在设备级别,我们华林科纳制造了像素间距为10μm(F IGURE 4)的OLED阵列,相当于2500 ppi。在这种情况下,一个重要的参数是对准精度,它定义了总显示区域中有多少可用于发射。另一个限制是PDL(像素定义层)的分辨率,这是将OLED堆栈与底部接触层分开的隔膜层。该层的分辨率限制了可以实现的最大开口,这相当于像素的光圈比 - 或用于OLED em ission的面积百分比。在这个例子中,“光致发光孔径比”,或OLED岛与像素区域的关系约为50%,这是通过小间距(<3μm)实现的。然而,“电致发光孔径比”,即发光面积的关系,是25%,因为PDL面积和OLED岛的必要重叠。假设最小线间距为1 μm,对于10 x 10 μm的亚像素,可以设想PL比为81%(9 x 9μm)和EL比为64%(8 x 8μm)。通过这种缩放,可以扩大阵列的可用面积,从而延长器件寿命(因为我们可以降低驱动电流密度),并减少或消除屏蔽门效应。
显然, 在超高真空中中断最佳沉积过程并将OLED堆栈暴露在光刻材料下会对器件性能产生影响。仅仅打破真空就会对使用寿命性能造成影响。此外,我们的初始工艺流程包括将烟囱暴露 在环境气氛(空气和湿度)中,因为我们一直在使用标准洁净室设备。一开始,这种“最坏情况”导致了在图案化后发射OLED的概念验证,但毫不奇怪,器件寿命仅为few分钟。在开发过程中,我们在三个方面进行了改进。首先,光刻胶系统不断升级,使其与有机堆栈更加兼容。其次,工艺流程已选择可视化,以减少工艺参数对设备性能的影响。第三,OLED堆栈已经过稳健性调整,例如为最关键的接口引入了额外的保护层。所有这些操作导致设备在 1000 尼特亮度下长达数百小时。由于在这项技术的准备过程中,寿命是主要关注点,因此这是一项持续的努力,旨在将所有参数提高到行业可接受的水平。
在提高性能的同时,我们一直在开发一种使用光刻技术对多色阵列进行图案化的途径。在这种情况下,主要挑战是保护前一个“颜色”(OLED堆栈),同时对下一个“颜色”进行图案化。一旦满足了这一条件,就可以实现具有多个堆栈的并排阵列 - 并且,这不仅限于光发射器。例如,在红-绿-蓝OLED旁边,可以制造一个有机光探测器子像素,以增加显示器的功能。在制造方面,前面板的每种“颜色” 都将以类似于背板每层的方式制造。
在我们最近的工作中,我们制造了一个2色无源OLED显示器,这个原型在Touch Taiwan 2017 exhibition上进行了演示(图5)。1400 x 1400 像素阵列的子像素间距为 10 μm,分辨率为 1250 ppi。这些堆叠是磷光红色和绿色小分子OLED,通过热蒸发沉积。该显示器专为顶部发光而设计,并使用玻璃封装。由于两组子像素的单独驱动,两种颜色可以独立显示。原型已经运行了几十个小时,所有像素都打开了,没有明显的退化。这说明,多色图案化的工艺流程证明了基本功能,并且已经确保了合理工作时间的稳定性。类似的前面板可以与TFT或CMOS背板集成,从而实现视频操作模式,并手动驱动每个亚像素。在另一个演示中,我们还验证了制造工艺与使用IGZO TFT和柔性基板的FPD背板工艺兼容。
考虑到所有因素,orga nic半导体的光刻是一种新兴技术,可以实现高分辨率OLED显示器。许多技术里程碑已经被清除 - 我们知道我们可以实现几微米的图案,实现并排多色像素,将pixeled前面板集成到不同的背板上,并获得令人鼓舞的效率和使用寿命性能。目前,图案化后OLED性能的优化仍然是重中之重。同时,我们正在解决完整的集成流程和可制造性方面的问题。要将该技术完全整合到晶圆厂工艺流程中,需要进行材料和设备开发。尽管如此,在基于标准半导体技术的工艺流程中,具有同时具有高孔径比的超高分辨率的前景仍然非常有吸引力,并且有理由加倍努力应对悬而未决的工程挑战。
审核编辑:汤梓红
-
显示器
+关注
关注
21文章
4981浏览量
140063 -
OLED
+关注
关注
119文章
6203浏览量
224298 -
光刻
+关注
关注
8文章
322浏览量
30191
发布评论请先 登录
相关推荐
lvds接口如何实现高分辨率显示
使用DM642 DSP和THS8200驱动器的高分辨率视频
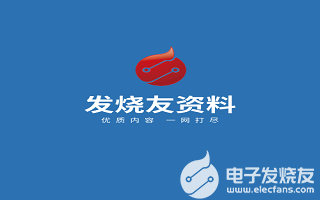
鼎阳科技|高分辨率产品增长39.42%,引领高端市场新浪潮!
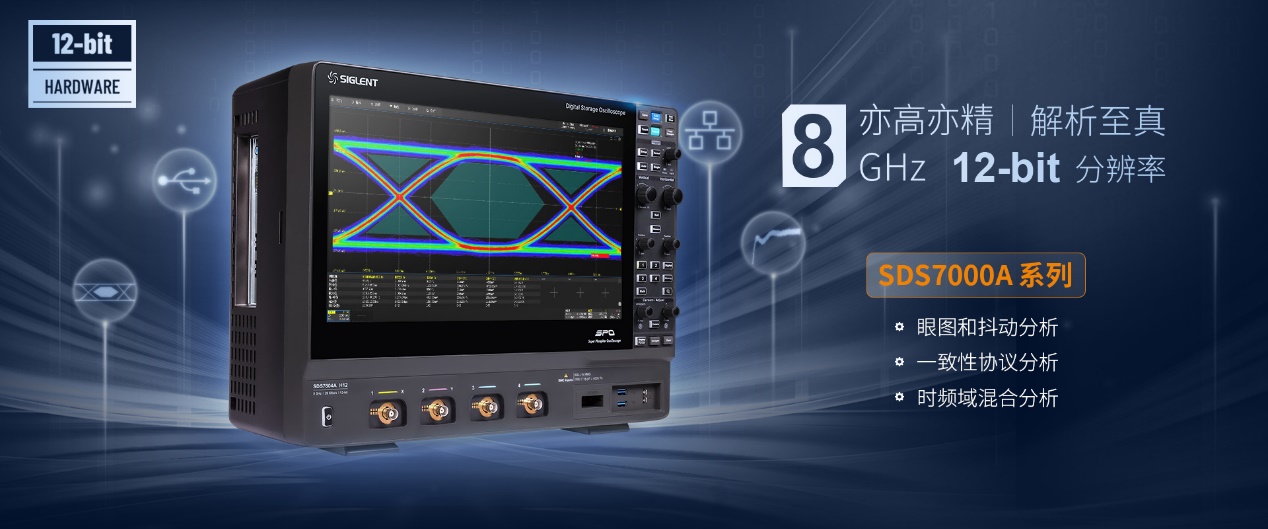
什么是高分辨率示波器?它有哪些优势?
Moritex 5X 高分辨率远心镜头 助力晶圆检测
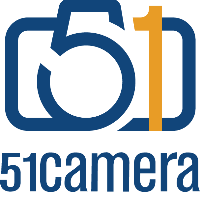
高管洞察:高分辨率音乐需要高分辨率扬声器
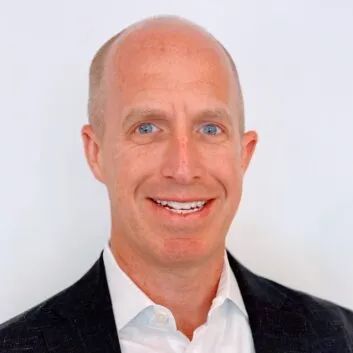
高分辨率音频和普通音频之间的区别
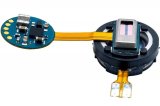
评论