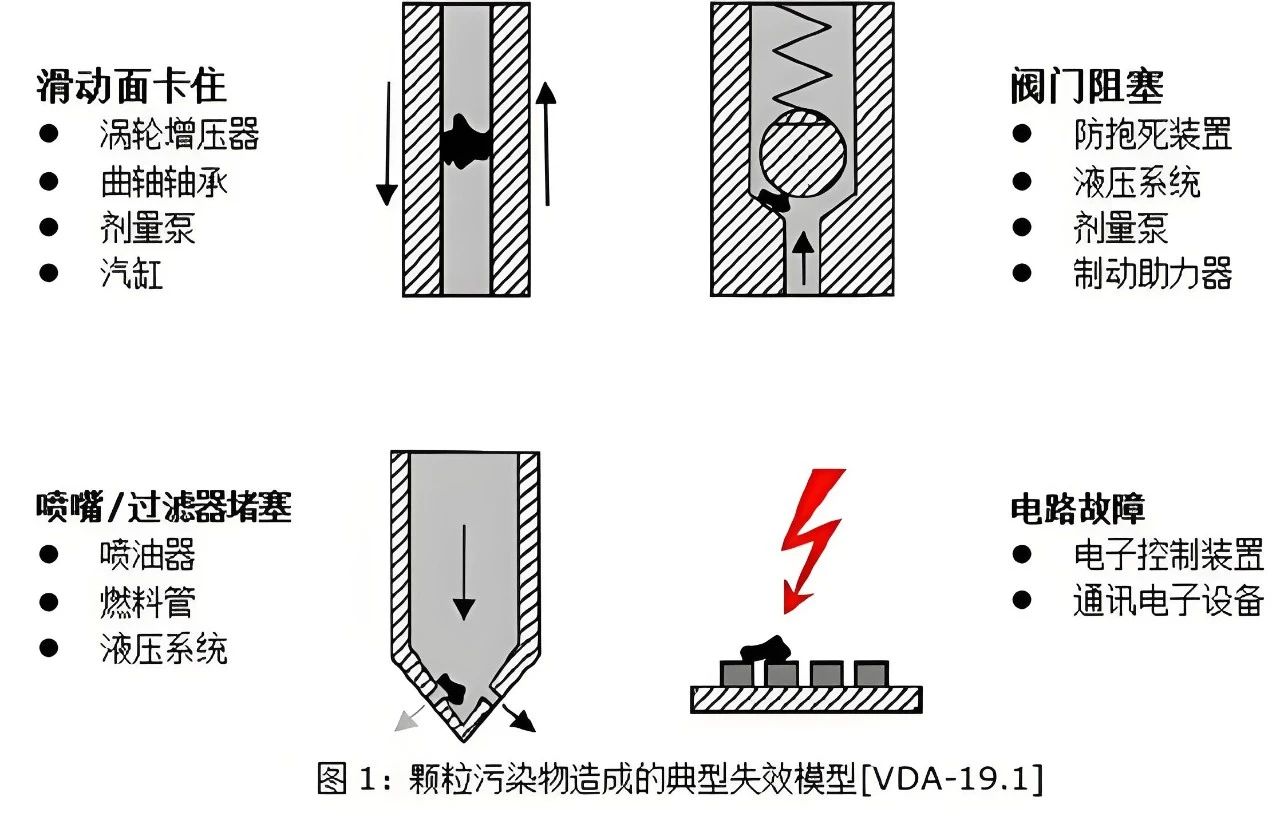
详解不同晶圆级封装的工艺流程
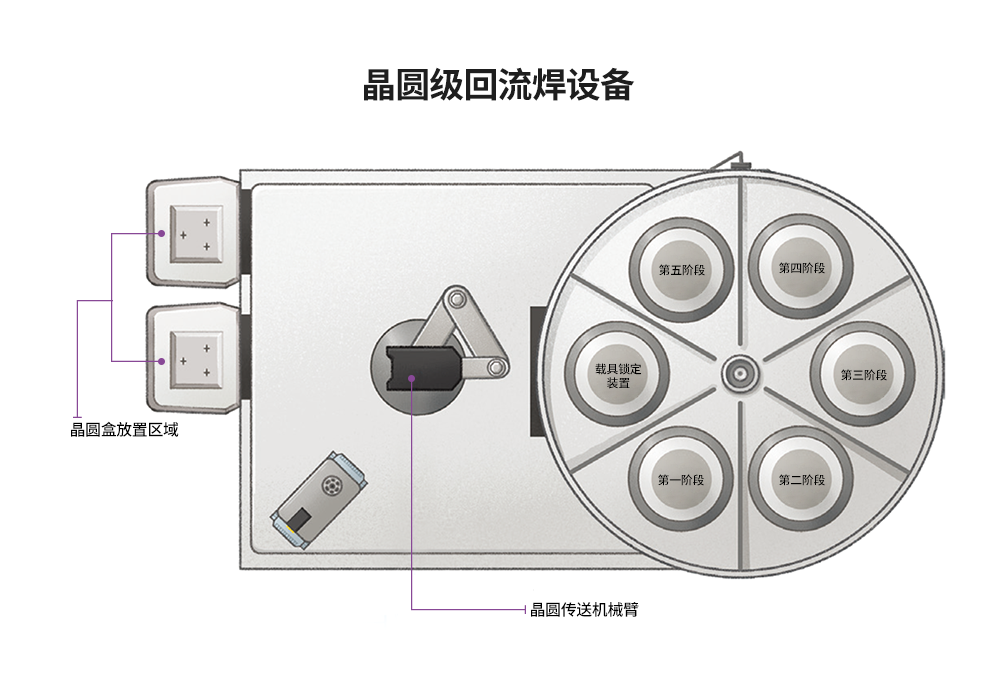
碳化硅晶圆和硅晶圆的区别是什么
蔡司EVO扫描电子显微镜进行轴承清洁度检测
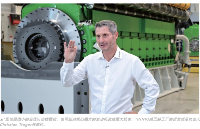
评论