本文重点介绍高密度 SiC 电源模块在电动方程式赛车中的相关作用,这是最先进和最具挑战性的比赛电动汽车 ( EV )。将详细介绍已成功用于电动方程式的 Hitachi ABB Power Grids RoadPak 电源模块。
电动方程式锦标赛始于 2014 年,在 2018 年获得 ABB 赞助后,目前被称为“ABB FIA 电动方程式锦标赛”,需要全面优化的功率半导体模块,例如最新一代的功率转换器。由于其竞争性质,Formula E 包括商业电动汽车所没有的特定要求。一个例子是所谓的攻击模式,几年前引入的目的是使比赛更加壮观和有吸引力。该功能可在车辆穿过赛道上的指定赛道时激活,在一定时间内为电机提供额外的 35 kW 功率。攻击模式的使用,通过蓝光指示在 Halo 设备上进行监控,
电动方程式要求
作为一项竞争性挑战,Formula E 主要侧重于在锦标赛期间实现 PM 的出色表现,因此,长期可靠性和成本等要求不如商用电动汽车重要。功率密度(或每单位表面的电流)、重量功率比和即时满功率可用性都是电动方程式的强制性要求。一个优点是逆变器的设计具有更大的灵活性,因为批量生产更加轻松要求和更手动的逆变器组装过程。而且,冷却液的选择和冷却特性可以更自由地选择,冷却系统的允许压降更高。
设计注意事项
与许多其他应用一样,考虑到 SiC 是一种很有前途的替代技术,Formula E 硅 IGBT 模块已逐渐被碳化硅 MOSFET 器件取代。作为以轻量化和提高效率为关键因素的应用,Formula E 可以从逆变器设计中 SiC MOSFET 的低损耗中受益。Hitachi ABB Power Grids RoadPak 1.2-kV SiC MOSFET 半桥模块,如图 1 所示,在小尺寸 (《70 × 75 mm) 中包含具有低损耗和高可靠性的最新一代 SiC MOSFET,以满足日益增长的需求电动汽车市场。
图 1 : Hitachi ABB Power Grids RoadPak 1.2-kV SiC MOSFET 半桥模块
面向电动汽车市场的 RoadPak 基线设计基于 8 个并行 SiC 芯片,在不改变外形的情况下可以增加到 10 个。这是最实用的解决方案,因为由于制造中的良率挑战,增加单个 SiC 芯片的活性表面受到限制(目前市场上的 SiC MOSFET 的活性面积小于 30 mm 2)。正如热模拟所证实的那样,由于相邻芯片之间的热串扰,并联连接几个 SiC 会导致更差的热扩散和热阻 (R th )的增加,需要仔细考虑。
SiC MOSFETs shall be properly selected based on their conduction losses (P cond ), switching losses (P sw ) at different switching frequencies, and, of course, reliability considerations. 传导损耗在限制的最大电流,它是MOSFET的(R的信道导通状态电阻的一个主要功能发挥的最相关的角色的RDS(on)根据下式导通期间)P COND〜- [R DS(ON) ×我rms 2。因此,选择具有尽可能低的 R DS(on)的 SiC MOSFET是强制性的,但必须考虑生命周期的权衡。基于 SiC 的 PM 提供的另一个优势是它们的低开关损耗,包括导通 (E on )、关断 (E off ) 和反向恢复损耗 (E rec )。然而,应该注意的是,开关频率越高,功率模块中的总开关损耗就越高。除了 R DS(on),最大电流取决于最大结温 T Jmax。因此,需要选择具有较高T Jmax 的器件并优先考虑热管理以降低模块的R th。而市场上大多数 SiC MOSFET 的额定值为 T Jmax150°C 至 175°C,当前 RoadPak 模块的额定温度为 175°C,并且趋势是将 T Jmax增加到 200°C。
与商用电动汽车不同,Formula E 汽车不愿意在极低的环境温度下运行,因此,冷却液可以在水-乙二醇混合物中加入较少的乙二醇,从而降低粘度和提高冷却性能。此外,粘度较低的冷却剂会降低系统中的压降,因此需要更小、更轻的泵。经过仔细研究,RoadPak 电源模块选择了采用优化针翅方式的串行单侧冷却,该解决方案可提供高冷却性能并易于集成到逆变器中。
除了冷却方案外,热阻还受设计选择的影响,例如芯片连接材料和厚度、基板陶瓷类型和底板设计。对于 RoadPak,选择了烧结贴片材料,因为它在功率循环期间具有更高的可靠性、更低的电阻和更高的热导率。与焊接相比,用于芯片连接的薄而致密的银烧结层(具有 320 W/mK 的热导率)实现了约 5% 的热阻降低。关于 RoadPak 设计的散热器/底板,由于铜具有更高的热导率(Cu 为 385 W/mK,而 AlSiC 为 180 W/mK)和更好的热- 传播效果。由于具有高热膨胀系数 (CTE),通常预计带有铜基板的模块在被动功率循环中的寿命较短。然而,通过仔细选择与整体功率模块设计的有效 CTE 相匹配的模塑料,在 RoadPak 设计中有效地补偿了 Cu 基板高 CTE 的负面影响。电源模块布局在电磁设计方面需要特别注意。为了达到高额定电流,并且由于 SiC MOSFET 的尺寸小,必须并联多个 SiC 器件。出现的非均匀开关会导致设备的振荡和寄生导通增加。这些不良影响还可能导致电流降额或开关速度受限,从而降低 SiC MOSFET 的低损耗优势。RoadPak 1. 电动方程式的 2-kV 设计得到优化并制造了模块,旨在达到最大可能的功率密度。经验证的 Z优化的 6Pak 设计的第 th曲线(对单位功率阶跃的瞬态温度响应)如图 2 所示。
图 2:经过验证的 RoadPak 模块的 Zth 曲线
由于 PM 热管理和整体冷却系统的改进,在图 2 所示的条件下实现了小于 83 K/kW的 R thmax。平均 Zth 和最热芯片 Zth 之间的微小差异表明均匀冷却的并行设备。上述低 R th允许在工作条件下(V DC = 800 V,f sw = 10 kHz,T in = 45˚C,CosΦ = 0.825,m = 0.95)的工作点 I rms 》 900 A,并具有干净的开关,这使 RoadPak 成为适用于要求严苛应用的基准 SiC 功率模块。
-
电动汽车
+关注
关注
156文章
12058浏览量
231025 -
功率模块
+关注
关注
10文章
463浏览量
45094 -
碳化硅
+关注
关注
25文章
2743浏览量
49002
发布评论请先 登录
相关推荐
碳化硅SiC在电动车中的应用
Wolfspeed助力捷豹TCS车队征战FE电动方程式上海站
碳化硅功率器件的工作原理和应用
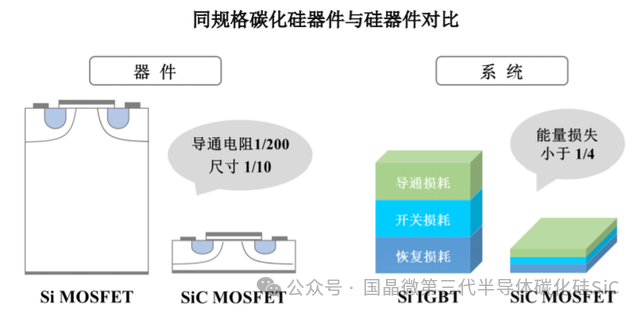
同星智能赞北京理工大学东风日产方程式赛车队(BITFSAE)
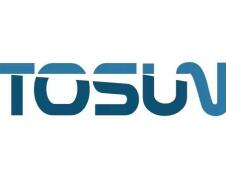
评论