导读
传统车间柔性化程度低,不适应于多品种、小批量、定制化、批产混线生产等需求,建设具有“数字化、网络化、智能化”特征的智能制造车间势在必行。
看点
01
前言
通过对柴油机制造行业企业老式车间调研、参与智能制造专项车间搭建工作及对国内其他智能制造车间建设经验的研究发现,传统车间柔性化程度低,不适应于多品种、小批量、定制化、批产混线生产等需求,建设具有“数字化、网络化、智能化”特征的智能制造车间势在必行。为此,针对上述问题,开展柴油发动机数字化车间的研究对于柴油发动机生产企业的智能化转型与升级具有重要的现实意义。
02
柴油机数字化车间构建需求分析
2.1 国内柴油发动机制造主要工艺流程现状分析
柴油发动机车间的生产线主要由缸盖加工线、缸体加工线、发动机总装配线、发动机预装线、试车线、涂装线、后整理线、包装线等生产线组成,如图1所示。
(1)缸体、缸盖制造工艺分析:目前而言,国内多数内燃机企业在发动机的生产过程中仅需要对缸体和缸盖进行机械加工(缸体和缸盖的铸造成型一般依赖于外协企业),其余的零部件大部分外委采购。近十年来,国内柴油发动机得到了快速发展,国内也逐渐对缸体和缸盖生产线进行了升级,少数企业开始采用高速卧式加工中心来组建柔性生产线,利用机械手进行上下料操作,并逐步加入了自动在线检测等设备。但多数柴油机生产企业在单缸和多缸小缸径柴油机的缸体、缸盖的粗加工和精加工中,还是以主要以组专机床和少量卧式加工中心加专用夹具组成的流水线为主,部分采用了机动辊道来实现工序间的工件传递,上料和下料主要以电动单梁悬挂起重机为主,整个生产线的刚性生产能力强,但柔性生产能力较差。
(2)装配生产线工艺分析:与汽油机制造相比,我国在柴油机整机制造方面的发展相对比较落后,整机装配流水线按工位进行划分,依赖人工进行装配的工序占比重较高。装配线的输送方式一般采用积放链或者板链,部分企业开始使用辊道线,并开始采用一些手段来实现产品信息的自动采集。一些关键部件的装配开始采用电动装置,如采用电动拧紧机来拧紧固定螺栓。
图1 传统车间生产线工艺流程
总体而言,从目前大多数柴油机生产企业的制造工艺流程来看,虽然在流水线作业的基础上,部分实现了加工信息的采集和信息的追溯,但车间整体数字化水平仍然较低,没有实现加工装备、加工工件、装配、质检等信息的自动化采集,信息流动大部分还是采用手工操作记录的方式和传递的方式。
2.2 数字化车间构建需求分析
(1)制造工艺的数字化升级需求:将传统的面向工序的工艺模式通过先进的智能制造技术升级为面向过程的智能化工艺管理模式。传统工艺重点在于工序化管理,依靠工艺流程卡来管控产品的制造过程,效率比较低。开展智能制造,需要改变工艺管理模式,构建产品、工艺和制造紧密关联的工艺模型,建立工艺管理系统,形成对 MES)的有力数据支撑,实现面向过程的工艺管理,提高对关键工艺工程要素的可监测性、可控制性及其可优化性。
(2)智能化设备的配备或老旧车间设备数据采集问题的改造需求:为实现产品的质量控制,必须对设备的刀具磨损情况、工件加工过程中的机床运行状态等进行有效监控。如果不能够对加工环节的信息进行有效的采集和存储,将无法实现产品的可追溯性,达不到对产品生命全周期的有效管理。为此,必须将以传统的工艺流水配置的生产装备升级为智能化、数字化装备。依托国内领先系统集成商、软件开发商、核心智能制造装备供应商,紧扣发动机关键工序智能化、关键岗位机器人替代、生产过程智能优化控制和供应链优化需求,构建面向智能制造的柴油发动机智能化装备集群。
(3)生产线的柔性化需求:形成柔性生产能力是生产线数字化构建的重要内容,就目前柴油发动机市场需求而言,常常需要技术开发与批产混线,多品种小批量混线生产。由此必须结合柴油发动机生产企业的现状,对企业现有的多品种产品的工艺流程进行提前规划,并对加工设备进行提前布局,运用数字化工厂软件对各个环节进行模拟仿真和优化,由此对生产线的数字化构建提供参考,满足生产线的柔性化生产需求,提高DF生产线的工作效率,降低生产成本。
看点
03
数字化车间信息物理系统架构
为了能实现车间内部虚拟平台与物理对象的相互映射及无缝融合,促使数字化车间走向智能化,并对车间内时间和空间信息进行联合处理,从而提高生产线数据的实时性,以满足车间平台任务安排与信息反馈的实时性要求,结合国内外柴油发动机建设的先进经验、存在的问题及考虑智能工厂的发展前景,参照国际标准ISA-95设计了柴油发动机数字化车间的信息物理系统架构,如图2所示。主要包含五个层次,由下而上为:设备层,控制层,网络层,系统层和管理层。
设备层主要包括智能制造设备、智能工装设备、智能物流设备(如上料机器人、AGV小车、传送装置)、智能传感器、智能测试设备。主要功能是实现柴油发动机产品制造、产品检测、工位信息采集、零部件自动化运输、成品运输过程,同时,也是柴油机生产数字化信息的源头与控制层执行生产计划的工具,比如:RFID(无线射频识别)属于智能传感器中的一种,通过在柴油机各加工、装配工位安装RFID传感器,实现车间人员、设备、物料、工装等的编码信息、位置信息、状态信息的非接触式实时采集,再存入MES数据库以数字化升级制造工艺,替代传统车间工艺流程卡来管控柴油机生产。
图2 参考ISA-95标准的车间总体框架
控制层主要包括PLC(可编程逻辑控制器)、单片机等自动化控制器与驱动装置及HMI(人机交互界面)。主要功能是接收来自网络层的加工、装配、采集柴油机生产过程信息等操作指令,再通过控制层的各种硬件进行驱动及控制设备层的各种智能化设备进行柴油机零件制造加工、加工装配数据采集、零部件自动化物流运送等操作。
网络层主要包括工业PON(无源光纤网络)、DNC(分布式数控)网络、各种通讯及控制总线、SCADA系统(数据采集与监视控制系统)、DCS系统(分布式控制系统)和FCS系统(现场总线控制系统)等内容。功能是实现车间智能化加工设备、智能仪表、加工工艺和测试仪器等之间的数据传递及采集,且将系统层中MES系统的柴油发动机计划排产人工或者自动化分解成加工指令,并发布生产指令至控制层。
在这一层级,通过工业PON、DNC网络及工业现场总线等通讯网络在整个车间内部把数控机床、缸体试漏设备、零件压装设备、大量的工控机等形成互联互通的工业通讯网络,以实现生产各个工位之间数据的传递;柴油发动机车间需要配置SCADA系统、DCS系统及FCS系统,以实现车间每条数字化生产线或者每个工位生产的数据实时采集、实时监测、集中管理与分散控制等指令的生成与发布。例如,:缸体加工线每台机床数据采集、监测、管理与控制的高效实现即是依赖于这一网络层的合理设计。
系统层由MES系统及WMS(仓库管理系统)组成,MES系统主要功能是实现柴油机生产车间的管理与生产监控。
首先,承接来自管理层中ERP(企业资源计划)的生产数据(包括柴油机生产日计划,物料库存、调配数据,生产变更数据)与PLM的工艺数据(零部件原材料的种类、相关属性,各条产线的工艺路线,每个工位的工艺信息,数据变更信息);
其次,为操作人员在生产过程中提供图纸工艺和技术文档等内容的无纸化查询及指导操作人员进行生产;
再者,接收来自于网络层所上传的柴油机加工、装配的工艺数据和所有资源(人、设备、物料、客户需求)的当前状态信息,实现车间级的协调、跟踪、决策和调度。
WMS系统与MES系统在软件系统层以 Web 方式进行数据的交互,其接收来自于MES系统的当日生产计划、零部件的物流调配信息与成品完工信息,用于柴油机生产车间物料的调度和配送及成品的入库管理和统计。
管理层包括PLM系统和ERP系统。管理层通过PLM进行产品全生命周期的设计,并通过ERP获取PLM内部工艺数据制定出车间的主生产计划、物料主数据下放至MES系统分解为若干个MES车间生产子任务;同时,MES向ERP系统进行生产进程反馈与生产计划报表。ERP系统主要功能是提升企业管理层的综合管控能力,解决传统车间的工艺、资金、采购、物流等业务之间的信息孤岛效应,并在生产计划管控、企业资产管理、企业财务管控等方面体现其独特的优势。
对于设备层、控制层和网络层这三个层级,通过无线通讯技术与有线通讯技术(如EPON)在车间形成一体化工业网络,解决了传统老式车间信息无法全面采集的问题。
看点
04
柴油机智能制造数字化车间构建策略
根据已规划好的数字化车间信息物理系统架构及构建智能车间的实际需求,数字化车间可按以下五个阶段进行构建:
第一阶段,构建柴油发动机产品研发体系及研发适应市场的产品。在车间构建之前,通过集成有CAD/CAM/CAPP等产品研发系统的PLM平台设计几类面向当前市场的柴油发动机新产品及其产品相关的所有信息(如产品工艺流程、材料、制造、装配、图纸等),以为后期车间设计奠定基础;在车间构建完成之后,利 用 PLM 平台,对发动机结构拓扑、产品工艺进行持续的改进创新、建模仿真、验证分析,从而不断优化产品的工艺流程、研发水平和全生命周期,以升级企业产品制造水平及适应各阶段市场的需求。
第二阶段,数字化车间生产环境的建模及基本布局的规划。分析第一阶段设计出的几种型号柴油发动机产品信息及工艺流程,采用三维模拟技术对发动机生产环境进行数字化建模,建立车间总体的数字化模型及详细规划各产线工艺流程及基本布局,设计出可生产多种类型柴油发动机的数字化生产线。整体规划内容包括生产线数量、各生产线的生产流程、工位数量及位置、工位加工装配内容、数据采集类型及位置和智能化设备种类。
利用三维仿真技术对生产系统进行仿真运行及持续性优化。在车间真实生产之前,仿真生产系运行的各种细节(如:车间物流、产线设备和车间布局等)对各产线产能、成品率和生产成本的影响及发动机生产线生产多机型的柔性化能力,以验证车间布局设计和各种调度计划的合理性;设计多种运行方案,并分析、对比三维仿真系统中车间的运行数据,最终修正设计的问题及规划出满足数字化升级产线、合理配备智能设备、高度柔性化等条件的基本布局;在车间真实生产之后,数字化模拟技术为车间后续生产提供几乎是无限的生产柔性,通过仿真的方式,测试不同生产调度策略对新、旧产品生产的影响。
第三阶段,数字化车间的建设。首先,按照依托国内设备厂商、发动机关键工序智能化、关键岗位机器人替代和生产过程智能优化控制的原则,进行智能化设备、智能传感器的选择,并将智能化设备(如数控机床、上料机器人、气门油封压装机、油道干试试漏机)、智能传感器(如RFID、无线温度传感器、接近开关)安装在第二阶段所设计基本布局的对应位置,并根据数字化模型配备自动化传输线;
其次,安装PLC等自动化控制器与驱动器实现数字化产线设备的自动化控制、智能传感器的数据采集与处理;再 者,在数字化产线载入工业PON网络(优势:高带宽、高抗干扰性、传输距离远)、各种工业通讯总线(如ProfiBUS)、DNC网络等形成数字化车间实时通讯网络,以及在数字化生产线载SCADA系统、DCS系统、FCS系统等控制车间设备进行加工、装配、物流运送等操作及对车间生产进行实时数字化监测。
最终,在车间层级将设备、硬件、监控系统软件融为一体。而在数字化车间构建中数字化的内容主要包括三方面:
(1)部分数据(如设备运行状况、刀具磨损情况)使用智能化设备自带的SCADA系统进行采集;
(2)人、 机、料、工装等的编码、位置、状态信息则通过RFID技术、条码扫描枪、手持终端进行采集,提高产品的可追溯性与生产过程的有效管理,形成对MES的有力支撑;
(3)数字化加工生产线把多台柔性化数控机床通过计算机网络技术构成DNC网络系统,并将自动化辊道、上料机器人、桁架机械臂、空中小车等组成全自动化物流线,在网络中同时嵌入大量传感器实时采集柔性加工线的数据。并且在多种生产模式综合应用下,实现了对工艺要素的监测、产品质量的控制及车间柔性化升级,不仅可以实现当前产品的多品种、小批量的生产,更可以通过替换部分工位设备或者修改部分工位加工工艺的方式快速适应产品更新换代之后的生产且不需重新搭建新的生产线。
第四阶段,载入ERP系统、MES系统、WMS系统等车间级软件平台。将ERP系统与PLM系统进行集成,实现研发/生产一体化,同时,通过 ERP 系统提升企业资源管理水平。PLM 系统向ERP系统中自动传递或者手动传递产品工艺相关的信息、物料清单和工艺路线等信息。
紧接着,载入MES系统,与传统的工艺流程卡号管控车间的功能类似,MES功能为通过为每台柴油发动机创建一对一的序列号的方式,并在实际生产过程中在每个工序通过扫描获取序列号的形式访问工艺数据库获得该工序相关的控制信息,实现从工序管控到车间管控的数字化升级;MES系统接收来自第二阶段布置的数据采集网络的数据以供管理层生产高级排程、产品质量分析及设备管理;再通过上线WMS系统配合MES使用,实现物料出入库、存储、配送等物料管理工作,最终实现数字化车间虚拟系统与物理系统进行无缝衔接,构建出数字化车间信息物理系统架构。
第五阶段,引入新型制造模式。利用最新的云计算技术、大数据分析技术实现产品的未来规划,吸收当前电子商务、云服务等互联网技术的优势等方式,最终实现柴油发动机这一离散型制造行业的智能制造、协同制造、大规模个性化定制和远程运维等新型制造模式。
看点
05
应用实施案例及实际效率比对
在此,针对某柴油机生产企业下属子公司车间制造工艺落后、老旧加工设备数据采集困难及产线柔性化程度低等问题,根据上述构建策略,分五个技术层面/阶段对该企业的生产车间做出了改进,并搭建新型车间:
(1)由于该企业集团公司PLM平台构建比较完善,基于企业PLM和云服务的融合,实现了与该企业集团公司与子公司之间的跨地域实时协同工作,在此仅需完善该企业子公司在产品设计方面的数字化工作。
首先,采用PLM集成的柴油机三维设计软件(SolidWorks 3D)对该车间待产的发动机产品的零件模型及整机装配模型进行了建模,并绘制出相应的工程图,并编写相应的工艺信息和工艺流程信息;其次,对产品的三维模型图、二维工程图及其中所包含的产品各种结构信息与产品属性信息(结构信息包括产品装配信息、尺寸信息;属性信息包括零件材料信息等,即装配图和零件图里面的标题栏信息)、相应的工艺信息和工艺流程信息进行归类整理;最后,将设计结果一起构建在PLM数据库模型中,并自动产生产品结构树。
(2)根据PLM数据库中已有的产品工艺信息和工艺流程信息,对数字化车间整体产线设计进行了整体规划。共设计四条生产线:前两条作为发动机缸盖及缸体的机加工线,后两条分别作为车间总装配线和后整理线。机加工线、装配线及后整理线均通过已经设计好的加工、装配工艺进行布置各工序的机加工设备,主要有:数控机床、自动拧紧设备、智能试漏设备、缸体翻转机器人及带有HMI界面与数据输出接口的智能设备,所选机加工设备及装配设备满足于多种机型的要求,提升机加工线的柔性度;对于与产线相匹配的自动化物流线,使用自动化辊道、空中小车、上下料机器人、自动化转台、AGV车等进行整个车间机体和物料的自动化运送。最终在数字化虚拟仿真平台上验证这一套生产线是否实现小批量、多品种柴油发动机产品的生产。并且多次仿真实验及修改设计,最后购买合适的加工设备且安装设备。
(3)基于上一步所设计的生产线布局进行车间数字化建设,主要包括四个方面:
a.前两条机加工线由带有先进数控系统的格劳博机床组成,通过屏蔽性良好的网线将所有数控机床网口、分别接入到交换机上,再汇入工业PON的ONU(光网络单元)设备中,完成机加工线的DNC网络。同时有数据接口的智能化设备也以网口直接接入交换机或通过RS485转网口形式接入交换机,最终转接入ONU设备;
b.针对数控机床、智能设备无法自身采集加工数据且人工无法手工录入数据的位置,主要有:数控机床主轴温度、数控机床电机工作温度、机床主轴转速,通过自行安装传感器的方式采集这些数据,安装传感器对应有在线式红外测温仪、PT100螺钉式热电阻及温度变送器、霍尔传感器,最后接入到车间西门子PLC的S7-300系列并通过PLC主机自带的网口接入交换机及ONU设备;
c.在各种零件/物料众多的总装配线和后整理线使用RFID读卡器(型号:SIMATIC RF340R)进行装配的机体序列号采集,接入方法为b点中的方法;
d.使用人工辅助采集方式采集车间一些不易采集的数据,主要有:使用扫码枪扫码采集RFID读卡器没有成功采集的数据,使用手机上报车间的异常工况于维修部门等。
(4)使用工业PON(无源光网络)进行车间整体联网通讯,主要联网步骤有:先接入光网络单元(ONU),再接入光线路终端(OLT),最后接入到车间核心交换机进入数据中心。把车间各工位已采集至网关、PLC或者工控机的数据传输至车间的数据中心汇总,以解决老式车间数据无法采集或者数据采集实时性低的问题。
(5)通过在智能制造车间载入高实时性的MES系统且将车间的各种生产数据存入到MES系统中实现数字化升级柴油机生产车间的制造工艺与生产过程管理水平。同时,将ERP与MES系统集成实现车间级与企业管理层在生产过程中充分的交互。最终车间实现全面数字化升级,基于以上设计在某企业进行相应的实际应用已实现实际的效果,且现有传统车间与已经搭建的智能制造车间的对比图,如图3所示。
图3 老式车间与智能制造车间对比
根据对某柴油机企业智能制造车间与老式车间当前生产状况的分析与对比可知,智能制造车间总体的年产量相比老式车间提高了53%,生产成本降低了5%,生产效率提高25%,订单交付时间缩短20%,车间产能提高了1倍多。
看点
06
总结
面向智能制造的柴油发动机数字化车间构建与实施过程中,在传统车间的基础上优化了传统车间的总体架构、构建过程、设备配备及生产线工艺流程,实现了有效的提升。主要有以下三个方面:
1)在关键工序配备智能化设备以监控加工、装配、测试的实时状态,构建智能化装备集群,实现生产过程优化控制、数据实时采集及产品的质量控制;
2)整套数字化生产线通过使用生产工序精细化,关键设备模块化、通用化的方法,提高其生产的适应性与柔性;
3)采用智能制造技术,提升了工厂整体的制造工艺的数字化水平。新的柴油机生产车间构建策略与实施经验对将来柴油机数字化车间及国内离散型车间的构建与实施具有很大的借鉴性。
审核编辑 :李倩
-
智能化
+关注
关注
15文章
4884浏览量
55379 -
数字化
+关注
关注
8文章
8740浏览量
61780 -
智能制造
+关注
关注
48文章
5561浏览量
76337
原文标题:案例 | 潍柴动力数字化车间构建与实施
文章出处:【微信号:industry4_0club,微信公众号:工业4俱乐部】欢迎添加关注!文章转载请注明出处。
发布评论请先 登录
相关推荐
构建RFID数字化车场建设:从挑战到解决方案
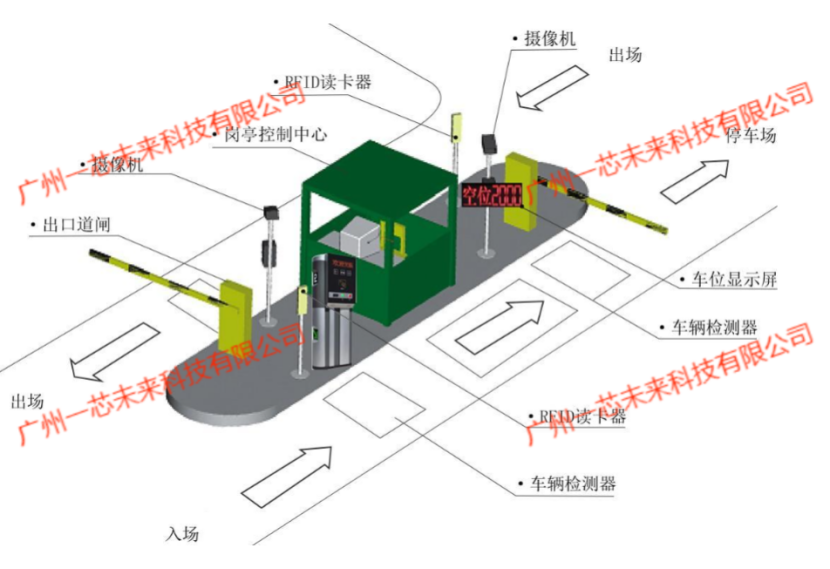
数字化挑战与机遇分析
数字化生产车间物联网平台是什么
高速数字化仪的技术原理和应用场景
数字化车间能为工厂带来哪些改变?
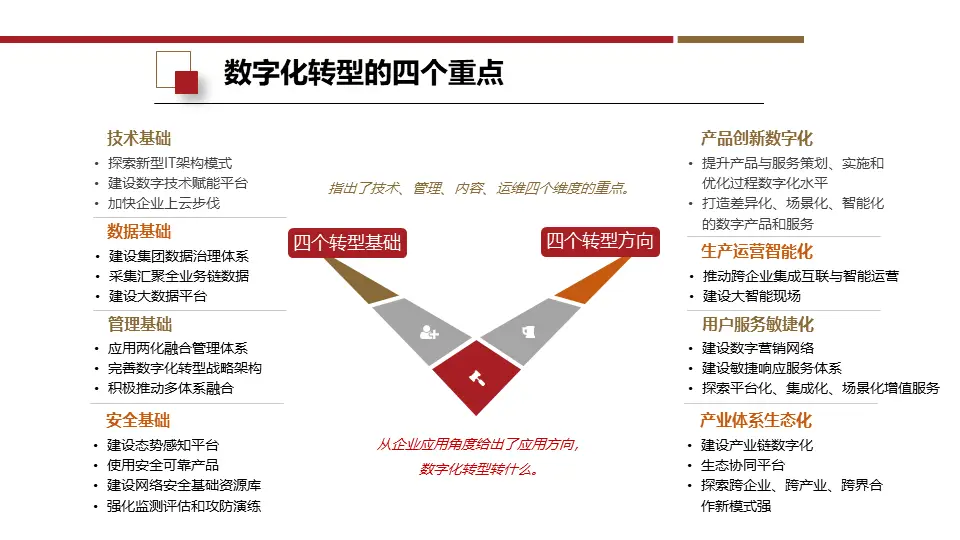
PLC智能网关如何助力车间实现数字化转型?
智能工厂和数字化车间的区别
印刷车间数字化监控管理系统解决方案
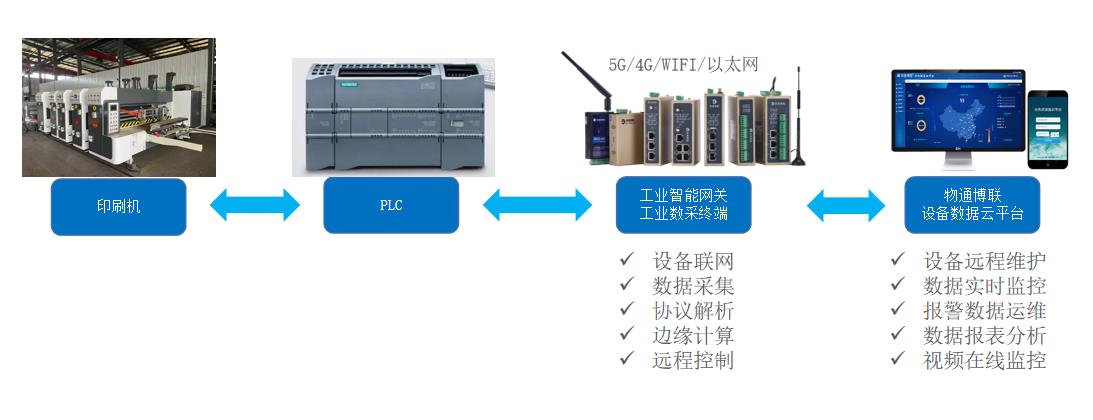
工业网关的数字化车间机械手和工业生产设备远程监控解决方案应用
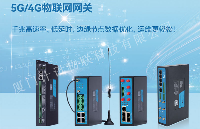
数字化车间管理系统意义?
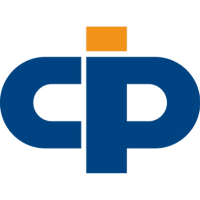
评论