随着电子装联技术质量的提高以及市场的竞争需要,全自动插装机得到迅速普及。这样对单面PCB纸基板材冲孔质量(少数单双面非金属化孔环氧-玻璃布基板也采用冲孔)的要求也就越来越高。
本文主要介绍了PCB冲孔常见的十大瑕疵以及解决办法,分别有毛刺、铜箔面孔口周围凸起、孔口铜泊向上翻起、基板面孔口周围分层泛白、孔壁倾斜和偏位、断面粗糙、孔之孔与间裂纹、 外形鼓胀、废料上跳及废料堵塞等,具体的跟随小编一起来了解一下。
一、毛刺
产生原因:
凹、凸模间隙过小,造成在凸模和凹模两侧产生裂纹而不重合,断面两端发生两次挤压剪切。
凹、凸模间隙过大,当凸模下降时,裂纹发生晚,像撕裂那样完成剪切,造成裂纹不重合。
刃口磨损或出现圆角与倒角,刃口未起到楔子的分割作用,整个断面产生不规则的撕裂。
解决方法:
合理选择凹、凸模的冲裁间隙。这样的冲裁剪切介于挤压和拉伸之间,当凸模切入材料时,刃口部形成楔子,使板材产生近于直线形的重合裂纹。
及时对凹、凸模刃口所产生的圆角或倒角进行整修。
确保凹、凸模的垂直同心度,使配合间隙均匀。
确保模具安装垂直平稳。
二、铜箔面孔口周围凸起
产生原因:
凹、凸模冲裁间隙过小,且凸模刃口变钝。当凸模入被预热而软化的印制板时,板材就在凸模周围产生向外,向上的挤压移动。
凸模刃口端有锥度。当凸模不断进入板材后,孔口周围凸起的现象就会随着凸模锥度的增加而增加。
解决方法:
被冲裁应超过原设计厚度的百分之二十;否则更换板材或重新设计冲模。
冲裁应有足够的压料力,用以克服冲孔时材料移动的反挤力;
三、孔口铜泊向上翻起
产生原因:
由于反冲,使铜箔拉入凹、凸模的冲裁间隙中。
铜箔与基材的结合力差,当凸模从被从被冲的印制板孔中拔出时,铜箔随凸模向上提拉。
凸模刃口端有倒锥,鼓胀变形,当凸模从被冲印制板的孔中拔出时,铜箔随凸模向上提拉。
解决方法:
采用正冲。
更换凸模。
凸模与卸料板的配合间隙不能大,应采用滑配合。
四、基板面孔口周围分层泛白
产生原因:
凹、凸模冲裁间隙不适当或凹模式刃口变钝。冲孔时,被冲板材难以在凹模式刃口处形成剪切裂口。
基板冲裁性能差或没有在冲裁前预热。
压料力小。
凹模刃口下部漏料孔堵塞或漏料阻力大,产生膨胀分层。
解决方法:
合理扩大凹,凸模冲裁间隙;
及时修复变钝的凹模刃口;
增加压料力;
调整基板预热温度;
扩大或铰光漏料孔
五、孔壁倾斜和偏位
产生原因:
凸模刚性较差,定心不稳,倾斜冲入工件。
凸模安装倾斜或与卸料板的配合间隙太大,卸料板对凸模起不到精密导向作用;
凹、凸模的配合间隙不均匀。间隙小的一边,凸模径向受力大,向间隙大的一边滑移;
凹、凸模式装配同心度差;推料板与凹、凸模外形偏位;推料板与凹模配合精度太差(指复合冲裁时)。
解决方法:
合理选择凸模的材料;提高凸模刚性、强度、硬度和不直度。
提高凸模与凹模的加工同心度和装配同心度。
提高凸模与卸料板的配合精度,确保精密导向。
确保导柱、导套的加工精度和装配精度;减少推料板外形与凹模的配合间隙,并使推料板的外形和凹凸外形一致。
六、断面粗糙
产生原因:
凹、凸模冲裁间隙太大;凹模刃口磨损严重。
冲床的冲裁力不足,且不平稳。
板材冲裁性能差。例如,基材含胶量过高、基材、老化、层压结合力低等。
解决方法:
选择适当的凹、凸模冲裁间隙。
及时修整凹模刃口。
选用冲裁性能较好的基材并严格按工艺要求控制预热温度和时间。
七、孔之孔与间裂纹
产生原因:
孔壁太薄,冲孔时的径向挤压力超过印制板基材的孔壁强度。
相邻很近的两孔不是同时冲出,后冲的孔当凸模进入板材时,由于孔壁太薄而被挤裂。
解决方法:
印制板上的孔距设计要合理,孔壁不应小于基板厚度。
相邻较近的孔应便用一副模具同时冲出。
把相邻很近的两个凸模,做成相差 0.5mm的不同长度,使小面积范围内较集中的冲裁力瞬时分散。
八、 外形鼓胀
产生原因:
模具设计不合理。对外形尺寸较大的印制板,如采用凹模内无推料板的下落料时,被冲印制板在自重的情况下,总是向凹模式孔内弯曲。加之,凸模下冲时,气流对工件有一股冲击波,使工件中心更为下曲,而靠近凹模刃口处向下弯曲量很小,造成外形鼓胀。
外形落料的凹模变形,出现长边处产生鼓胀。
解决方法:
印制板的外形尺寸大于200mm时,宜采用上落料结构的模具冲外形。如采用下落料的模具结构时,则一定要在凹模内装一块具有弹性托料力的推料板,使印制板不变形。
增加凹模的壁厚,或选用具有足够的抗弯、抗张强度的材料造模具。
尽量减少凹模的热处理变形。对几何形状复杂的凹模,可采用选热处理淬硬,后用线切割加工的办法来克服变形。
九、废料上跳
有时部份废料在冲孔时不是向下掉,而是向上跳;有的进入工件孔内,还需人工清除;有的跳在下模上面,影响冲裁工作正常进行。
产生原因:
铜箔与基材的粘合力差,冲孔时废料上的铜箔容易脱落,随着凸模退出凹模时,进入被冲孔内。
凹模间隙过大,且漏料不畅通,当凸模退出凹模卸料时,废料随之上跳。
凹模孔有倒锥,冲孔废料难以下落,反而随着凸模退出凹模时向上跳。
解决方法:
加强对基板材料的进厂检验。
减小凹、凸模的间隙,扩大漏料孔。
及时修整凹模孔的倒锥。
十、废料堵塞
产生原因:
凹模刃口太高、废料积存太多。
凹模漏料孔太小或刃口部有倒锥以及孔壁太粗糙。
下垫板和下模座上的漏料孔与凹模孔的同心度差,孔的对接有如阶。
漏料孔太大,废料易在孔内作不规则堆集;相邻两漏料孔成内切时也易堵塞。
下垫板上无导料孔,当废料从凹模孔内落下时,不能顺利的进入下面的漏料孔。
解决方法:
降低凹模刃口,在0.2mm之间可减少废料积存的个数。
当凹模孔《ф0.2mm ,漏料孔最好做成圆锥孔,当凹模孔大于ф0.2mm时,漏料孔可做成直孔,凹模刃口高度部分不能有倒锥。
调整凹模、下垫板以及下模座上的漏料孔的垂同心度,并将各部件上的漏料孔扩大。
相邻两漏料孔内切时,为了不堵塞漏料应做成腰圆孔,或做成一个大孔。
凹模支承杆和下模座的去撑筋要有足够的斜度或漏料通道,使废料顺利地漏下,不致堆积和堵塞。
原文标题:专门解决PCB冲孔的十大瑕疵,后悔没有早知道……
文章出处:【微信公众号:Torex产品资讯】欢迎添加关注!文章转载请注明出处。
-
pcb
+关注
关注
4319文章
23105浏览量
398141 -
基板
+关注
关注
2文章
278浏览量
23021
发布评论请先 登录
相关推荐
端子失效的常见原因及解决办法
常见垫圈故障及解决办法 防漏垫圈的设计与应用
电力电缆的常见故障及解决办法 电力电缆与通讯电缆的区别
雷达探测器常见故障及解决办法
PCBA板常见故障及解决办法
温控器常见故障及解决办法
常见稳压器故障及解决办法
电力电容器的常见故障及解决办法
常见MCU故障及解决办法
万用表常见故障及解决办法
常见元器件故障及解决办法
分析波峰焊时产生连锡(短路)的原因以及解决办法
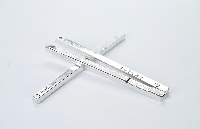
评论