在集成电路制造工艺中,氧化硅薄膜形成的方法有热氧化和沉积两种。氧化工艺是指用热氧化方法在硅片表面形成二氧化硅(SiO2)的过程。热氧化形成的二氧化硅薄膜,因其具有优越的电绝缘性和工艺的可行性,在集成电路制造工艺中被广泛采用,其最重要的用途是作为 MOS 器件结构中的栅介质,其他用途还包括器件保护和隔离、表面钝化处理、离子注人掩蔽层、扩散阻挡层、硅与其他材料之间的缓冲层等。硅在空气中会与空气中的氧自然反应生成氧化硅薄膜,其氧化速率约为 1.5nm/h,最大厚度约为 4nm。自然氧化层的厚度很难精确控制,而且质量很差,在制造过程中需要尽量避免和去除;而在氧气浓度更高的环境中进行高温加热,可以更快速地得到更厚的高质量二氧化硅膜。
根据反应气体的不同,氧化工艺通常分为干氧氧化和湿氧氧化两种方式。干氧氧化化学反应式为 Si + O2 = SiO2;反应气体中的氧分子以扩散的方式穿过已经形成的氧化层,到达二氧化硅-硅界面,与硅发生反应,进一步生成二氧化硅层。干氧氧化制备的二氧化硅结构致密,厚度均匀,对于注人和扩散的掩蔽能力强,工艺重复性强,其缺点是生长速率较慢。这种方法一般用于高质量的氧化,如栅介质氧化、薄缓冲层氧化,或者在厚层氧化时用于起始氧化和终止氧化。
湿氧氧化化学反应式为H2O(水汽)+ Si =SiO2+2H2;在湿氧工艺中,可在氧气中直接携带水汽,也可以通过氢气和氧气反应得到水汽,通过调节氢气或水汽与氧气的分压比改变氧化速率。注意,为了确保安全,氢气与氧气的比例不得超过 1.88:1。湿氧氧化由于反应气体中同时存在氧气和水汽,而水汽在高温下将分解为氧化氢(HO),氧化氢在氧化硅中的扩散速率比氧快得多,所以湿氧氧化速率比干氧氧化速率高约一个数量级。
除了传统的干氧氧化和湿氧氧化,还可在氧气中摻入含氯气体,如氯化氢 (HCL)、二氯乙烯 DCE(C2H2Cl2)或其衍生物,使氧化速率及氧化层质量均得到提高。氧化速率提高的主要原因是,掺氯氧化时,不仅反应产物中含有可加速氧化的水汽,而且氯积累在 Si-SiO2界面附近,在有氧的情况下,氯硅化物易转变成氧化硅,可催化氧化。氧化层质量改善的主要原因是,氧化层中的氯原子可以钝化钠离子的活性,从而减少因设备、工艺原材料的钠离子沾污而引入的氧化缺陷。因此,多数干氧氧化工艺中都有掺氯行为。
由于传统氧化工艺所需温度较高,时间较长,引入的热预算(Thermal Budget) 很高,造成了硅片中杂质的再分布,在先进技术节点中会导致器件性能劣化,因此应严格控制热预算。在后高k(High-k Last)的高k金属栅工艺中,一般会采用快速热氧化(Rapid Thermal Oxidation, RTO)或化学品氧化(Chemical Oxidation)等方法生长栅介质超薄界面层 (Interfacial Laver)。快速热氧化中的升/降温速率比普通热氧化快 100~1000 倍,减少了升/降温过程中的热预算。在化学品氧化中,结合臭氧氧化和化学品处理,可以在按近室温条件下获得高质量的界面氧化层,减少了由于高温带来的热预算。
审核编辑 :李倩
-
集成电路
+关注
关注
5400文章
11689浏览量
364529 -
硅片
+关注
关注
13文章
372浏览量
34836
原文标题:氧化工艺(Oxidation Process)
文章出处:【微信号:Semi Connect,微信公众号:Semi Connect】欢迎添加关注!文章转载请注明出处。
发布评论请先 登录
相关推荐
等离子体蚀刻工艺对集成电路可靠性的影响
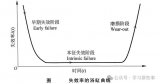
【「大话芯片制造」阅读体验】+ 芯片制造过程和生产工艺
集成电路工艺学习之路:从零基础到专业水平的蜕变
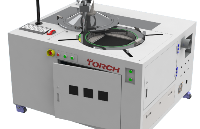
集成电路封装基板工艺详解:推动电子工业迈向新高度!
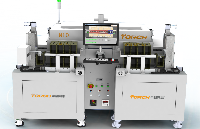
评论