整车线束作为汽车关键零部件之一,起到连通各个整车用电器的作用。当线束出现质量问题时,易导致的安抛、保安防灾类问题。作为线束制造和生产的供应商,在其质量管控过程中,必须将涵盖的质量要素进行管控,保证出厂质量合格,以及主机厂或终端客户使用过程中不出现质量问题。
建立整车线束质量管控标准化流程,使供应商从原材料进货检验,一直到上线生产制造,再到成品出库包装,每一个环节或工序都要进行严格的质量把关,做到不接收、不制造和不流出。
1 供应商端线束质量管控要素
1.1 汽车线束的主要分类
汽车线束主要分为前舱线束、顶棚线束、仪表线束、发动机线束和地板线束等,其中前舱线束构成最复杂,分支最多,功能最全。
1.2 线束生产工艺流程介绍
主要流程:来料检查→开线→防水套预装→端子压接→超声波焊接→热缩管处理→预装→总装→通电测试→外观检测→存储→运输至主机厂。
1.3 生产制造各工序管控要素
1.3.1 进货检验
此过程要控制单个零部件的入厂质量,供应商需建立完善的内部原材料认可流程。在认可阶段进行全尺寸、全性能、全功能的验证,每年要求分供方提交一次全性能试验报告。在专门的检验场地,具备检验资质的人员使用相检验工具(如:推拉力计、游标卡尺、硬度计、2D 投影仪、阻燃试验箱、电阻测试设备等)对零部件进行检验。如导线,检验项目包含线径大小、绝缘层厚度、导线电阻和颜色等;线束端子,重点检测关键尺寸、材料、型号、外观等;波纹管,检测阻燃特性和关键尺寸;热缩管,主要检测产品的壁厚、阻燃性及内径。
1.3.2 导线剥皮
为保证端子压接后的质量与外观,在压接前需建立导线剥头长度与对应端子相互匹配的数据库。针对剥线后剥头的长度及外观,需进行首末检验,并保存记录。不允许出现剥头处刀口斜切和剥头不完全现象。线径小于1.5mm2的导线剥头不允许断铜丝,1.5mm2以上的导线允许有8%以下铜丝断裂。
同时做完的半成品使用悬挂方式进行存放和转运,不允许有堆压和拖地现象。剥头完工后应按照一定数量把电线捆扎成把,同时必须使用专用的工装和护具进行保护,如护线杯、护线套等。不允许使用保鲜膜、保鲜袋、塑料纸杯等非常容易造成线芯损伤的物品。导线剥皮作为第一个工序,对后续的质量有关键作用。
1.3.3 防水套预装
选用与匹配线径的防水套,在装配前,防水套不可以出现飞丝、铜丝断裂破损以及铜丝被拧紧现象。在装配后,不可以发生防水套松动和自动脱落的现象。防水套在整个线束中起到绝缘和防护进水的作用,所以必须保证防水套装配到位。
1.3.4 端子压接
①模具管理。压接模具必须要进行剖面验收,针对易损的压接钳口必须配备足够数量的备件。模具在使用前要进行日常开班点检,模具及压接钳口要进行点检台帐记录,且记录清晰。记录内容包括:模具使用的次数、钳口使用的次数、钳口和模具维修信息、保养信息、更换信息等。
模具使用结束后应及时清理,并将信息维护到台账内。入库后应按照库位定制放置,因此要使用较为松软的物体保护钳口,防止损伤。值得关注的是在生产完工后,模具上应保留最后一个端子压接的样品。
②过程管控。选择使用气动模具(自动或半自动),以保证线束端子在送料过程中放置位置正确,且一致性良好,满足质量要求。端子压接需确保人员能力满足和设备的稳定性。因此要提前进行端子压接人员的培训,提升操作工熟练度,并进行考核鉴定,以提高压接生产的一致性。同时也要进行设备cpk 分析,大于1.67才表明过程稳定。如图1为端子压接示意图。
图1 端子压接
针对压接后半成品的存放,采用定量捆扎且悬挂的方式,不可以堆放。明确端子压接后要进行的常规检测项目,如端子压接高度和宽度测量、拉脱力测量、端子剖面检测、接触电压降检测、外观检测等。
1.3.5 超声波焊接
超声波焊接在各个工序需有明确的操作指导书规定标准化的操作流程,用以指导员工操作。设备设定过程参数,也要有专人负责,如焊接的温度、焊接的时间、焊接后的冷却时间、焊接后尺寸等,同时以上参数作为日常开班点检内容进行确认和记录。焊接设备必须具备压力监控装置,可识别漏线、绝缘皮误放入等缺陷。焊接完成后不允许出现以下问题,如飞丝、铜丝弯折等现象。如图2所示焊接后两端露出的铜丝长度、拉脱力等需测量及记录,同时超声波焊接使用的导线线径差不得超过1mm2。
图2 超声波焊接
1.3.6 热缩管处理
不允许直接使用热烘枪处理热缩管,必须使用履带式和往复式热缩机,同时机器参数设定需和热缩管规格型号相匹配。热缩管装配过程控制的参数需设定完整:如温度、时间、外观等要求。热缩后不可出现以下问题,如铜丝外漏、胶量不足、导线线皮破损、导线铜丝刺穿热缩管等缺陷。热缩管是对线束的一种防护,因此不可以出现破损的情况。在转运过程中,一定要注意工装金属不可外露,必须包覆好。
1.3.7 预装
在生产线布置时,各个总装线的附近应设置预装工序的区域,其目的就是包装产品顺利装配。在装配时,必须配备专用预装工装。预装前要仔细核对工艺指导文件上规定的护套型号和导线种类,要检查护套及电线、端子压接的质量,特别注意防水插件盲堵装配要到位。针对护套的预装,护套的长度和颜色必须检查,不可以使用错误。
1.3.8 总装
制作线束总成工装板,以保证各个接插件、卡扣及附件定位准确,将附件型号、装配方向在工装板上体现,保证操作工在实际操作过程中可以将扎带及卡扣装入定位模块,确保防错有效。员工在扎带捆扎时,要保证位置准确。
捆扎后扎带不可以串动,扎带尾部保留3~5 节,且剪切圆滑。对以波纹管方式的包扎时,需在波纹管两端导线上用胶带缠绕3~5圈后再固定波纹管。包扎完成后波纹管不允许出现脱落和位移现象。原材料和半成品需定点定量存放,工位挂线料架的高度应根据半成品长度制作,不允许出现端子落地、物料堆积的现象。针对关键位置的卡扣,需进行自检划线。带分支走向的产品,同时需在工装板要体现图纸版本信息。
1.3.9 通电测试
制作设备导通测试工作台如图3 所示,检测的项目包含:电性能、防水性插件的密封性、导通性,方向是否使用正确、插件二次自锁是否装配到位、端子是否退位等。此工序的检测人员,需设定指定人员和人员权限。对检测人员要进行培训和考试,经鉴定合格后再上岗工作。导通测试时,所有插件接好后必须处于正常的自然放置状态,不能使用人员手动挤压插件。作业前和作业结束后,导通台内传感器、探针、测试模块都需每日进行点检,不允许出现探针歪曲、不回弹、测试模块损坏等问题。当出现此问题时,要及时上报对应管理人员和维修人员。
图3 线束导通台
1.3.10 外观检测
需设定专用区域用于检验,规划待检区、合格品区和不合格品区。设置封样件或者线束数据图,最好是1:1 大图(需体现图纸版本信息),目视在现场,并与总成工装板和导通检测台版本号一致。此工序检测内容含有:对比确认插件型号安装使用是否正确(区分不同配置)、各个插件端子有无损坏、附件有无漏缺损、线色和线径是否正确、轧带捆扎是否牢固、绞线及防护胶带缠绕样式是否正确、接插件是否符合等。检测完成后,在电检合格标签上盖章确认,并粘贴在产品上,并将合格的产品放置在转台器具上。
1.3.11 存储
存取区域需要注意通风、防潮和防电,必要时进行温湿度的控制。成品库区应设置4个区域:呆滞件存放区域、试装件存放区域、不合格件存放区域和合格件存放区。不合格件使用红色标签,呆滞件、试装件可用黄色标签,合格件使用绿色标签。同时需要进行批次管理,使用批次管理系统,有效执行零部件的先进先出管理要求。
2 结束语
线束在整车系统中的关键作用毋庸置疑,对于其复杂的制作过程,每一个制作工序都应该值得重视。不可盲目的追求进度,应充分识别和控制各个工序的要素。仅以此文将各个过程或工序的主要管控要素进行展示,便于供应商更好地做好质量管控的要求。
-
超声波
+关注
关注
63文章
3014浏览量
138350 -
数据库
+关注
关注
7文章
3794浏览量
64362 -
线束
+关注
关注
7文章
973浏览量
25977
原文标题:整车线束生产工艺质量管控要素分析
文章出处:【微信号:焉知连接器,微信公众号:希骥知芯】欢迎添加关注!文章转载请注明出处。
发布评论请先 登录
相关推荐
救援生命线:单北斗智能手持终端在应急响应中的关键作用
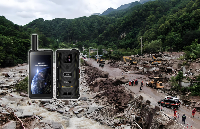
单北斗有源终端产品在智慧交通系统中的关键作用
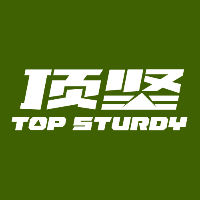
工控机在现代工业中的关键作用
应用DMAIC降低汽车线束开线工序质量损失
行星搅拌在锂离子电池液中的关键作用
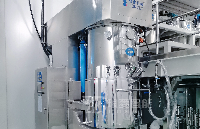
M8_8pin接头在电子设备中的关键作用
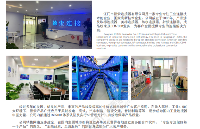
评论