焊接,也称作熔接,是一种以加热、高温或者高压的方式接合金属或其他热塑性材料如塑料的制造工艺及技术。
现代焊接的能量来源有很多种,包括气体焰、电弧、激光、电子束、摩擦和超声波等,随着工业的发展和科技的不断进步,焊接智能装备凭借其输出能量大、焊接速度快、适用性强的优势已在航空航天、汽车、3C电子等制造业中得到广泛应用。
在这些行业应用过程中,市场也不断对焊接加工品质提出了更高的需求,例如更多类型材料的焊接能力、焊点焊面的完整度与连续性、焊接品质的检测效率等。
1、焊接焊点外观检测的必要性
焊接作为工业生产中不可或缺的环节,对产品质量有着重要的影响。焊接过程中由于参数设置和运行 过程等因素影响焊接部件的缺陷难以避免。
如裂纹、夹渣 、气孔 、未焊透 、未熔合等,这些缺陷对安全生产以及产品质量构成严重威胁。因此,有效地检测出焊接过程中出现的缺陷对产品质量和生产制造都十分重要。
传统的缺陷检测方式采用人工检测,缺点是成本高,且检测效率随用工时间的延长迅速降低。后来,X射线探伤和超声波探伤的引入对于焊接缺陷检测提供了新的方法,这些方法有易于检测内部缺陷的优点,但成本高,成像欠清晰等问题始终困扰着这些检测方法。因此如何尽可能减少在生产过程中人工评定法的主观性、差异性成为各个行业及客户的主要诉求。在此背景下,配备高效智能的外观缺陷检测系统变得尤为重要。
随着工业机器视觉的发展,深度学习在图像特征学习中的独特优势使其在表面缺陷检测中具备重要的实用价值,成为了工业智能检测领域的主流研究方向
2、基于深度学习的焊接焊点缺陷检测
深度学习主要包含卷积神经网络和Faster R-CNN两种网络模型,通过利用算法模型自动学习的特点,不再受限于复杂多变的环境,可自动提取缺陷特征,最终实现自动检测。
一方面,避免了传统算法中人工提取特征的局限性和复杂性;
另一方面,深度学习在自然语言处理、图像分类和图像分割等领域已获得了广泛应用,为外观缺陷检测系统的研发奠定了坚实基础。
基于深度学习的焊接、焊缝、焊点等缺陷自动检测系统如图所示 ,由工业摄像机 、计算机 、采集卡 、光源 、工件及工件运动控制装置组成 。
1. 图像获取:①工业相机与光学镜头、②照明光源、③传感器、④图像采集卡;
2. 图像处理:⑤PC平台、⑥视觉处理软件、⑦控制单元。
工业相机和图像采集卡采集目标区域的图像 ,在计算机中进行实时自动处理和分析,系统的核心在于图像处理。
工业现场中,采集的图像并非仅限于缺陷存在的区域,往往是待检对象所处的整个区域,这个区域通常包括光源、背景工件、背景板等诸多因素,尤其是某些情况下,实际检测对象需要与光源 “交叉 ” 。因此,为了得到最终的检测结 果需要诸多步骤实现目标区域的逐步锁 定,并最终利用缺陷检测的相关技术对感兴趣区域进行最终检测以判断是否存在缺陷问题。
为了实现这样的目标,首先需要考虑将目标对象与背景进行分割,得到初步目标 (预定位 ),通过具体检测目标的相关特征进一步锁定检测对象,然后在得到检测对象的基 础上锁定感兴趣区域,最后对感兴趣区域进行检测判断是否存在缺陷并标记。
3、以PCB焊点缺陷检测为例
针对 PCB 板的正反面进行检测,PCB 焊点缺陷检测主要有四种类型:多锡、少锡、焊锡合适和漏焊。
照明方式的设计
考虑到光源与镜头的相对位置以及相关的光学原理等因素,照明方式有很多种,常用的方式有同轴光源照射、背光光源照射等,下面对照明方式进行设计比较。
考虑到 PCB 板特点以及环形照射优点:PCB 基板对光线反射能力弱,焊点反射能力强;焊点分布有一定的范围;环形照射会减弱阴影出现。因此选用的光源为环形光源, 每个 LED 灯珠向内侧倾斜 30 度, 减弱了反光影响。
机器视觉检测方案总体设计
采用机器视觉和图像处理技术对 PCB 焊点缺陷进行检测, 机器视觉检测系统的重要组成部分如下:
2、光学系统:由圆环形光源、图像采集卡、工业相机、光学镜头、实验支架以及实现相机采集图像的控制软件等组成;
3、图像处理检测系统:主要是 PCB 焊点图像检测识别算法,包括多曝光图像融合、图像预处理、特征提取、焊点缺陷检测分类等;
4、系统软件:在 PC 机上,根据相关系统软件,对采集到的焊点图像进行一系列图像处理, 得出测试数据并进行分析。
审核编辑 :李倩
-
机器视觉
+关注
关注
163文章
4440浏览量
121183 -
焊接
+关注
关注
38文章
3298浏览量
60398 -
焊点
+关注
关注
0文章
121浏览量
12888
发布评论请先 登录
相关推荐
X-Ray检测设备能检测PCBA的哪些缺陷
焊点能量反馈检测设备的应用与优势分析
全自动焊点强度检测仪:提升焊接质量与效率的关键设备
焊点能量实时检测仪:确保焊接质量与效率的新利器
激光焊接如何保证焊点质量
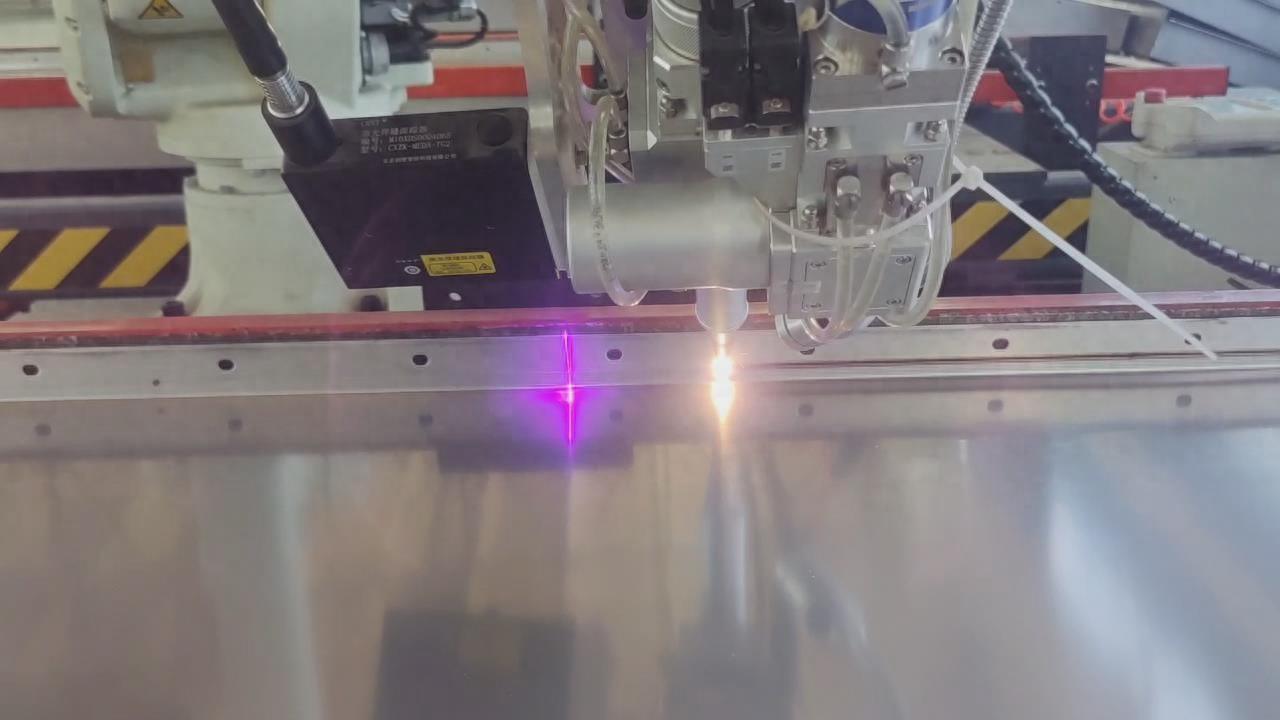
深度学习在工业机器视觉检测中的应用
基于AI深度学习的缺陷检测系统
基于深度学习的小目标检测
外观缺陷检测原理
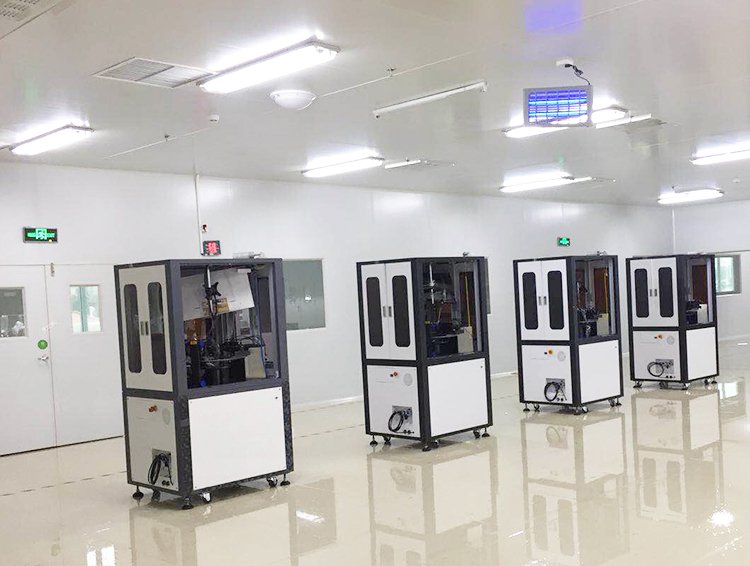
常用的几种BGA焊点缺陷或故障检测方法

焊接质量缺陷产生的主要原因
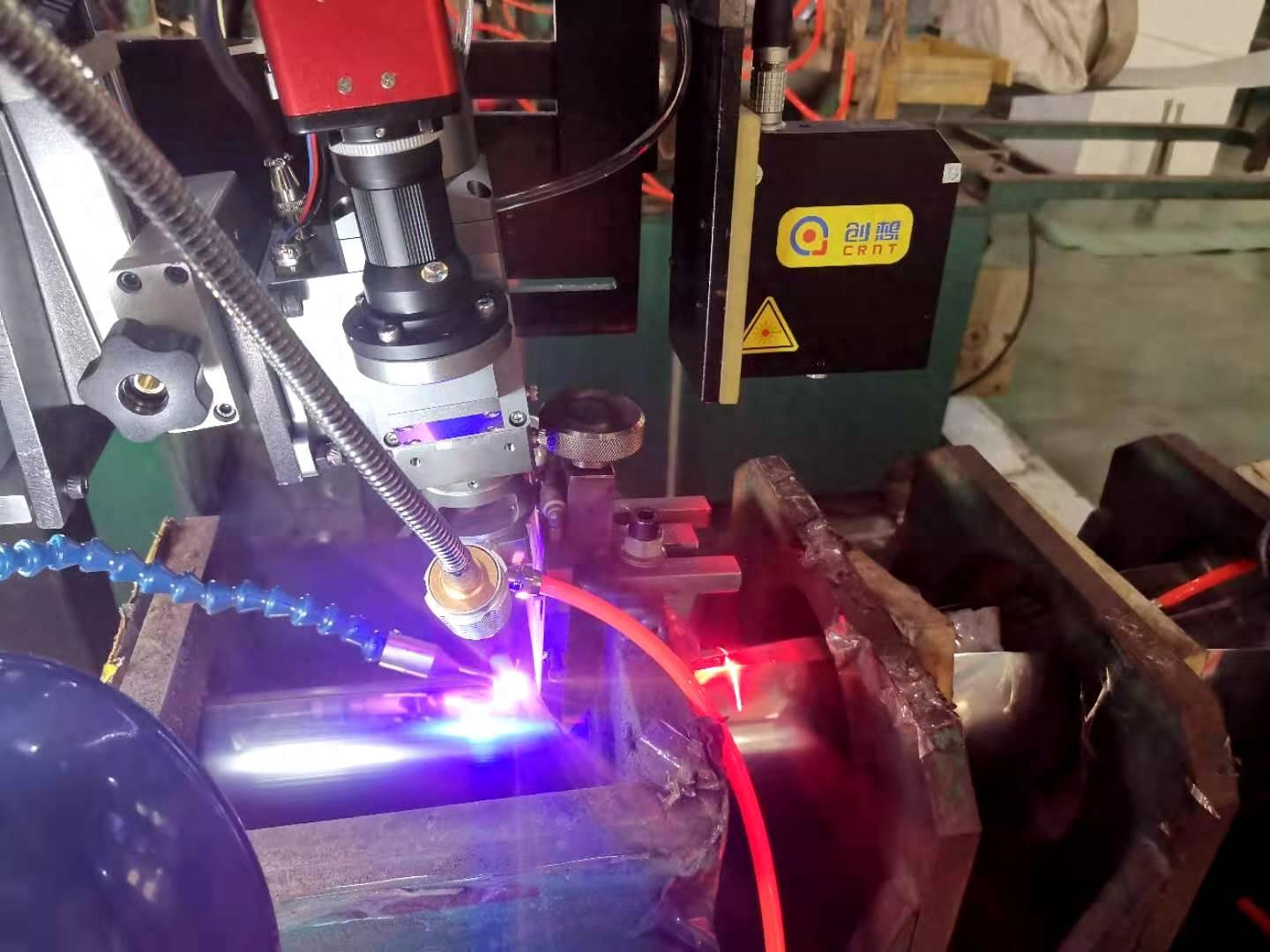
为什么说“AOI检测”是SMT焊接质量的把关者?
基于深度学习的缺陷检测方案
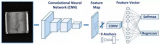
评论