2022年,新能源、动力电池已经从汽车产业链火爆出圈成为家喻户晓的话题。在上游的天齐锂业等锂盐公司以87%的夸张毛利率,半年豪取103亿净利润吸引走大家眼球的同时,汽车热管理这个对大多数人来说未曾听说的板块已经在二级市场中跑赢锂盐及动力电池,诠释了闷声发大财的精髓。
把时间拉回到2020年,一向以挑剔著称的马斯克竟一反常态,大肆表扬“Model Y的热泵是我这段时间见过最好的工程设计之一”。
比亚迪随后在2021年推出e3.0平台的热管理系统,全面取消了耗能最大的PTC控制模组,将驾驶舱制暖预热交给热泵电动空调系统以及来自“8合1”电驱+电控系统的余热,在设计思路上借鉴了特斯拉。
无独有偶,一直想在汽车产业有所作为的华为也在2021年HI新品发布会上重点发布了热管理系统TMS,采用一体化的设计理念,分配和传导乘员舱、电池、电驱等区域的热能,提升整车热量的综合利用率。
众多大厂纷纷将热管理系统推上C位,璞跃中国移动出行团队认为其深层原因在于电动车热管理系统水平高低对单车能量利用效率、续航里程及三电系统工作状态均有较大影响,战略意义大幅提升。同时,新的需求催生出新的市场,各大厂均希望在市场变革早期进行技术卡位,对投资机构来说,热管理同样具有很高投资价值。
01
电动车单车热管理系统价值翻倍,
重要性提升
为何燃油车热管理成本低
燃油车发动机工作温度高(最高温度可达2000℃),因此在制热系统上利用发动机工作产生的热量即可,空调系统仅需考虑制冷功能,无需额外加装制热装置。在发动机温度低时,冷却液走小循环减少散热,使得水温快速提升到最佳温度(90℃),改善排放性能。温度高时,冷却液走大循环通过散热器和风扇增加散热效率。
此外,由于燃油车配备的电池容量通常很小(HEV车型的电池容量大,可以使用电动压缩机),因此无法匹配电子压缩机,只能选择机械压缩机来作为空调制冷的手段。虽然机械压缩机相比电动压缩机会增加油耗,但是在前装的一次性成本上也节约了1000元左右,燃油车整车热管理系统的成本仅在两、三千元上下。
电动车热管理系统成本暴涨,
占比仅次于三电系统
对于电动车而言,其热管理系统由空调热管理、电机电控热管理及电池热管理三部分组成。空调热管理由于没有了发动机提供制热,因此需要采用PTC/热泵/薄膜加热器来提供热源(氢燃料电池车理论上可以像燃油车一样由动力系统提供热源,但启动时间更长)。
PTC技术成熟,但是由于其电加热的技术原理导致电能利用效率低于100%(每产生1焦耳的热量需消耗超过1焦耳的电量),对电池消耗较大。尤其考虑到空调制热功能最重要的使用场景是冬天,且温度越低需要的制热功率越大,采用PTC制热会让电动车在冬季本就少得可怜的续航里程雪上加霜,严重破坏实用性。
热泵制热则是把热量从相对低温处(车外)搬到相对高温处(车内),利用低沸点的制冷剂将环境中的热量带入到乘客舱中,乘客舱得到的热量为消耗的电能与吸收的低位热能之和,因此其制热系数 COP [(吸收的低位热能+消耗电能)/消耗电能]必然大于1(通常为1.5-5),减少了对电池的负荷。大众ID.4 CROZZ在搭载CO2热泵后,其冬季续航里程提升了30%。
电机和电控热管理可以很好地借鉴燃油车发动机和变速箱热管理模块,同样采用风冷和水冷两种方式。风冷主要应用于电机功率较小的低端车型,水冷则主要在功率较高的车型中使用。工作时依靠水泵带动冷却液在冷却管道中循环流动,通过散热器等热交换过程,使冷却液带走电机、电控产生的热量。
电池热管理可以说是电动车热管理最大的增量,同时由于环境温度对电池的工作状态有巨大影响,因此电池热管理的好坏对电动车用户体验至关重要。动力电池高效工作温度区间是 20-35℃,温度过低(<0℃)会导致电池活性下降,充放电功率性能下降,缩短续航里程,破坏电池寿命;温度过高(>45℃)则不仅会破坏电池寿命,还可能导致电池热失控,甚至起火等严重事故发生。电池内部温度和电池模块间温度均匀性同样会影响电池使用性能和循环寿命,因此电池热管理系统需要复杂、精细的冷却回路来维持电芯温度一致性,并能够准确测量和监控电池温度,在电池温度过高时及时散热、温度过低时快速加热。目前电池热管理有风冷、水冷、直冷、相变材料等多种方式。
液冷方式由于其冷却速度更快、换热系数更高是应用前景最好的电池热管理方案(可以配合相变材料等技术辅助)。由于动力电池电芯排列较为整齐,因此电池液冷主要通过液冷版的形式进行。传统电池液冷板采用整板结构,置于电池组下方。宁德时代在刚刚发布的旗舰产品——麒麟电池中采用在两块电芯中间加装液冷板的全新布局,使相邻两块电芯的热传导降低、提升安全性,但单车液冷板用量也会成倍增加。
02
热管理新技术
为中国带来弯道超车契机
国际四巨头垄断燃油车热管理系统
由上图可知,日本电装(丰田集团旗下)、法国法雷奥、韩国翰昂和德国的马勒在燃油车热管理领域掌控了全球约6成的市场份额。他们不仅拥有几十年甚至上百年的汽车热管理经验,更重要的是,在长期的合作中他们与下游主机厂形成了深度绑定,新进入者很难与之竞争。
特斯拉推出高集成化热管理系统,
开创了电动车热管理新的发展方向
随着电动车销量的增加,传统四巨头并非没有涉足其中,只不过在设计思路上没有打开,有照搬燃油车的思维惯性(或是对市场份额有恃无恐)。如2022年才开始登陆高端量产车的热泵系统,日本电装早在2013年就在雷诺Zoe和日产LEAF上进行了搭载。翰昂也是早在2014年就将热泵搭载到起亚Soul等韩系车型。但是直到2020年特斯拉在Model Y上搭载的第四代热管理系统问世,没有人尝试将量产车的电机电控以及空调热管理的余热进行集成回收来为电池加热,各模块间依旧独立运行。
特斯拉在Model Y的热管理系统中没有单独设置外置冷凝器,而是通过热交换器和管路连接,与电池回路和电机回路进行耦合,实现整个热管理系统的热量交互,同时进一步集成化,采用了集成歧管模块和集成阀门模块。该系统通过控制膨胀阀开度,止向阀动作来控制冷媒的循环,通过控制八通阀的位置来控制冷却液的循环,最终可实现12种制热模式及3种制冷模式来应对不同工况需求,降低了单车能耗,增加续航里程。
中国企业奋起直追
特斯拉第四代热管理的核心器件——八通阀正是由特斯拉与中国企业三花智控联合开发完成的。三花的前身是1994年中日合资企业三花不二,经过三十年持续不断地在电子膨胀阀、四通阀等制冷部件领域投入研发并改进产品性能,先后切入家用冰箱、空调、汽车等领域,时至今日终于在阀类产品走到世界前列。凭借电动车热管理带来的新需求,发力向汽车热管理Tier1企业努力。
华为意识到自己在汽车机械素质、操控性领域技术薄弱,在看到面对电动车热管理的新需求,业界无人能给出最优解,存在着弯道超车的机会后,毅然将汽车热管理系统作为核心发力点之一。其TMS系统在部件域将压缩机、储液罐、水阀、电子阀等12个主要零部件集成为一体,以基板取代传统的互通管路,实现管路数量降低40%,部件数量降低10%,装配工作量降低60%。在控制单元域,传统的热管理系统各部件由电子控制单元(ECU)单独控制,TMS将所有部件的控制单元集成于一个电子驱动单元(EDU),能够有效降低系统故障率,便于维护、诊断各系统部件的生命周期,提升热管理系统可靠性。
03
高度集成化
是热管理系统未来发展核心
当前电动车热管理系统系统集成度较低,仍以分散式为主,三电系统和空调系统的回路彼此独立,有各自的温控和管路系统,导致热管理流程复杂,零部件较多且能量利用不充分。从整车层面看,各个分散的热管理系统通过统筹管理可以减少能量浪费和体积占用。当前面临的主要困难是控制逻辑复杂以及铝合金加工工艺上面存在挑战,但璞跃中国移动出行团队认为,高能量利用效率、轻量化、长续航的集成式热管理系统是行业发展的必然趋势。
马瑞利在其新推出电动车热管理系统中,突破了传统铝合金铸造工艺的限制,将加热、散热、传热、温控、温感环节集成为一个部件,重量由上一代产品的7kg减少到0.6kg,体积大幅缩小,是电动车热管理集成化的一次很有意义的突破。
针对热泵在低温环境启动慢、制热效果差的问题,可以使用CO2热泵及/或加装薄膜加热器来进行应对。CO2热泵空调比现有空调冷媒更加环保,在低温下比R1234yf型热泵能源利用率更高,以更少的耗电量达到相同的制热效果。相比普通的热泵空调系统很难在-15℃以下进行使用的硬伤,CO2热泵空调可以在-30℃持续工作,增加了实用性。CO2热泵没能普及的主要原因是运行压力高(为传统热泵的8-9倍),因此需要将整个空调系统更换为耐高压零部件,如耐高压管路、耐高压电子膨胀阀、耐高压的空气压缩机等,会增加技术难度和成本。
使用薄膜加热器+热泵的方案确实可以很好应对低温工况的问题,但是成本显著增加同时增加热管理系统的体积,导致该方案仅能在高端车领域进行应用。
璞跃中国移动出行团队认为,虽然中国企业和特斯拉在电动车热管理系统初期竞争中反应迅速,但以Big4为代表的老牌欧美日韩的Tier1及整车厂巨头仍然有着竞争优势和举足轻重的行业影响力,部分在电动车热管理领域开创的新技术也会反哺到燃油车热管理上进行应用。大众集团在奥迪A8(2018)及大众ID系列(2021)率先搭载了CO2热泵,是全球最早在走量车型上搭载CO2热泵的公司,其高门槛部件高压电子压缩机正是出自燃油车热管理Big4之一的翰昂。中国企业仍然需要以挑战者的姿态,戒骄戒躁,以十年为单位制定企业战略,坚定研发导向,不断改进产品的同时敢于去拥抱新技术,才真正有希望在这场没有终点的马拉松当中建立核心优势。
审核编辑 黄昊宇
-
电动车
+关注
关注
73文章
3047浏览量
115134 -
热管理
+关注
关注
11文章
457浏览量
21965
发布评论请先 登录
相关推荐
来吧,拆个比亚迪!
比亚迪入股庆虹电子,连接器有何市场机遇?
简述智慧供热管理服务平台
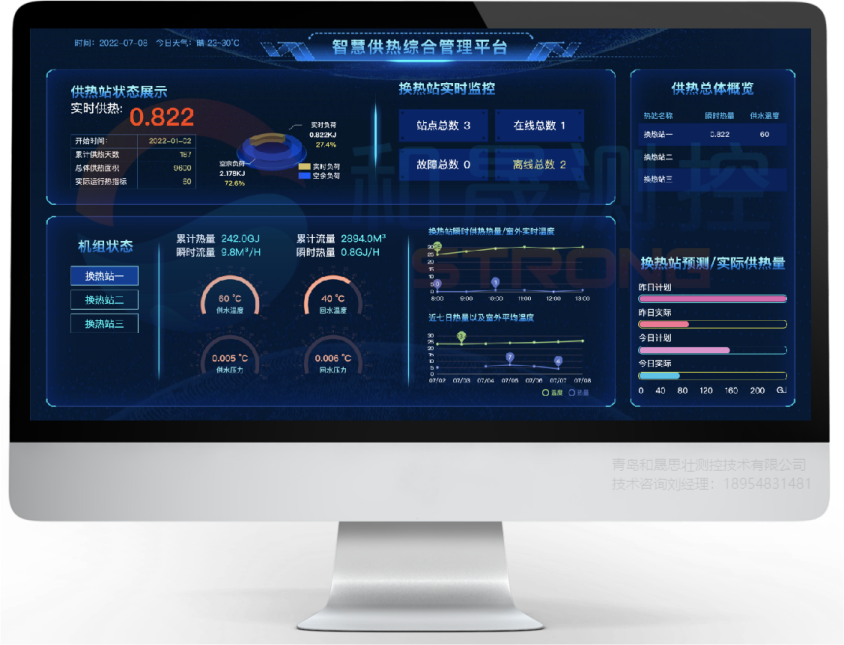
soc设计中的热管理技巧
电池热管理系统的冷却方式有哪些?
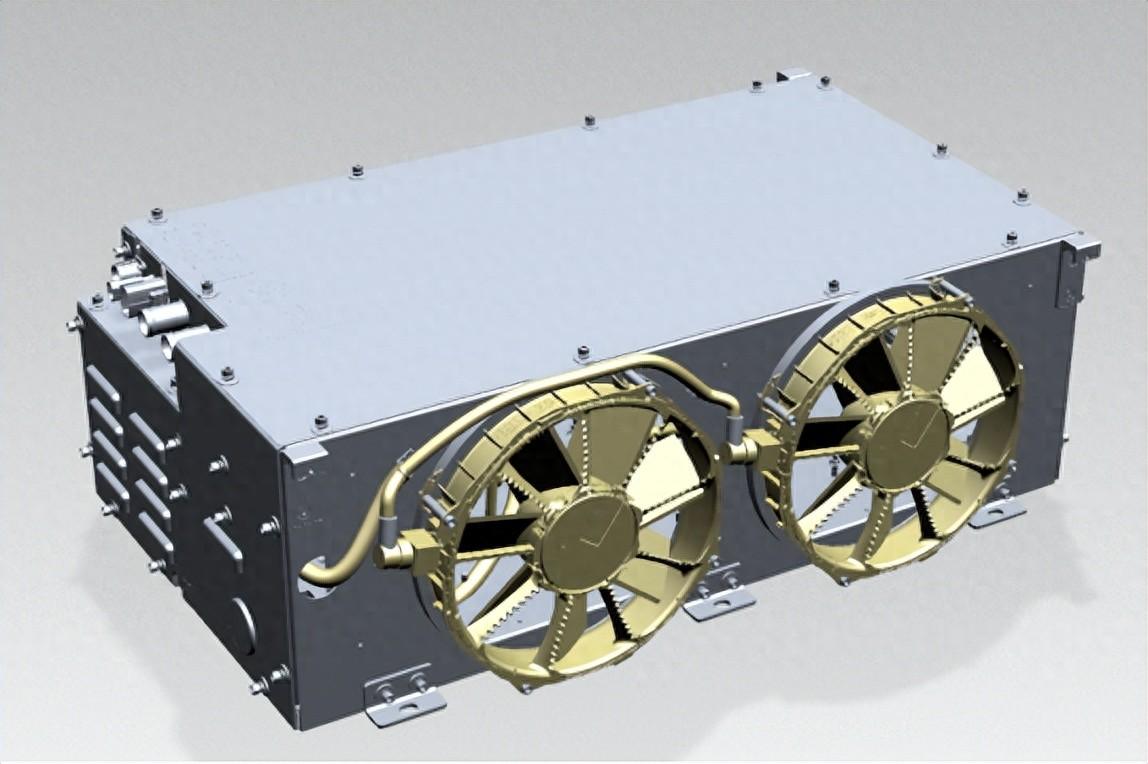
PID控制器在热管理系统中的应用
电动汽车热管理系统常见故障有哪些?
新能源电池包的热管理系统材料有哪些
热管理系统的工作原理 热管理系统的主要功能
电池模组的热管理系统是如何设计的,有哪些高效的热管理方案?
探索特斯拉新能源汽车热管理系统集成技术
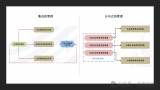
评论