摘 要
作者总结十多年来在汽车电子工厂从事铣刀式分板机(这里说的是带毛刷式的)编程与工艺实践的心得体会,针对目前工厂中要求低周期时间(Cycle Time)、高分割精度、低应力、低粉尘、低振动、低成本等情况,结合设备、夹具、铣刀、电路板拼板设计、电路板基材、成本投入等现状,初步探析如何从编程的角度最大限度地满足工厂及客户要求。
一、前言
随着最近几年来国内汽车电子行业的不断兴起,行业竞争日趋白热化,拼产品质量和价格成为大势所趋。为了提高产品的质量,很多时候不得不购买高性能的设备,而高性能的设备往往意味着高昂的价格甚至高昂的维护。高昂的设备价格又造成产品的价格的提升,而产品价格的提升又造成产品在市场上的竞争力的下降。
对于分板工艺,以半自动设备为例,基本配置的高性能设备本身就有近80万人民币,如果配置稍高些就达130万人民币。再加上除尘设备也要20万人民币至40万人民币不等,总体价格就不菲了。考虑到周期时间可能需要配置额外的设备,那线体总价就更令人瞠目了。
毫无疑问,分板工艺需要经济效益最大化。也就意味着也用最小的投资创造最大的价值。在现有设备已定的情况下,如何提高产出(包括数量及质量)、减少成本成了企业要面临的问题。
根据笔者十多年来从事分板工艺的经验,很多时候编程的作用被低估了。一个好的程序,可以达到一个理想的周期时间,也能达到一个理想的分割边缘轮廓及应力。甚至能对粉尘及振动有特别要求的产品有一个很好改善,同时可以提高铣刀的寿命。而编程本身可以由工厂技术人员完成,是不需要额外投资的。也就是说通过好的程序可以减少对设备的依赖(不同品牌、型号及配置),可以减少夹具(不同的设计)的限制,可以提高产品的质量,可以增加铣刀的寿命,从而最终实现低投入高产出、产品的成本降低,在市场上的竞争力提升。
二、分板工艺编程现状概述
目前有些企业人员流动频繁,资深的工程师凤毛麟角,很难会有技术的沉淀。对于分板机的编程能够独立完成已经相当不错了,更别谈做得尽善尽美了。遗憾的是客户对产品的要求越来越高,而企业为了减少成本会购买低价的原材料,为了提高产出,需要设备提高运行速度,工艺的管控难度大大提升。而为了减少人力成本,会接收一些学历、技能不高的操作工甚至采用外包工,这对设备维护和使用无疑增加了不少不确定因素。加上一些工厂管理不善,造成设备的使用与维护处于一种很危险状态。于是各种质量问题、设备停机等纷至沓来。
好的分板程序,需要考虑由于设备可能会的失效造成的潜在风险(停机、质量、成本等),需要考虑设备的长期使用稳定性。可惜的是,能明白这些并且做好的并不多见。
三、分板编程经验汇总
首先,为了保证分板的精度,原则上分板路径坐标及基准点(fiducial mark)坐标取来自产品图纸,或由软件自动生成或由编程者手动输入。
尽量避免通过视觉系统教导(teach)来生成,因为产品本身有误差(一般误差±0.125mm),产品放在治具中在会有水平度和角度等误差,对于复杂图形(如多圆弧相连图形)的连接点起始点的确认也会存在误差,这些都会造成分板路径及基准点坐标不准确,对于有精度要求的分板工艺控制是相背离的。
由于本文阐述的是毛刷式分板编程,一般为了避免元件被毛刷或切割头损坏,一般工作头面向电路板辅面(也就是包含最简单、数量最少元件面)。
3.1 半自动分板机(也叫离线分板机)
半自动分板机指板子分割由设备XYZ轴驱动主轴按程序及PLC指令自动完成但板子的取放由操作工手动完成,所以设备不能和轨道流水线对接,又称“离线分板机”。英文叫“Offline Depaneling”或“Stand Alone Depaneling”也称“Semi-Automatic Depaneling”(半自动分板机)。具体操作步骤是操作工把待分割的拼板放入夹具并固定好,然后把通过按钮或手动把夹具/工作台送入机器,然后机器自动完成板子分割后自动退出,操作工把分割好的放入下一站WPC或作为在制品放入Tray盘。
以下以毛刷式分板机(上集尘)为例,此设备的特点是主轴在电路板上面,铣刀四周由毛刷密封。
3.1.1编程之除尘取向
(俯视图1)(剖面图)
(俯视图2)(剖面图)
备注:假设以上每个子板的四个角都有预分割(这里指来自PCB原材料的预分割)或下刀孔;
注意:只有预分割区域或下刀孔等非板材区域才可以下刀,否则会有板子分层风险。
经验总结
根据分割时粉尘在铣刀行进方向的右侧,靠近拼板边缘部分要逆时针方向分割。
铣刀行进方向的右侧朝向不容易积累粉尘的元件或对粉尘不敏感的元件,如片式元件(chip component)等。不可朝向容易积累粉尘的元件(一般为大元件如铝电解电容、连接器等)或对粉尘敏感的元件(如IC、连接器等)。
3.1.2 编程之周期时间取向
由于分板机关注于铣切工艺,X、Y轴一般采用高速的线性马达可达1500 mm/sec, Z轴一般只用于在空板的地方下刀或打孔测试而不用于台阶式铣刀,故Z轴精度和速度都不需要太高,速度一般20–50 mm/sec,因此要减少Z轴下刀以便节省分割时间,通常铣切路径走近似“8”字形路线来实现。
3.1.2.1 不考虑MES制造执行系统,主要用于产品追溯,多用于汽车电子产品)中打叉板或报废板不分割,以下面板子为例:
以上分割顺序分9步,其中黑色字体部分1~6为一次下刀,红色字体7~9为第二次下刀。
3.1.2.2 考虑MES中打叉板或报废板不分割:
以上分割顺序分10步,其中黑色字体部分1~2、3~4、5~6、7~8分别4次下刀,剩余9、10为第5、6次下刀。
经验总结
1) 前4刀在联MES时,当有打叉板时可以跳过。如当第PCB1为打叉板时5~6可以跳过不分割。但是如果第5步和第4步连接在一起为一刀或6和7连接在一起为一刀,就无法实现区分哪一刀属于哪块板子,也就无法跳过PCB1而不分割。
2) 5~6属于PCB1专属部分,可以用于区分它与另外3块板子的区别,当它打叉时跳过不分割,也可以独立把PCB1留在边框上。
3.1.3 编程之分割质量取向
此分割质量包括分割轮廓精度与粉尘,由于粉尘问题比较特殊,而且在不同类型设备(半自动和全自动)中表现不一样所以独立阐述,此处质量问题重点讨论分割轮廓。
3.1.3.1不考虑MES中打叉板或报废板不分割,以下以抽屉式分板机为例,板子方向为分板放置方向。
经验总结
1)对于拼板中每个子板单个分割会达到好的板边质量;
2)每个子板的最后一刀落在板子结构相对结实的地方,防止收刀时板子被拉动而影响分割质量;
3)一般来讲,拼板要从左往右,从下往上。同时每个子板以逆时针分割,当然,这只是一个大致的规律,具体还得视情况来调整。如步骤1的下方如果有积累粉尘的元件或对粉尘敏感的元件可以调整分割方向。
4)尽量避免铣刀从子板上方通过,防止铣刀或毛刷损伤到元件。有时铣刀会掉刀或程序设定抬刀高度不够等,当铣刀从子板上方通过时会造成元件损伤。还有些元件会有带盖子的(如电感)或易变形的(如某些弹簧类元件),当毛刷从元件上方经过会损伤到它。
3.1.3.2考虑MES中打叉板或报废板不分割。以下以抽屉时分板机为例,板子方向为分板放置方向。
经验总结
1)在联MES时,铣刀所走路径仍然依照3.1.3.1的规律,不同的是要考虑相邻板子公共边(如第1和11步,第4和6步,第5和15步,第12和14步)。
2)特殊情况,有时在最后一刀(如本例中第16步)收刀时板子会被带起来,这一般是因为毛刷把板子吸起来造成的,包括联或不联MES的任何情况。分析进一步的原因,首先在设备选型最好选择毛刷和铣刀分离控制式的设备(即毛刷独立控制型的,如Grohmann的PRM100等)其次程序的制作也有很多技巧。固然有些设备有关闭吸尘器之功能 ,但是收效甚微而且还会造成周期时间(CycleTime)变长、粉尘在收刀时有堆积等问题,这是由于设备残留的真空无法在短时间内消除造成的。在实际运用中,最好的方法是把最后一刀先抬刀并保持毛刷下压待毛刷脱离板子时再抬起。如果设备有毛刷独立控制功能,可以在子板分割完成后先抬刀至毛刷脱离分割后的子板再抬毛刷效果更佳。
3)综上所述,联MES与不联MES的区别主要在于相邻板子的公共部分要分割两次,这样当有打叉板子需要跳过时另外一块板子也能得到分割。同时每个子板要有独立部分,不可与其它子板共用,是为了保证有打叉板跳过时仍能独立把当前子板留在板边上而不被分割。考虑到业界不联MES的多,以下内容就不再考虑联MES的例子了。
3.2 全自动分板机(也叫在线分板机)
在自动分板机指板子分割由设备XYZ轴驱动主轴按程序及PLC指令自动完成,每个子板的固定和放置由机械手完成或者机械手驱动夹具(此运用很少,下文就不再考虑了)完成,拼板分割及分割后的子板的运输均是在轨道流水线上完成,又称“在线分板机”。英文叫“Inline Depaneling”或“Fully Automatic Depaneling”(全自动分板机)。
具体操作步骤是物料员把料架(magazine)中待分割的板子放入上板机(loader),上板机把待分割的板子传送到分板机中,分板机分板后把子板放入工件托架(WPC)中传送到下一个工序。或者放到托盘(Tray)中作为在制品(WIP:Work In Progress)。
以下以毛刷式分板机(下集尘)为例,此设备的特点是主轴在电路板上面,铣刀四周由毛刷密封。
3.2.1编程之除尘取向(Dust Removal Orientation)
经验总结
1)根据分割时粉尘在铣刀行进方向的左侧,靠近拼板边缘部分要顺时针方向分割。
2)铣刀行进方向的左侧朝向不容易积累粉尘的元件或对粉尘不敏感的元件,如chip component片式元件等。不可朝向容易积累粉尘的元件(如铝电解电容、连接器等)或对粉尘敏感的元件(如IC、连接器等)。
3.2.2 编程之周期时间取向
由于自动分板机要使用夹爪,而有时对应产品没有预分割,或者预分割不充分无法先用夹爪夹住待分割的产品,往往需要对设备先进行分割然后再下夹爪。另外考虑到每个子板分板(multi-gripper工作原理类似,此处也不讨论了)后夹爪把产品放到下一工序(WPC或tray 盘等)并返回待分割产品也需要时间,在此期间为了提高设备利用率也会先对产品进行部分预分割,待夹爪返回后夹住产品继续完成剩余工作。
以下就以产品没有预分割(或预分割不充分无法先下夹爪)和预分割充分为例来讨论实际工作中如何处理问题的,考虑全自动分板分割顺序相对复杂,以下就以8拼板来举例。
3.2.2.1 产品没有预分割或预分割不充分:
经验总结
1)其实有时也无法完全把周期时间取向与质量取向分开,因为无法完全不考虑分割质量;
2)由于这个产品的特殊性,如果从拼板边缘分割如PCB7分割,剩余的PCB5、PCB3、PCB1由于重力作用会下沉,在下夹爪前板子就向下倾斜造成潜在的质量风险。要从拼板中间逐步向两边分割,这样就能尽量减少分割后剩余板子下沉而造成的质量隐患。
3)由于全自动分板机只能要一块板一块板地分割(multi-gripper稳定性相对差,维护困难,使用的少,本文就不阐述了),因此为了减少周期时间,整体要一个方向(顺时针或逆时针)分割。
4)拼板要从长度方向先分割,然后再从宽度方向完成。
5)为了下夹爪,需要在夹爪设计方向(一般夹爪为镜向的一对,一边2个夹指,共4个夹指),所以下夹爪前需要把夹爪的位置留出来,或在分板机上完成或在PCB来料时完成。
3.2.2.2 产品有充分预分割
经验总结
1)此分割顺序与3.2.2.1 产品没有预分割或预分割不充分大致相同,所不同的是下夹爪的步骤,整体分割顺序更细化了。
2)由于每个子板有两个分割点,为了减少周期时间可以在夹爪拾放期间多分割一部分。此拼板分割点多,以上顺序只是一个例子,由于不同产品放置位置、夹爪机器手运行速度、分割速度不一样、产品的差异等,可能实际运用当中会有差异。一个原则是让设备利用率最大化,尽量让铣刀不要停下来,利用夹爪拾取过程来多分割一部分。
3.2.3 编程之分割质量取向
3.2.3.1 产品没有预分割或预分割不充分
经验总结
1)此分割顺序与3.2.2.1 产品没有预分割或预分割不充分大致相同,因为它也考虑了一定的质量问题。
2)其实以上分割顺序并非完美,有时做一个完善的程序不太容易甚至不太可能即使只为质量取向的,这时可以根据实际情况做个取舍。比如PCB3中是主要考虑粉尘问题,当铣刀从第3步到第4步过程中,如果有特殊元件(如铝电容类高元件或弹簧等易损元件),可能会被毛刷或铣刀损伤到。此时可以通过加大抬刀距离、抬毛刷等方法来解决,或者如果产品粉尘不严重(如高元件并不高或不容易沾染粉尘或者后面有清洁工艺可除尘等),可以考虑调整第3、4步的分割方向。其它分割步骤也有类似情况,要根据实际情况进行调整。
3.2.3.2 产品有充分预分割
此问题相对复杂也很有代表性,本文用两个工作中非常典型的例子来阐述,以便读者理解。
例1:
经验总结
1)此分割顺序与3.2.2.2 产品有充分预分割相同,因为它也考虑了一定的质量问题。
2)对于全自动分板设备,不像半自动设备板子有夹具固定相对很牢固,全自动设备用夹爪固定板子相对稳定性差一些。因此要注意在夹爪设计及夹爪位置调整好的基础上,下夹爪前板子要尽量平整。要做到这一点,产品要相对边预留有分割点,如果是对角有预留分割点就更好了, 这样板子在下夹爪前的支撑会更好些不容易变形。
经验总结
每个产品的最后一刀很重要,最好是向着最近的夹指位置分割,或者说最后一刀收刀点要在板子固定很好的地方,以下图中拼板中最后一刀为例来说明。
例2:
下面板子由一台预分板机(Premilling)和一台终分板机(FinalMilling)完成,板子长400mm,宽度为200mm。
经验总结
1)预分板机和终分板机都是由PCB6PCB3PCB5PCB2PCB4PCB1的顺序来完成 ;
2)“0.x”属于子板间公共边,要先分割开来,这样可以使整个拼板应力释放,以免夹爪夹住产品分割时由于应力累积而造成板子位置移动或不平而影响分割质量。
3)由于板边框中间连接“筋”很细(最细处小于2mm)又很长(400mm),那边以PCB1为例,先分割左下角与弱“筋”连接点再分割右上角与边框连接的强点。同时,切割方向要走顺时针方向,这样由于切割向力板子如果有移动只会“多肉”(切的少留的多)不会“少肉”(切的多留的少)或露铜。
四、结束语
以上是针对分板工艺的经验总结,由于不同设备编程方法也不尽相同,所以具体编程步骤本文就不涉及了。简单来讲,DXF格式的panel drawing是一种常用的编程数据来源,或把它导入软件生成分割坐标点,或通过CAD来测量相关分割路径坐标数据。
为了以后维护的方便,建议使用直接坐标,最好不要使用铣刀补偿的间接坐标,否则可能会影响周期时间,阅读起来也不直观。基准点(fiducial mark)最好先在拼板边框对角,以更好的补偿板子分割位置。
审核编辑:刘清
-
plc
+关注
关注
5010文章
13272浏览量
463072 -
电路板
+关注
关注
140文章
4952浏览量
97694 -
分板机
+关注
关注
0文章
39浏览量
10437
原文标题:铣刀式分板机编程初探
文章出处:【微信号:actSMTC,微信公众号:actSMTC】欢迎添加关注!文章转载请注明出处。
发布评论请先 登录
相关推荐
TAS5630如何才能最大限度地减少电压失调,或者调节为0?
最大限度地减少TRF7964A和TRF7970A省电模式下的电流消耗
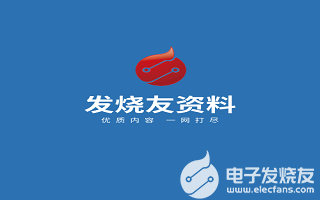
最大限度地减少TPS53355和TPS53353系列器件的开关振铃
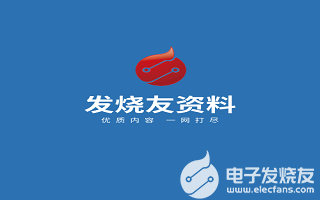
最大限度地提高GSPS ADC中的SFDR性能:杂散源和Mitigat方法
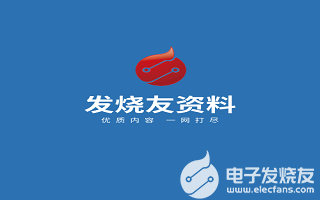
TIDA-050027.4-具有灵活分区以最大限度实现节能的多轨电视电源 PCB layout 设计
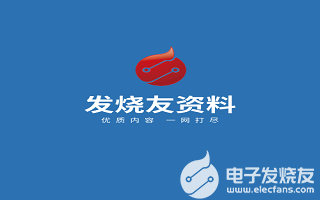
如何最大限度地降低差分测量误差?
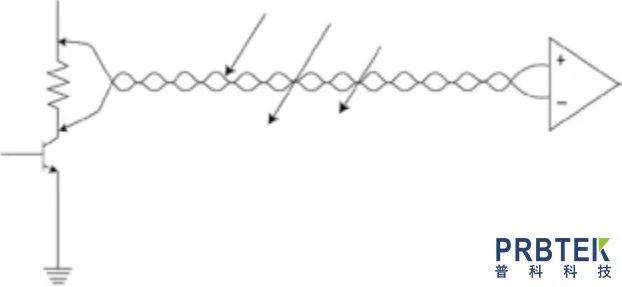
如何使用低电容探头最大限度地减少探头负载
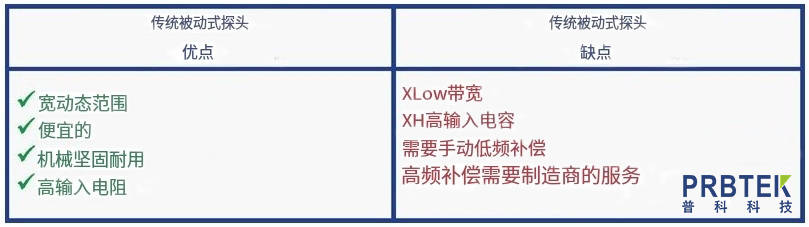
PCB生产为什么要使用PCB分板机?
用于并行采样的EVADC同步转换,如何在最大化采样率的同时最大限度地减少抖动?
Wi-SUN 可最大限度地提高太阳能跟踪器的性能
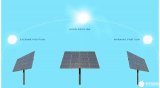
评论