不用亲临车间的生产现场,透过大屏幕就能对车间内的一切了如指掌。不仅能随时查看车间员工所处的位置和工作状态,还能随时查看车间里各个设备的配置、位置、运行状态、物料的准备情况,以及设备内部各部件的状态,一旦出现安全威胁和设备故障还能提出预警……这些并不是科幻电影中的场景,而是重庆旗能电铝有限公司(以下简称“旗能电铝”)已经落地了的现实。旗能电铝携手软通动力,引入数字孪生技术,通过三维建模,对工厂设备和整体环境进行可视化呈现,实现了生产现场的安全可视化监控,促进了安全生产,提升了公司管理水平,为企业迈向智能化奠定了坚实的基础。
传统制造业要升级数字化技术是刚需
旗能电铝成立于2008年,是由重庆市国资委下属重庆市能源投资集团有限公司主要出资并控股的大型国有企业,注册资本18.29亿元。公司是以电解铝为基础,集电力、物流、信息化服务、区域电网为一体、铝-电-网一条龙经营的大型企业,是重庆地区规模最大、两化融合程度最高的电解铝供应商。
作为一家典型的传统铝业制造企业,旗能电铝面临着传统产业优化升级的压力,正致力于通过数字化转型推动企业从传统制造向智能制造转型。一直以来,旗能电铝非常重视数字化技术,作为电解铝行业首家采用MES、ERP信息化系统,对电解、发电与铁路实行一体化管控的企业,引领了行业的信息化发展。经过多年的建设,目前旗能电铝已经具备比较好的信息化基础,但如何进一步通过数字化技术加速旗能电铝的数字化转型进程,赋能企业的发展成为旗能电铝要面对的一个问题。数字孪生技术的发展让旗能电铝找到了突破口。
旗能电铝面临以下需求:公司需要一套系统实现智能工厂展示、掌控生产状态、对公司整体环境、生产车间及设备、安全重点监控区域进行可视化监控;通过设备的互联互通,将车间的生产设备等数字化设备实现程序网络通信、数据远程采集、程序集中管理、数据溯源、大数据分析、可视化展现、智能化决策支持,将设备由以前的单机工作模式,升级为数字化、网络化、智能化的管理模式;企业需要更大范围、更高效率、更加精准地优化生产和服务资源配置,促进企业产业转型升级。
而数字孪生技术正好可以帮助旗能电铝克服这些挑战。一方面,通过数字孪生技术可以将处于不同部门、不同系统数据格式的海量数据进行汇总,实现多源异构数据融合;另一方面,通过数字孪生技术提升设备工作效率和操作透明度,对车间生产设备进行精准监控,并进一步催生出个性化定制、智能化生产等新模式、新业态。
引入数字孪生 加速智慧工厂建设
了解到数字孪生技术对于提升公司管理水平的价值后,旗能电铝决定在“电厂铝厂一体化运行方式”和“冰晶石-氧化铝融盐电解法生产工艺”项目中引入数字孪生技术,对项目实现智能化改造。通过公开招投标,旗能电铝选择与软通动力合作来完成数字孪生工厂的建设。
接手项目后,软通动力依托其数字孪生平台IssMeta,融合AIoT技术能力,为旗能电铝打造出一体化的孪生工厂,实现了全厂区空间精准化监控、工艺流程实时仿真、远程运维、安全模拟演练、双碳能源减排等主要业务功能,圆满地达到了预期目标。
在数字孪生工厂的建设中,三维建模是基础,也是关键环节。软通动力基于IssMeta技术平台的智能逆向建模技术,结合激光点云数据构建的全厂实景孪生模型,真实还原了旗能电铝智能工厂从宏观到微观的虚拟场景;通过数据智能匹配实现了对工厂、重点生产区域、安全重点区域孪生空间的构建,并通过对接(包含槽控系统、电厂SIS系统、MES系统、高温铝液系统等)构建统一的数据图谱,形成工厂孪生资产,对孪生体对象实现信息可视、可追溯、可共享的规则;实现了物理厂区的数字化精准化映射、设备生产要素的全方位同景还原。
软通动力还依托IssMeta产品的仿真技术、工艺流程组件、工艺流程算法、蓝图组件等关键技术,针对生产过程中关键生产环节的重点事故(电解槽漏槽、油罐爆燃、氨气泄漏),搭建了重点事故模拟训练环境,形成预警方案库,辅助作业线人员对操作流程、应急响应、处理预案做到了然于胸,并可远程对每个生产环节节点的信息追踪,辅助管理能源调度,提高人员处理问题效率,提升生产安全意识。
另外,通过数字孪生工厂的建设,当前厂区可达到所见即所得的业务信息处理,对于生产中的各类业务数据进行可视透明的展示与查看,便于各业务周期的人员信息同步与统一协作。
值得一提的是,在构建数据图谱的过程中,还通过设备的互联互通,实现了车间数字化设备数据的融合,将设备由以前的单机工作模式向网络化、智能化的管理模式升级,为后续的数据分析和利用打下了良好的基础。
目前该系统已经投入运行,取得了非常好的效果。在2022年一季度运行期间支撑了电解铝车间持续安全生产90天的生产活动,保障了在疫情压力下的第一季度安全生产经营指标提前10天达成,实现了疫情下的重庆原铝供应保障。同时,第一季度旗能电铝公司相比去年同期原铝产量提升10%,该系统的上线运行也发挥了关键作用。
工业元宇宙推动制造业数字化升级
当前,中国制造业正面临向数字化、智能化转型的关键时期,转型成功与否决定了企业在未来生存和发展的命运,也决定了未来制造业持续发展的态势。《“十四五”智能制造发展规划》明确提出,到2035年规模以上制造业企业全面普及数字化、网络化,重点行业基本全面实现智能化,推动制造业数字化战略转型已迫在眉睫。
在推动制造业迈向智能化的诸多技术之中,数字孪生备受关注,也被寄予厚望。利用数字孪生技术实现物理世界的工厂在虚拟世界的一对一映射和实时联动,打通虚拟世界与物理世界,通过虚实融合,不仅可以实现了可视化展示,还可以实现精准预警以及运营优化,成为当下智慧工厂建设中的热门技术。
软通动力依托其在制造行业多年积累的丰富行业经验和数字化技术,打造出了IssMeta数字孪生平台。该平台深度融合人工智能、大数据、数字孪生等前沿技术,将信息、技术、设备与产业综合体管理需求有机结合,覆盖设备运行监控、数据交互联动、巡检管理数字化、工艺仿真及参数智能调优、仿真模拟应急训练等多个业务领域,实现对工厂的实时映射、感知、分析、预测和监控,可以帮助企业提升数字化能力,提升管理水平,为下一步智慧工厂的建设奠定坚实的基础。
今天,数字孪生技术赋能的智慧工厂已经成为制造业的发展刚需,通过打造智慧工厂提高生产经营效率和管理水平正成为越来越多制造企业的选择。随着智慧工厂的普及,数字孪生也将迎来大发展时期,而作为扎根制造行业多年并已经在数字孪生技术率先布局的软通动力也必将迎来更多机遇和更大舞台,为中国制造企业迈向智能制造发挥更大价值。
审核编辑:汤梓红
-
制造业
+关注
关注
9文章
2240浏览量
53623 -
软通动力
+关注
关注
1文章
804浏览量
15158 -
智慧工厂
+关注
关注
2文章
408浏览量
27507 -
数字孪生
+关注
关注
4文章
1327浏览量
12261
原文标题:软通动力赋能旗能电铝落地数字孪生工厂,“虚实融合”释放数字潜力
文章出处:【微信号:isoftstone-group,微信公众号:软通动力】欢迎添加关注!文章转载请注明出处。
发布评论请先 登录
相关推荐
软通动力出席原生鸿蒙使能徐州专场推介会
东软载波工厂AI智慧照明方案解析
华为全联接大会2024|软通动力携手华为发布ISDP伙伴支撑中心
软通动力联合华为助力永锋临港建设钢铁行业大模型
软通动力荣获2024金鼎奖“科技赋能业务创新案例奖”
云动鸿蒙计划 软通动力携手华为云及伙伴共扬鸿蒙千帆
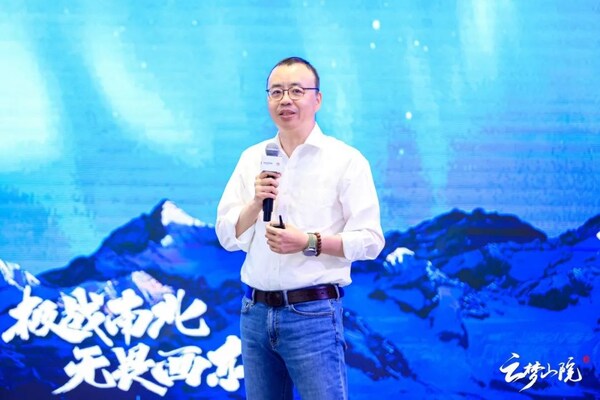
软通动力携手金蝶成立苍穹PaaS联合共建实验室
软通动力与华为联合发布智慧养殖解决方案
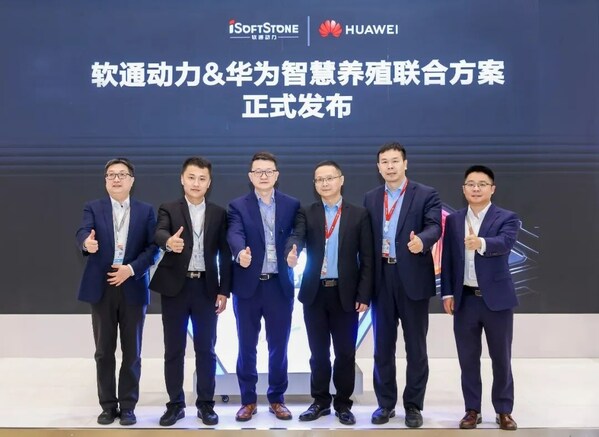
评论