最近小组开始整DFMEA分析了,之前对DFEMA没有完整的梳理过,趁这次机会梳理一下。
01. FMEA的历史
首先DFMEA为Design Failure Mode and Effects Analysis的缩写,即设计过程中的潜在失效模式及后果分析,是一种以预防为主的可靠性设计分析技术。针对产品设计或者制造过程, 以产品的系统、 子系统、 制造工序的功能或要求进行一一分析, 将功能或要求的失效模式、 影响及原因关联, 并对失效模式采取事先预防措施。
按照设计开发过程,可以将FMEA分为设计FMEA(DFMEA)、过程FMEA(PFMEA)。其中DFMEA适用于产品设计阶段的失效模式及故障分析,PFMEA 适用于工艺过程和制造过程的失效模式及故障分析。
FEMA最开始是美国在上世纪50年代,在军事领域进行信息系统的设计分析中应用,后面扩展到航天工业,到70年代,FMEA开始用于民营企业,到70年代末期,FMEA开始被美国汽车工业所采纳。
1997年,福特是最为最早实施FMEA的公司之一,将FMEA技术操作标准写入其操作手册标准中,这不仅仅是用于福特内部,福特公司还规定其所有供应商都必须对其供应给福特公司的零部件进行 FMEA 分析。
1993 年, 福特、 通用和克莱斯勒三大汽车巨头制定了一套针对汽车产业中的所有零件的" 潜在失效模式与影响分析参考手册", 至此, FMEA 作为一种标准化的技术在美国汽车行业中得到了极大的应用。
1994 年, 作为QS-9000 的核心方法之一,为了提高产品的质量,ISO 推荐将 FMEA 方法用于产品的设计阶段, 以确保产品生产过程的稳定性。
到目前,FMEA已经成为汽车行业普遍使用的一种技术方法。
02. 评价指标
评价指标主要包含三个部分,分别为严重度、探测度、频度。
严重度代表失效影响的严重程度,关系到被评估功能的既定失效模式的最严重失效影响程度。
▲图1 不同严重度含义表(来源知网)
频度是根据评级标准对预防控制有效性的衡量, 频度评级的值是 FMEA范围内的一个相对级别。
▲图2 不同频度含义表(来源知网)
探测度是对探测控制有效性的估计, 用于在项目交付生产前, 可靠的证明失效起因或失效模式,这个还依赖探测方法。
03. DFMEA分析
对于车载控制器而言,DFMEA 具有很强的时限性, 必须明确在什么阶段做什么内容。在项目立项后开始组建 DFMEA 团队;在控制器设计阶段充分理解设计概念, 开始 DFMEA 分析;在设计规范发布后早期产品加工图样完工且产品制造之前完成 DFMEA 分析;在生产前完成 DFMEA 措施;如果设计发生变更时及时更新 DFMEA。
▲图3DFMEA分析(来源公众号:鲜万世质量频道)
以下以整车控制器的软件功能DFMEA分析为例,在之前的文章我们讲到整车控制器的功能(感兴趣可以戳回送门:谈谈整车控制器的功能),分别包括快充控制、能量回收、定速巡航、扭矩控制、高压上下电控制等。 这几个大的功能具体包含哪些呢?下面以高压上下电和扭矩控制回收为例说明。
1) 高压上下电功能与要求包括:
制动踏板响应正常;
正常接收 PEPS 启动请求;
正常完成防盗认证;
VCU硬件可正常唤醒休眠;
高压主继电器可以正常断开;
实现行车模式切换;
车辆行驶过程中扭矩正常输出;
根据油门开度正常输出扭矩; 基于以上两个功能,会存在哪些失效模式和失效起因呢?
失效模式 | 失效起因 |
VCU发送信号周期与BMS接收周期不匹配 |
1.VCU报文发送周期为20ms,与要求的10ms不符合; |
整车起步时抖动明显 |
动力传动齿轮间隙过大; 扭矩过零处理不够平缓; |
行驶过程中或滑行减速过程中,车辆意外加速; |
扭矩输出MAP标定不合理; 驾驶模式信号判断不合理,行驶过程中错误切换模式; |
车辆无法ready | 1、在VCU下电流程的不可撤回过程中,收到唤醒信号,导致车辆无法ready; 2、VCU的关联件报故障; |
▲图4部分失效分析示例
最后根据列出的失效原因,对软件进行修复,并且借助探测方法,比如实车验证、台架验证、注入验证等,来验证修复后的软件是否达到目标。
整体的流程如下图所示。
▲图5失效模式处理流程(来源知网)
以上就是借助这次小组梳理DFMEA之际,对DFMEA的一些梳理。
审核编辑:刘清
-
继电器
+关注
关注
132文章
5329浏览量
148784 -
控制器
+关注
关注
112文章
16299浏览量
177783 -
FMEA
+关注
关注
1文章
96浏览量
13604
原文标题:DFMEA的历史以及简单示例
文章出处:【微信号:eng2mot,微信公众号:汽车ECU开发】欢迎添加关注!文章转载请注明出处。
发布评论请先 登录
相关推荐
建议DFM工具里的拼版在完善一下
DFM在实际应用中的关键考虑和策略
堆栈和内存的基本知识
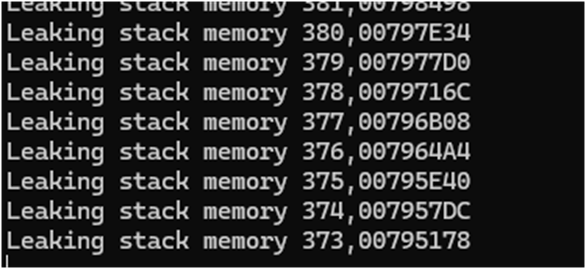
光刻工艺的基本知识
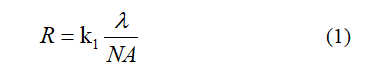
欢创播报 支付宝“碰一下”正式发布
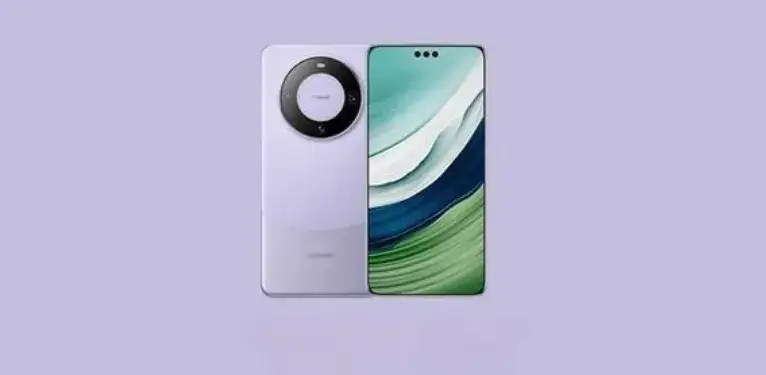
华秋DFM使用问答精选合集(一)
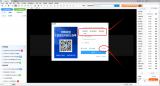
评论