产生失误的原因基本可归为三大类,即人的原因、方法原因和设备原因,其中人为失误所占的比重很大,这是很多质量学者和公司管理层很早就认识到的。
长期以来,一直被各大公司沿用的防止人为失误的主要措施是“培训与惩罚”,即对作业者进行大量培训,管理人员每每劝戒作业者工作要更加认真和努力,确实,通过培训,可以避免相当一部分人为失误,比如由对过程/作业不熟悉,缺乏工作经验、缺乏适当的作业指导所导致的失误。但由于人为疏忽、忘记等所造成的失误却很难防止。
因此,制造企业对防错技术有着广泛而迫切的需求,“防错”的概念对产品设计和制造过程设计很有实际意义,日本许多工厂大量采用非常简单而实用的防错装置,并将其干百次的反复应用,日复一日长期坚持,出现了质量奇迹:每百万零件不合格数(PPM)下降至个位数甚至为零,产品质量显著提高。
本文主要介绍防错的五类方法和五大原则。
01设备上的防错装置技术应用
在汽车配件的制造过程中,设备上的防错装置技术应用主要有以下几类:
(1) 定性的防错通过图像识别技术,光电、限位、接近开关的逻辑控制技术等来完成防错,比如:
——即时摄片比较:区分装配零件的方向是否正确;传感器感应检测:机加工自动线根据不同产品型号的外形变化,传感器将感应到的信息反馈给后面的加工工序,使后面的工序调用对应的加工程序,实施相应的加工内容;
——硬探头:检测零件的不同型号,实施不同的装配或加工工艺,如用探头探测零件的外形,实施不同的装配,如硬探头探测缸孔,区分3.0L或3.4L缸体;
——导向挡块:区分零件的输送导向;
——光栅防错:通过光栅的检测控制,达到工件是否摆放到位;
—— 夹具防错:控制装配零件在夹具上的摆放是否到位来防错。
(2) 定量的防错通过测量探头感应或经过气电转换的测量技术(气体流量转换成电量)来达到防错的目的,如:红宝石探头探测数据反馈:通过红宝石探头探测已压装气门座圈的内径来区别零件是3.0L还是3.1L汽车配件的缸盖; 泄漏测试:汽车配件如缸盖、缸体的油道以及水道的在线测试等,控制泄漏件流入下道工序;随线检具直径测量:这在机加工自动线中镗孔及铰孔后的工位应用较广,达到100%控制不合格产品的出现;扭矩控制:汽车配件如很多螺栓固定的拧紧程度均通过扭矩枪来控制。
02物料防错
工件盛放器具的防错:加工完成的产品盛放实施防错技术,有方向性地定置摆放,预防工件相互碰撞,保证加工零件的表面质量;色标防错:装配区域零件的盛放料架,使用色标防错。
03人工防错
(1)建立标准的操作SOS:如加工过程中的成品、待制品、待处理品、料废、工废等下线零件必须马上按照各类零件的处理规范挂上不同颜色的识别标签,刀具设定正常使用耐用度,防错装置建立TPM、PM维护保养制度等;
(3)工件目检、测量防错:操作工按照检验频次目检、测量工件加工中及毛坯本身存在的缺陷,把不合格工件剔除出来,在本工位上使其离线。
防错技术的等级
根据防错的效果,防错技术可分为如下三个等级:
(1) 不制造缺陷的防错,即不可能制造出坏零件,可能损坏的零件数为零;
(2) 不传递缺陷的防错,即不可能将坏零件传递到下一工位;
(3) 不接受缺陷的防错,即后续工位不接受坏零件。
防错技术的理想状态是不制造缺陷的防错,这是最主动、最经济、可预见并防止错误的控制技术。如加工前的探头探测、导向限位、传感器感应等的防错就能达到不 制造缺陷的目标。
防错装置的验证
使用新的防错装置时,必须进行功能准确率的验证,预防差错率。只有通过PPAP(生产件批准程序)方式的验证,方可使用。
防错系统的验证
防错系统的正常运作是实施、验证、维护的过程,在其应用中必须保证:
(1) 确认防错系统运转正常实际生产中,对防错装置必须进行定期的维护与验证。如:缸体、缸盖的泄漏量检测,对泄漏测试机每天必须进行工件的泄漏量核定与验证;同样,生产线的各种防错装置均需进行定期的维护验证,确认防错功能正确运作。
(2) 确认人为因素处于受控状态
对防错系统的验证过程,验证检查记录必须存档,如有差错必须采取必要的措施进行规范的修正;实施防错验证的操作工必须确保操作工经过培训并且培训内容记录已存档;保证防错系统达到预期的检验能力,验证流程有效地按照计划处于受控状态。
04防错的五类方法和五大原则
有5种类型的错误防止方法:
失效-安全装置、传感器放大、冗余、倒计数和特殊检验、控制装置。
介绍如下:
1. 失效-安全装置(Fail-safe devices)
互锁顺序:保证在前一个操作顺利完成前,下一个操作不能开始;
预警与中断:将在过程中出现法场情况时被激活;全部完成信号:将在全部补救措施完成后被激活;
防傻型工件夹紧装置:保证工作的一部分只能被固定在一个位置;
限位机械装置:用来保证工具不能超过某一位置或数量。
2. 传感器放大:用来增强人的视觉、听觉、嗅觉、触觉、味觉和肌肉力量,如:光学放大、多重视觉和听觉信号、监控危险过程的遥控以及用图片代替文字等等。
3. 冗余:用作保证质量的附加措施。
多重确认码:例如防止产品混淆的条码和彩色码
冗余措施和批准:需要两个人独立工作;
审核评审和检查程序:保证计划被跟踪;
验证设计:利用特殊设计,如:观察孔,来确定产品或过程是否在令人满意的执行;
复合测试台:可检查很多特征,如出现在高速生产线上的特征。
4. 倒计数
组织读出数据和信息过程来让错做程序保持并行,以便检查每一个步骤,如航天器发射,它还在手术操作和焊接中被有效应用。
5. 特殊检验、控制装置:如计算机检查信用帐号,无效帐号被拒绝,及时的反馈被提供。
有5个错误防止原则:
消除(Elimination):将可能错误消除在过程和产品被重新设计的过程中;
替代(Replacement):是进入更可靠的过程的一个变更;
简单化(Facilitation):将过程运行变的更简单化,也更可靠;
检测(Detection):使错误在下一步操作前被发现;
缓和(Mitigation):是将错误的影响降低到最低。
审核编辑 :李倩
-
传感器
+关注
关注
2551文章
51156浏览量
754069 -
光栅
+关注
关注
0文章
287浏览量
27524 -
图像识别
+关注
关注
9文章
520浏览量
38279
原文标题:防错的五类方法和五大原则是哪些?
文章出处:【微信号:线束专家,微信公众号:线束专家】欢迎添加关注!文章转载请注明出处。
发布评论请先 登录
相关推荐
超五类网线适用场合
超五类网线与五类网线区别
超五类非屏蔽网线和超五类屏蔽网线的区别
怎么查看是不是超五类网线
超五类网线怎么识别
分布式存储系统的七大原则之二:区分环境数据与业务数据
职业健康在线监管系统五大功能
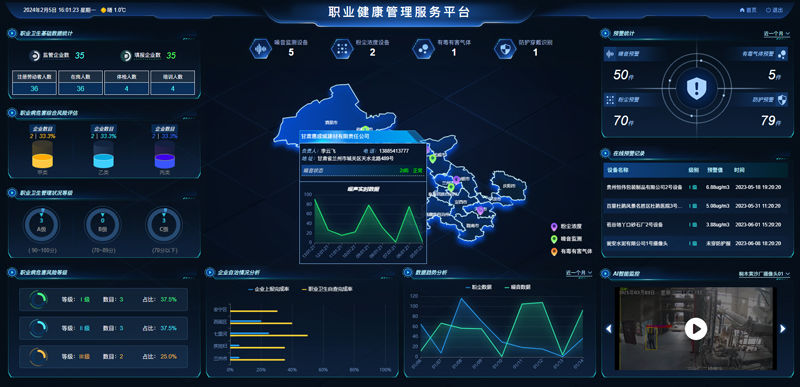
评论