昨天在朋友圈看到一个图,并借用2017年IBM的一个硅光耦合的图来解释“无源封装”技术
我再写一下什么叫无源封装,或者叫无源耦合。在合集2020第76页有过一些简单的描述。
在我汇总的一个硅光行业报告中,有较为详细的分类解析。
我自己来恢复一下这个图,这个图的含义包括了电学、光学和热学
电学:硅光芯片和两个浅蓝色的模拟电芯片的电信号连接内容,需要3D堆叠封装,与高频信号损耗有关。
光学:光纤阵列宽度,耦合容差,以及硅波导的SSC模斑转换,IBM在2017年版本的基础上2020年做了优化,改为倏逝波耦合,结构写在硅光行业报告的第187-188页。
热学:对接耦合需要考虑Z轴的一致性与损耗。
在硅光芯片上刻蚀V型槽,能起到三维限位的作用,V型槽的宽度间距和光纤间距一致,产业链大约分为两大类,一大类是250μm,另一大类是减包层后的特殊间距,约在160μm左右。
优化后的倏逝波耦合,要有一段扇入扇出,硅波导间距不用V型槽,而改为50微米间隔,用于降低Z轴翘曲、对准精度、耦合损耗等几个方面的影响。
只看一个光纤,通过V型槽对准硅波导的SSC转换,精度很高。
如果是阵列,就比较麻烦。
早期,V型槽是玻璃基板刻蚀,与硅波导做耦合。毕竟是两个器件,XYZ以及倾斜度,对于整体的耦合损耗控制比较难。
用“无源”耦合方式,行业报告的第194-195页,可以通过边沿两侧的波导,在硅光芯片不通电的情况下,可进行前期对准。通过两边的光纤,一个外部耦合光源进入,结合硅的环波导,继而从另一侧光纤输出,在耦合设备处放一个探测器,通过探测器的电流峰值状态,就能知道耦合效率的最高点。
如果考虑到多个光纤的耦合损耗分布,上述的无源耦合并不能解决损耗一致性的问题。
我们理想的光路对接是下图这样的,4个/8个/16个/32个,每个间距250微米,总计好几个毫米的状态下,他们的波导高度都一致。
但是现实可能做不到,比如硅光芯片是需要电信号引入引出的,那么焊接时的局部高热,会引起芯片的翘曲,虽然宏观上产生的Z轴高度差异很小,几个毫米长,只有千分之一的高度变化,几个微米而已。要知道咱们单模光纤的波导直径也是几个微米,Z轴翘度会导致很大的损耗不均匀。
这个时候面临的困境,即使是“无源”耦合,也会导致部分通道耦合损耗极大的隐患。
解决方案有几种,第一种在硅基板上刻蚀V型槽,可缓解分立结构的翘曲不一致,第二种在对接两侧采用准直透镜,扩大尺寸冗余度,第三种是采用对称透镜将XY平面耦合,转换为Z向对准,第四种将对接耦合改为倏逝波耦合,不再依赖Z轴高度的亚微米精度的一致性。
第一种方案是直接在硅光芯片上刻蚀V型槽,对于Z轴翘曲的容忍性,比分立器件好很多。
审核编辑:刘清
-
ssc
+关注
关注
0文章
25浏览量
11264 -
电信号
+关注
关注
1文章
840浏览量
20712 -
硅光芯片
+关注
关注
5文章
48浏览量
6142
原文标题:每一次开学,都离梦想更近
文章出处:【微信号:appotronics2006,微信公众号:光峰科技】欢迎添加关注!文章转载请注明出处。
发布评论请先 登录
相关推荐
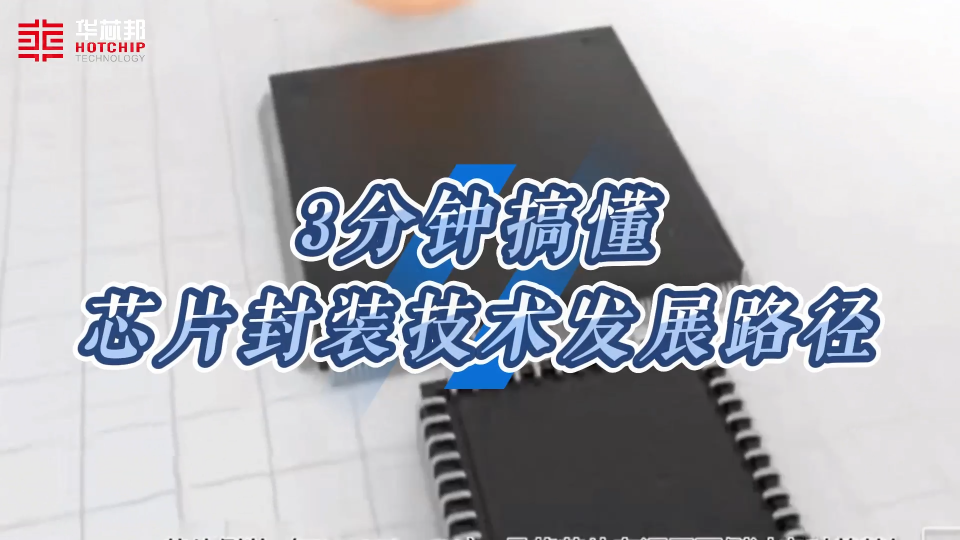
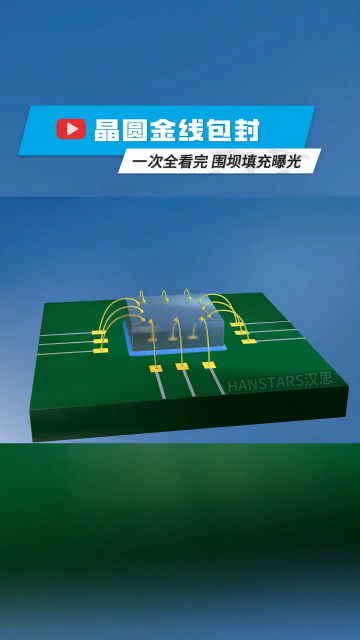
硅光芯片创新转型,测试测量新需求
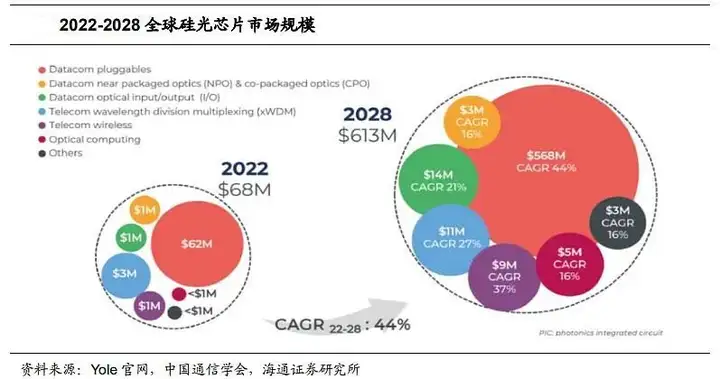
评论